- お役立ち記事
- Fundamentals of reliability prediction and verification using stress/strength models and reliability statistical theory
月間77,185名の
製造業ご担当者様が閲覧しています*
*2025年2月28日現在のGoogle Analyticsのデータより
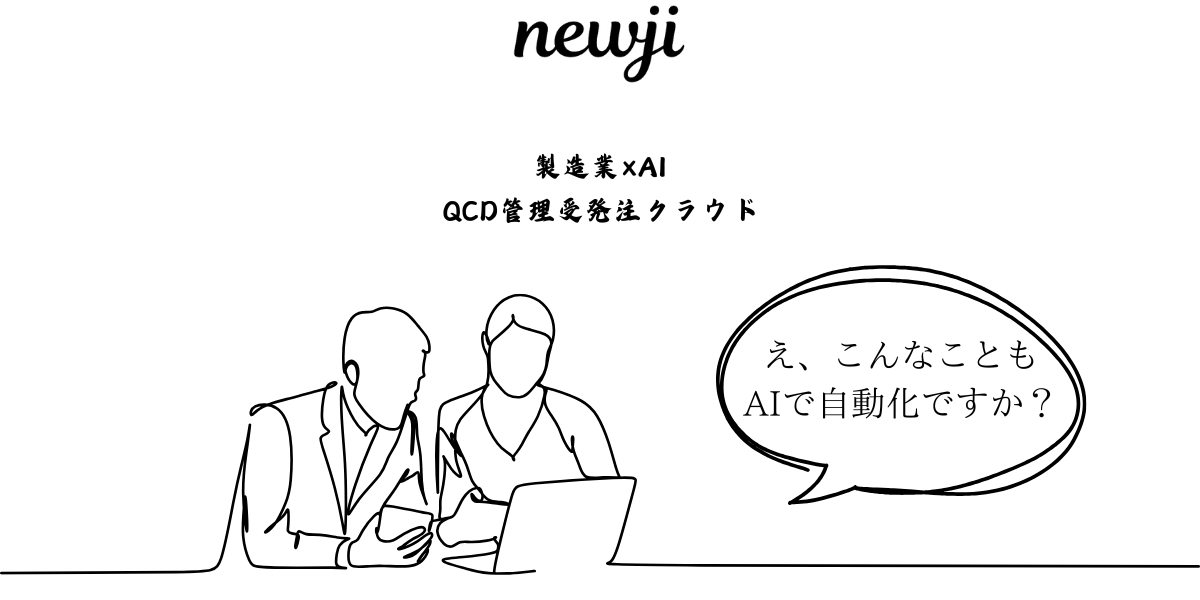
Fundamentals of reliability prediction and verification using stress/strength models and reliability statistical theory
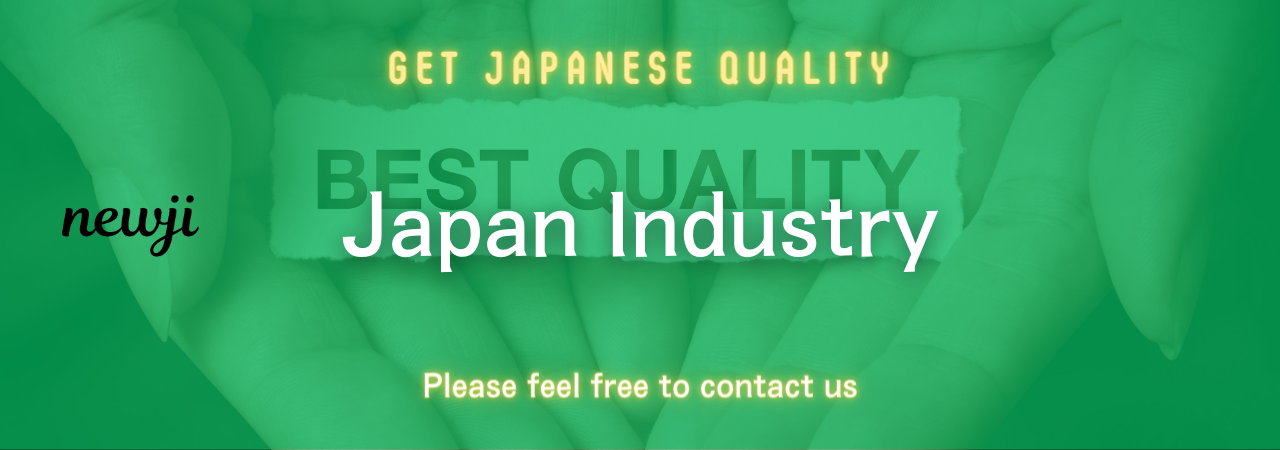
目次
Understanding Reliability Prediction
Reliability prediction is an important concept used by engineers and manufacturers to estimate a product’s performance over time.
This approach helps in identifying potential failures and enhances product design to meet user expectations.
Reliability prediction uses existing data and statistical models to assess how different components will perform under various conditions.
The primary goal is to minimize unexpected failures and ensure customer satisfaction.
There are various methods and models available for reliability prediction.
