- お役立ち記事
- Fundamentals of powders, methods of controlling fluidity and chargeability, and application to prevention of adhesion
月間76,176名の
製造業ご担当者様が閲覧しています*
*2025年3月31日現在のGoogle Analyticsのデータより
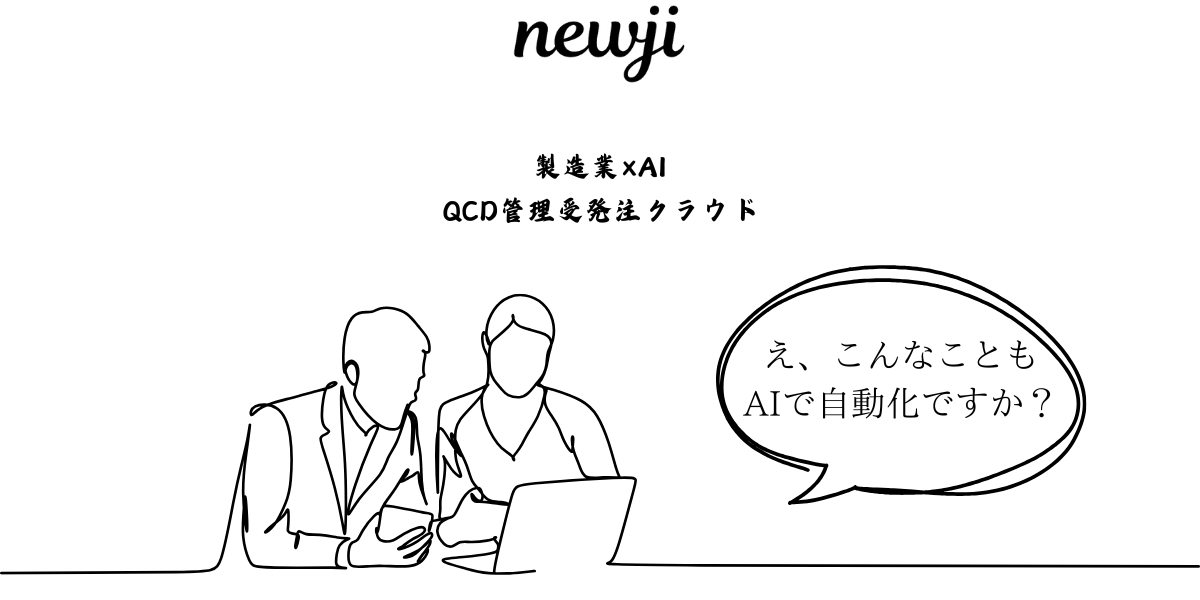
Fundamentals of powders, methods of controlling fluidity and chargeability, and application to prevention of adhesion
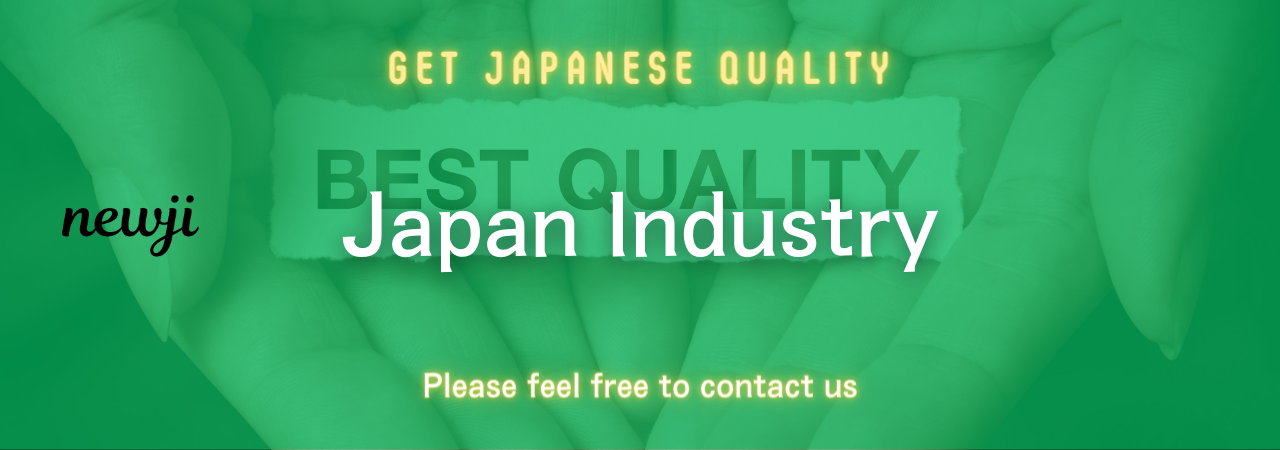
目次
Understanding the Basics of Powders
Powders are an integral part of various industries, from pharmaceuticals and food production to cosmetics and manufacturing.
Essentially, a powder is a dry, bulk solid composed of a large number of very fine particles that may flow freely when shaken or tilted.
Understanding the behavior of powders, including their fluidity and chargeability, is crucial for efficient processing in these industries.
Fluidity refers to the ability of powder particles to flow, and it is a critical factor in the handling and processing of materials.
Chargeability, on the other hand, involves the static electric charge that powder particles can acquire, affecting their behavior and interactions.
The properties of powders can be influenced by several factors, including particle size, shape, surface texture, and moisture content.
