- お役立ち記事
- Fundamentals of plastic product design and effective use of resin flow analysis
Fundamentals of plastic product design and effective use of resin flow analysis
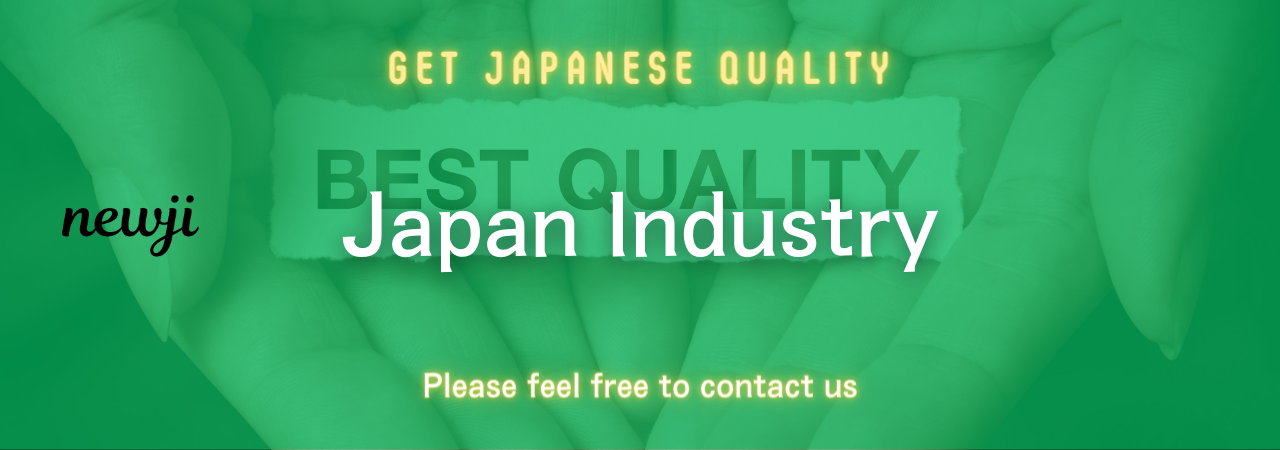
目次
Understanding the Basics of Plastic Product Design
Plastic product design is a crucial part of manufacturing industries, responsible for creating a wide array of items we use daily.
From household goods to automotive parts, understanding the basics of plastic product design can lead to more innovative and efficient products.
Material Selection
One of the first steps in plastic product design is selecting the appropriate material.
Different types of plastics, or resins, have specific properties that make them suitable for certain applications.
For example, polyethylene is often used for containers because of its durability and flexibility, while polystyrene is chosen for products needing rigidity.
Selecting the right material affects not only the product’s functionality but also its manufacturing cost and environmental impact.
It is essential to consider these factors early in the design process.
Design Considerations
When designing plastic products, engineers must consider several factors, including structural integrity, aesthetics, manufacturability, and cost.
The product must be strong enough to withstand its intended use while also having an appealing design.
A product must be designed with the manufacturing process in mind to ensure it can be produced efficiently.
This includes considering the parting line, draft angles, and wall thickness, which can all affect the ease of injection molding.
Prototyping
Prototyping is an essential phase in the design process.
It provides a tangible model of the product, allowing designers to test and refine their ideas.
Prototypes can be created using 3D printing, CNC machining, or traditional building methods.
Prototyping helps identify design flaws and provides an opportunity to make adjustments before moving to full-scale production.
The Importance of Resin Flow Analysis
Resin flow analysis is a simulation process used in plastic manufacturing to predict the behavior of molten plastic within a mold.
It is a critical component of ensuring high-quality, defect-free products.
Enhancing Design Accuracy
Resin flow analysis allows engineers to visualize how plastic flows during the molding process.
By simulating this, they can identify potential issues such as air traps, weld lines, or uneven cooling, which can lead to defects.
Addressing these issues before production helps in creating more accurate and reliable designs.
Optimizing Production Efficiency
Using resin flow analysis, manufacturers can optimize production settings to ensure efficient use of materials and resources.
By adjusting factors such as injection speed, temperature, and pressure, companies can reduce cycle times and minimize waste.
Reducing Costs
Identifying and fixing potential issues early in the design phase can save a significant amount of money.
Resin flow analysis helps in preventing expensive defects and reducing material costs.
By optimizing the use of materials and energy, companies can produce high-quality products at a lower cost.
Improving Product Quality
High-quality products are essential for maintaining a company’s reputation and customer satisfaction.
Resin flow analysis helps ensure that products meet quality standards from the first batch.
By reducing the likelihood of defects and ensuring consistent quality, this process adds significant value to the end product.
Implementing Resin Flow Analysis in Your Design Process
Integrating resin flow analysis into your design process can significantly enhance the outcome of your plastic product designs.
Software Solutions
There are various software solutions available for conducting resin flow analysis.
These tools provide detailed simulations that help predict the behavior of plastic as it is injected into a mold.
By using these advanced tools, designers can make informed decisions and adjustments to their designs.
Collaboration Between Teams
Effective use of resin flow analysis requires strong communication and collaboration between design, engineering, and manufacturing teams.
By working together, these teams can identify potential issues early and make necessary adjustments.
Collaboration ensures a seamless transition from design to production, resulting in a more efficient manufacturing process.
Continuous Improvement
Incorporating resin flow analysis is not a one-time process; it is essential to continually analyze and adapt to new findings.
As new materials and technologies emerge, manufacturers must keep up to date to maintain efficiency and quality.
This process of continuous improvement helps companies stay competitive in an ever-evolving industry.
Conclusion
Understanding the fundamentals of plastic product design and the effective use of resin flow analysis is crucial for manufacturing high-quality products.
By focusing on material selection, thorough design considerations, and incorporating resin flow analysis, companies can optimize their manufacturing processes.
This leads to efficient production, reduced costs, and high-quality products that satisfy customer needs.
Embracing these practices can position a company as a leader in the field, ready to innovate and grow in a competitive market.
資料ダウンロード
QCD調達購買管理クラウド「newji」は、調達購買部門で必要なQCD管理全てを備えた、現場特化型兼クラウド型の今世紀最高の購買管理システムとなります。
ユーザー登録
調達購買業務の効率化だけでなく、システムを導入することで、コスト削減や製品・資材のステータス可視化のほか、属人化していた購買情報の共有化による内部不正防止や統制にも役立ちます。
NEWJI DX
製造業に特化したデジタルトランスフォーメーション(DX)の実現を目指す請負開発型のコンサルティングサービスです。AI、iPaaS、および先端の技術を駆使して、製造プロセスの効率化、業務効率化、チームワーク強化、コスト削減、品質向上を実現します。このサービスは、製造業の課題を深く理解し、それに対する最適なデジタルソリューションを提供することで、企業が持続的な成長とイノベーションを達成できるようサポートします。
オンライン講座
製造業、主に購買・調達部門にお勤めの方々に向けた情報を配信しております。
新任の方やベテランの方、管理職を対象とした幅広いコンテンツをご用意しております。
お問い合わせ
コストダウンが利益に直結する術だと理解していても、なかなか前に進めることができない状況。そんな時は、newjiのコストダウン自動化機能で大きく利益貢献しよう!
(Β版非公開)