Some of the most commonly used include the stress/strength model, failure modes and effects analysis, and reliability growth models.
Each of these methods utilizes statistical data and mathematical calculations to predict potential issues and their impact on product performance.
Stress/Strength Models: The Basics
The stress/strength model is a fundamental concept in reliability prediction.
At its core, this model compares the stress applied to a component with the strength or capacity of that component.
Reliability is achieved when the strength exceeds the stress.
Stress can include factors such as mechanical load, temperature changes, and electrical current.
Meanwhile, strength is the ability of a material or component to withstand these stresses without failing.
By analyzing the distribution of stress and strength for a component, engineers can predict the likelihood of failure over a given period.
Application of Stress/Strength Models
To apply stress/strength models effectively, engineers undertake several critical steps.
First, they collect data on the types of stresses a component will endure during its operation.
This could be obtained through field data, simulation, or testing under controlled conditions.
Next, they determine the strength distribution of each component.
Statistical analysis is used to represent both stress and strength as probability distributions.
Engineers compare these distributions to calculate reliability, which is the probability that strength will exceed stress under specified conditions.
This analysis helps identify potential weak points in a design, allowing manufacturers to make necessary adjustments before production.
It also aids in selecting materials and components with the most appropriate strength characteristics for specific applications.
Reliability Statistical Theory
Reliability statistical theory forms the backbone of reliability prediction.
This theory employs statistical methodologies to evaluate and predict product life cycles.
It allows engineers to quantify and express reliability through measurable terms such as mean time to failure (MTTF) or mean time between failures (MTBF).
The theory accommodates different types of data, from historical performance to accelerated life tests.
A key aspect of this theory is the use of probability distributions, like exponential, Weibull, and lognormal, which model time-to-failure data and capture variations in data distribution.
Probability Distributions in Reliability
Probability distributions are fundamental in reliability statistical theory as they help model random variations and uncertainties within product life cycles.
– **Exponential Distribution**: It is often used when the failure rate is constant, which simplifies calculations.
– **Weibull Distribution**: This flexible distribution can adjust to a variety of failure rates, indicating early failures, random failures, or wear-out failures.
– **Lognormal Distribution**: Useful when analyzing complex systems where components age differently, leading to a skewed life distribution.
Each distribution provides insights into the failure mechanism, guiding engineers in refining their reliability predictions.
Verification of Reliability Predictions
Verification is a crucial step following reliability prediction.
This process ensures that the predicted reliability aligns with actual performance outcomes.
Verification involves testing components under expected use conditions to confirm their ability to perform without failure.
Testing methods may include accelerated life testing, where products are exposed to extreme conditions to simulate long-term usage in a shorter timeframe.
Statistical analysis of these tests helps validate the predicted reliability metrics and identify any deviations.
By verifying reliability predictions, manufacturers can refine their models and improve product design and development processes.
The Impact of Reliability on Product Development
Reliability prediction and verification offer significant advantages in product development.
They reduce the risk of costly recalls and warranty claims by enabling designers to address potential failures before mass production.
Moreover, they enhance customer satisfaction by delivering products that meet or exceed reliability expectations.
Reliability prediction also fosters innovation.
By understanding failure mechanisms and how to mitigate them, engineers can explore new materials and technologies that improve product durability and performance.
Additionally, these insights facilitate continuous improvement and maintenance strategies within manufacturing processes.
Conclusion
Understanding the fundamentals of reliability prediction and verification using stress/strength models and reliability statistical theory is essential for product development.
These methods help identify potential failures, refine designs, and ensure products meet performance expectations.
By incorporating reliable methodologies into the engineering and design process, manufacturers can enhance product quality, ensure customer satisfaction, and maintain a competitive edge in the market.
Ultimately, the pursuit of reliability leads to better products, stronger brands, and a more robust engineering landscape.
資料ダウンロード
QCD管理受発注クラウド「newji」は、受発注部門で必要なQCD管理全てを備えた、現場特化型兼クラウド型の今世紀最高の受発注管理システムとなります。
ユーザー登録
受発注業務の効率化だけでなく、システムを導入することで、コスト削減や製品・資材のステータス可視化のほか、属人化していた受発注情報の共有化による内部不正防止や統制にも役立ちます。
NEWJI DX
製造業に特化したデジタルトランスフォーメーション(DX)の実現を目指す請負開発型のコンサルティングサービスです。AI、iPaaS、および先端の技術を駆使して、製造プロセスの効率化、業務効率化、チームワーク強化、コスト削減、品質向上を実現します。このサービスは、製造業の課題を深く理解し、それに対する最適なデジタルソリューションを提供することで、企業が持続的な成長とイノベーションを達成できるようサポートします。
製造業ニュース解説
製造業、主に購買・調達部門にお勤めの方々に向けた情報を配信しております。
新任の方やベテランの方、管理職を対象とした幅広いコンテンツをご用意しております。
お問い合わせ
コストダウンが利益に直結する術だと理解していても、なかなか前に進めることができない状況。そんな時は、newjiのコストダウン自動化機能で大きく利益貢献しよう!
(β版非公開)