- お役立ち記事
- Fundamentals of raw material transportation risk management from the perspective of the purchasing department
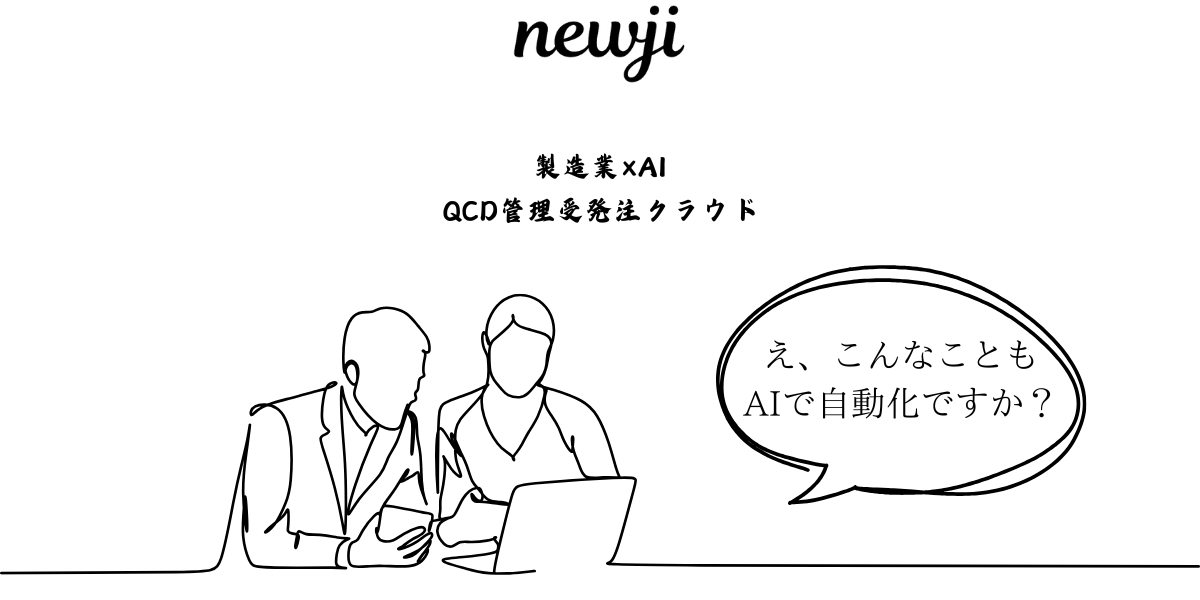
Fundamentals of raw material transportation risk management from the perspective of the purchasing department
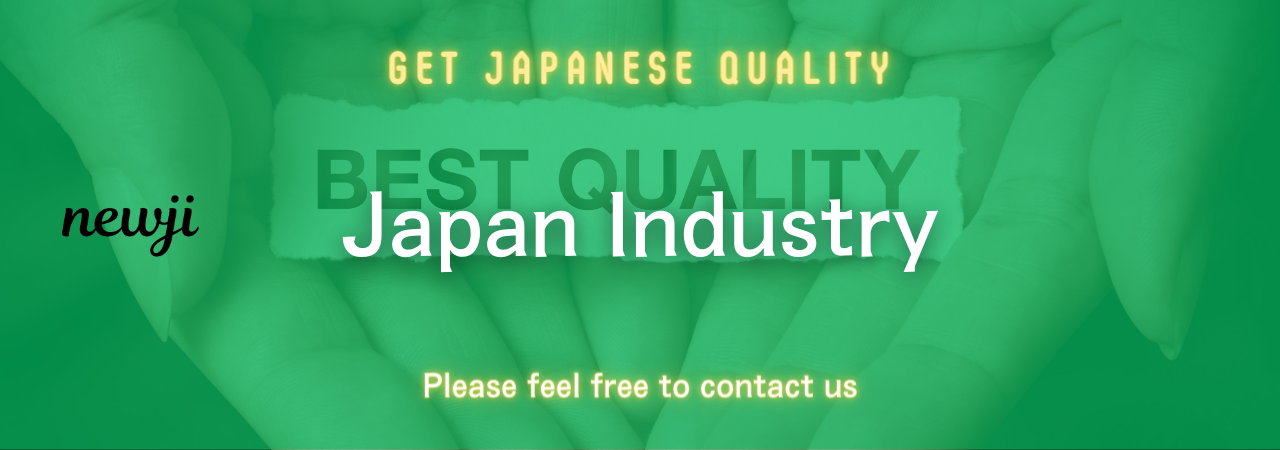
目次
Understanding Raw Material Transportation Risk
In the world of supply chain management, raw material transportation is a critical component.
Ensuring a smooth transition of goods from suppliers to manufacturers demands a meticulous understanding of the risks involved.
For the purchasing department, these risks can significantly impact both the cost and efficiency of obtaining raw materials.
Understanding potential disruptions, delays, and other risks is essential to maintaining a reliable supply chain.
Transportation risks can arise from several sources.
Weather conditions, geopolitical tensions, and regulatory changes are just a few external factors that can alter logistical plans.
Operational risks such as equipment failures, labor strikes, and accidents can also disrupt transportation.
For the purchasing department, recognizing these risks early is key to minimizing their impact on the overall supply chain.
Identifying Key Risk Factors
The purchasing department should begin by identifying key risk factors associated with raw material transportation.
This involves analyzing both external and internal factors that could potentially disrupt the supply chain.
External factors often include adverse weather conditions like hurricanes, floods, or snowstorms.
