- お役立ち記事
- Fundamentals of production management and production scheduling, applications to optimization, and how to utilize cyber-physical systems (CPS)
月間76,176名の
製造業ご担当者様が閲覧しています*
*2025年3月31日現在のGoogle Analyticsのデータより
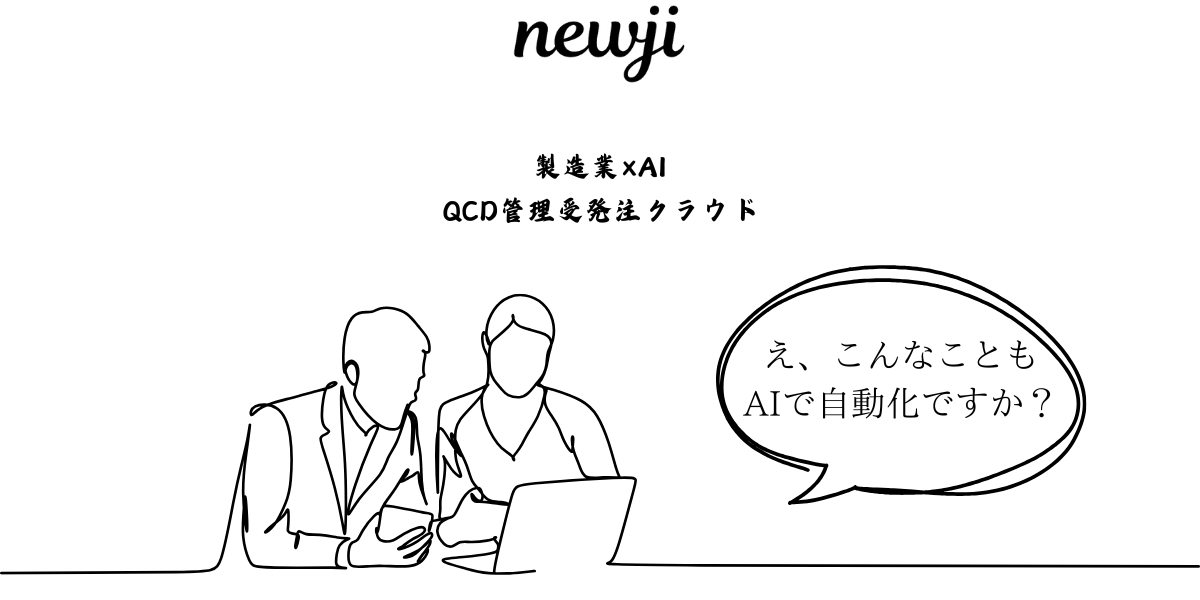
Fundamentals of production management and production scheduling, applications to optimization, and how to utilize cyber-physical systems (CPS)
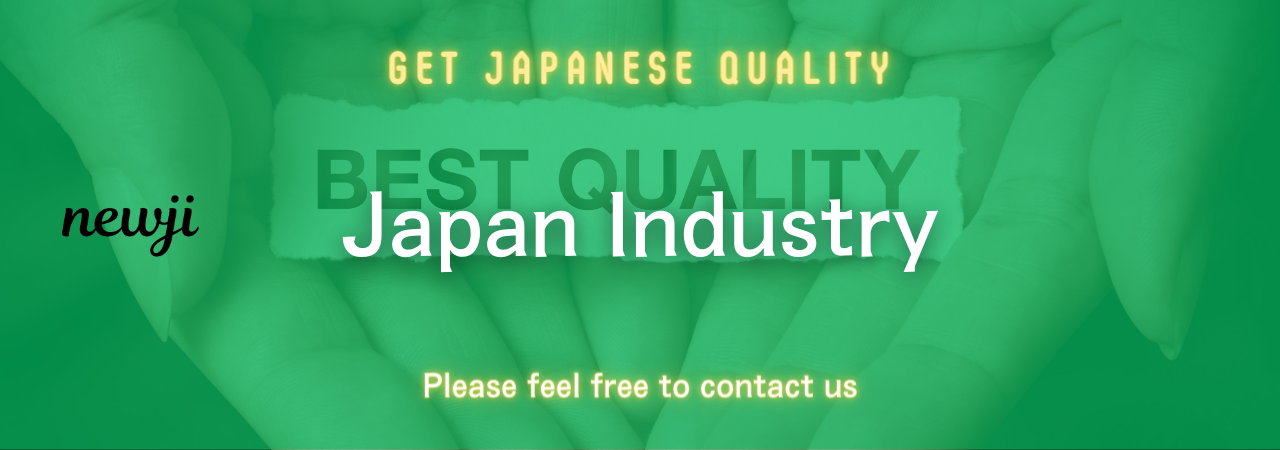
Understanding Production Management
Production management is a critical aspect of any manufacturing or production-based industry.
It involves overseeing the entire production process, from planning and scheduling to execution and monitoring.
The primary goal of production management is to ensure that the production process runs smoothly, efficiently, and effectively, while optimizing resource utilization and minimizing waste.
A core component of production management is the development of a production schedule that outlines what needs to be produced, in what quantity, and by when.
This schedule is crucial as it helps managers allocate resources, track progress, and make adjustments as necessary to meet demand.
