- お役立ち記事
- Fundamentals of reaction engineering and practical know-how for scale-up necessary for production sites
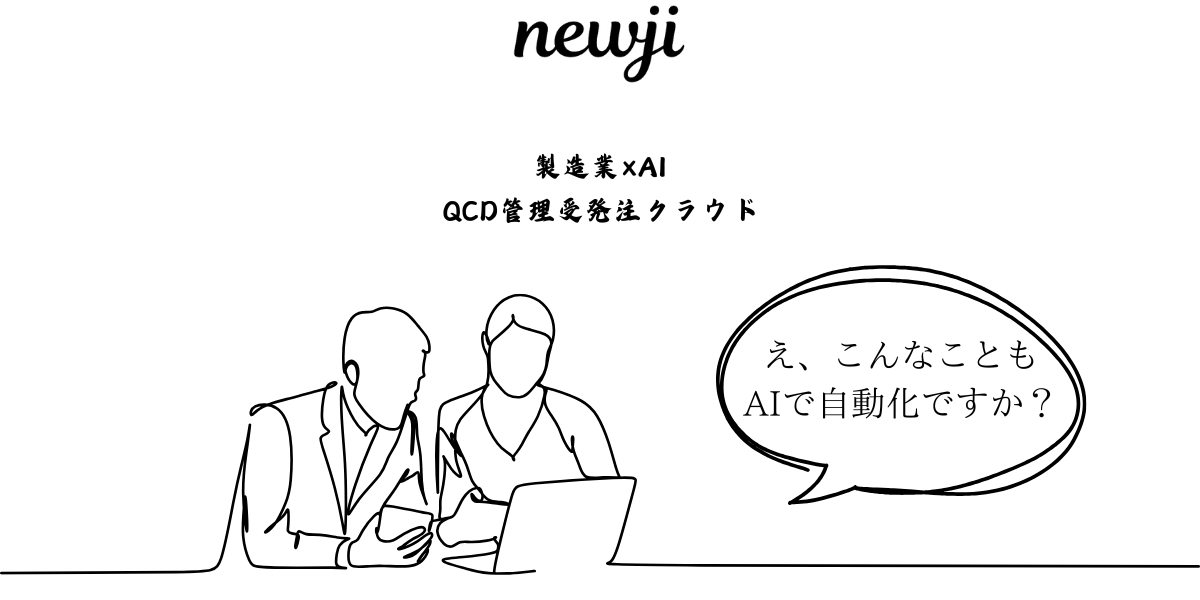
Fundamentals of reaction engineering and practical know-how for scale-up necessary for production sites
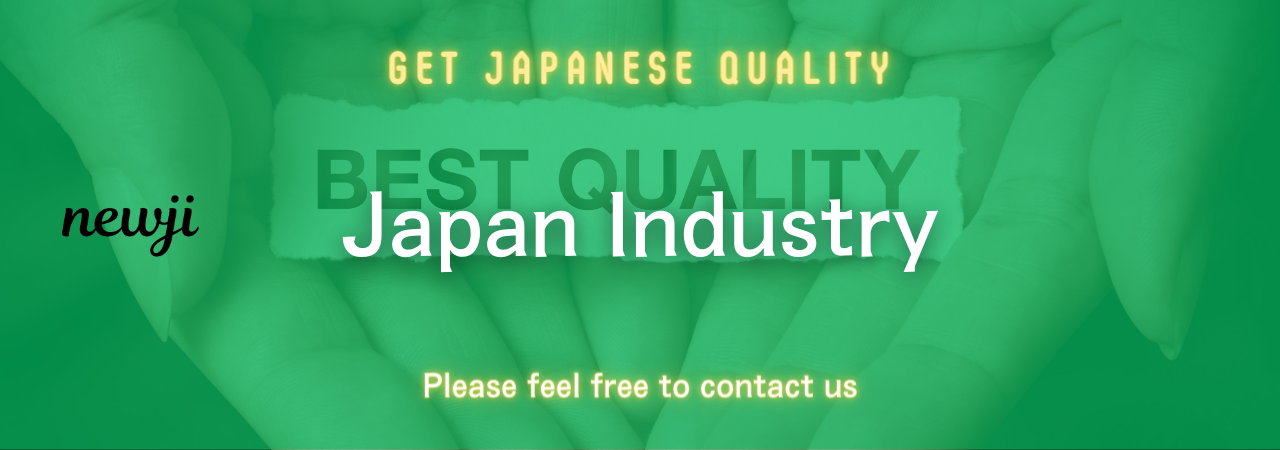
目次
Understanding Reaction Engineering
Reaction engineering is a crucial aspect of chemical engineering that focuses on the design and optimization of chemical reactions on an industrial scale.
It involves the study of chemical kinetics and reactor design to ensure that chemical processes are efficient, safe, and economically viable.
Professionals in this field strive to understand the behavior of chemical reactions to develop methods for scaling up from laboratory to production levels.
Grasping the fundamentals of reaction engineering is essential for anyone involved in the development and manufacture of chemical products.
Chemical Kinetics
Chemical kinetics, a core component of reaction engineering, involves the study of reaction rates and the factors that influence them.
Understanding how and why reactions occur at specific speeds enables engineers to manipulate these variables to achieve desired outcomes.
Factors such as temperature, pressure, concentration, and catalysts can significantly affect the rate of a reaction.
By controlling these components, engineers can optimize reaction conditions, making processes more efficient and cost-effective.
