- お役立ち記事
- Fundamentals of plating process and key points to prevent problems
月間76,176名の
製造業ご担当者様が閲覧しています*
*2025年3月31日現在のGoogle Analyticsのデータより
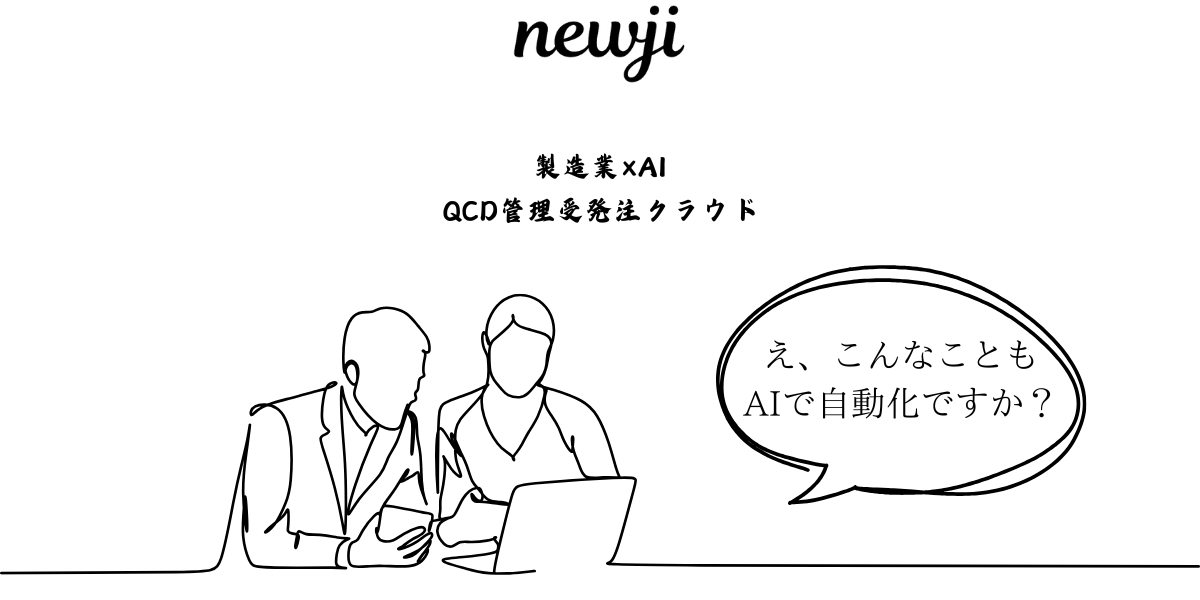
Fundamentals of plating process and key points to prevent problems
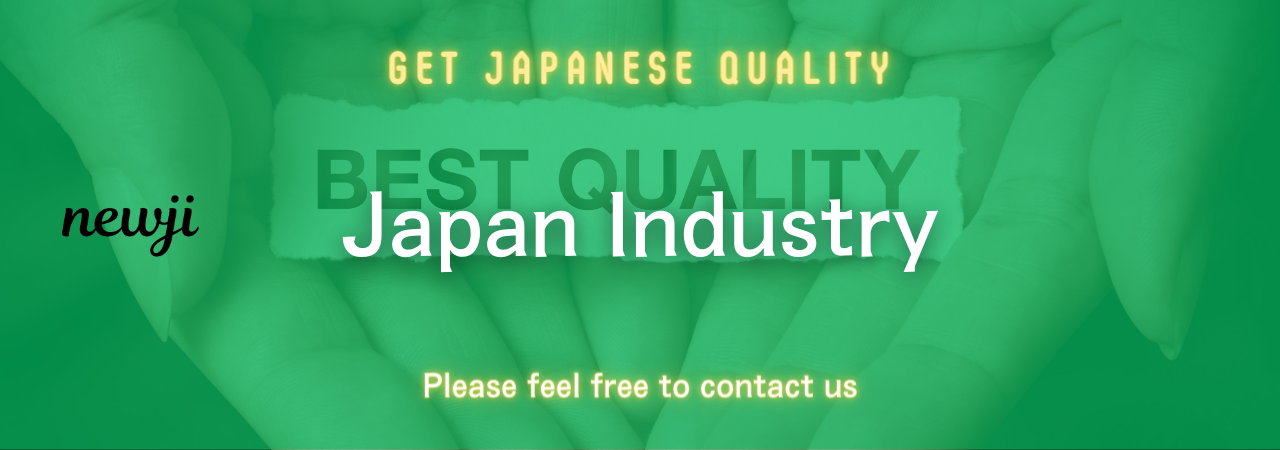
目次
Introduction to the Plating Process
The plating process is a fascinating method used to coat various materials with a thin layer of metal.
This technique extends the durability, enhances the appearance, and improves resistance to corrosion.
From electronics to jewelry, plating finds its applications across various industries, making it a vital part of manufacturing.
Plating can be accomplished through different methods, such as electroplating, electroless plating, and immersion plating.
Understanding the fundamentals of these methods is crucial to selecting the right process for specific applications.
Each technique has its unique qualities and can affect the final product in different ways.
Electroplating: A Popular Method
Electroplating is perhaps the most widely recognized method in the plating world.
This process involves using an electrical current to deposit metal ions onto a substrate.
During electroplating, the substrate to be plated acts as the cathode.
The metal to be deposited serves as the anode.