These natural events can delay shipments or damage goods, introducing uncertainties into the supply chain timeline.
Geopolitical issues, such as conflicts or trade disputes, can also cause delays due to border closings or altered trade agreements.
On the other hand, regulatory changes, such as new tariffs or transportation laws, can increase costs or restrict material flow.
Internally, operational risks should be considered.
These may involve equipment failures, accidents, human error, or labor strikes.
For instance, a breakdown in a key transportation vehicle could delay the delivery of crucial materials, leading to production downtime.
By identifying these risk factors, the purchasing department can develop strategies to mitigate their impacts.
Strategies for Risk Mitigation
Once potential risks are identified, the next step involves creating strategies to mitigate them.
A proactive approach can make a significant difference in minimizing disruptions in raw material transportation.
One effective strategy is diversifying suppliers and transportation modes.
By establishing relationships with multiple suppliers and utilizing different transportation methods, companies can reduce their reliance on a single source or mode.
If one route or supplier is disrupted, an alternative can quickly be deployed.
Additionally, maintaining a flexible logistics network allows companies to adapt their transportation plans at short notice.
This can be achieved through real-time analytics and robust communication systems, enabling quick responses to any disruptions.
Strategic sourcing and long-term contracts with suppliers can also help mitigate risks.
By securing long-term contracts, companies can lock in favorable terms and plan for future disruptions.
Furthermore, closer communication with suppliers can lead to early warnings of potential issues.
Leveraging Technology in Risk Management
Technology plays a crucial role in modern risk management.
By leveraging advanced tools and systems, purchasing departments can enhance their capabilities to anticipate and respond to risks effectively.
Supply chain management software provides comprehensive visibility into logistics networks.
These tools allow teams to track shipments in real-time, monitor weather forecasts, and receive updates on geopolitical developments.
This enhanced visibility empowers purchasing departments to make informed decisions quickly.
Predictive analytics and machine learning algorithms can further augment risk management processes.
These technologies can analyze historical data and predict potential disruptions, allowing companies to develop contingency plans ahead of time.
For example, algorithms can forecast weather conditions that might impact transportation routes, enabling preemptive action.
Moreover, blockchain technology can enhance transparency and security in supply chains.
By providing a decentralized record of all transactions and shipments, blockchain ensures that all parties involved have access to trustworthy data.
This can improve accountability and reduce the risk of fraud or misinformation.
Developing a Risk Management Plan
An essential aspect of transportation risk management is developing a comprehensive risk management plan.
This plan serves as a guide for the purchasing department to identify, assess, and address potential risks systematically.
A risk management plan should begin with a thorough risk assessment.
This involves evaluating both the likelihood and impact of potential risks.
After identifying and prioritizing risks, the next step is developing strategies to mitigate these risks.
The plan should include clear roles and responsibilities for team members.
Each member should understand their part in risk management, from initial risk identification to implementing contingency plans.
Regular reviews and updates of the risk management plan are critical.
The global landscape is constantly evolving, and new risks can emerge at any time.
By regularly reviewing the plan, purchasing departments can ensure they remain prepared to handle new challenges.
Collaboration and Communication
Risk management in raw material transportation is not a solo endeavor.
Collaboration and communication are vital across various departments within the organization and with external stakeholders.
Internally, the purchasing department should work closely with logistics, production, and finance teams.
This collaboration ensures that all aspects of the supply chain are aligned and prepared for potential disruptions.
Externally, maintaining strong relationships with suppliers and transport companies can improve communication and coordination.
Frequent communication helps establish trust and ensures timely notifications about any potential issues or delays.
Engagement in industry forums and collaborative platforms can also provide valuable insights into emerging risks and best practices.
Sharing information with peers can lead to better preparedness and a more robust risk management strategy overall.
Conclusion
In conclusion, the fundamentals of raw material transportation risk management from the purchasing department’s perspective involve a comprehensive understanding of potential risks and proactive strategies to mitigate them.
By identifying key risk factors, leveraging technology, developing a robust risk management plan, and fostering collaboration, purchasing departments can enhance their ability to manage transportation risks effectively.
Ultimately, this leads to a more resilient and efficient supply chain that delivers consistent value to the organization.
資料ダウンロード
QCD調達購買管理クラウド「newji」は、調達購買部門で必要なQCD管理全てを備えた、現場特化型兼クラウド型の今世紀最高の購買管理システムとなります。
ユーザー登録
調達購買業務の効率化だけでなく、システムを導入することで、コスト削減や製品・資材のステータス可視化のほか、属人化していた購買情報の共有化による内部不正防止や統制にも役立ちます。
NEWJI DX
製造業に特化したデジタルトランスフォーメーション(DX)の実現を目指す請負開発型のコンサルティングサービスです。AI、iPaaS、および先端の技術を駆使して、製造プロセスの効率化、業務効率化、チームワーク強化、コスト削減、品質向上を実現します。このサービスは、製造業の課題を深く理解し、それに対する最適なデジタルソリューションを提供することで、企業が持続的な成長とイノベーションを達成できるようサポートします。
オンライン講座
製造業、主に購買・調達部門にお勤めの方々に向けた情報を配信しております。
新任の方やベテランの方、管理職を対象とした幅広いコンテンツをご用意しております。
お問い合わせ
コストダウンが利益に直結する術だと理解していても、なかなか前に進めることができない状況。そんな時は、newjiのコストダウン自動化機能で大きく利益貢献しよう!
(Β版非公開)