- お役立ち記事
- Fundamentals of precision extrusion molding technology, flow analysis using CAE, and key points for countermeasures against molding defects
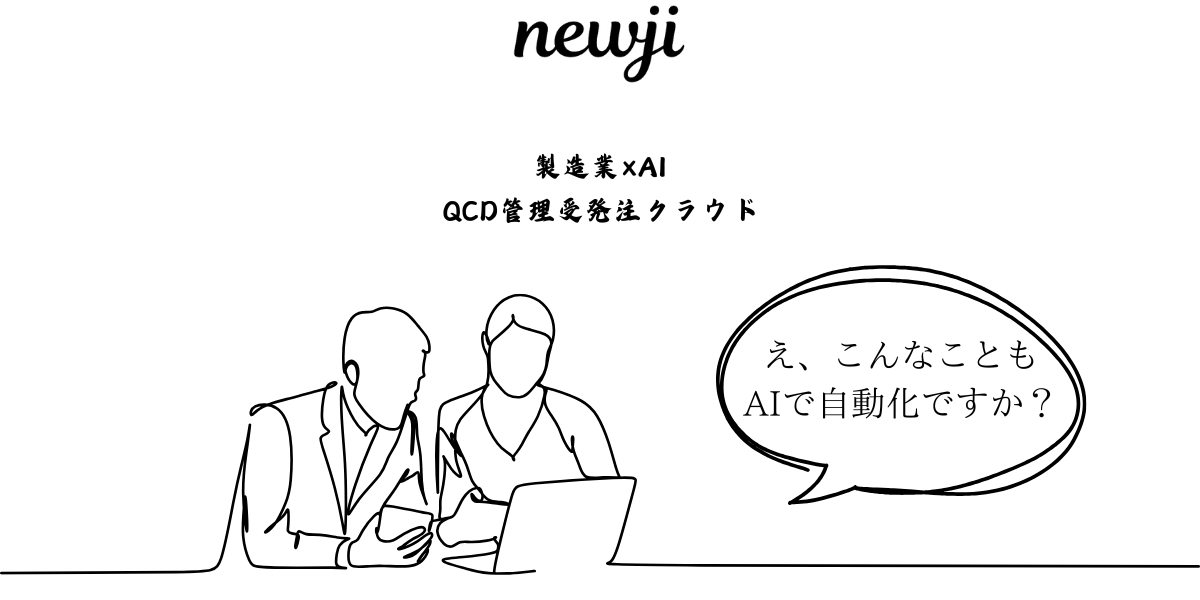
Fundamentals of precision extrusion molding technology, flow analysis using CAE, and key points for countermeasures against molding defects
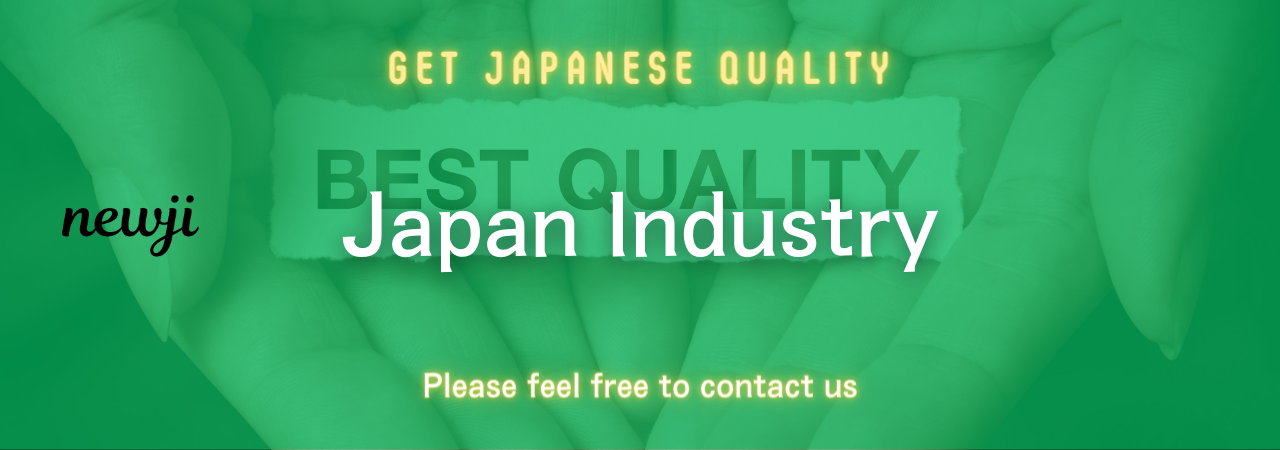
目次
Understanding Precision Extrusion Molding Technology
Precision extrusion molding is a highly specialized process used in manufacturing to produce intricate and precise components from a variety of materials, including metals and plastics.
This process involves pushing or drawing a material through a die to create a product with a fixed cross-sectional profile.
