- お役立ち記事
- Fundamentals of plastic molding and causes and countermeasures for molding defects
月間77,185名の
製造業ご担当者様が閲覧しています*
*2025年2月28日現在のGoogle Analyticsのデータより
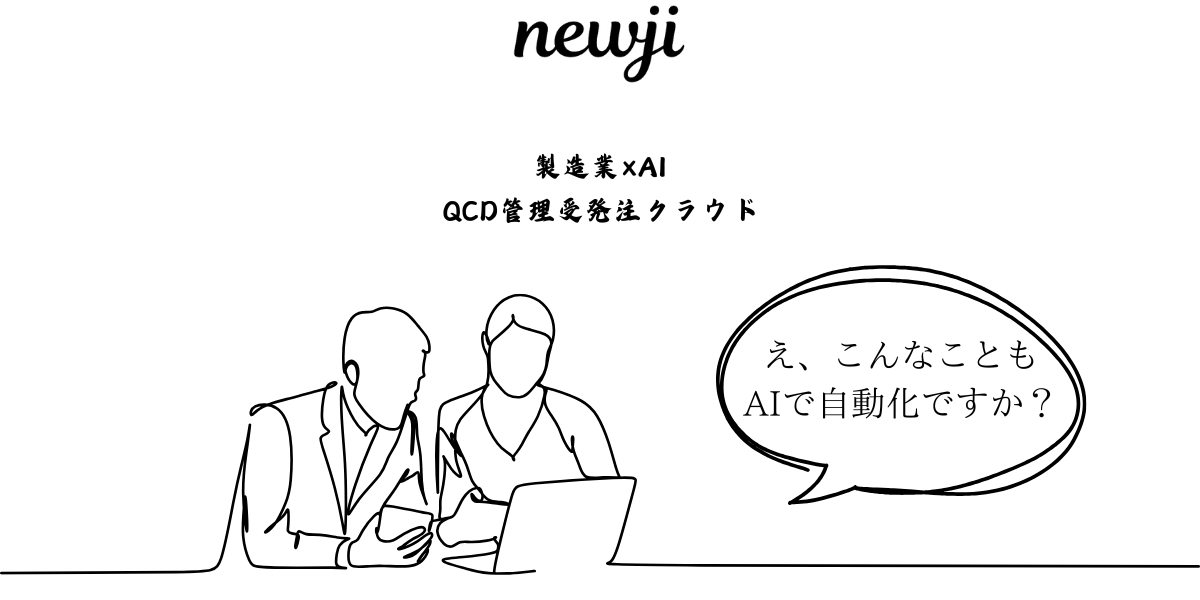
Fundamentals of plastic molding and causes and countermeasures for molding defects
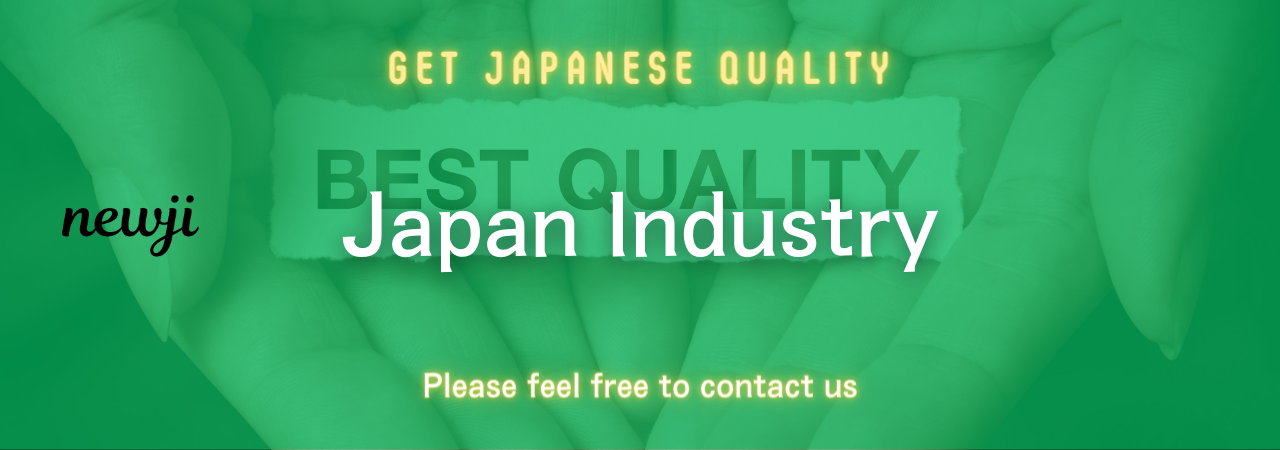
目次
Understanding Plastic Molding
Plastic molding is a manufacturing process used to create a wide variety of plastic products.
This versatile technique involves shaping raw plastic material into desired forms by employing different molding technologies.
These technologies include injection molding, blow molding, rotational molding, compression molding, and extrusion molding.
Each method has its distinct characteristics and applications.
