- お役立ち記事
- Fundamentals of plastic welding and key points of laser welding and ultrasonic welding
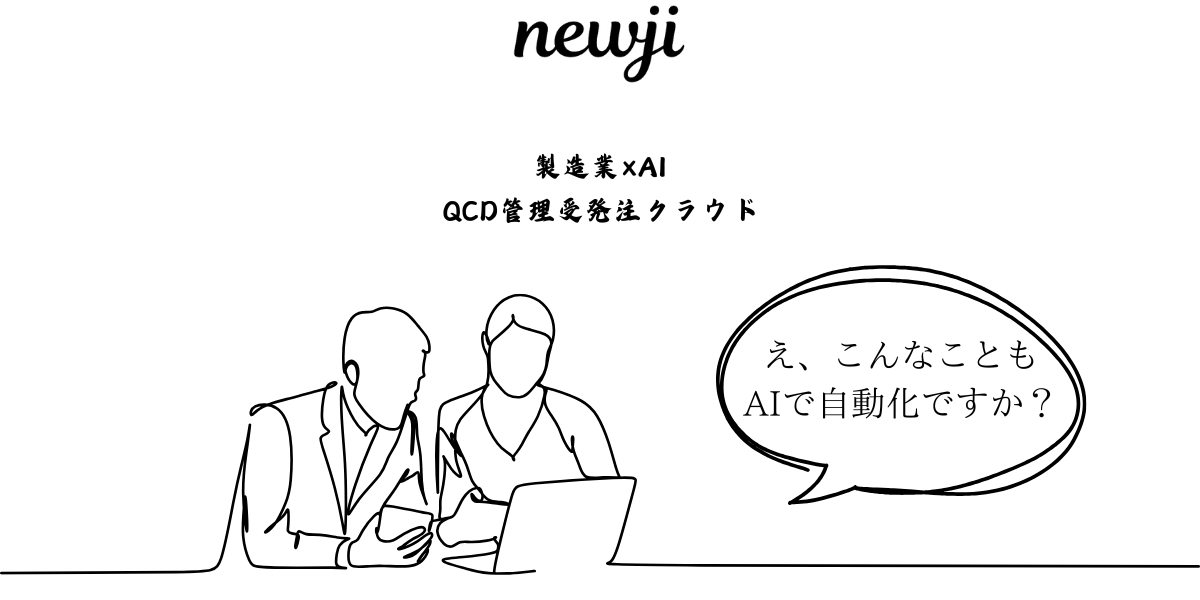
Fundamentals of plastic welding and key points of laser welding and ultrasonic welding
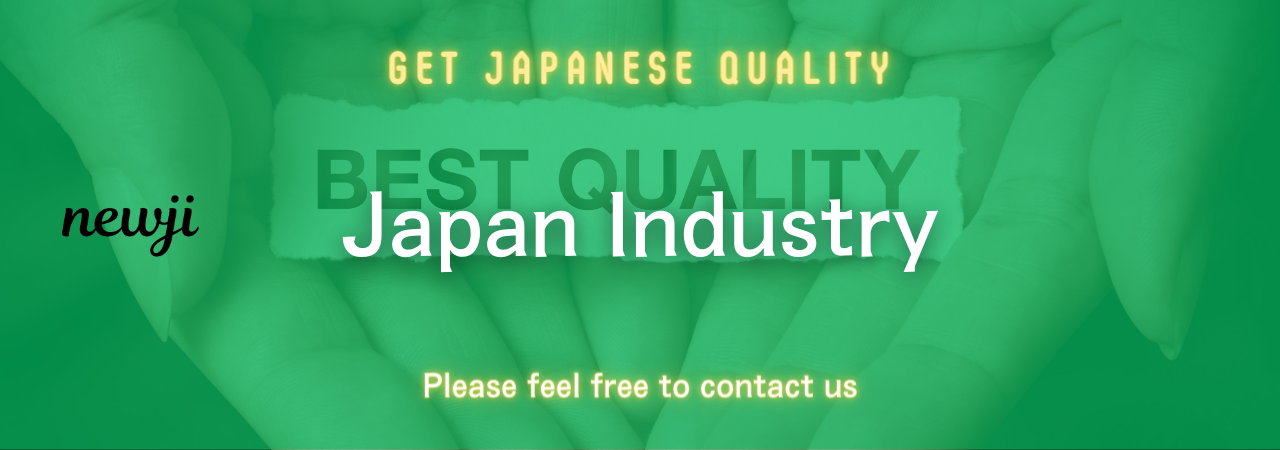
目次
Introduction to Plastic Welding
Plastic welding is a fascinating process that joins two pieces of plastic together using heat, pressure, or a combination of both.
Unlike metal welding, plastic welding does not involve melting the base material entirely.
Instead, it softens the surfaces that need to be joined, allowing them to fuse as they cool down.
This technique is widely used in various industries, from automotive to consumer electronics, due to its versatility and efficiency.
Types of Plastic Welding Techniques
There are several types of plastic welding techniques that cater to different materials and applications.
Some of the most common methods include hot air welding, hot plate welding, laser welding, and ultrasonic welding.
Each method has its own advantages and is suited to specific types of plastics and usage scenarios.
Hot Air Welding
Hot air welding, also known as hot gas welding, uses a stream of hot air to soften both the base material and a filler rod.