An electrolyte solution containing metal ions completes the circuit.
When an electrical current is introduced, the metal ions are attracted to the substrate, creating a metal coating.
Electroplating is popular because it allows for precise control over the thickness and uniformity of the metal layer.
This method is commonly used in automotive, aerospace, and electronics industries to enhance components’ performance and aesthetics.
Electroless Plating: An Even Coating
Unlike electroplating, electroless plating does not require electrical current.
This method involves a chemical reduction process that deposits metal onto the substrate.
Electroless plating provides a uniform coating, even on complex geometries and intricate surfaces.
It is especially beneficial for parts that require uniformity and can’t be connected to an electrical circuit.
In this process, the substrate is immersed in a solution containing metal ions, reducing agents, and stabilizers.
Through a series of chemical reactions, the metal ions are reduced and deposited on the substrate, forming a smooth layer.
Electroless plating is favored in industries like electronics, due to its ability to plate non-conductive surfaces.
Immersion Plating: Simple Yet Effective
Immersion plating, also known as displacement plating, is a simpler method compared to electroplating and electroless plating.
In this process, the substrate is immersed in a solution that contains metal ions, resulting in a spontaneous chemical reaction.
This method relies on the difference in electrode potentials between the substrate and the plating metal.
The metal ions are transferred onto the substrate surface, forming a thin metallic layer.
Immersion plating is often used for pre-treatments or specific applications where a thin layer is desirable.
It’s widely used in the electronics industry for coating PCBs with thin layers of precious metals.
Key Considerations in the Plating Process
Choosing the right plating method depends on various factors like the desired coating thickness, substrate material, and intended application.
Below are some key considerations that play a crucial role in successful plating:
1. Substrate Preparation
Proper substrate preparation is the foundation for successful plating.
Cleaning and degreasing the substrate removes impurities, ensuring an even coat.
Different methods, like acid cleaning or abrasive cleaning, might be chosen based on the material and plating technique.
Incorrect preparation may lead to adhesion problems, affecting the quality of the coating.
2. Bath Composition
The solution used in the plating bath is integral to the process.
Correct bath composition ensures the proper deposit rate and coating.
The solution should have a balanced mix of metal ions, pH regulators, stabilizers, and other additives.
Monitoring and maintaining the bath composition is essential to prevent defects and achieve consistent results.
3. Electrical Parameters
In electroplating, controlling voltage and current is vital for optimal results.
Too high or too low current can lead to uneven layers, waste of material, or power.
Adjusting current density allows control of deposition rate, essential for specific applications.
Careful control of these parameters stabilizes the process and ensures a quality finish.
4. Plating Time
The duration of the plating process affects the thickness and properties of the deposited layer.
Longer plating times may lead to thicker coats but can also contribute to defects if not managed.
It’s important to determine the correct plating time for each application.
This ensures that the desired thickness and quality are achieved without compromising integrity.
Preventing Common Plating Problems
Plating processes may run into challenges if proper precautions are not observed.
Some common issues and ways to solve them are highlighted below:
1. Poor Adhesion
Poor adhesion results from improper substrate preparation or incompatible materials.
Solution: Ensure surfaces are clean and etched before plating to resolve this issue.
2. Pitting and Roughness
This is often caused by contamination in the plating bath or incorrect bath composition.
Solution: Regularly check and maintain the bath, using filtration to prevent impurities.
3. Uneven Coating
Uneven coating may be a result of improper electrical parameters or plating time.
Solution: Carefully monitor current density and adjust plating time to achieve uniformity.
4. Discoloration
Discoloration can occur due to bath instability or contamination.
Solution: Maintain bath stability through regular checks and additives to prevent changes in color.
Conclusion
The plating process, whether through electroplating, electroless plating, or immersion plating, is essential for many industries.
Understanding and applying the fundamentals helps in selecting the right methods for specific needs.
By considering key factors such as substrate preparation, bath composition, and electrical parameters, manufacturers can achieve superior results.
Employing best practices and troubleshooting common problems ensures the longevity and performance of the plated material.
With careful attention to these basics, success in the plating process is achievable, enhancing both the aesthetics and functional qualities of materials.
資料ダウンロード
QCD管理受発注クラウド「newji」は、受発注部門で必要なQCD管理全てを備えた、現場特化型兼クラウド型の今世紀最高の受発注管理システムとなります。
ユーザー登録
受発注業務の効率化だけでなく、システムを導入することで、コスト削減や製品・資材のステータス可視化のほか、属人化していた受発注情報の共有化による内部不正防止や統制にも役立ちます。
NEWJI DX
製造業に特化したデジタルトランスフォーメーション(DX)の実現を目指す請負開発型のコンサルティングサービスです。AI、iPaaS、および先端の技術を駆使して、製造プロセスの効率化、業務効率化、チームワーク強化、コスト削減、品質向上を実現します。このサービスは、製造業の課題を深く理解し、それに対する最適なデジタルソリューションを提供することで、企業が持続的な成長とイノベーションを達成できるようサポートします。
製造業ニュース解説
製造業、主に購買・調達部門にお勤めの方々に向けた情報を配信しております。
新任の方やベテランの方、管理職を対象とした幅広いコンテンツをご用意しております。
お問い合わせ
コストダウンが利益に直結する術だと理解していても、なかなか前に進めることができない状況。そんな時は、newjiのコストダウン自動化機能で大きく利益貢献しよう!
(β版非公開)