- お役立ち記事
- Fundamentals of powder, tips on crushing, classification, and sieving techniques, and their applications and key points for troubleshooting
Fundamentals of powder, tips on crushing, classification, and sieving techniques, and their applications and key points for troubleshooting
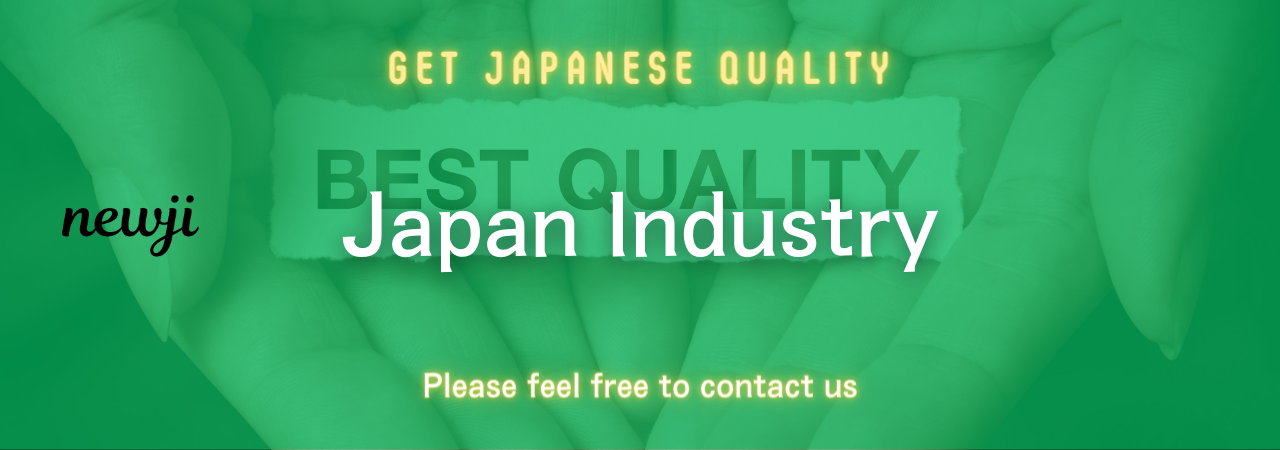
目次
Understanding Powder Crushing
Powder crushing is the process of reducing solid material’s size through mechanical forces. Various mechanisms can achieve this, including compression, impact, attrition, and cutting. Each method has unique advantages and limitations depending on the material and desired final particle size.
Compression Crushing
Compression involves applying force to materials until they break. This process is suitable for brittle materials and leads to controlled and consistent particle sizes. Machinery like jaw crushers and gyratory crushers commonly adopt this method.
Impact Crushing
In impact crushing, materials are broken down through high-speed collisions. Impact crushers and hammer mills are frequently used for this purpose. This technique is effective for brittle materials and can generate fine particles.
Attrition Crushing
Attrition involves grinding two surfaces together with pressure. The method is typically used for softer materials or achieving uniform particles. Devices like ball mills and roller mills offer attrition crushing.
Classification Techniques
Classification segregates particles according to size, allowing for precision in product quality and consistency. Several methods are used in powder classification to enhance accuracy and efficiency.
Air Classification
Air classification uses a stream of air to separate particles based on size and density. It’s an efficient technique that offers a high degree of control. It’s often applied post crushing to refine particle sizing.
Wet Classification
Wet classification involves water to sort particles. Hydrocyclones and other liquid-based classifiers use this process, especially where particles require a specific moisture content.
Sieve Classification
Sieve classification is a straightforward method where particles are separated through mesh screens. Its effectiveness lies in simplicity and reliability for coarse and medium powder sizes.
Sieving Techniques
The sieving process separates particles through vibration or agitation. This ensures particles are of uniform size and quality before their final application. Various mechanical means assist in sieving.
Vibration Sieving
Vibro sieves or vibratory sieve shakers agitate the material to pass through screens. This method is efficient for different sizes and can handle wet and dry powders. Vibration sieving is effective for precise particle separation.
Rotary Sieving
Rotary sieves use a rotating drum or mesh, whereby materials rotate to pass through openings. This method facilitates smoother processing and works for dry powders continuously.
Ultrasonic Sieving
In ultrasonic sieving, high-frequency sound waves assist in separating particles. This technique achieves highly accurate and fine separation, especially suitable for pharmaceutical and fine chemical powders.
Applications of Powder Processing
Powder processing is crucial across diverse industries due to its ability to achieve precision and product consistency. Its applications extend to producing pharmaceuticals, enhancing food textures, and creating specialized materials.
Pharmaceutical Industry
In pharmaceuticals, precise powder processing ensures dosage accuracy. Consistent particle size is necessary for effective drug delivery systems like tablets and capsules.
Food Industry
The food industry relies on powder processing for texture and flavor enhancement. Ingredients like flour, sugar, and spices undergo careful processing to meet quality standards.
Materials Production
Material sciences use powder processing for metals, ceramics, and composites, where control over particle size affects the mechanical properties and functionality of the final product.
Troubleshooting Powder Processing Challenges
Despite the benefits, powder processing can pose challenges. Understanding common issues and solutions enhances efficiency and product quality.
Avoiding Agglomeration
Agglomeration, where particles clump together, impedes processing. Ensuring adequate moisture control and using anti-caking agents are effective solutions.
Maintaining Equipment Efficiency
Regular maintenance of crushers, classifiers, and sieves prevents mechanical failures. Monitoring wear and tear extends the life and efficiency of processing equipment.
Handling Dust Generation
Many processes result in dust, affecting air quality and safety. Implementing dust collection systems and ensuring proper ventilation reduces these risks.
Powder processing is a critical operation in various industries. Understanding the nuances of crushing, classification, and sieving—and the careful application of each—ensures superior product quality and efficiency. This knowledge, coupled with proactive troubleshooting, can significantly enhance operational capabilities.
資料ダウンロード
QCD調達購買管理クラウド「newji」は、調達購買部門で必要なQCD管理全てを備えた、現場特化型兼クラウド型の今世紀最高の購買管理システムとなります。
ユーザー登録
調達購買業務の効率化だけでなく、システムを導入することで、コスト削減や製品・資材のステータス可視化のほか、属人化していた購買情報の共有化による内部不正防止や統制にも役立ちます。
NEWJI DX
製造業に特化したデジタルトランスフォーメーション(DX)の実現を目指す請負開発型のコンサルティングサービスです。AI、iPaaS、および先端の技術を駆使して、製造プロセスの効率化、業務効率化、チームワーク強化、コスト削減、品質向上を実現します。このサービスは、製造業の課題を深く理解し、それに対する最適なデジタルソリューションを提供することで、企業が持続的な成長とイノベーションを達成できるようサポートします。
オンライン講座
製造業、主に購買・調達部門にお勤めの方々に向けた情報を配信しております。
新任の方やベテランの方、管理職を対象とした幅広いコンテンツをご用意しております。
お問い合わせ
コストダウンが利益に直結する術だと理解していても、なかなか前に進めることができない状況。そんな時は、newjiのコストダウン自動化機能で大きく利益貢献しよう!
(Β版非公開)