Injection molding is the most common process and works by injecting molten plastic into a mold cavity.
It is ideal for making complex and high-volume plastic parts with precision and efficiency.
Blow molding, on the other hand, is employed for hollow plastic products like bottles and containers.
It involves inflating a heated plastic tube until it takes the shape of the mold cavity.
Different products require specific molding techniques, each with its own set of parameters and conditions.
Causes of Plastic Molding Defects
Despite the many advantages of plastic molding, defects can occur throughout the process.
These defects can affect the quality and functionality of the final product.
Understanding the causes of these defects is crucial to maintaining production efficiency and product quality.
Mold Design Issues
The design of the mold is a significant factor in the molding process.
Faulty design can lead to defects such as sink marks, warping, and flow lines.
These occur when the mold does not support uniform filling or proper cooling of the plastic material.
Improper sizing and poor venting design can also cause incomplete filling, leading to defective parts.
Material Quality
The quality of the plastic material used is another critical factor.
Contaminants or inconsistent quality can cause a range of issues.
Problems like discoloration, weak spots, and inconsistent texture may arise if the raw materials are compromised.
Material properties such as viscosity and melting point must be suitable for the molding process being employed to avoid defects.
Processing Conditions
Temperature, pressure, and cooling rates are vital parameters in the molding process.
If these conditions are not optimized correctly, defects can occur.
For instance, insufficient temperature can prevent the plastic from melting adequately, leading to incomplete filling and weak parts.
Conversely, excessive temperature can cause degradation of the material.
Pressure settings must be precise to ensure complete filling without creating stress within the material.
Similarly, improper cooling can result in warping and distortion of the final product.
Equipment Malfunctions
Machines used in plastic molding must be properly maintained and calibrated.
Any malfunction or misalignment can cause defects.
For example, worn-out or damaged mold cavities can introduce flaws into every produced part.
Regular maintenance and inspection are crucial to ensure equipment functions optimally.
Countermeasures for Molding Defects
To minimize and prevent molding defects, several countermeasures can be implemented.
These measures revolve around design improvements, material selection, process optimization, and equipment maintenance.
Refining Mold Design
Optimizing mold design is one of the most effective ways to prevent defects.
This involves ensuring proper venting, adequate cooling channels, and precise cavity dimensions to support the intended product.
Simulation tools can help identify potential issues in the design phase, allowing for adjustments before production begins.
Creating balanced runners and gates can also help ensure uniform distribution of material during the molding process.
Material Selection and Testing
Choosing the right material is crucial for successful molding.
Manufacturers should evaluate different plastic grades to find the one best suited to their needs.
Properly testing the material’s performance under expected processing conditions can help eliminate defects related to material quality.
Regular quality checks of incoming materials can also help detect contamination before it affects production.
Optimizing Processing Conditions
Careful control and monitoring of processing conditions is vital to avoid defects.
This includes setting optimal temperatures, pressures, and cooling times based on the specific molding process and material used.
Real-time monitoring systems can help maintain consistency throughout the production run.
Adjustments should be made as soon as deviations from the desired conditions are detected to minimize defects.
Regular Equipment Maintenance
To prevent defects related to equipment malfunction, regular maintenance and machine calibration are essential.
Preventive maintenance schedules should be established to address wear and tear before they result in major issues.
Ensuring that equipment is in top operational condition minimizes the risk of producing defective parts.
Conclusion
Plastic molding is a cornerstone of modern manufacturing, offering efficiency and versatility to produce countless products.
However, achieving defect-free production requires careful attention to mold design, material quality, processing conditions, and equipment maintenance.
By understanding the causes of molding defects and implementing the appropriate countermeasures, manufacturers can enhance the quality and reliability of their plastic products.
資料ダウンロード
QCD管理受発注クラウド「newji」は、受発注部門で必要なQCD管理全てを備えた、現場特化型兼クラウド型の今世紀最高の受発注管理システムとなります。
ユーザー登録
受発注業務の効率化だけでなく、システムを導入することで、コスト削減や製品・資材のステータス可視化のほか、属人化していた受発注情報の共有化による内部不正防止や統制にも役立ちます。
NEWJI DX
製造業に特化したデジタルトランスフォーメーション(DX)の実現を目指す請負開発型のコンサルティングサービスです。AI、iPaaS、および先端の技術を駆使して、製造プロセスの効率化、業務効率化、チームワーク強化、コスト削減、品質向上を実現します。このサービスは、製造業の課題を深く理解し、それに対する最適なデジタルソリューションを提供することで、企業が持続的な成長とイノベーションを達成できるようサポートします。
製造業ニュース解説
製造業、主に購買・調達部門にお勤めの方々に向けた情報を配信しております。
新任の方やベテランの方、管理職を対象とした幅広いコンテンツをご用意しております。
お問い合わせ
コストダウンが利益に直結する術だと理解していても、なかなか前に進めることができない状況。そんな時は、newjiのコストダウン自動化機能で大きく利益貢献しよう!
(β版非公開)