- お役立ち記事
- Fundamentals of PM motor control technology and its application to motor control design and its key points
月間76,176名の
製造業ご担当者様が閲覧しています*
*2025年3月31日現在のGoogle Analyticsのデータより
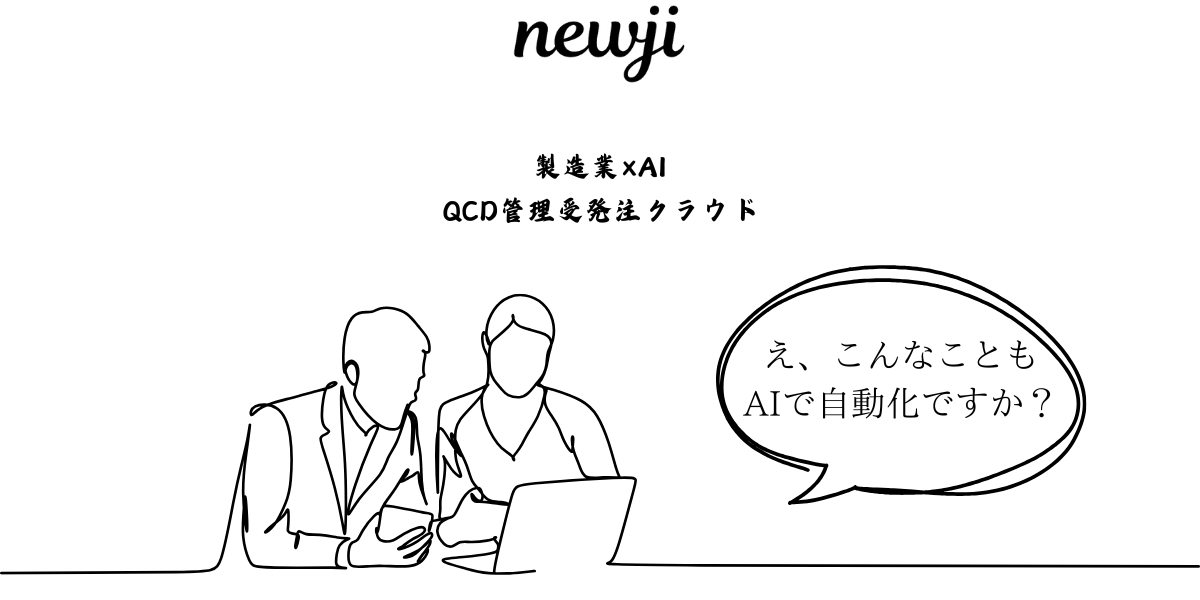
Fundamentals of PM motor control technology and its application to motor control design and its key points
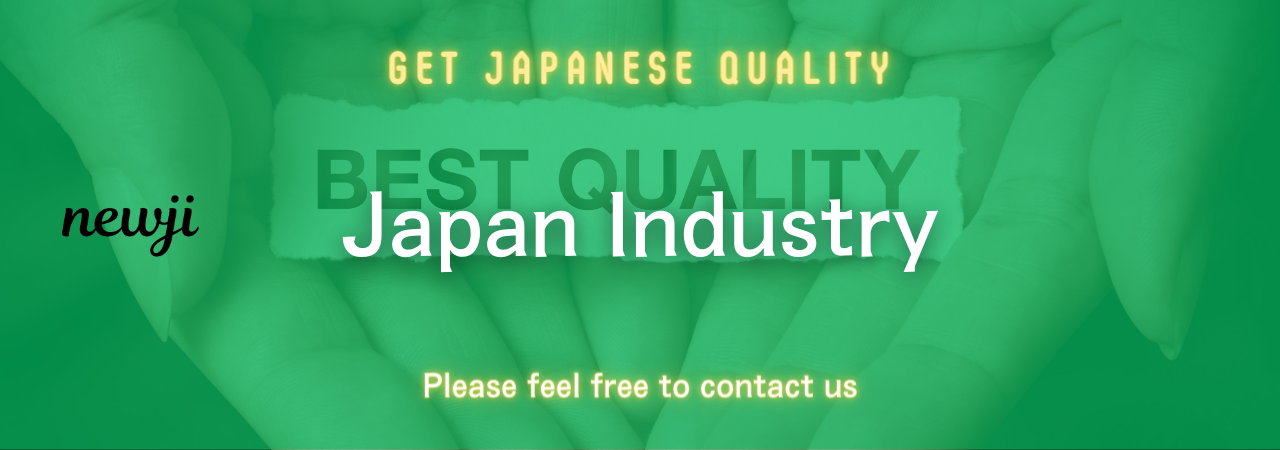
目次
Introduction to PM Motor Control Technology
Permanent Magnet (PM) motor control technology plays a crucial role in the efficient and precise operation of motors used in various applications.
As industries continue to demand higher efficiency and performance from their motor-driven systems, understanding the fundamentals of PM motor control becomes essential.
This article will explore the basics of PM motor control technology and discuss its application in motor control design and the key points that engineers should focus on.
What is PM Motor Control?
PM motor control refers to the technology used to regulate the performance of permanent magnet motors.
These motors utilize permanent magnets embedded in their rotor to produce a consistent magnetic field, which in turn enables efficient operation.
PM motors are known for their high torque density, reliability, and efficiency compared to other types of motors such as induction motors.
