- お役立ち記事
- Fundamentals of powder metallurgy and high-performance technology
月間76,176名の
製造業ご担当者様が閲覧しています*
*2025年3月31日現在のGoogle Analyticsのデータより
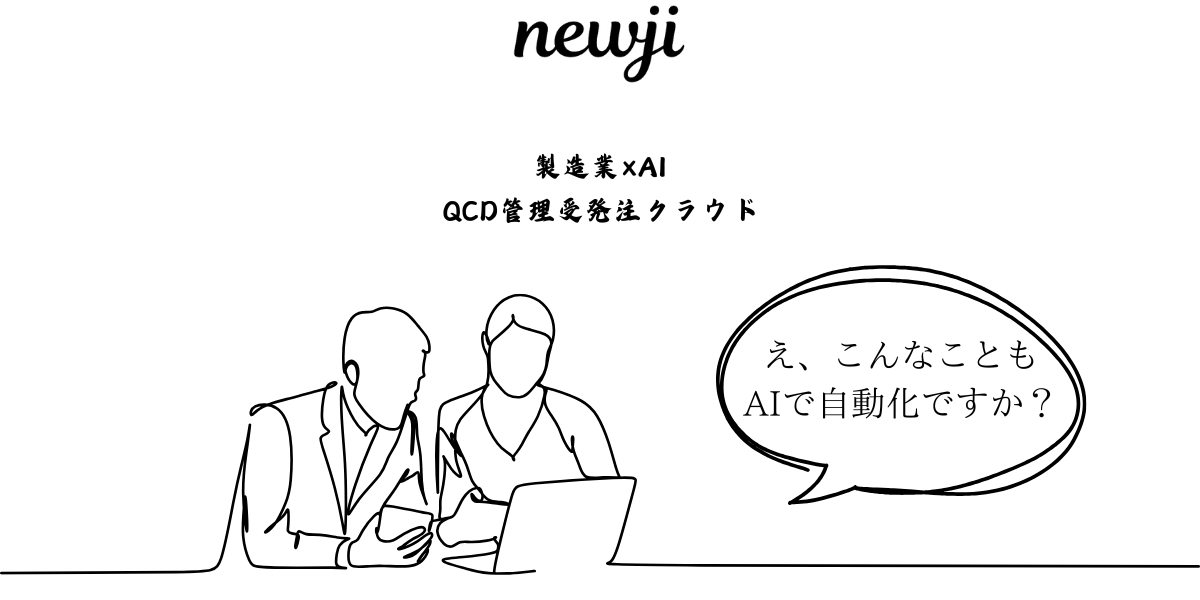
Fundamentals of powder metallurgy and high-performance technology
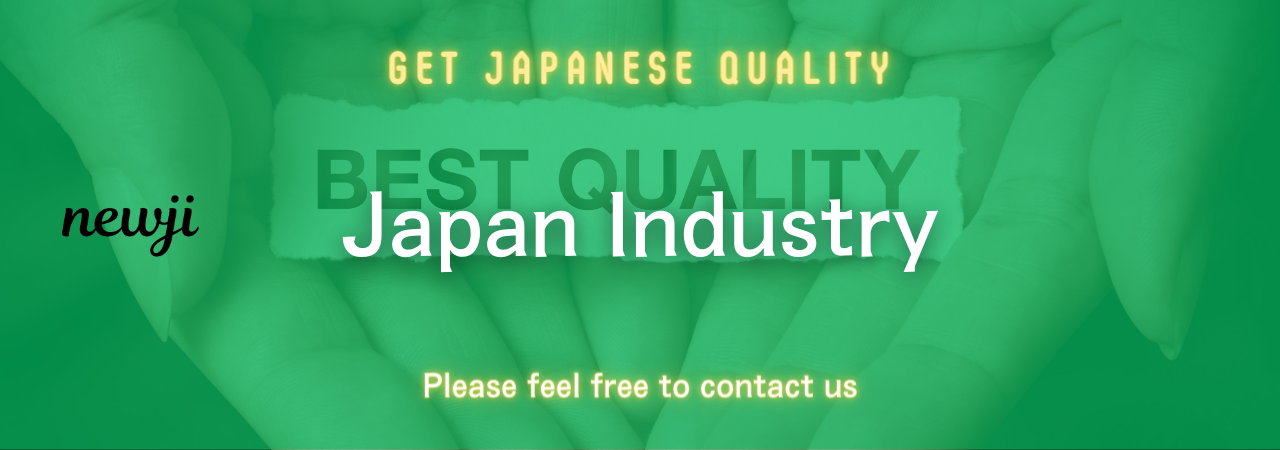
目次
Understanding Powder Metallurgy
Powder metallurgy is an advanced manufacturing process that focuses on the production and utilization of metal powders to create various products.
This methodology involves the compression of metal powders into a desired shape and then heating them to solidify the structure without melting it completely.
As one of the most efficient ways to produce metal parts, powder metallurgy offers significant advantages in precision, cost-effectiveness, and material conservation.
The Basic Steps in Powder Metallurgy
The powder metallurgy process typically follows a series of carefully controlled steps.
Understanding these steps can provide insights into how this technology manages to produce high-quality components efficiently.
Firstly, the preparation of metal powders is crucial.
Powders are produced through different methods such as atomization, reduction, or mechanical alloying.