Extrusion molding is essential in industries such as automotive, aerospace, and consumer electronics, where the precision of components is paramount.
The advantages of precision extrusion include high quality, cost-effectiveness, and the ability to produce complex shapes.
In precision extrusion molding, maintaining high accuracy and meeting strict specifications are vital.
Therefore, understanding the underlying principles and technologies involved is crucial for practitioners in the field.
Key Elements of Extrusion Molding Technology
There are several key elements in precision extrusion molding that contribute to its effectiveness and efficiency:
Materials
Choosing the right material is essential, as it directly affects the product’s properties and performance.
Different materials have different flow characteristics, thermal properties, and mechanical strengths.
Common materials used include plastics like polyethylene and polypropylene, as well as metals and alloys.
Extrusion Process
The extrusion process involves several steps, including feeding the raw material into an extruder, melting and mixing it, then forcing it through a die to form the desired shape.
Temperature control and pressure settings are crucial to achieve the desired product quality and consistency.
Dies and Tooling
The die is a specially designed tool that shapes the extruded material.
It is critical in determining the final product’s shape and size.
Precision in die design and maintenance is necessary to avoid defects and ensure the smooth operation of the extrusion process.
Flow Analysis Using CAE
Computer-Aided Engineering (CAE) plays a significant role in optimizing precision extrusion molding processes.
Flow analysis using CAE allows engineers to simulate and analyze the flow of materials during extrusion.
Importance of Flow Analysis
Flow analysis helps in predicting the behavior of materials, identifying potential areas of concern, and optimizing process parameters.
It allows engineers to understand how different factors, such as temperature, pressure, and material properties, affect the extrusion process.
CAE Tools and Techniques
Several CAE tools are available for performing flow analysis in extrusion molding.
These tools use advanced algorithms and simulations to model the extrusion process under different conditions.
They provide valuable insights into velocity distribution, temperature gradients, and pressure variations within the material flow.
Optimization of Process Parameters
With the help of CAE, engineers can optimize various process parameters to improve product quality and reduce waste.
By simulating different scenarios, they can identify the ideal settings for temperature, pressure, and material flow to achieve the best results.
Addressing Molding Defects
Despite the controlled environment of extrusion molding, defects can occasionally arise.
Identifying and addressing these defects is crucial to maintaining the quality of the final product.
Common Molding Defects
Some common defects in precision extrusion molding include warping, surface blemishes, inconsistent thickness, and poor mechanical properties.
Each defect has specific causes, which range from improper material selection to incorrect process parameters.
Countermeasure Strategies
To address and counteract these defects, several strategies can be employed:
– **Material Selection:** Choosing the appropriate material with suitable properties for the application is critical.
– **Process Control:** Maintaining strict control over temperature, pressure, and speed to ensure uniformity and consistency.
– **Die Maintenance:** Regular inspection and maintenance of dies to avoid wear and tear that could lead to product defects.
– **Real-time Monitoring:** Using sensors and monitoring systems to continuously observe the process and make adjustments as needed.
Continuous Improvement
Implementing a feedback loop for continuous improvement is essential.
This involves analyzing defect data, learning from previous issues, and making necessary adjustments to the process.
Training and updating personnel on the latest technologies and techniques can also lead to better results.
Precision extrusion molding is a complex process that requires a deep understanding of the materials, processes, and technology involved.
By leveraging the power of CAE for flow analysis and implementing effective countermeasures against defects, manufacturers can achieve high-quality results consistently.
Staying informed about advancements in technology and methodologies ensures that practitioners can continuously improve their processes and meet the ever-evolving demands of precision components.
資料ダウンロード
QCD調達購買管理クラウド「newji」は、調達購買部門で必要なQCD管理全てを備えた、現場特化型兼クラウド型の今世紀最高の購買管理システムとなります。
ユーザー登録
調達購買業務の効率化だけでなく、システムを導入することで、コスト削減や製品・資材のステータス可視化のほか、属人化していた購買情報の共有化による内部不正防止や統制にも役立ちます。
NEWJI DX
製造業に特化したデジタルトランスフォーメーション(DX)の実現を目指す請負開発型のコンサルティングサービスです。AI、iPaaS、および先端の技術を駆使して、製造プロセスの効率化、業務効率化、チームワーク強化、コスト削減、品質向上を実現します。このサービスは、製造業の課題を深く理解し、それに対する最適なデジタルソリューションを提供することで、企業が持続的な成長とイノベーションを達成できるようサポートします。
オンライン講座
製造業、主に購買・調達部門にお勤めの方々に向けた情報を配信しております。
新任の方やベテランの方、管理職を対象とした幅広いコンテンツをご用意しております。
お問い合わせ
コストダウンが利益に直結する術だと理解していても、なかなか前に進めることができない状況。そんな時は、newjiのコストダウン自動化機能で大きく利益貢献しよう!
(Β版非公開)