- お役立ち記事
- Fundamentals of reaction engineering, scale-up in chemical reactors, and its key points
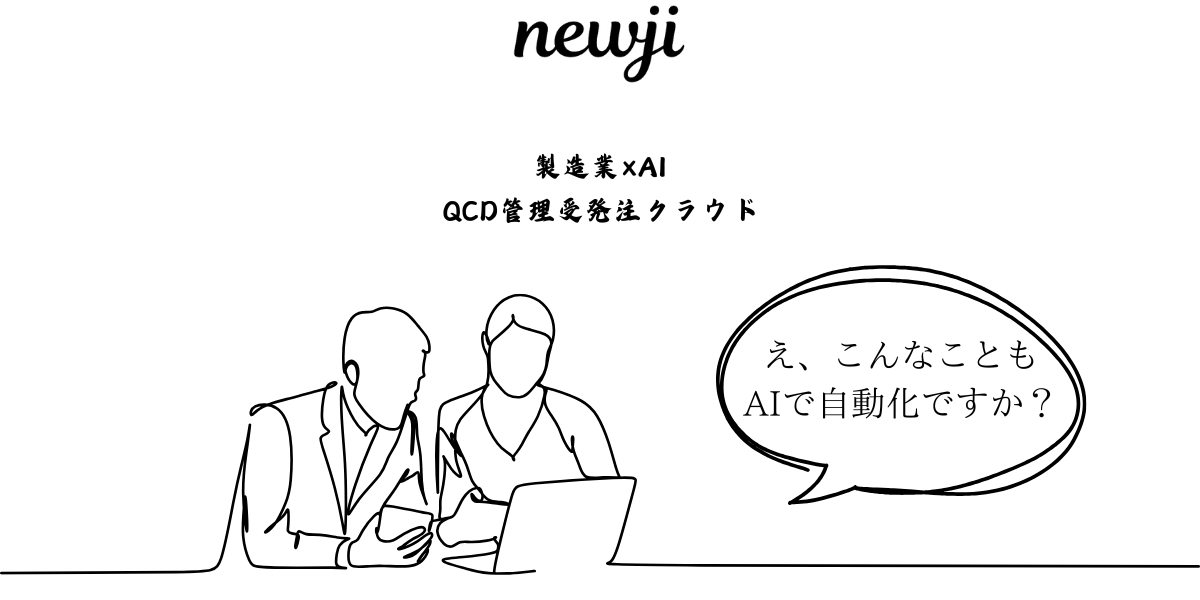
Fundamentals of reaction engineering, scale-up in chemical reactors, and its key points
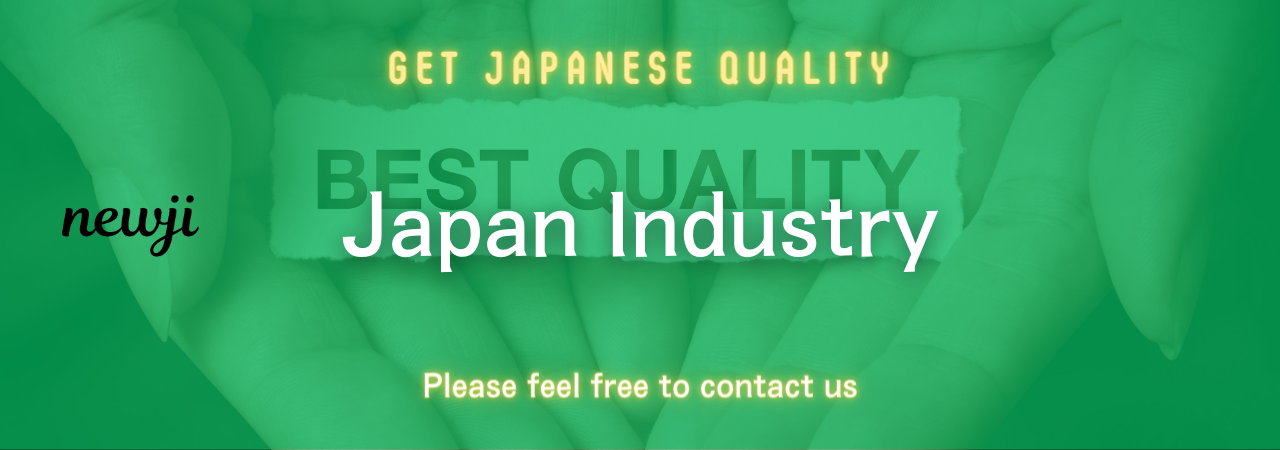
目次
Understanding Reaction Engineering
Reaction engineering is a fundamental aspect of chemical engineering, focusing on the treatment of chemical reactions.
This field involves the analysis and design of reactors where chemical transformations occur.
One key objective is to achieve maximum efficiency and yield from the reactions while optimizing the conditions required for these reactions.
Reaction engineering combines the principles of chemistry, physics, and mathematics.
