- お役立ち記事
- Fundamentals of quality control and supplier evaluation that purchasing personnel should know
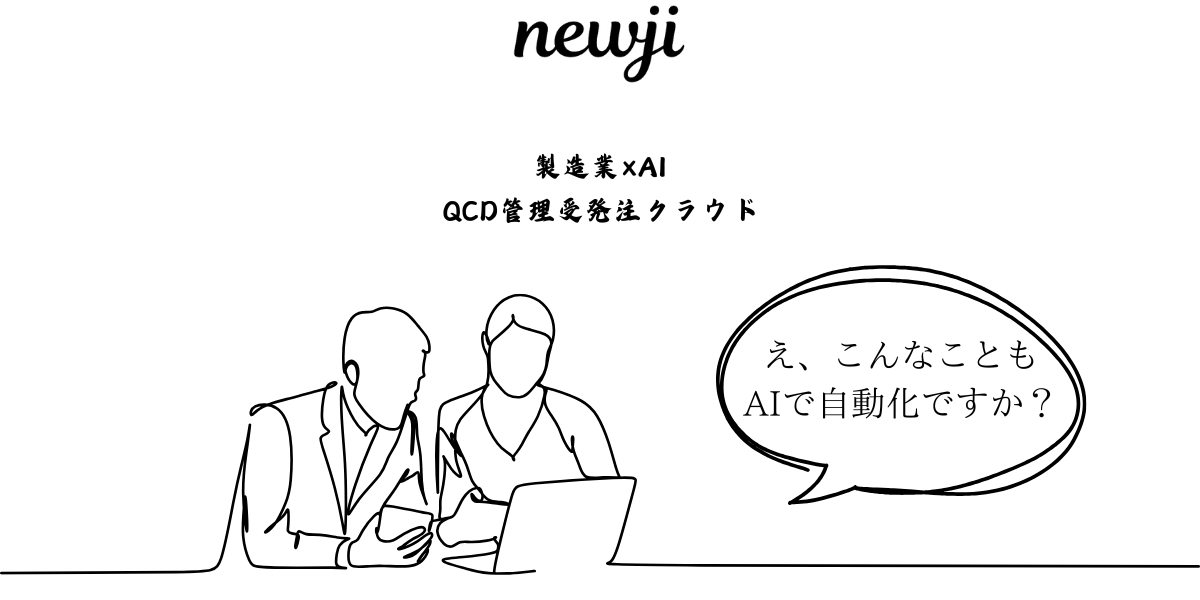
Fundamentals of quality control and supplier evaluation that purchasing personnel should know
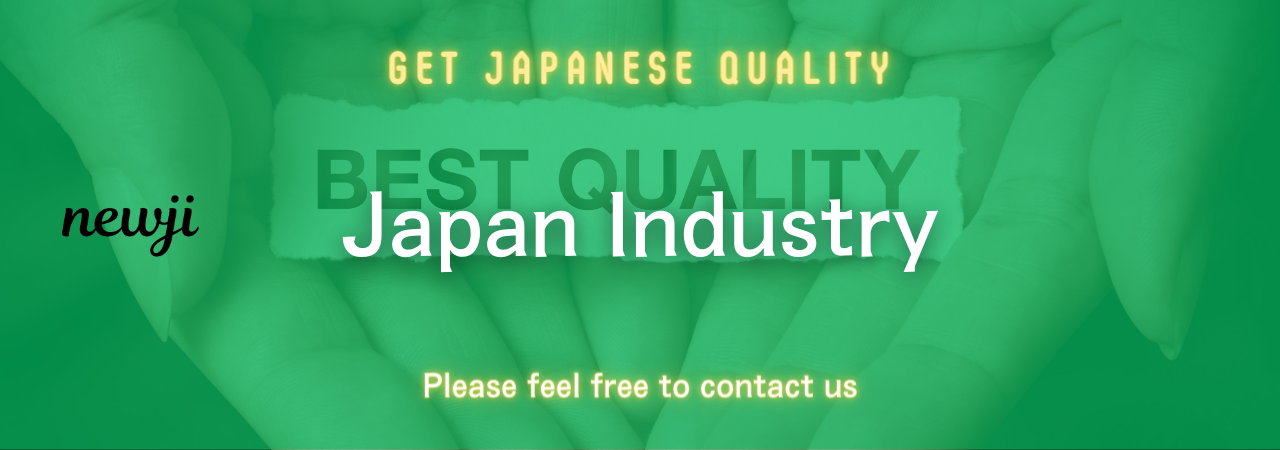
Understanding the fundamentals of quality control and supplier evaluation is crucial for purchasing personnel.
In any business, ensuring that the products or services meet quality standards is essential for customer satisfaction and company reputation.
Let’s delve into the basic aspects of quality control and supplier evaluation that every purchasing officer should know.
目次
What is Quality Control?
Quality control is the process through which products and services are evaluated to ensure that they meet specific standards and requirements.