Atomization involves breaking down molten metal into fine particles, while reduction involves converting metal oxides into powders.
Mechanical alloying allows for the combination of different metals to produce alloys with unique properties.
Once the metal powders are ready, they undergo mixing and blending.
The powders are carefully mixed to ensure uniformity and consistency in the final product.
Additives such as lubricants or binders may also be included to aid in the ease of the pressing stage.
The mixed powders are then compacted into the desired shape using a die.
This step is known as pressing, and it compacts the powder into a solid form called a green compact.
The pressing operation is pivotal as it influences the strength and properties of the final product.
After pressing, the green compacts are subjected to a process called sintering.
Sintering heats the compacted powder to a temperature just below its melting point.
This step allows the particles to bond together, enhancing the strength and integrity of the material.
Applications of Powder Metallurgy
Powder metallurgy has become a vital component across various industries due to its versatility and efficiency in producing components.
The automotive industry, in particular, benefits significantly from this technology.
Manufacturers use powder metallurgy to create components like gears, bearings, and bushings, which are essential for enhancing vehicle performance and fuel efficiency.
In the electronics industry, powder metallurgy is used to produce components with high thermal and electrical conductivity.
These properties are crucial for ensuring that electronic devices operate optimally and remain reliable over time.
The healthcare industry also benefits from powder metallurgy techniques, particularly in the production of porous implants and surgical instruments.
The ability to precisely control the microstructure of materials makes it possible to create customized solutions tailored to specific medical needs.
Advantages of Powder Metallurgy
Powder metallurgy offers several advantages over traditional manufacturing methods, making it a preferred choice for high-performance applications.
One of the most significant benefits is material conservation.
The process generates minimal waste, as metal powders can be recycled and reused, leading to cost savings and environmental sustainability.
Furthermore, powder metallurgy allows for the precise control of material properties.
Manufacturers can produce components with specific characteristics, such as enhanced strength, wear resistance, or magnetic properties, by manipulating the composition and structure of the powders.
The flexibility in design afforded by powder metallurgy is another major advantage.
Complex shapes that would be challenging or impossible to achieve through other methods can be easily crafted using powder metallurgy techniques.
This capability is particularly important in fields that demand intricate designs and high precision.
High-Performance Technologies in Powder Metallurgy
Advancements in powder metallurgy have led to the development of high-performance technologies that broaden its scope and applicability.
One such technology is metal injection molding (MIM), which combines the versatility of plastic injection molding with the strength and properties of metals.
MIM is ideal for producing small, complex components with a high degree of precision.
Another significant advancement is the development of additive manufacturing (AM) techniques within powder metallurgy.
Also known as 3D printing, these techniques build components layer by layer using metal powders.
This innovative approach allows for rapid prototyping and the creation of designs that were previously unattainable.
The integration of computer-aided design (CAD) and computer-aided manufacturing (CAM) software is also enhancing the capabilities of powder metallurgy.
These tools enable engineers to simulate the manufacturing process, optimize designs, and predict the performance of components before production, reducing the time and cost associated with trial and error.
The Future of Powder Metallurgy
As technology continues to evolve, the future of powder metallurgy is promising.
Emerging materials and techniques are likely to further expand its applications and increase its efficiency.
Researchers are exploring the potential of using nanoscale powders to create materials with even more remarkable properties.
Sustainability is another area where powder metallurgy is expected to make significant strides.
With an increasing focus on environmentally friendly manufacturing processes, powder metallurgy’s ability to minimize waste and energy consumption will likely become an even more valued asset.
The combination of technological advancements, environmental considerations, and the growing demand for high-performance materials positions powder metallurgy as an essential component of modern manufacturing.
By continuing to innovate and adapt, the industry can meet the evolving needs of various sectors and stay at the forefront of technological progress.
In summary, powder metallurgy bridges the gap between traditional manufacturing and cutting-edge technology, offering efficient, precise, and sustainable solutions.
Its fundamentals and potential for high-performance applications make it an exciting field with boundless opportunities for future development.
資料ダウンロード
QCD管理受発注クラウド「newji」は、受発注部門で必要なQCD管理全てを備えた、現場特化型兼クラウド型の今世紀最高の受発注管理システムとなります。
ユーザー登録
受発注業務の効率化だけでなく、システムを導入することで、コスト削減や製品・資材のステータス可視化のほか、属人化していた受発注情報の共有化による内部不正防止や統制にも役立ちます。
NEWJI DX
製造業に特化したデジタルトランスフォーメーション(DX)の実現を目指す請負開発型のコンサルティングサービスです。AI、iPaaS、および先端の技術を駆使して、製造プロセスの効率化、業務効率化、チームワーク強化、コスト削減、品質向上を実現します。このサービスは、製造業の課題を深く理解し、それに対する最適なデジタルソリューションを提供することで、企業が持続的な成長とイノベーションを達成できるようサポートします。
製造業ニュース解説
製造業、主に購買・調達部門にお勤めの方々に向けた情報を配信しております。
新任の方やベテランの方、管理職を対象とした幅広いコンテンツをご用意しております。
お問い合わせ
コストダウンが利益に直結する術だと理解していても、なかなか前に進めることができない状況。そんな時は、newjiのコストダウン自動化機能で大きく利益貢献しよう!
(β版非公開)