The primary goal of PM motor control is to ensure the motor operates efficiently while meeting specific performance criteria.
This involves managing parameters such as speed, torque, and current to optimize the motor’s performance under various load conditions.
Types of PM Motors
There are several types of PM motors, each with its unique characteristics and applications.
The most common types include:
1. **Brushless DC Motors (BLDC):** These motors are widely used in applications that require high efficiency and reliability.
BLDC motors have a permanent magnet rotor and a stator with wound coils.
They are known for their low maintenance due to lack of brushes and commutators.
2. **Permanent Magnet Synchronous Motors (PMSM):** PMSMs are used in applications that demand precise control of speed and position.
They operate at synchronous speed and are widely used in industrial applications.
3. **PM Stepper Motors:** Stepper motors offer precise control of motion, making them ideal for applications such as robotics and precise positioning systems.
They work by energizing coils in a sequence to move the motor in discrete steps.
The Control Mechanism of PM Motors
To effectively control a PM motor, an appropriate control mechanism must be put in place.
This involves using controllers and algorithms to ensure that the motor functions as desired.
Here are some key components and considerations:
Controllers
Controllers are devices that manage the operation of PM motors by regulating voltage, current, and speed.
They receive input from sensors and execute control algorithms to adjust the motor’s performance.
Some commonly used controllers in PM motor applications include:
– **Field-Oriented Control (FOC):** FOC is a popular control method for PMSMs and BLDCs, offering precise control of speed and torque by manipulating the rotor magnetic field.
– **Direct Torque Control (DTC):** DTC is an advanced form of motor control that directly regulates the motor’s torque and flux to achieve rapid response and high efficiency.
– **Scalar Control:** Often used in simple applications, scalar control involves adjusting the voltage and frequency applied to the motor to control its speed.
Sensors
Sensors are crucial for providing feedback to the controllers about the motor’s current state, such as speed, position, and torque.
Common sensors used in PM motor control include:
– **Hall Effect Sensors:** These are typically used for rotor position detection in BLDC motors.
– **Encoders:** High precision applications use encoders to provide exact speed and position feedback.
– **Current Sensors:** Measure the current flowing through the motor to ensure safe and efficient operation.
Applications of PM Motor Control
PM motors are used in a wide range of applications across different industries due to their superior efficiency and performance.
Some of the prominent applications include:
Industrial Automation
In industrial settings, PM motors are used for tasks such as robotics, conveyor systems, and machine tools where precise speed and position control are paramount.
The reliability and efficiency of PM motors make them ideal for round-the-clock operations in automation.
Electric Vehicles
With the shift towards electrification, PM motors have become a preferred choice for electric vehicles (EVs) due to their high power density and efficiency.
They contribute to longer driving ranges and better performance compared to traditional internal combustion engines.
Consumer Electronics
PM motor control technology is also leveraged in consumer electronics for applications such as cooling fans, hard drives, and other devices requiring quiet operation and efficient power use.
Key Considerations in PM Motor Control Design
Designing an effective PM motor control system involves several key considerations to ensure optimal performance and reliability:
Efficiency
Efficiency is a critical consideration in motor control design.
High efficiency reduces energy consumption and operational costs while minimizing heat generation that can adversely affect the motor’s lifespan.
Reliability
Reliability is vital, especially in applications where downtime is unacceptable.
The motor control system must be robust and capable of handling varying load conditions and environmental challenges.
Cost
Cost considerations involve not just the initial investment but also the long-term operating expenses.
Selecting cost-effective components and optimizing energy use can result in significant savings over time.
Scalability
As technological advancements continue, the need for scalable motor control solutions becomes apparent.
Designs should be adaptable to incorporate future updates or changes without requiring complete overhauls.
Conclusion
Understanding the fundamentals of PM motor control technology and its applications is essential for engineers and designers working in fields that require precise and efficient motor control.
By focusing on key design considerations such as efficiency, reliability, cost, and scalability, engineers can create effective PM motor control solutions that meet the growing demands of modern applications.
資料ダウンロード
QCD管理受発注クラウド「newji」は、受発注部門で必要なQCD管理全てを備えた、現場特化型兼クラウド型の今世紀最高の受発注管理システムとなります。
ユーザー登録
受発注業務の効率化だけでなく、システムを導入することで、コスト削減や製品・資材のステータス可視化のほか、属人化していた受発注情報の共有化による内部不正防止や統制にも役立ちます。
NEWJI DX
製造業に特化したデジタルトランスフォーメーション(DX)の実現を目指す請負開発型のコンサルティングサービスです。AI、iPaaS、および先端の技術を駆使して、製造プロセスの効率化、業務効率化、チームワーク強化、コスト削減、品質向上を実現します。このサービスは、製造業の課題を深く理解し、それに対する最適なデジタルソリューションを提供することで、企業が持続的な成長とイノベーションを達成できるようサポートします。
製造業ニュース解説
製造業、主に購買・調達部門にお勤めの方々に向けた情報を配信しております。
新任の方やベテランの方、管理職を対象とした幅広いコンテンツをご用意しております。
お問い合わせ
コストダウンが利益に直結する術だと理解していても、なかなか前に進めることができない状況。そんな時は、newjiのコストダウン自動化機能で大きく利益貢献しよう!
(β版非公開)