It aims to model and predict the behavior of chemical processes on different scales.
This understanding is crucial for the successful design and operation of chemical reactors.
Types of Chemical Reactions
Reactions can be broadly classified into several types, each with distinct characteristics.
Some common types of chemical reactions include:
– **Combination Reactions:** Where two or more substances combine to form a single product.
– **Decomposition Reactions:** Where a compound breaks down into two or more simpler substances.
– **Displacement Reactions:** Where an element in a compound is replaced by another element.
– **Redox Reactions:** Involving a transfer of electrons between two species, crucial in many industrial processes.
Understanding these reaction types helps engineers determine the appropriate reactor designs and operational parameters needed.
Scale-Up in Chemical Reactors
Scale-up is the process of increasing the size or capacity of a chemical reactor to handle larger quantities.
This is necessary for moving from laboratory-scale experiments to industrial-scale operations.
It involves replicating the conditions and outputs achieved in smaller reactors on a larger scale.
However, transitioning from small-scale to large-scale systems introduces complexities due to changes in reaction dynamics.
Hence, engineers must carefully consider factors such as heat transfer, mixing, and mass transfer during the scale-up process.
These factors can significantly influence the efficiency and safety of chemical processes in large reactors.
Key Challenges in Scale-Up
Scale-up presents several challenges that engineers must address:
1. **Non-Linear Scaling:** Reaction rates, heat transfer, and mixing processes often don’t scale linearly with reactor size.
2. **Heat Management:** Larger reactors generate more heat, necessitating efficient heat removal systems to prevent overheating.
3. **Mixing Efficiency:** Ensuring effective mixing in larger volumes is crucial to maintain uniform reaction conditions.
4. **Mass Transfer Limitations:** The movement of reactants and products can be limited in larger systems.
Addressing these challenges requires sophisticated modeling and simulation tools to predict the behavior of chemical processes accurately.
Key Points in Scale-Up Process
Successfully scaling up a chemical reactor requires careful consideration of several key points:
1. Detailed Kinetic Studies
Understanding the reaction kinetics is paramount.
Conducting detailed studies on reaction rates and mechanisms helps in developing accurate models for scaling up.
This information guides the design of reactors that operate efficiently under large-scale conditions.
2. Simulation and Modeling
Advanced computer simulations and modeling tools can predict how changes in scale will affect reactor performance.
These tools help engineers identify potential issues before physical scale-up, saving time and resources.
3. Pilot-Plant Testing
Before full-scale production, pilot-plant testing is crucial.
Pilot plants operate on a smaller scale than full industrial units, allowing engineers to test the processes under realistic conditions.
This intermediate stage ensures that potential problems are identified and addressed before final scale-up.
4. Material Selection
Choosing the right materials for reactor construction is critical for ensuring safety and durability.
Materials must withstand the chemical, thermal, and mechanical stresses encountered during operations.
5. Safety Considerations
Safety is a priority in chemical reactor scale-up.
Large-scale reactions involve considerable risk, so designing adequate safety measures and controls is essential.
These may include pressure relief systems, spill containment, and emergency shutdown procedures.
Conclusion
The field of reaction engineering and the process of scaling up chemical reactors play a significant role in maximizing the efficiency and productivity of chemical processes.
By understanding the fundamental principles of reaction types and dynamics, engineers can design reactors that achieve desired outcomes effectively.
Scale-up, while complex, can be managed successfully with careful planning, detailed studies, and the application of advanced simulation tools.
Ultimately, these efforts lead to safer and more efficient chemical production, meeting the demands of various industries while minimizing environmental impact.
Reaction engineering and scale-up are integral to the progress of technology and industry alike.
資料ダウンロード
QCD調達購買管理クラウド「newji」は、調達購買部門で必要なQCD管理全てを備えた、現場特化型兼クラウド型の今世紀最高の購買管理システムとなります。
ユーザー登録
調達購買業務の効率化だけでなく、システムを導入することで、コスト削減や製品・資材のステータス可視化のほか、属人化していた購買情報の共有化による内部不正防止や統制にも役立ちます。
NEWJI DX
製造業に特化したデジタルトランスフォーメーション(DX)の実現を目指す請負開発型のコンサルティングサービスです。AI、iPaaS、および先端の技術を駆使して、製造プロセスの効率化、業務効率化、チームワーク強化、コスト削減、品質向上を実現します。このサービスは、製造業の課題を深く理解し、それに対する最適なデジタルソリューションを提供することで、企業が持続的な成長とイノベーションを達成できるようサポートします。
オンライン講座
製造業、主に購買・調達部門にお勤めの方々に向けた情報を配信しております。
新任の方やベテランの方、管理職を対象とした幅広いコンテンツをご用意しております。
お問い合わせ
コストダウンが利益に直結する術だと理解していても、なかなか前に進めることができない状況。そんな時は、newjiのコストダウン自動化機能で大きく利益貢献しよう!
(Β版非公開)