- お役立ち記事
- Fundamentals of position control and force control in robot manipulators and their application to high-precision control system design
月間76,176名の
製造業ご担当者様が閲覧しています*
*2025年3月31日現在のGoogle Analyticsのデータより
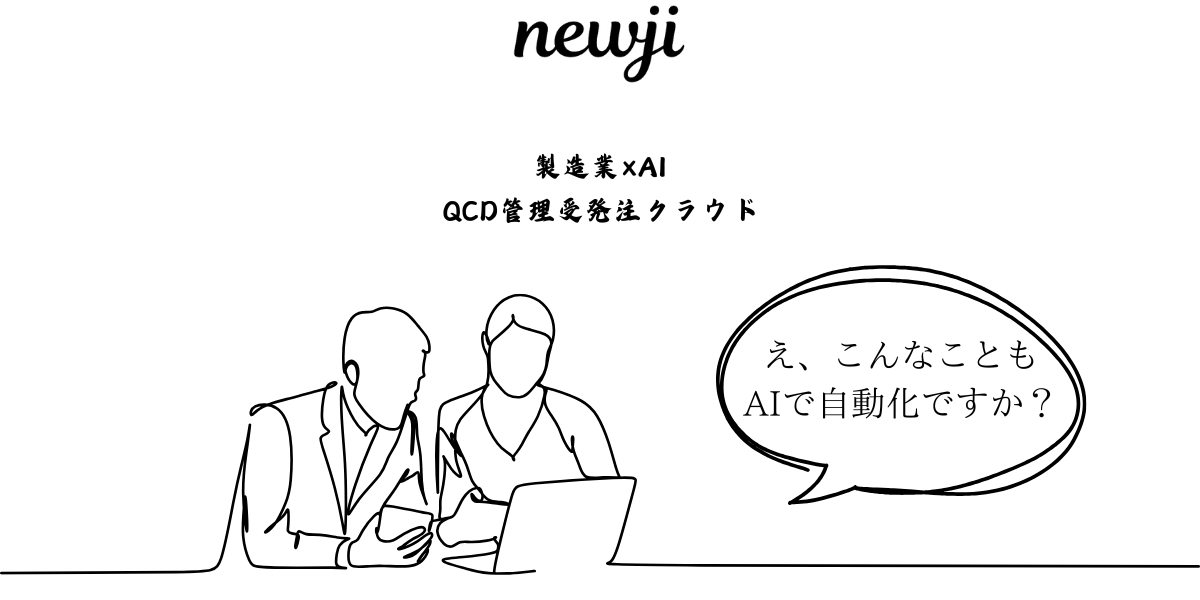
Fundamentals of position control and force control in robot manipulators and their application to high-precision control system design
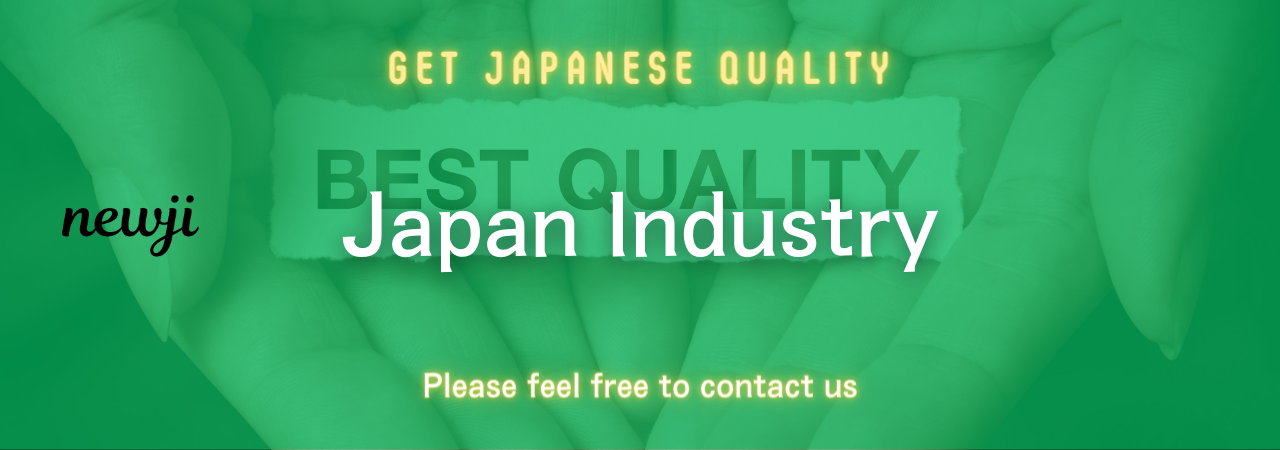
目次
Introduction to Robot Manipulators
Robot manipulators are essential components of modern automation and robotics systems.
They are widely used in industries such as manufacturing, healthcare, and logistics due to their ability to handle tasks with precision and efficiency.
A fundamental aspect of operating robot manipulators involves position control and force control, which are crucial for achieving high precision in control system design.
