- お役立ち記事
- Fundamentals of powder, tips on crushing, classification, and sieving techniques, and application to troubleshooting
月間77,185名の
製造業ご担当者様が閲覧しています*
*2025年2月28日現在のGoogle Analyticsのデータより
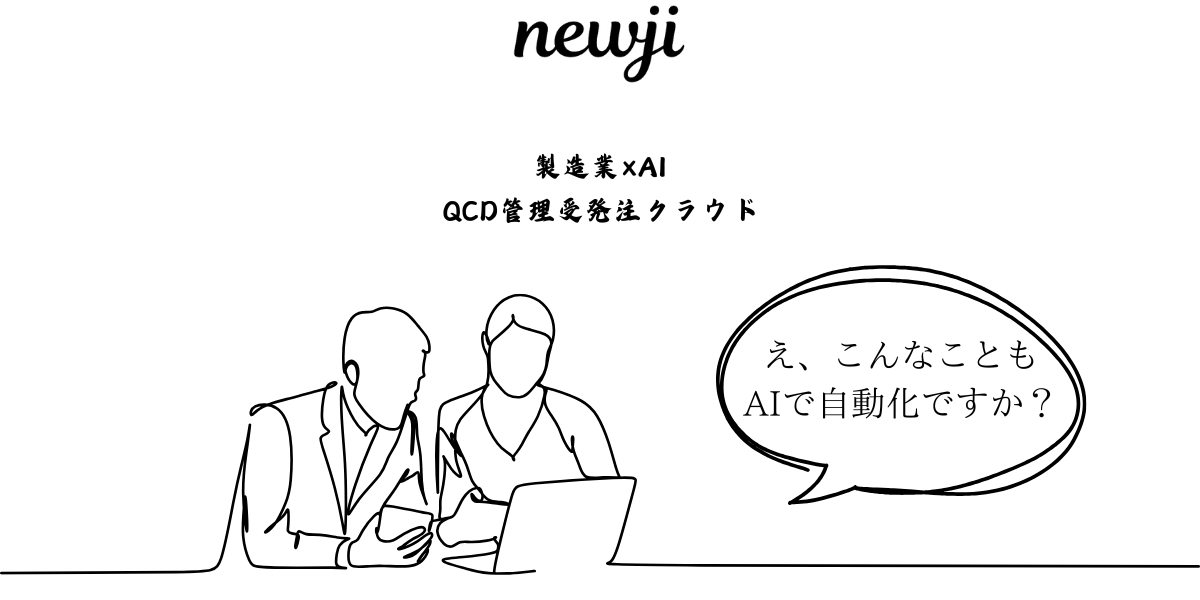
Fundamentals of powder, tips on crushing, classification, and sieving techniques, and application to troubleshooting
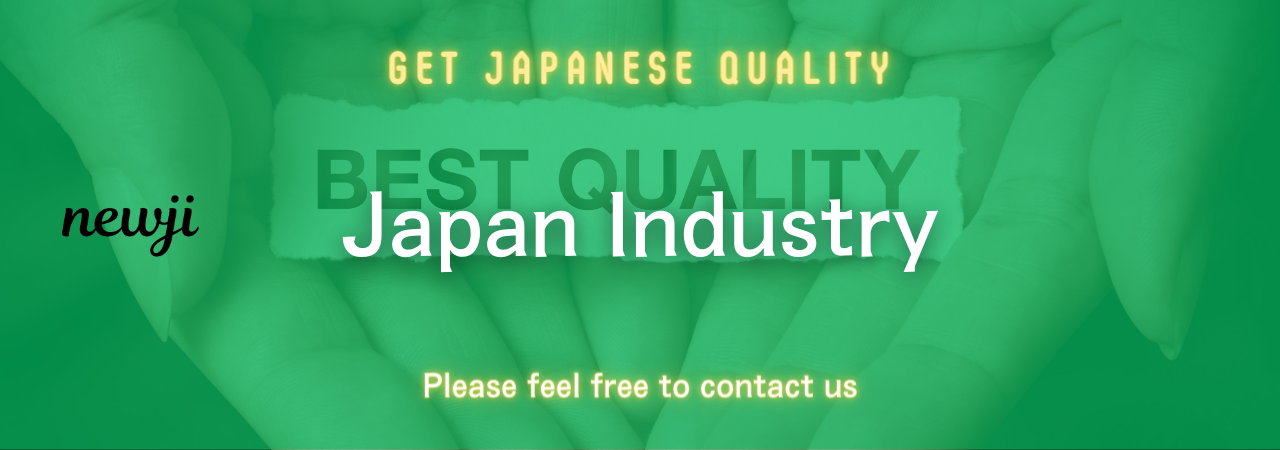
目次
Understanding the Basics of Powder
Powders play a crucial role in numerous industries, from pharmaceuticals to food processing, and even in manufacturing materials like ceramics and metals.
Understanding the fundamentals of powder is essential to achieving the desired quality and performance in end products.
Powders are defined as solid substances composed of fine particles.
The handling and processing of powders involve several critical steps, including crushing, classification, and sieving, each of which impacts the final product’s characteristics.
Powder Crushing Techniques
Crushing is the first step in the powder processing chain, where larger particles are reduced to smaller sizes, making them easier to work with and enhancing their properties.
Various techniques are employed in different industries based on the material type and desired outcome.
