- お役立ち記事
- Fundamentals of powder metallurgy/MIM, applications and key points for product development
月間76,176名の
製造業ご担当者様が閲覧しています*
*2025年3月31日現在のGoogle Analyticsのデータより
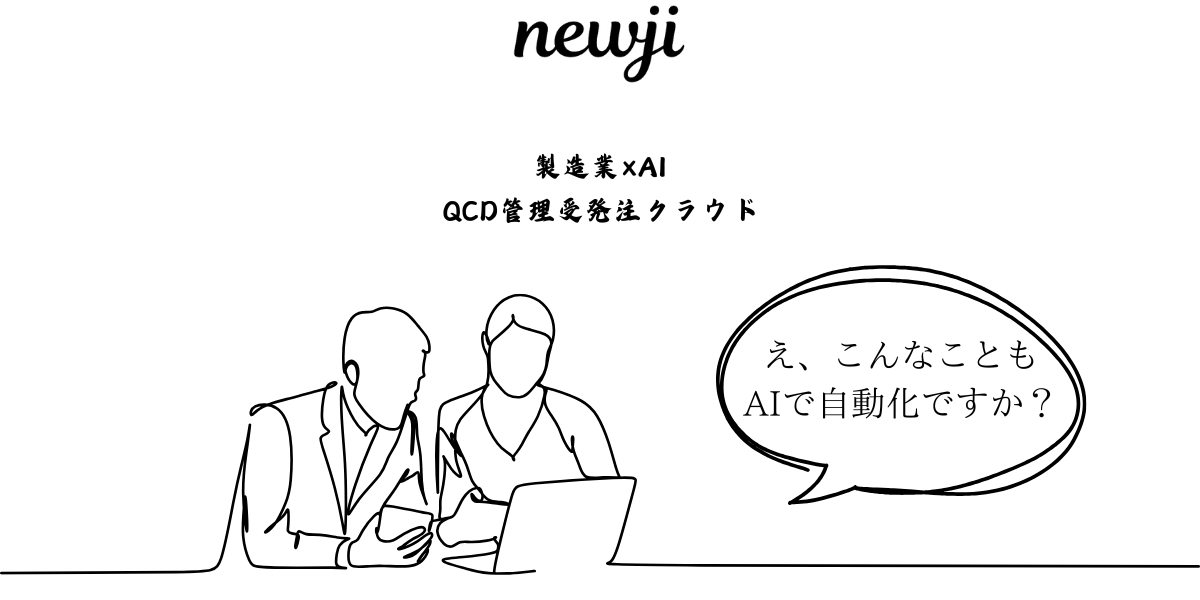
Fundamentals of powder metallurgy/MIM, applications and key points for product development
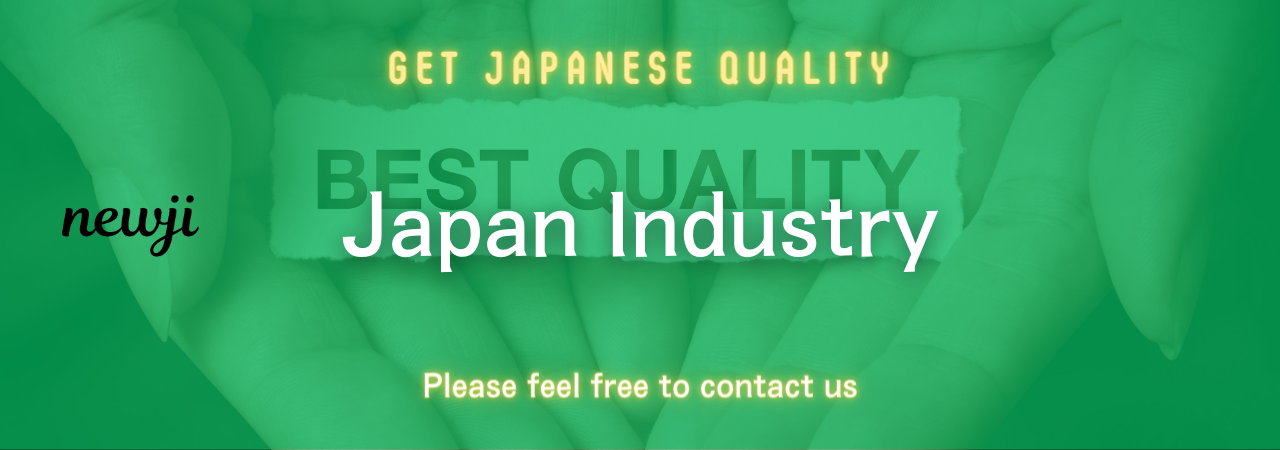
目次
Understanding Powder Metallurgy and MIM
Powder metallurgy, often abbreviated as PM, is a process where metal powders are compacted and then sintered to create solid metal components.
This approach allows for precise control over the material composition and structure, leading to parts that boast high levels of durability and precision.
Metal Injection Molding (MIM) is a subset of powder metallurgy.
This technique combines the versatility of plastic injection molding with the strength and integrity of metals.
MIM is particularly well-suited for the production of small, complex shapes that would be difficult to make through traditional machining methods.
Powder metallurgy, including MIM, serves as a cornerstone in modern manufacturing thanks to its ability to reduce waste, improve structural integrity, and facilitate innovative designs.