This technique is similar to torch welding in metals.
It is primarily used for welding thermoplastics and is commonly seen in the construction and repair of plastic tanks and piping systems.
Hot Plate Welding
Hot plate welding involves pressing the surfaces of two plastic parts against a heated plate.
Once the surfaces are sufficiently softened, the plate is removed, and the parts are pressed together to form a weld.
This method is ideal for large, flat plastic components and provides strong, leak-proof joints.
Laser Welding in Plastic Welding
Laser welding is a high-precision technique that uses a concentrated laser beam to join plastics.
It offers several advantages, particularly for intricate or delicate components.
How Laser Welding Works
In laser welding, the laser beam is focused on the joint area, causing the surfaces to melt and fuse.
The process can be finely controlled, allowing for precision and consistency in the welds.
This technique often involves minimal heat-affected areas, reducing the risk of thermal damage to the surrounding material.
Advantages of Laser Welding
One of the key advantages of laser welding is its speed.
It produces high-quality welds quickly, which is essential for mass production environments.
Additionally, laser welding does not require any filler material, making it a clean and efficient process.
It is also non-contact, which means the risk of contamination is minimal, and the laser can reach areas that might be difficult to access with other welding methods.
Applications of Laser Welding
Laser welding is widely used in industries requiring precision.
It is prevalent in the automotive industry for components such as airbag covers and taillight housings.
Additionally, it is used in medical device manufacturing, where precision and cleanliness are crucial.
The electronics industry also benefits from laser welding, particularly in microelectronics where small, precise welds are needed.
Ultrasonic Welding in Plastic Welding
Ultrasonic welding is another advanced technique used to join plastics.
It is particularly valued for its speed and cleanliness.
How Ultrasonic Welding Works
Ultrasonic welding uses high-frequency ultrasonic vibrations to generate heat at the joint area of the two plastic parts.
The heat causes the plastic to melt and fuse upon cooling.
The process is completed in a matter of seconds, making it one of the fastest welding techniques available.
Advantages of Ultrasonic Welding
This method offers several notable advantages.
Firstly, it is extremely fast, making it ideal for high-volume production environments.
Secondly, it requires no adhesives or solvents, resulting in a clean process with minimal environmental impact.
Another significant advantage is the strength and reliability of the welds, which are often comparable to the strength of the base material itself.
Applications of Ultrasonic Welding
Ultrasonic welding is widely used across many industries, including automotive, electronics, and medical device manufacturing.
In the automotive sector, it is used for welding components like instrument panels and door assemblies.
In electronics, it’s used for circuit boards and housing components.
In the medical field, ultrasonic welding is employed for assembling items such as catheters and filters, where precision and contamination-free conditions are necessary.
Key Considerations in Plastic Welding
When selecting a plastic welding method, several factors need to be considered to ensure a successful outcome.
Material Compatibility
Not all plastics can be welded with every technique.
Selecting a method that is compatible with the specific type of plastic being used is crucial.
Factors like melting temperature, chemical properties, and thickness play significant roles in determining the appropriate welding method.
Joint Design
The design of the joint can significantly impact the strength and durability of the weld.
Various joint designs, such as butt joints, lap joints, and tongue and groove joints, are used based on the application requirements.
Careful consideration of the joint design can prevent material failure and ensure long-lasting performance.
Quality Control
Maintaining strict quality control is essential in plastic welding to ensure the integrity and reliability of the welds.
Regular testing and inspections should be conducted to detect any defects or inconsistencies.
Techniques such as visual inspection, non-destructive testing, and destructive testing are often employed to assess weld quality.
Conclusion
Plastic welding plays a critical role in modern manufacturing processes, offering efficient and reliable methods to join plastic components.
Laser welding and ultrasonic welding stand out for their precision and speed, serving diverse industrial applications.
Understanding the fundamentals of these welding techniques and considering their specific requirements is crucial for achieving optimal results.
By doing so, manufacturers can ensure the production of high-quality, durable plastic products that meet the demands of today’s market.
資料ダウンロード
QCD調達購買管理クラウド「newji」は、調達購買部門で必要なQCD管理全てを備えた、現場特化型兼クラウド型の今世紀最高の購買管理システムとなります。
ユーザー登録
調達購買業務の効率化だけでなく、システムを導入することで、コスト削減や製品・資材のステータス可視化のほか、属人化していた購買情報の共有化による内部不正防止や統制にも役立ちます。
NEWJI DX
製造業に特化したデジタルトランスフォーメーション(DX)の実現を目指す請負開発型のコンサルティングサービスです。AI、iPaaS、および先端の技術を駆使して、製造プロセスの効率化、業務効率化、チームワーク強化、コスト削減、品質向上を実現します。このサービスは、製造業の課題を深く理解し、それに対する最適なデジタルソリューションを提供することで、企業が持続的な成長とイノベーションを達成できるようサポートします。
オンライン講座
製造業、主に購買・調達部門にお勤めの方々に向けた情報を配信しております。
新任の方やベテランの方、管理職を対象とした幅広いコンテンツをご用意しております。
お問い合わせ
コストダウンが利益に直結する術だと理解していても、なかなか前に進めることができない状況。そんな時は、newjiのコストダウン自動化機能で大きく利益貢献しよう!
(Β版非公開)