- お役立ち記事
- Fundamentals of plastic injection molds and key points on design and production for product design and mold engineers
月間77,185名の
製造業ご担当者様が閲覧しています*
*2025年2月28日現在のGoogle Analyticsのデータより
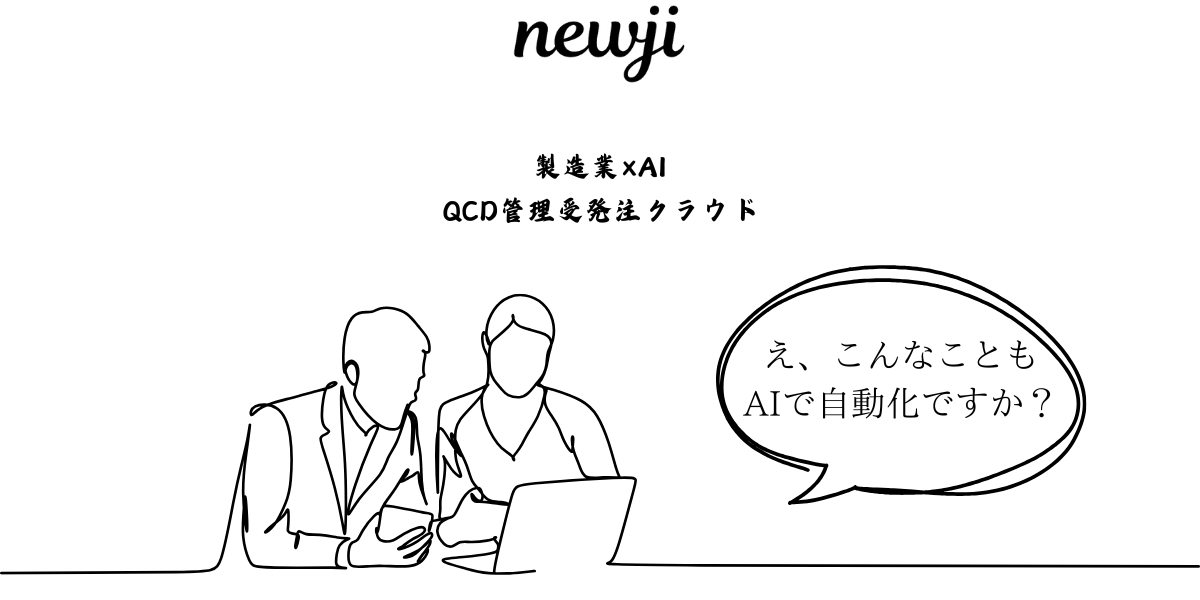
Fundamentals of plastic injection molds and key points on design and production for product design and mold engineers
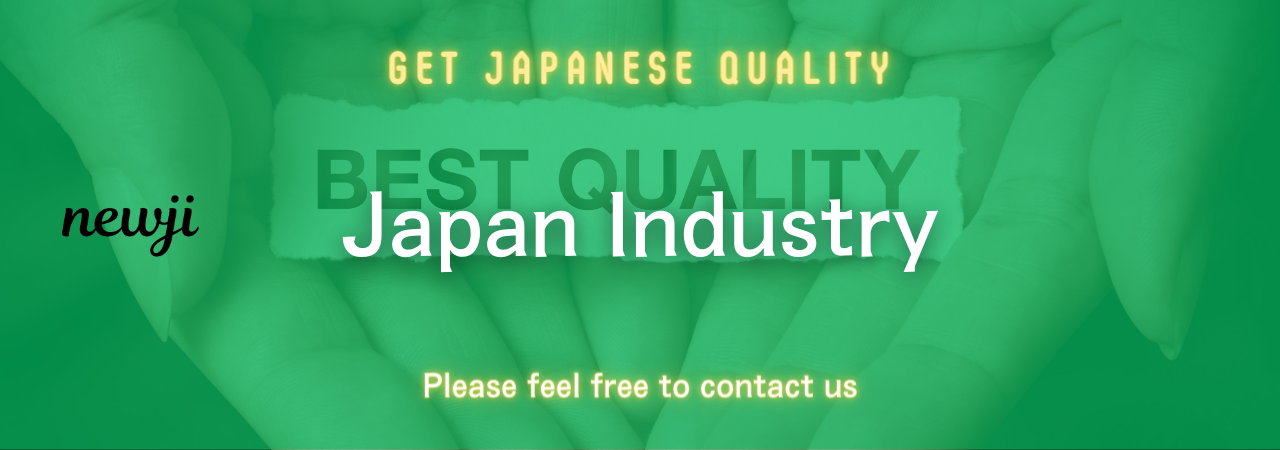
Plastic injection molding is a cornerstone in the manufacturing industry, known for its efficiency in producing complex and high-quality parts. Understanding the fundamentals of plastic injection molds is crucial for product design and mold engineers. In this article, we will explore the essential aspects of plastic injection molding, including design and production considerations.