One common method is mechanical crushing, involving the use of machines such as jaw crushers and ball mills.
These machines apply mechanical forces to break down the particles.
Jaw crushers are particularly useful when large chunks need to be broken into smaller fragments.
Ball mills, on the other hand, are more suitable for achieving a finer powder grade.
Another method is impact crushing.
This involves the use of high-speed rotors that impact the particles, breaking them down efficiently.
Impact crushers are ideal for materials that are tough and require more force to disintegrate.
Careful consideration of the material characteristics and the end-use of the powder is vital when selecting the appropriate crushing method.
Classification of Powders
Once the powder is crushed, the next crucial step is classification.
This process involves separating particles based on size, shape, or density.
This ensures that only the desired particle sizes are present in the final product, which can significantly affect performance and application.
Classification can be conducted through several techniques.
Air classification is one prevalent method.
It uses air streams to separate particles based on their size and density.
Finer particles are carried away by the air stream, while heavier ones fall to the bottom.
This method is commonly used in the pharmaceutical industry to obtain uniform particle sizes.
Another technique is sieving.
Various mesh sizes are used to separate particles of different sizes physically.
Sieving is a straightforward yet effective method, especially in industries like food processing, where precise particle size is crucial for product consistency.
Ultrasonic classification uses high-frequency vibrations to segregate particles.
It is particularly beneficial when dealing with fine powders, ensuring a higher degree of precision.
Sieving Techniques for Powder Processing
Sieving is a vital step in ensuring the right particle size distribution.
It involves the use of a sieve or screen to filter out particles that do not meet the size requirement.
There are different types of sieves available, catering to various industrial needs.
Vibratory sieves are widely used for their efficiency and ability to handle a large volume of material.
They employ vibration to facilitate the movement of particles across the sieve.
Vibro sieves ensure that particles fall through the mesh openings, effectively separating them by size.
Rotary sieves use a rotating motion to classify particles.
These sieves work by circulating the material through a screen, separating different sizes based on the sieve openings.
Rotary sieves are popular in industries where continuous and high-throughput processing is required.
Static sieves are a more traditional approach, utilizing gravity to allow particles to fall through the sieve.
Although slower, this method is still effective for small-scale operations and when a high degree of cleanliness is necessary.
Troubleshooting Common Issues in Powder Processing
Despite the advancements in powder processing techniques, several challenges may still arise.
Understanding these common issues and their solutions is essential to maintain high-quality powder processing outcomes.
Over-sizing or under-sizing of particles is a frequent problem.
It often results from incorrect crushing or classification parameters.
To address this, it is important to regularly calibrate equipment and continuously monitor particle size distribution.
Moisture control is crucial in powder processing as excess moisture can cause clumping and affect flow properties.
Implementing drying steps or using anti-caking agents can help mitigate these effects.
Equipment wear and tear is another concern.
Regular maintenance and part replacement are necessary to ensure machinery operates efficiently.
Implementing a preventative maintenance schedule can reduce the risk of equipment failure and unscheduled downtime.
Operator training is vital.
Inadequate knowledge or handling of equipment may lead to suboptimal results.
Ensuring that staff are adequately trained on equipment operation and safety protocols can greatly improve processing outcomes.
Application of Powder Processing Techniques in Various Industries
Powder processing techniques find widespread application across numerous industries, each with unique requirements and challenges.
In the pharmaceutical industry, achieving uniformity in particle size is crucial for drug formulation and efficacy.
Accurate classification and sieving techniques ensure that active ingredients are delivered consistently in every dose.
In the food industry, powders are used in products like instant beverages and baking ingredients.
Precise particle size impacts dissolution rates and texture, making sieving techniques indispensable.
The manufacturing industry benefits significantly from powder processing, especially in the production of ceramics, metals, and polymers.
Crushing and classification help achieve the necessary material characteristics for specific applications.
Conclusion
Understanding the fundamentals of powder, including crushing, classification, and sieving techniques, is essential for various industrial applications.
Selecting the appropriate methods and troubleshooting common issues can enhance product quality and performance.
As technology advances, these techniques will continue to evolve, offering even greater precision and efficiency in powder processing.
資料ダウンロード
QCD管理受発注クラウド「newji」は、受発注部門で必要なQCD管理全てを備えた、現場特化型兼クラウド型の今世紀最高の受発注管理システムとなります。
ユーザー登録
受発注業務の効率化だけでなく、システムを導入することで、コスト削減や製品・資材のステータス可視化のほか、属人化していた受発注情報の共有化による内部不正防止や統制にも役立ちます。
NEWJI DX
製造業に特化したデジタルトランスフォーメーション(DX)の実現を目指す請負開発型のコンサルティングサービスです。AI、iPaaS、および先端の技術を駆使して、製造プロセスの効率化、業務効率化、チームワーク強化、コスト削減、品質向上を実現します。このサービスは、製造業の課題を深く理解し、それに対する最適なデジタルソリューションを提供することで、企業が持続的な成長とイノベーションを達成できるようサポートします。
製造業ニュース解説
製造業、主に購買・調達部門にお勤めの方々に向けた情報を配信しております。
新任の方やベテランの方、管理職を対象とした幅広いコンテンツをご用意しております。
お問い合わせ
コストダウンが利益に直結する術だと理解していても、なかなか前に進めることができない状況。そんな時は、newjiのコストダウン自動化機能で大きく利益貢献しよう!
(β版非公開)