- お役立ち記事
- Fundamentals of production system design and improvement methods to flexibly respond to changes in the market environment
月間76,176名の
製造業ご担当者様が閲覧しています*
*2025年3月31日現在のGoogle Analyticsのデータより
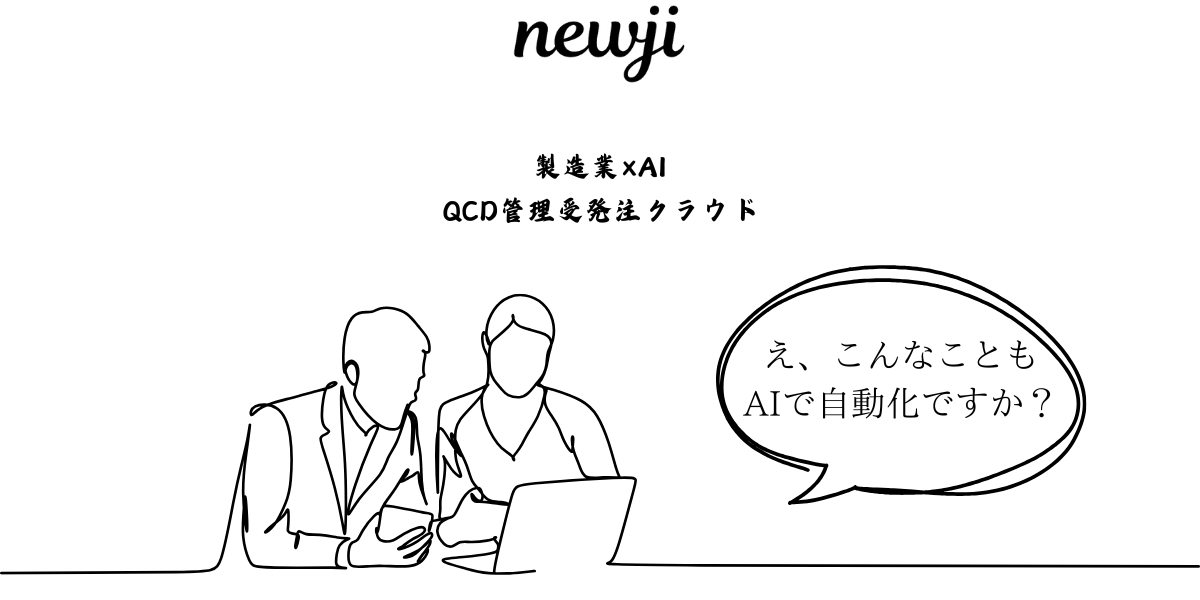
Fundamentals of production system design and improvement methods to flexibly respond to changes in the market environment
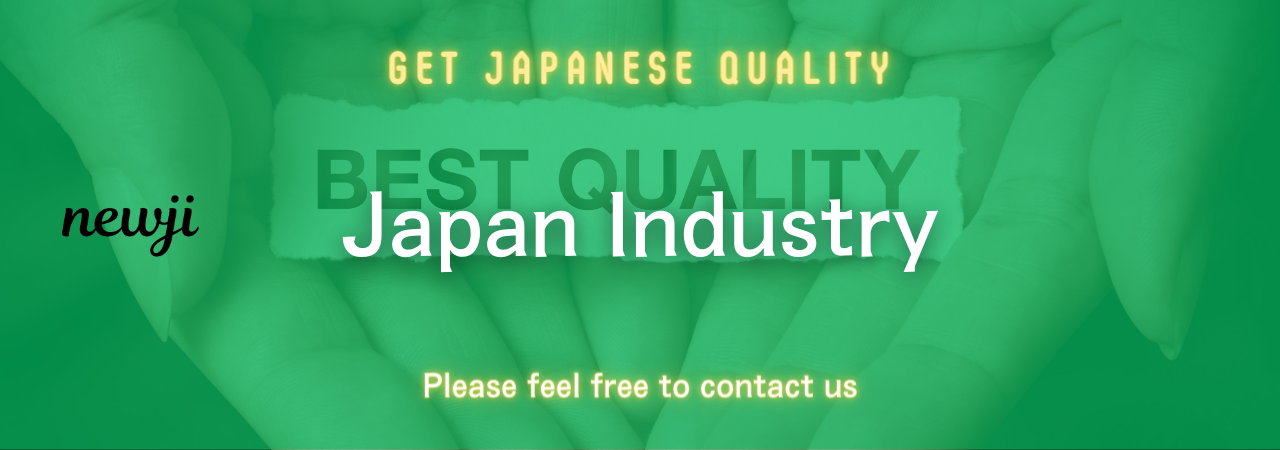
目次
Understanding Production System Design
Production system design is a critical component of any manufacturing process.
It involves creating a structured framework that governs how production activities are executed.
This includes everything from the arrangement of machinery and equipment to the flow of materials throughout the production line.
At its core, production system design aims to optimize efficiency, minimize waste, and ensure product quality.
A well-designed production system can lead to significant cost savings and improved productivity.