Understanding Position Control
Position control is a technique used to accurately manage the location and orientation of a robot manipulator.
The primary objective is to ensure that the manipulator reaches and remains at a desired position without deviation.
This is typically achieved through the use of sensors and feedback mechanisms such as encoders which continuously monitor the robot’s position.
Position control involves the calculation of position errors and the generation of corrective actions to minimize these errors.
Proportional-Integral-Derivative (PID) controllers are commonly employed in position control systems.
They adjust the manipulator’s movements based on the difference between the desired and actual positions.
For applications where high precision is required, position control must be finely tuned.
This includes selecting appropriate controller gains, optimizing feedback loops, and identifying any sources of mechanical backlash or friction that could affect the manipulator’s accuracy.
The Role of Force Control
While position control focuses on achieving a precise position, force control is concerned with regulating the force and torque applied by the robot manipulator.
Force control is especially important in tasks involving interaction with the environment, such as assembly or machining.
There are two primary methods of force control: impedance control and admittance control.
Impedance control adjusts the manipulator’s position based on the interaction force measured, providing a compliant response.
Admittance control, on the other hand, modifies the desired force output based on the position error, effectively making the manipulator act as if it has a certain mechanical impedance.
Force control strategies are vital in scenarios where delicate handling is required or where the robot must interact safely with humans.
For instance, in industrial applications, excessive force can lead to damage of components or injury to human operators.
Integration of Position and Force Control
In many advanced applications, it is necessary to integrate both position and force control to achieve optimal performance.
A typical example is in robotic surgery or complex assembly tasks, where both precise movements and controlled force application are needed.
Hybrid control systems combine the benefits of both strategies, enabling the robot manipulator to maintain an accurate position while also effectively controlling interaction forces.
These systems use a combination of sensors and actuators to dynamically adjust the control parameters based on real-time data.
The integration of position and force control ensures that manipulators can adapt to dynamic environments and unexpected interactions, enhancing their versatility and effectiveness in various applications.
High-Precision Control System Design
Designing control systems for high-precision tasks requires a deep understanding of both position and force control principles.
Engineers must develop algorithms that accurately model the behavior of the robot manipulator and its interaction with the environment.
Control system design involves choosing the right hardware and software components, such as high-resolution sensors and real-time processors.
These components enable precise measurement and control of the manipulator’s motion and interaction forces.
Advanced techniques, like model predictive control and machine learning, are increasingly used to improve the performance of control systems.
These methods allow for adaptive control strategies that can anticipate changes and adjust accordingly, further enhancing the precision and reliability of the system.
Applications in Industry
The application of high-precision control systems is vast.
In the automotive industry, robot manipulators equipped with sophisticated control systems are used for tasks like welding, painting, and assembly, ensuring high-quality production with reduced downtime.
In healthcare, robotic systems for surgery rely on precise control to perform minimally invasive procedures with great accuracy.
The integration of position and force control is critical in these scenarios to handle delicate tissues without causing damage.
Challenges and Future Trends
Despite the advancements, challenges remain in the field of robotic control systems.
Ensuring stability and robustness in dynamic environments is an ongoing concern, as is the reduction of latency in control responses.
Future trends in robot manipulator control will likely include the increasing use of AI and IoT technologies to create smarter, more connected systems.
These technologies promise to improve the adaptability and predictive capabilities of control systems, opening new avenues for automation and human-robot collaboration.
Conclusion
The fundamentals of position control and force control are central to the successful operation of robot manipulators.
These principles not only ensure the precise execution of tasks but also enhance safety and reliability across various applications.
As technology advances, the integration of these control systems with emerging technologies will continue to evolve, driving innovation and efficiency in industries worldwide.
Understanding and mastering these fundamental concepts is crucial for engineers and researchers working to design the next generation of robotic systems.
資料ダウンロード
QCD管理受発注クラウド「newji」は、受発注部門で必要なQCD管理全てを備えた、現場特化型兼クラウド型の今世紀最高の受発注管理システムとなります。
ユーザー登録
受発注業務の効率化だけでなく、システムを導入することで、コスト削減や製品・資材のステータス可視化のほか、属人化していた受発注情報の共有化による内部不正防止や統制にも役立ちます。
NEWJI DX
製造業に特化したデジタルトランスフォーメーション(DX)の実現を目指す請負開発型のコンサルティングサービスです。AI、iPaaS、および先端の技術を駆使して、製造プロセスの効率化、業務効率化、チームワーク強化、コスト削減、品質向上を実現します。このサービスは、製造業の課題を深く理解し、それに対する最適なデジタルソリューションを提供することで、企業が持続的な成長とイノベーションを達成できるようサポートします。
製造業ニュース解説
製造業、主に購買・調達部門にお勤めの方々に向けた情報を配信しております。
新任の方やベテランの方、管理職を対象とした幅広いコンテンツをご用意しております。
お問い合わせ
コストダウンが利益に直結する術だと理解していても、なかなか前に進めることができない状況。そんな時は、newjiのコストダウン自動化機能で大きく利益貢献しよう!
(β版非公開)