- お役立ち記事
- Fundamentals of Quality Management: Techniques and Case Studies for Preventing Quality Defects
Fundamentals of Quality Management: Techniques and Case Studies for Preventing Quality Defects
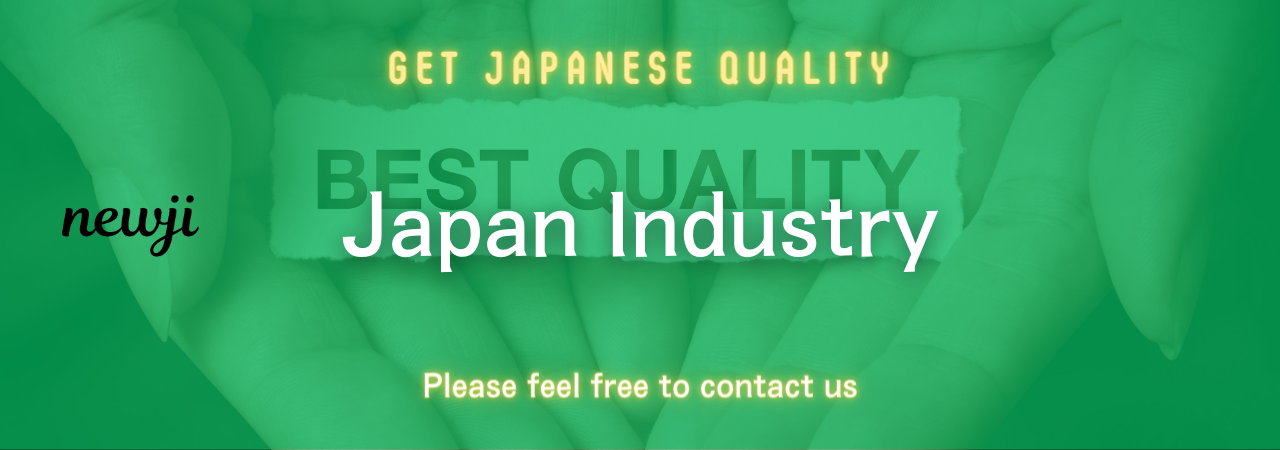
Quality management is crucial for any organization seeking to deliver products or services that meet customer expectations consistently.
Understanding its fundamentals and implementing effective techniques can significantly reduce defects, leading to enhanced customer satisfaction and improved bottom lines.
Here, we will delve into the essential aspects of quality management, exploring various techniques, tools, and notable case studies that highlight successful defect prevention.
目次
What is Quality Management?
Quality management is a systematic approach aimed at ensuring that products or services are consistent, reliable, and meet specified standards.
It encompasses several processes and practices geared towards minimizing defects and improving production quality.
The primary components of quality management include quality planning, quality assurance, quality control, and continuous improvement.
Key Techniques in Quality Management
Total Quality Management (TQM)
Total Quality Management is a holistic approach where all members of an organization participate in improving processes, products, services, and the culture within which they work.
TQM involves various methodologies like continuous feedback loops and constant process evaluations to ensure quality objectives are met.
Six Sigma
Six Sigma is a data-driven technique focused on reducing defect rates to less than 3.4 defects per million opportunities.
Using statistical tools and concepts, Six Sigma aims to improve processes by identifying and eliminating sources of variability.
Specially trained professionals, like Green Belts and Black Belts, lead these initiatives within organizations.
Lean Manufacturing
Lean manufacturing focuses on minimizing waste without sacrificing productivity.
The primary objective is to enhance value for the customer by identifying non-value-added activities and eliminating them.
Techniques under Lean include the 5S method, Kaizen (continuous improvement), and Just-In-Time (JIT) production.
ISO 9001 Standards
ISO 9001 is an internationally recognized standard for quality management systems.
Organizations that adhere to ISO 9001 guidelines ensure that their processes meet the necessary standards for quality.
Adopting these standards involves performing audits, maintaining documentation, and implementing corrective actions when deviations occur.
Common Tools for Quality Management
Fishbone Diagram (Ishikawa)
The Fishbone Diagram, also known as the Ishikawa diagram, is a visual tool used to identify and analyze the root causes of defects.
By categorizing potential cause factors into different branches, organizations can pinpoint the origin of an issue and implement targeted solutions.