It allows manufacturers to produce goods at a faster pace while maintaining a high level of quality.
Moreover, efficient production systems are more adaptable to changing market demands.
This adaptability is essential in today’s fast-paced global market, where consumer preferences and technological advancements are constantly evolving.
Key Elements of Production System Design
To design an effective production system, several key elements must be considered:
Layout Design
The layout of a production system is fundamental.
It determines the physical arrangement of facilities, equipment, and workstations.
A well-thought-out layout minimizes material movement and wait times, which can reduce production time and costs.
There are several layout types, including process layout, product layout, fixed-position layout, and hybrid layouts, each suited for different types of production processes.
Process Planning
Process planning involves selecting the most efficient sequence of production operations.
This step is crucial to ensure that each stage of production is completed in the correct order and in the least amount of time.
Process planning also includes choosing the appropriate machinery, tools, and personnel needed for the operations.
Workforce Efficiency
A critical component of production system design is workforce efficiency.
This involves ensuring that workers are appropriately trained and positioned in roles that match their skills.
An efficient workforce is necessary to maintain smooth operations and prevent bottlenecks in the production process.
Material Flow and Inventory Management
Managing the flow of materials and maintaining optimal inventory levels are essential for a successful production system.
Efficient material flow ensures that materials are available at the right time and in the right place, reducing delays in production.
Proper inventory management helps in minimizing holding costs and reducing the risk of obsolescence.
Quality Control
Quality control is integral to production systems to ensure that products meet the required standards.
It involves regular inspection and testing of products at different stages of the production process.
Quality control helps in identifying defects early, preventing defective products from reaching the market.
Improvement Methods for Production Systems
In order to respond flexibly to changes in the market environment, various improvement methods can be applied to production systems:
Lean Manufacturing
Lean manufacturing techniques focus on waste reduction and optimizing production processes.
By identifying and eliminating non-value-adding activities, manufacturers can significantly improve efficiency and reduce costs.
Lean principles include practices such as Just-In-Time (JIT) production and the 5S system for workplace organization.
Six Sigma
Six Sigma is a data-driven approach that aims to improve the quality of process outputs by identifying and eliminating defects.
It uses statistical methods to monitor and control production processes.
Through Six Sigma, manufacturers can enhance product quality and reduce variation, leading to greater customer satisfaction.
Total Quality Management (TQM)
TQM is a comprehensive approach that involves all employees in the organization to improve processes, products, and services.
It emphasizes customer satisfaction and continuous improvement.
With TQM, production systems can become more adaptable, ensuring that they meet the changing needs of the market.
Flexible Manufacturing Systems (FMS)
FMS incorporate advanced technologies and automation to produce a variety of products without extensive setup changes.
They provide manufacturers with the ability to quickly adjust production schedules and adapt to new product designs.
This flexibility is crucial in responding to varying consumer demands.
Value Stream Mapping
Value stream mapping is a tool used to visualize and analyze the flow of materials and information in a production process.
By identifying bottlenecks and areas for improvement, manufacturers can streamline operations, reduce lead times, and enhance overall efficiency.
The Importance of Adaptation
In today’s dynamic market environment, being able to adapt is more important than ever.
Consumer preferences shift rapidly, and technological advancements constantly change the competitive landscape.
Production systems must be designed with the flexibility to adjust to these changes swiftly.
Investing in advanced technologies, fostering a culture of continuous improvement, and training a skilled workforce are all essential steps in creating adaptable production systems.
By doing so, manufacturers can maintain a competitive edge and ensure sustained growth in an ever-evolving market.
In conclusion, the fundamentals of production system design and improvement methods are crucial for maintaining efficient operations and staying competitive.
By focusing on key elements such as layout design, process planning, and quality control, and employing improvement methods like lean manufacturing and Six Sigma, manufacturers can flexibly respond to market changes and drive success.
資料ダウンロード
QCD管理受発注クラウド「newji」は、受発注部門で必要なQCD管理全てを備えた、現場特化型兼クラウド型の今世紀最高の受発注管理システムとなります。
ユーザー登録
受発注業務の効率化だけでなく、システムを導入することで、コスト削減や製品・資材のステータス可視化のほか、属人化していた受発注情報の共有化による内部不正防止や統制にも役立ちます。
NEWJI DX
製造業に特化したデジタルトランスフォーメーション(DX)の実現を目指す請負開発型のコンサルティングサービスです。AI、iPaaS、および先端の技術を駆使して、製造プロセスの効率化、業務効率化、チームワーク強化、コスト削減、品質向上を実現します。このサービスは、製造業の課題を深く理解し、それに対する最適なデジタルソリューションを提供することで、企業が持続的な成長とイノベーションを達成できるようサポートします。
製造業ニュース解説
製造業、主に購買・調達部門にお勤めの方々に向けた情報を配信しております。
新任の方やベテランの方、管理職を対象とした幅広いコンテンツをご用意しております。
お問い合わせ
コストダウンが利益に直結する術だと理解していても、なかなか前に進めることができない状況。そんな時は、newjiのコストダウン自動化機能で大きく利益貢献しよう!
(β版非公開)