The Process of Powder Metallurgy
The powder metallurgy process begins with the production of metal powders.
These powders can be pure metals or alloys, depending on the desired properties of the final product.
The powders are mixed with lubricants and binders to facilitate the molding and sintering processes.
Once the mix is prepared, it undergoes compaction.
Here, the powder is placed into a mold where pressure is applied, compacting the particles into a cohesive shape.
This step is crucial as it provides the formation needed for sintering.
Sintering is the next stage, where the compacted shape is heated at a temperature below its melting point.
The heat allows the powder particles to bond together, enhancing the part’s strength and integrity.
This step solidifies the part and determines most of its final properties.
If necessary, secondary operations like machining, polishing, or coating are performed to meet specific requirements or enhance the component’s attributes.
Applications of Powder Metallurgy
The applications of powder metallurgy are extensive, thanks to its versatility and efficiency.
In the automotive industry, PM and MIM techniques are used to fabricate a variety of components, such as gears, bearings, and filters.
These parts benefit from the high precision and strength provided by the powder metallurgy process.
The medical field also utilizes powder metallurgy for the creation of surgical instruments and equipment.
It allows for the production of complex, miniaturized shapes necessary for devices like pacemakers and orthodontic bracketing systems.
In the aerospace sector, powder metallurgy contributes to producing reliable and lightweight components that meet stringent safety standards.
Parts created through PM are crucial in achieving efficient fuel usage and improved aerodynamics in aircraft and spacecraft.
Additionally, everyday consumer goods like power tools and sports equipment are enhanced through PM technology.
Powder metallurgy allows manufacturers to produce durable and cost-effective components, improving product longevity and performance.
Key Points in Product Development Using Powder Metallurgy
Product development using powder metallurgy involves several important considerations to ensure success.
Firstly, selecting the right material is essential.
The specific requirements of the application dictate the choice of metal or alloy powders.
Properties such as hardness, strength, corrosion resistance, and thermal stability should align with the desired outcomes.
Secondly, designing for manufacturability is crucial.
While PM offers flexibility in shape and size, it’s important to consider aspect ratios and complexities to optimize production efficiency.
Designers should leverage the benefits of PM by considering features that are difficult to achieve with traditional methods.
Another vital aspect is the precision in controlling the process parameters.
Variations in pressure during compaction or incorrect sintering temperatures can lead to defects, compromising the final product’s integrity.
Quality control measures should be implemented at each stage to ensure accuracy and reliability.
Cost-efficiency is another significant factor.
While PM typically reduces waste and material costs, the initial investment in tooling and equipment can be substantial.
Proper planning and volume projections are necessary to balance initial outlays with long-term savings.
Environmental considerations should also be addressed.
Powder metallurgy is inherently more sustainable than many traditional methods, as it minimizes waste and allows for recycling of materials.
Nonetheless, manufacturers should strive to continually improve their environmental impact through innovative processes and technologies.
Future Trends in Powder Metallurgy and MIM
As technology advances, powder metallurgy and MIM are expected to evolve, offering even more capabilities and possibilities.
One promising area is the incorporation of additive manufacturing, or 3D printing, into the PM process.
This integration could further enhance the complexity and customization of parts while reducing lead times and costs.
Research in new materials, including energy-efficient alloys and composite materials, may pave the way for components with superior performance in demanding environments.
Advancements in automation and robotics are predicted to improve precision and scalability, making PM and MIM more accessible to a broader range of industries.
Incorporating data analytics and machine learning can also optimize processes, predict potential failures, and improve overall production quality.
By embracing these trends, powder metallurgy and MIM will continue to be at the forefront of innovation, driving advancements across numerous sectors.
In conclusion, powder metallurgy and metal injection molding are transformative manufacturing processes with broad applications and benefits.
Understanding the fundamentals and considering key points in product development can lead to successful outcomes, positioning manufacturers to leverage future advancements and maintain a competitive advantage.
資料ダウンロード
QCD管理受発注クラウド「newji」は、受発注部門で必要なQCD管理全てを備えた、現場特化型兼クラウド型の今世紀最高の受発注管理システムとなります。
ユーザー登録
受発注業務の効率化だけでなく、システムを導入することで、コスト削減や製品・資材のステータス可視化のほか、属人化していた受発注情報の共有化による内部不正防止や統制にも役立ちます。
NEWJI DX
製造業に特化したデジタルトランスフォーメーション(DX)の実現を目指す請負開発型のコンサルティングサービスです。AI、iPaaS、および先端の技術を駆使して、製造プロセスの効率化、業務効率化、チームワーク強化、コスト削減、品質向上を実現します。このサービスは、製造業の課題を深く理解し、それに対する最適なデジタルソリューションを提供することで、企業が持続的な成長とイノベーションを達成できるようサポートします。
製造業ニュース解説
製造業、主に購買・調達部門にお勤めの方々に向けた情報を配信しております。
新任の方やベテランの方、管理職を対象とした幅広いコンテンツをご用意しております。
お問い合わせ
コストダウンが利益に直結する術だと理解していても、なかなか前に進めることができない状況。そんな時は、newjiのコストダウン自動化機能で大きく利益貢献しよう!
(β版非公開)