- お役立ち記事
- Fundamentals of powder, improving fluidity and filling properties, and key points for mixing powder and granular materials
Fundamentals of powder, improving fluidity and filling properties, and key points for mixing powder and granular materials
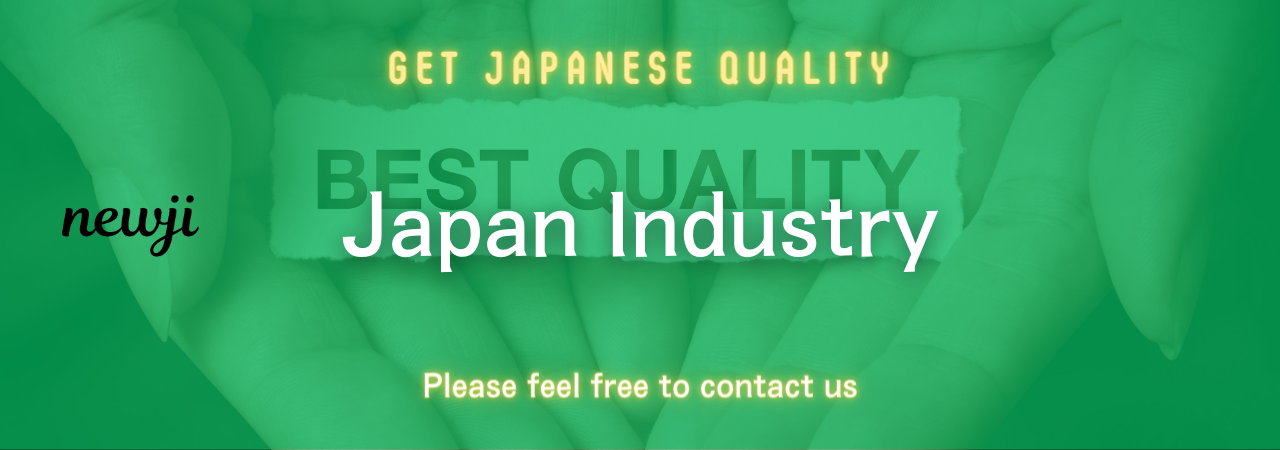
目次
Understanding the Basics of Powder
Powder is an essential component in various industries, including pharmaceuticals, food, and manufacturing.
Understanding its fundamentals can significantly impact the efficiency of any process involving powder.
Simply put, powder is a collection of fine particles that can flow freely but may clump together when compressed.
The properties of powder can vary based on particle size, shape, and the presence of moisture.
A crucial aspect of working with powder is its flowability, or fluidity.
This characteristic determines how easy or challenging it is to handle and transport powdered materials.
Good fluidity ensures smooth operations in processes like mixing, filling, and conveying.
Several factors influence fluidity, such as particle size distribution and surface texture.
Small, spherical particles tend to have better fluidity due to reduced friction, while irregular shapes or larger particles may lead to poor flow.
Improving Fluidity and Filling Properties
Achieving better fluidity is pivotal for efficient powder handling.
Techniques to improve fluidity include adjusting the particle size distribution and treating the particles’ surface with specific agents.
Altering the environment where powder is stored or processed, such as controlling humidity, can also affect its fluidity.
In industries that involve packaging or tablets, filling properties are equally important.
This refers to how well a powder packs into containers or molds, which directly impacts the outcome of the final product.
Ensuring a consistent and predictable filling process minimizes waste and product variation.
Surface coatings can be used to enhance the flow properties of powders.
These coatings reduce particle friction and prevent them from sticking together.
Additionally, incorporating flow aids or additives can also help improve fluidity.
These substances act as lubricants, reducing inter-particle forces and promoting smoother flow.
Utilizing Specialized Equipment
Specialized equipment plays a significant role in improving fluidity and filling properties.
For instance, vibratory feeders can help powders flow more consistently by applying small vibrations to dislodge particles.
Hoppers with specific angles can prevent powder hang-ups and ensure complete discharge.
Incorporating air into powder can also improve its flow characteristics.
Aeration devices strategically introduce air, making the powder behave more like a fluid.
This method is particularly beneficial in preventing arching or ratholing in silos and bins.
Mixing Powder and Granular Materials
Mixing powders and granular materials is a common practice across several industries.
It requires careful attention to achieve a homogeneous blend, vital for product consistency and quality.
The key to effective mixing lies in understanding the properties of both the powder and the granular material.
Different mixing methods suit different types of powders and granules.
Tumbling mixers are excellent for gentle blending, using rotation to combine materials.
On the other hand, shear mixers apply mechanical force to produce a more aggressive mix, ideal for materials that are difficult to blend.
One of the primary challenges when mixing powders and granules is preventing segregation.
Segregation occurs when particles separate based on size, shape, or density, resulting in an uneven mix.
This can be minimized by controlling the particle size distribution and selecting the appropriate mixing equipment.
Key Points for Successful Mixing
Several strategies can enhance the effectiveness of mixing processes.
Adding liquids or binders can help aggregate particles, reducing the chances of segregation.
While this method can improve uniformity, it requires care to avoid forming lumps.
The order of component addition is another critical consideration.
By introducing powders and granular materials at different stages or blending them in stages, you can achieve a more even distribution.
Regular monitoring of the mix ensures products meet industry standards.
Using sampling techniques to verify the homogeneity of the batch can guide necessary adjustments during the process.
Conclusion
In summary, understanding and improving the behavior of powders is crucial for efficient industrial operations.
Optimizing fluidity and filling properties ensures smooth processing, while careful mixing enables consistency and quality in the final product.
Employing strategic methods and equipment can significantly enhance the performance of powders and granular materials.
Attention to detail in these processes can lead to cost savings and improved product quality in various applications.
資料ダウンロード
QCD調達購買管理クラウド「newji」は、調達購買部門で必要なQCD管理全てを備えた、現場特化型兼クラウド型の今世紀最高の購買管理システムとなります。
ユーザー登録
調達購買業務の効率化だけでなく、システムを導入することで、コスト削減や製品・資材のステータス可視化のほか、属人化していた購買情報の共有化による内部不正防止や統制にも役立ちます。
NEWJI DX
製造業に特化したデジタルトランスフォーメーション(DX)の実現を目指す請負開発型のコンサルティングサービスです。AI、iPaaS、および先端の技術を駆使して、製造プロセスの効率化、業務効率化、チームワーク強化、コスト削減、品質向上を実現します。このサービスは、製造業の課題を深く理解し、それに対する最適なデジタルソリューションを提供することで、企業が持続的な成長とイノベーションを達成できるようサポートします。
オンライン講座
製造業、主に購買・調達部門にお勤めの方々に向けた情報を配信しております。
新任の方やベテランの方、管理職を対象とした幅広いコンテンツをご用意しております。
お問い合わせ
コストダウンが利益に直結する術だと理解していても、なかなか前に進めることができない状況。そんな時は、newjiのコストダウン自動化機能で大きく利益貢献しよう!
(Β版非公開)