- お役立ち記事
- Fundamentals of press working and key points for improving formability through servo press working
月間76,176名の
製造業ご担当者様が閲覧しています*
*2025年3月31日現在のGoogle Analyticsのデータより
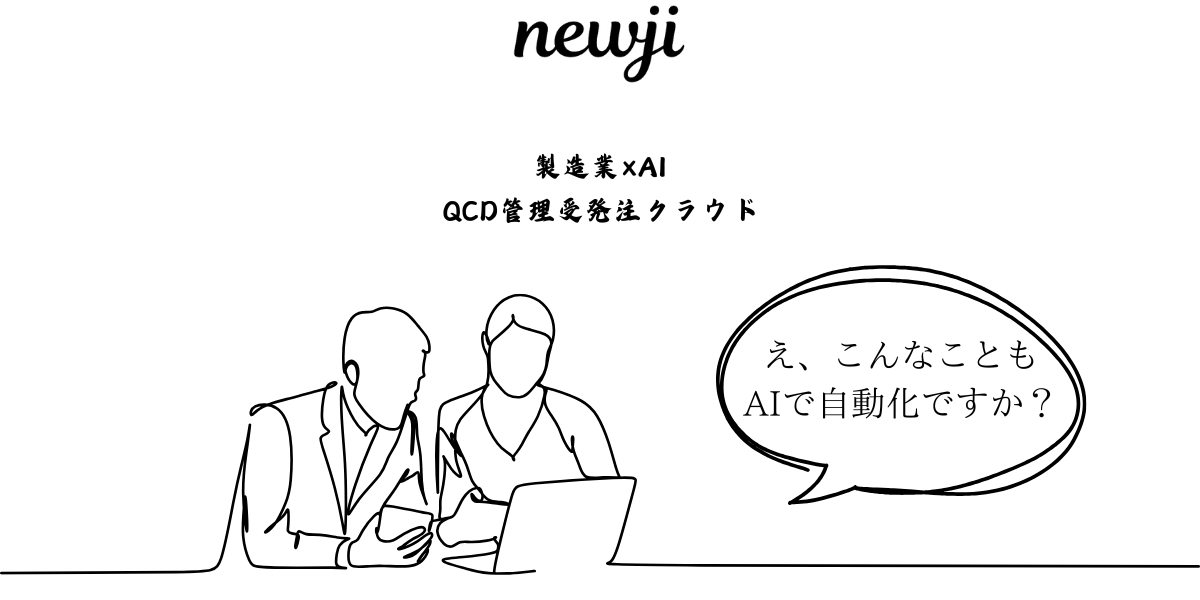
Fundamentals of press working and key points for improving formability through servo press working
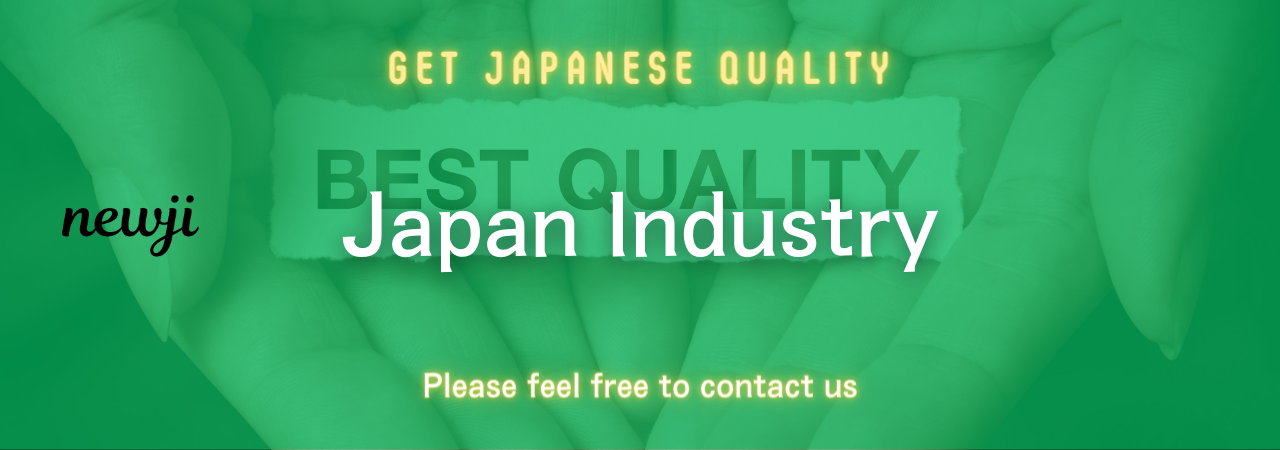
目次
Understanding Press Working
Press working, also known as stamping, is a manufacturing process crucial in shaping metal parts into various desired forms.
This method involves using a press machine to exert a significant amount of force on metal sheets, shaping them into the desired outline.
Press working is highly favored in the manufacturing industry due to its efficiency, precision, and ability to produce complex shapes quickly.