Moreover, understanding kinetic models helps in predicting the behavior of reactions, which is paramount for scaling up from laboratory to industrial production.
Types of Reactors
The choice of reactor is a pivotal decision in reaction engineering and scale-up processes.
Several reactor types exist, each with its features and suitability for various reactions.
The most common types are batch reactors, continuous stirred-tank reactors (CSTR), plug flow reactors (PFR), and packed bed reactors.
– Batch Reactors: These are closed systems where reactions occur without any material entering or leaving during the process.
They are suitable for small-scale production and provide higher levels of control over reaction conditions, making them ideal for pharmaceuticals and specialty chemicals.
– Continuous Stirred-Tank Reactors (CSTR): These involve continuous input and output of materials, ensuring a steady state of operation.
CSTRs are often used for liquid-phase reactions and are advantageous for reactions requiring constant stirring.
– Plug Flow Reactors (PFR): These are tubular reactors where reactants flow through a pipe.
They are beneficial for reactions that need efficient heat transfer and are commonly used in large-scale chemical manufacturing.
– Packed Bed Reactors: These are fixed-bed reactors typically used for gas-phase reactions where catalysts are essential.
They provide excellent contact between the reactants and catalysts, enhancing reaction efficiency.
Each reactor type has distinct characteristics, making them suitable for specific applications.
The correct selection aligns with the nature of the chemical reaction, production scale, and economic considerations.
Practical Know-How for Scale-Up
Scaling up a chemical reaction from laboratory to industrial production is a complex process that requires expertise and careful planning.
Here are some practical steps and considerations to facilitate a successful scale-up.
Understanding Scale-Up Challenges
The scale-up process poses several challenges, including maintaining reaction efficiency, product quality, and safety.
Identifying potential issues early in the process can save time, resources, and mitigate risks.
Laboratory conditions often differ significantly from industrial settings, so comprehensive testing and simulations are vital.
Common challenges include mass and heat transfer limitations, mixing and reactor design issues, and changes in reaction kinetics.
Addressing these concerns is imperative to ensure the scalability of the chemical process.
Simulation and Modeling
Computer simulations and modeling are invaluable tools in the scale-up process.
These technologies allow engineers to predict the behavior of chemical reactions under different conditions and reactor setups.
Simulation software can model fluid dynamics, heat, and mass transfer, providing insights into the reactions on a larger scale.
By using these tools, engineers can optimize the scale-up process, minimize risks, and reduce the need for costly experimental trials.
Pilot Plant Testing
Before full-scale industrial production, pilot plant testing is a crucial step in the scale-up process.
Pilot plants are smaller versions of industrial setups, designed to test the reactions and processes on a larger scale than laboratory experiments.
These tests allow engineers to gather data, identify potential issues, and make necessary adjustments to the process.
Pilot plant trials provide invaluable real-world insights and help validate the results obtained from simulations and modeling.
Safety Considerations
Safety is of paramount importance in any chemical manufacturing process.
Scaling up a reaction increases the potential risks associated with handling larger quantities of hazardous materials.
An in-depth risk assessment and the implementation of safety measures are essential.
Ensuring proper ventilation, storage, and handling procedures minimizes the risk of accidents and exposure to harmful substances.
Regular safety audits and staff training are crucial to maintain a safe working environment throughout the scale-up process.
The Importance of Collaboration
Successful scale-up requires collaboration between multiple departments and experts.
Chemical engineers, process engineers, safety officers, and quality control teams must work together to achieve a common goal.
Effective communication and teamwork ensure that the scale-up process is efficient, safe, and meets production goals.
With everyone contributing their expertise, the transition from laboratory to industrial production can be seamless.
Conclusion
The fundamentals of reaction engineering are critical for scaling up chemical reactions from the laboratory to production sites.
Understanding chemical kinetics, reactor design, and the practicalities of scale-up are essential for developing efficient, safe, and economically viable chemical processes.
Embracing modern technologies, conducting thorough testing, and prioritizing safety are necessary steps to ensure a successful scale-up.
In the dynamic field of reaction engineering, continuous learning and collaboration are key to overcoming challenges and driving innovation.
資料ダウンロード
QCD調達購買管理クラウド「newji」は、調達購買部門で必要なQCD管理全てを備えた、現場特化型兼クラウド型の今世紀最高の購買管理システムとなります。
ユーザー登録
調達購買業務の効率化だけでなく、システムを導入することで、コスト削減や製品・資材のステータス可視化のほか、属人化していた購買情報の共有化による内部不正防止や統制にも役立ちます。
NEWJI DX
製造業に特化したデジタルトランスフォーメーション(DX)の実現を目指す請負開発型のコンサルティングサービスです。AI、iPaaS、および先端の技術を駆使して、製造プロセスの効率化、業務効率化、チームワーク強化、コスト削減、品質向上を実現します。このサービスは、製造業の課題を深く理解し、それに対する最適なデジタルソリューションを提供することで、企業が持続的な成長とイノベーションを達成できるようサポートします。
オンライン講座
製造業、主に購買・調達部門にお勤めの方々に向けた情報を配信しております。
新任の方やベテランの方、管理職を対象とした幅広いコンテンツをご用意しております。
お問い合わせ
コストダウンが利益に直結する術だと理解していても、なかなか前に進めることができない状況。そんな時は、newjiのコストダウン自動化機能で大きく利益貢献しよう!
(Β版非公開)