By comprehending these fundamentals, industries can apply effective methods to manage and enhance the properties of powders.
Methods of Controlling Fluidity
Controlling fluidity is essential to ensure smooth processing in manufacturing and production environments.
Several techniques can be employed to improve or manage the fluidity of powders.
Particle Size and Distribution
One of the primary factors affecting powder fluidity is particle size and distribution.
Smaller particles tend to have less fluidity due to increased surface area and stronger cohesive forces.
However, by optimizing particle size distribution, manufacturers can enhance fluidity.
A well-balanced range of particle sizes can create a blend that flows more uniformly and reduces issues like clumping or arching.
Use of Flow Aids
Flow aids, also known as flow conditioners, are additives used to improve powder fluidity.
Common flow aids include silica, talc, and magnesium stearate.
These substances reduce interparticle friction and help prevent caking, leading to smoother flow characteristics.
Moisture Control
Moisture content can significantly affect powder fluidity.
Excess moisture can lead to clumping and hinder free flow, while overly dry powders may generate dust and pose safety risks.
By maintaining optimal moisture levels within the powder, its fluidity can be managed effectively.
This often requires the use of drying agents or controlled humidity environments during processing and storage.
Chargeability in Powders
Chargeability refers to the tendency of powder particles to become electrically charged.
This phenomenon can lead to several issues, such as clinging, buildup, and uneven dispensing.
Understanding and controlling chargeability is crucial for maintaining product quality and ensuring efficient manufacturing processes.
Static Charge Generation
Powder particles become charged primarily due to triboelectric charging, which occurs when particles come into contact with each other or other surfaces.
The movement and separation of particles during handling and processing contribute to the build-up of static charge.
Managing this charge is essential to prevent discrepancies in product consistency and avoid potential safety hazards.
Materials and Environmental Conditions
The nature of the materials and the conditions in which powders are processed can influence their chargeability.
Materials with high electrical resistance are more prone to static charge accumulation.
Additionally, environmental factors such as humidity and temperature play roles in chargeability.
Higher humidity levels usually help decrease static charge, whereas dry conditions might enhance charge build-up.
Charge Control Strategies
Several strategies can be applied to control chargeability in powders.
Adding anti-static agents or using conductive materials can help dissipate static charge.
Moreover, ensuring that processing equipment is properly grounded assists in reducing charge accumulation.
By implementing these strategies, industries can minimize the challenges posed by powder chargeability and enhance process efficiency.
Application to Prevention of Adhesion
Adhesion, or the unwanted sticking of powder particles to surfaces or each other, can pose significant challenges in powder processing.
Effective management of adhesion is imperative to ensure high-quality and consistent outputs.
Use of Coatings and Surface Treatments
Applying coatings or surface treatments to powders or processing equipment can help reduce adhesion.
Materials like non-stick or low-friction coatings can prevent powder particles from sticking to surfaces, facilitating smoother processing and easier cleaning.
Similarly, treating the surface texture of powders can alter their adhesive properties, reducing undesirable interactions.
Optimizing Processing Conditions
Adjusting processing conditions, such as temperature and humidity, can influence adhesion.
For instance, increasing temperature may reduce the viscosity of certain binding agents, thus minimizing adhesion.
By closely monitoring and controlling these conditions, adhesion can be mitigated, improving process efficiency.
Addition of Anti-Adhesive Agents
Adding specific anti-adhesive agents to powders can effectively decrease adhesion.
These agents interfere with the binding forces between particles and surfaces, facilitating freer movement and preventing unwanted sticking.
Industries often select anti-adhesive agents based on compatibility with the powder’s intended use, ensuring that the functional properties of the product are maintained.
Conclusion
Understanding the fundamentals of powders, including their fluidity and chargeability, is essential for optimizing processing and ensuring high-quality manufacturing outcomes.
By applying various methods to control fluidity and chargeability, industries can minimize challenges related to powder behavior.
Furthermore, efficient prevention of adhesion is crucial to maintain product consistency and process efficiency.
Through strategic interventions and careful management of powder properties, industries can harness the advantages of powders while mitigating potential issues.
資料ダウンロード
QCD管理受発注クラウド「newji」は、受発注部門で必要なQCD管理全てを備えた、現場特化型兼クラウド型の今世紀最高の受発注管理システムとなります。
ユーザー登録
受発注業務の効率化だけでなく、システムを導入することで、コスト削減や製品・資材のステータス可視化のほか、属人化していた受発注情報の共有化による内部不正防止や統制にも役立ちます。
NEWJI DX
製造業に特化したデジタルトランスフォーメーション(DX)の実現を目指す請負開発型のコンサルティングサービスです。AI、iPaaS、および先端の技術を駆使して、製造プロセスの効率化、業務効率化、チームワーク強化、コスト削減、品質向上を実現します。このサービスは、製造業の課題を深く理解し、それに対する最適なデジタルソリューションを提供することで、企業が持続的な成長とイノベーションを達成できるようサポートします。
製造業ニュース解説
製造業、主に購買・調達部門にお勤めの方々に向けた情報を配信しております。
新任の方やベテランの方、管理職を対象とした幅広いコンテンツをご用意しております。
お問い合わせ
コストダウンが利益に直結する術だと理解していても、なかなか前に進めることができない状況。そんな時は、newjiのコストダウン自動化機能で大きく利益貢献しよう!
(β版非公開)