目次
Understanding Plastic Injection Molds
Plastic injection molding involves the melting of plastic materials which are then injected into a mold to form a desired shape. This process is favored for its ability to produce parts with intricate designs and tight tolerances. The core concept relies on a mold made typically from steel or aluminum, which serves as a template for the parts.
How Does the Injection Molding Process Work?
The injection molding process begins with feeding plastic pellets into a heated barrel. The material is then melted by heat and forced through a nozzle into a mold cavity. The injected plastic takes the shape of the mold, cools, and solidifies. Once the cooling phase is complete, the mold opens, and the part is ejected.
Key Elements of Mold Design
Designing a mold is a critical aspect that influences product quality, production efficiency, and cost. Several key elements need special attention during the design phase.
Mold Material Selection
Choosing the right mold material is vital. Steel molds, often used for high-volume production, are robust and durable, while aluminum molds can be cost-effective for lower-volume manufacturing.
Cavity and Core Design
The cavity is the hollow part that shapes the final product, while the core helps in forming internal features. Accuracy in the design of these components is critical to ensuring the product meets its dimensional requirements.
Draft Angles
Draft angles facilitate the removal of the molded part from the mold. A proper draft angle reduces wear and tear on the mold and prevents damage to the part itself.
Cooling Systems
Effective cooling systems are essential for cycle time reduction and maintaining part quality. The design of cooling channels must ensure uniform cooling to prevent defects and warping.
Considerations in Injection Mold Design
To ensure a successful injection molding process, both product design and mold engineers must address several important considerations.
Understanding Material Properties
Different plastic materials possess unique properties. It’s essential to select a material that meets the product’s functional requirements and is compatible with the injection molding process.
Wall Thickness
Uniform wall thickness is crucial for reducing stress and ensuring consistent flow of material inside the mold. Variations in thickness can lead to defects such as warping or sink marks.
Parting Line Location
The parting line is where the two halves of the mold meet. Its strategic placement is important for minimizing finishing work and ensuring the aesthetics of the final product.
Gate Design and Placement
The gate introduces molten plastic into the mold cavity. Its design and location affect the flow of material and the quality of the finished part. Improper gate placement can result in flow lines or incomplete filling.
Producing a Mold
Once the design phase is complete, the production of the mold kicks off.
Machining and Fabrication
Creating a mold involves precision machining processes like CNC milling and EDM (Electrical Discharge Machining). These processes shape the mold to the exact design specifications.
Testing and Validation
Before moving to full-scale production, the mold is tested to identify potential issues. Trial runs help engineers fine-tune processes, ensuring optimal performance and part quality.
Maintenance
Regular maintenance of a mold extends its life and ensures consistent part quality. Maintenance activities include cleaning, repairing wear and tear, and ensuring the mold components function smoothly.
Advanced Techniques in Mold Design
Continuous advancements in technology have introduced sophisticated techniques in mold design that enhance efficiency and part quality.
Computer-Aided Design (CAD)
CAD software enables precise and intricate mold designs. It assists engineers in visualizing mold functionality and refining designs before production.
Simulation and Analysis
Simulation tools analyze mold flow to predict potential issues like air traps or weld lines. These insights allow engineers to make necessary adjustments pre-production.
3D Printing for Prototyping
3D printing offers a rapid and cost-effective way to develop prototypes and test designs iteratively. It allows product designers to validate concepts before committing to full-scale injection molding.
Conclusion
Mastering the fundamentals of plastic injection molds is essential for product design and mold engineers. By understanding the intricacies of mold design and addressing key considerations, manufacturers can optimize production and achieve high-quality results. Whether using traditional methods or adopting innovative technologies, the success of injection molding relies on meticulous planning, precise execution, and continuous improvement in design and production processes.
資料ダウンロード
QCD管理受発注クラウド「newji」は、受発注部門で必要なQCD管理全てを備えた、現場特化型兼クラウド型の今世紀最高の受発注管理システムとなります。
ユーザー登録
受発注業務の効率化だけでなく、システムを導入することで、コスト削減や製品・資材のステータス可視化のほか、属人化していた受発注情報の共有化による内部不正防止や統制にも役立ちます。
NEWJI DX
製造業に特化したデジタルトランスフォーメーション(DX)の実現を目指す請負開発型のコンサルティングサービスです。AI、iPaaS、および先端の技術を駆使して、製造プロセスの効率化、業務効率化、チームワーク強化、コスト削減、品質向上を実現します。このサービスは、製造業の課題を深く理解し、それに対する最適なデジタルソリューションを提供することで、企業が持続的な成長とイノベーションを達成できるようサポートします。
製造業ニュース解説
製造業、主に購買・調達部門にお勤めの方々に向けた情報を配信しております。
新任の方やベテランの方、管理職を対象とした幅広いコンテンツをご用意しております。
お問い合わせ
コストダウンが利益に直結する術だと理解していても、なかなか前に進めることができない状況。そんな時は、newjiのコストダウン自動化機能で大きく利益貢献しよう!
(β版非公開)