Control Charts
Control charts are used to monitor process stability over time.
By plotting data points in chronological order, organizations can detect variations within a process and determine whether these variations are within acceptable limits.
This helps in maintaining process consistency and early identification of anomalies.
Pareto Chart
A Pareto chart is a bar graph that identifies the most significant factors contributing to a problem.
According to the Pareto Principle, 80% of problems are typically caused by 20% of the factors.
Focusing on these major contributors can lead to more efficient problem-solving efforts.
Failure Mode and Effects Analysis (FMEA)
FMEA is a systematic tool used to identify possible failure modes within a process and their potential impact.
By prioritizing failures based on their severity, occurrence, and detectability, organizations can implement preventive measures to mitigate risks.
Case Studies Highlighting Successful Quality Management
Case Study 1: Toyota
Toyota is often cited as a prime example of successful quality management.
The automaker’s adoption of the Toyota Production System (TPS) revolutionized manufacturing with its focus on Lean principles.
By utilizing JIT production and continuous improvement (Kaizen), Toyota significantly reduced waste and defects, ensuring high-quality vehicles reached the market efficiently.
Case Study 2: Motorola
Motorola’s implementation of Six Sigma in the late 1980s resulted in substantial quality and efficiency gains.
Through meticulous data analysis and rigorous process improvements, Motorola managed to reduce their defect rate and save millions in costs.
Their successful adoption of Six Sigma set a benchmark, prompting many other organizations to adopt the methodology.
Case Study 3: General Electric
Under the leadership of Jack Welch in the 1990s, General Electric (GE) embraced Six Sigma to enhance their operational efficiency.
GE’s deployment of the Six Sigma methodology across various departments led to significant improvements in quality and customer satisfaction.
Their systematic approach to defect reduction and process optimization solidified GE’s standing as a leader in quality management.
The Benefits of Effective Quality Management
Effective quality management brings myriad benefits to an organization.
Firstly, it leads to improved product and service quality, which translates to higher customer satisfaction and loyalty.
Secondly, it enhances operational efficiency by identifying and eliminating waste, thereby reducing costs.
Additionally, effective quality management fosters a culture of continuous improvement, encouraging employees at all levels to contribute to quality initiatives.
Lastly, it can offer a competitive advantage, distinguishing an organization as a leader in its industry through consistent delivery of high-quality offerings.
Conclusion
In conclusion, understanding and implementing the fundamentals of quality management is essential for any organization aspiring to achieve excellence.
By leveraging techniques like TQM, Six Sigma, Lean Manufacturing, and adhering to ISO 9001 standards, businesses can significantly reduce defects and enhance their production quality.
Utilizing various tools such as Fishbone Diagrams, Control Charts, Pareto Charts, and FMEA, organizations can identify and address potential issues proactively.
Case studies from industry leaders like Toyota, Motorola, and General Electric demonstrate the tangible benefits of effective quality management.
Ultimately, the systematic approach to quality fosters a culture of continuous improvement, resulting in sustained success and customer satisfaction.
資料ダウンロード
QCD調達購買管理クラウド「newji」は、調達購買部門で必要なQCD管理全てを備えた、現場特化型兼クラウド型の今世紀最高の購買管理システムとなります。
ユーザー登録
調達購買業務の効率化だけでなく、システムを導入することで、コスト削減や製品・資材のステータス可視化のほか、属人化していた購買情報の共有化による内部不正防止や統制にも役立ちます。
NEWJI DX
製造業に特化したデジタルトランスフォーメーション(DX)の実現を目指す請負開発型のコンサルティングサービスです。AI、iPaaS、および先端の技術を駆使して、製造プロセスの効率化、業務効率化、チームワーク強化、コスト削減、品質向上を実現します。このサービスは、製造業の課題を深く理解し、それに対する最適なデジタルソリューションを提供することで、企業が持続的な成長とイノベーションを達成できるようサポートします。
オンライン講座
製造業、主に購買・調達部門にお勤めの方々に向けた情報を配信しております。
新任の方やベテランの方、管理職を対象とした幅広いコンテンツをご用意しております。
お問い合わせ
コストダウンが利益に直結する術だと理解していても、なかなか前に進めることができない状況。そんな時は、newjiのコストダウン自動化機能で大きく利益貢献しよう!
(Β版非公開)