The primary aim is to maintain the quality, consistency, and reliability of the product or service being produced.
This could involve inspecting products, evaluating processes, and reviewing the end results to ensure compliance with predetermined quality guidelines.
Effective quality control measures are essential in minimizing defects and ensuring that customers receive products that meet or exceed expectations.
Importance of Quality Control
Implementing a robust quality control process is fundamental for several reasons.
Firstly, it ensures that products meet safety standards and regulations, which is vital for consumer safety and brand trust.
Secondly, it helps in maintaining customer satisfaction by providing consistent product quality.
Additionally, quality control can result in cost savings by reducing waste and rework, ultimately leading to more efficient production processes.
It also aids in identifying areas for improvement, fostering innovation, and maintaining competitive advantage in the market.
The Role of Supplier Evaluation
Supplier evaluation is the process of assessing and approving potential suppliers through various criteria such as quality, delivery, price, and services.
Purchasing personnel use supplier evaluation to ensure that their suppliers are capable of delivering goods or services that meet the company’s standards.
This process is critical because the quality of the final product often depends on the materials and services provided by suppliers.
A robust supplier evaluation strategy helps in building strong, long-term relationships with reliable suppliers.
Key Criteria for Supplier Evaluation
When evaluating suppliers, purchasing personnel consider multiple factors to ensure a fair and comprehensive assessment.
Quality, as mentioned, is a top priority—ensuring that products are consistent and defect-free.
Delivery performance assesses whether suppliers can meet delivery schedules reliably and punctually.
Cost is another critical factor, as it affects the overall budget and pricing of the final product.
Furthermore, the supplier’s reliability and financial stability are also considered, ensuring they can support long-term business needs without risk of business interruption.
Innovation and technological capabilities are also evaluated, particularly in industries where keeping pace with advancements is crucial.
The supplier’s corporate social responsibility practices may also be reviewed, aligning with the company’s values and ethical standards.
Implementing Quality Control and Supplier Evaluation
To implement quality control and supplier evaluation effectively, purchasing personnel can follow several steps.
Firstly, they should define the quality standards and objectives clearly, making them aligned with the overall business goals and customer expectations.
Secondly, integrate quality control into the production and procurement processes.
This involves training staff on quality standards and setting up checkpoints or audits to monitor compliance.
For supplier evaluation, developing a comprehensive assessment criteria and conducting regular performance reviews is vital.
Building open communication lines with suppliers ensures transparency and helps address potential issues proactively.
Leveraging data and analytics can enhance both quality control and supplier evaluation processes, providing insights into performance trends and areas needing improvement.
Challenges in Quality Control and Supplier Evaluation
Though essential, quality control and supplier evaluation come with their set of challenges.
One common issue is resistance to change, where implementing new quality processes or reassessing suppliers might face opposition from within the organization.
Additionally, maintaining consistency in quality can be challenging, particularly in large-scale operations where numerous variables affect outcomes.
Similarly, supplier evaluation can be time-consuming and resource-intensive, especially for companies with extensive supply chains.
However, overcoming these challenges with a structured approach and clear communication can lead to significant long-term benefits, including enhanced product quality and stronger supplier partnerships.
Conclusion
A thorough understanding of quality control and supplier evaluation is crucial for purchasing personnel.
By ensuring that products meet standards and suppliers are reliable, purchasing officers contribute significantly to the company’s success.
Implementing these processes may require effort and resources, but the benefits of improved product quality, customer satisfaction, and cost efficiency are invaluable.
By staying informed and proactive, purchasing personnel can support their organizations in maintaining a competitive edge in the market.
資料ダウンロード
QCD調達購買管理クラウド「newji」は、調達購買部門で必要なQCD管理全てを備えた、現場特化型兼クラウド型の今世紀最高の購買管理システムとなります。
ユーザー登録
調達購買業務の効率化だけでなく、システムを導入することで、コスト削減や製品・資材のステータス可視化のほか、属人化していた購買情報の共有化による内部不正防止や統制にも役立ちます。
NEWJI DX
製造業に特化したデジタルトランスフォーメーション(DX)の実現を目指す請負開発型のコンサルティングサービスです。AI、iPaaS、および先端の技術を駆使して、製造プロセスの効率化、業務効率化、チームワーク強化、コスト削減、品質向上を実現します。このサービスは、製造業の課題を深く理解し、それに対する最適なデジタルソリューションを提供することで、企業が持続的な成長とイノベーションを達成できるようサポートします。
オンライン講座
製造業、主に購買・調達部門にお勤めの方々に向けた情報を配信しております。
新任の方やベテランの方、管理職を対象とした幅広いコンテンツをご用意しております。
お問い合わせ
コストダウンが利益に直結する術だと理解していても、なかなか前に進めることができない状況。そんな時は、newjiのコストダウン自動化機能で大きく利益貢献しよう!
(Β版非公開)