An effective production management system can significantly enhance a company’s competitiveness and profitability.
The Importance of Production Scheduling
Production scheduling is an essential process within the broader framework of production management.
It involves the assignment of tasks to resources over a specific period to ensure the efficient operation of the production process.
A well-designed production schedule takes into account factors such as machine availability, workforce capacity, raw material suppliers, and delivery deadlines.
By optimizing the scheduling process, companies can reduce idle times, increase throughput, and achieve a more balanced workload distribution among employees and equipment.
Production scheduling also helps in identifying bottlenecks and constraints within the production process, allowing managers to make necessary adjustments to improve overall efficiency.
Applications of Optimization in Production Management
Optimization plays a pivotal role in production management, as it helps organizations make informed decisions to maximize output while minimizing costs.
Various analytical techniques and algorithms are employed to optimize different aspects of the production process, such as resource allocation, inventory management, and production scheduling.
For example, linear programming (LP) can be used to determine the optimal mix of production activities that will yield the highest profit while meeting constraints like budget limits and material availability.
Simulation modeling is another optimization tool that helps managers visualize different scenarios and predict the outcomes of various production strategies.
Optimization not only improves the efficiency of the current production processes but also provides data-driven insights that can guide long-term strategic planning.
With the aid of advanced optimization techniques, companies can gain a competitive edge by delivering high-quality products faster and at a lower cost.
Introduction to Cyber-Physical Systems (CPS)
Cyber-physical systems (CPS) are becoming increasingly integral to modern production management.
CPS refers to a network of physical and digital components that work together to monitor and control the production environment.
This integration of physical systems with computational algorithms allows for real-time data collection, analysis, and decision-making.
The implementation of CPS in industrial settings leads to what is known as the “smart factory” or Industry 4.0 revolution.
In a smart factory equipped with CPS, machines, sensors, and computers are interconnected, providing seamless communication and improving coordination across the entire production process.
Utilizing CPS for Production Optimization
The use of cyber-physical systems in production management offers numerous benefits, particularly in optimizing production processes.
By leveraging interconnected devices and sensors, companies can access real-time data about their operations, enabling them to identify inefficiencies and implement corrective measures promptly.
One significant advantage of CPS is predictive maintenance, where data from machinery and equipment is continuously monitored to anticipate potential failures before they occur.
This approach reduces downtime and maintenance costs while extending the lifespan of equipment.
Additionally, CPS enables dynamic scheduling, where production schedules are updated in real-time based on current conditions and demand forecasts.
Dynamic scheduling improves flexibility and responsiveness, allowing manufacturers to adapt quickly to changes in customer needs or unexpected disruptions in the supply chain.
The integration of CPS also facilitates better collaboration and communication between different departments, leading to a more harmonious and efficient production environment.
By fostering a culture of data-driven decision-making, CPS empowers workers at all levels of an organization to contribute to production optimization efforts.
Challenges and Future Prospects
While the adoption of cyber-physical systems in production management offers considerable benefits, it also comes with challenges.
One of the primary concerns is ensuring the security and privacy of sensitive data transmitted across connected devices.
Companies need to invest in robust cybersecurity measures to protect their systems from potential threats.
Another challenge is the complexity of integrating CPS with existing legacy systems in older manufacturing facilities.
This integration requires significant investment in technology upgrades and training for the workforce to effectively use new tools and platforms.
Despite these challenges, the prospects for CPS in production management are promising.
As technology continues to evolve, the capabilities of cyber-physical systems will expand, enabling even greater optimization of production processes.
Companies that invest in CPS will likely see improved efficiency, cost savings, and a stronger competitive position in the market.
In conclusion, production management and scheduling are vital components of any manufacturing operation.
The application of optimization techniques and the utilization of cyber-physical systems can significantly enhance the efficiency and effectiveness of production processes.
As industries continue to embrace these technological advancements, they will pave the way for smarter, more agile production environments that are well-equipped to meet the demands of the digital age.
資料ダウンロード
QCD管理受発注クラウド「newji」は、受発注部門で必要なQCD管理全てを備えた、現場特化型兼クラウド型の今世紀最高の受発注管理システムとなります。
ユーザー登録
受発注業務の効率化だけでなく、システムを導入することで、コスト削減や製品・資材のステータス可視化のほか、属人化していた受発注情報の共有化による内部不正防止や統制にも役立ちます。
NEWJI DX
製造業に特化したデジタルトランスフォーメーション(DX)の実現を目指す請負開発型のコンサルティングサービスです。AI、iPaaS、および先端の技術を駆使して、製造プロセスの効率化、業務効率化、チームワーク強化、コスト削減、品質向上を実現します。このサービスは、製造業の課題を深く理解し、それに対する最適なデジタルソリューションを提供することで、企業が持続的な成長とイノベーションを達成できるようサポートします。
製造業ニュース解説
製造業、主に購買・調達部門にお勤めの方々に向けた情報を配信しております。
新任の方やベテランの方、管理職を対象とした幅広いコンテンツをご用意しております。
お問い合わせ
コストダウンが利益に直結する術だと理解していても、なかなか前に進めることができない状況。そんな時は、newjiのコストダウン自動化機能で大きく利益貢献しよう!
(β版非公開)