Key Components of Press Working
The process of press working consists of several fundamental components, each playing a crucial role in achieving the desired outcome.
Here are the main elements:
1. **Die:** The die is a specialized tool used to cut or shape the material.
It is usually custom-made for the particular job, ensuring that the end product meets specific design requirements.
2. **Punch:** The punch works in tandem with the die.
It exerts force onto the material, pushing it into the die, thereby shaping the material according to the die’s contour.
3. **Press Machine:** This is the main machine that provides the necessary force to carry out the stamping process.
Depending on the requirement, different types of press machines, such as hydraulic or mechanical presses, can be used.
4. **Material:** The material, commonly metal sheets, needs to be resilient enough to withstand the pressure and transform without breaking.
Steps in Press Working
The press working process can be broken down into several steps:
1. **Blanking:** This involves cutting out a flat metal piece from a larger sheet, forming a “blank” that can be used for further shaping.
2. **Bending:** The blank is bent into various angles and shapes, achieving the required outline for the product.
3. **Drawing:** This step involves pulling the blank into a three-dimensional shape.
4. **Piercing:** Holes are punched into the material as necessary for the product’s design.
5. **Trimming:** Excess material is removed, leaving a clean, finished product.
Improving Formability with Servo Press Working
Servo press working is a relatively new innovation in the stamping industry that offers enhanced capabilities for producing high-quality metal parts.
It incorporates advanced technology to improve the formability and efficiency of the press working process.
What is a Servo Press?
A servo press is a type of press machine that uses a servo motor to provide precise control over the press’s motion, speed, and position.
The servo motor allows for variable velocity and pressure throughout the pressing cycle, enhancing versatility and precision.
Advantages of Servo Press Working
1. **Precision Control:** Servo press machines offer precise control over the press stroke and pressure, which is essential in crafting complex and intricate parts with high accuracy.
2. **Sustainability:** These machines are typically energy-efficient, reducing power consumption and contributing to sustainable manufacturing practices.
3. **Quality Improvement:** The precise control and adaptability of servo presses help improve the quality and consistency of the produced parts.
4. **Reduced Wear and Tear:** Due to controlled pressure and motion, the tooling experiences less wear and tear, extending the lifespan of the equipment.
Key Points for Improving Formability
To maximize the benefits of servo press working, it is essential to focus on the following key points:
1. **Tool Design Optimization:** Ensure that the tools used are well-designed to accommodate the unique capabilities of the servo press machine.
This might involve custom designing dies and punches to work efficiently with variable press speeds and pressures.
2. **Material Selection:** Choose materials that are compatible with servo press working.
Materials that can better withstand the controlled press cycle will yield superior formability results.
3. **Process Control:** Maintain a strict control over the process parameters, such as stroke length, pressure, and speed.
Recording and analyzing these parameters will help in refining the process for optimal performance.
4. **Training and Expertise:** Ensure that operators are well-trained to handle the advanced capabilities of servo press machines.
Knowledgeable operators can make the most of the technology to improve production outcomes.
5. **Regular Maintenance:** Conduct regular maintenance checks on the servo press equipment to ensure it functions optimally, thus avoiding unforeseen downtimes or malfunctions.
Conclusion
Press working is a fundamental technique in the manufacturing sector, critical for producing a wide range of metal components efficiently and accurately.
The advent of servo press technology has further revolutionized this process by enhancing formability with precise control, energy efficiency, and improved quality.
By focusing on tool design, material selection, and maintaining stringent process controls, manufacturers can fully harness the potential of servo press working.
As technology continues to advance, embracing such innovations will be key in maintaining competitive advantages in the market.
資料ダウンロード
QCD管理受発注クラウド「newji」は、受発注部門で必要なQCD管理全てを備えた、現場特化型兼クラウド型の今世紀最高の受発注管理システムとなります。
ユーザー登録
受発注業務の効率化だけでなく、システムを導入することで、コスト削減や製品・資材のステータス可視化のほか、属人化していた受発注情報の共有化による内部不正防止や統制にも役立ちます。
NEWJI DX
製造業に特化したデジタルトランスフォーメーション(DX)の実現を目指す請負開発型のコンサルティングサービスです。AI、iPaaS、および先端の技術を駆使して、製造プロセスの効率化、業務効率化、チームワーク強化、コスト削減、品質向上を実現します。このサービスは、製造業の課題を深く理解し、それに対する最適なデジタルソリューションを提供することで、企業が持続的な成長とイノベーションを達成できるようサポートします。
製造業ニュース解説
製造業、主に購買・調達部門にお勤めの方々に向けた情報を配信しております。
新任の方やベテランの方、管理職を対象とした幅広いコンテンツをご用意しております。
お問い合わせ
コストダウンが利益に直結する術だと理解していても、なかなか前に進めることができない状況。そんな時は、newjiのコストダウン自動化機能で大きく利益貢献しよう!
(β版非公開)