- お役立ち記事
- Fundamentals of reliability testing, failure analysis, failure prevention methods, and examples
月間76,176名の
製造業ご担当者様が閲覧しています*
*2025年3月31日現在のGoogle Analyticsのデータより
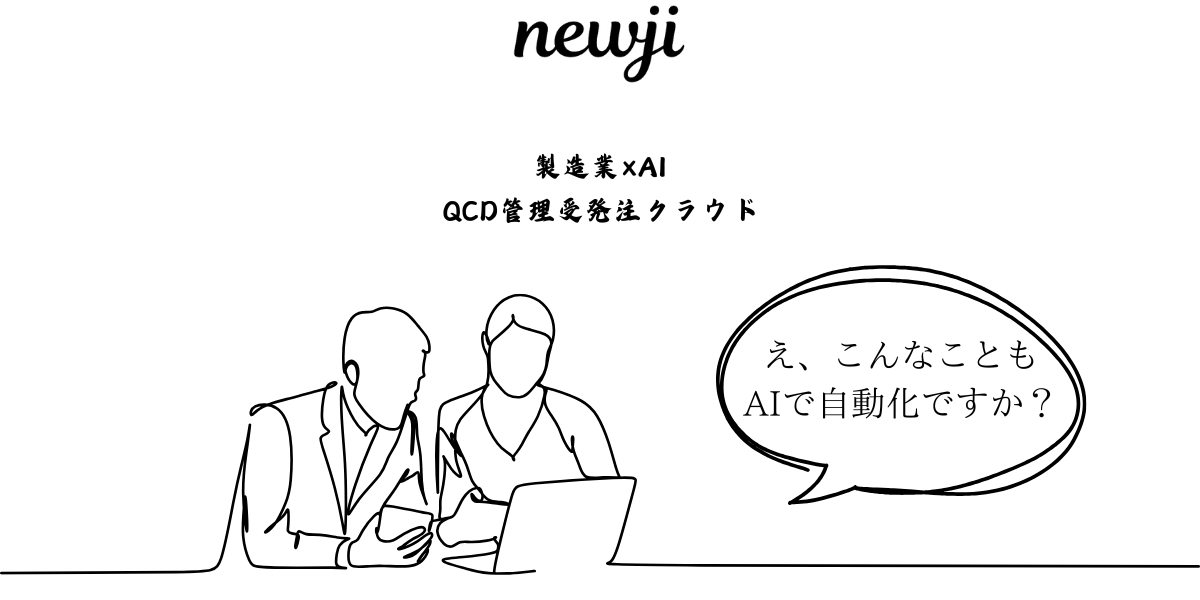
Fundamentals of reliability testing, failure analysis, failure prevention methods, and examples
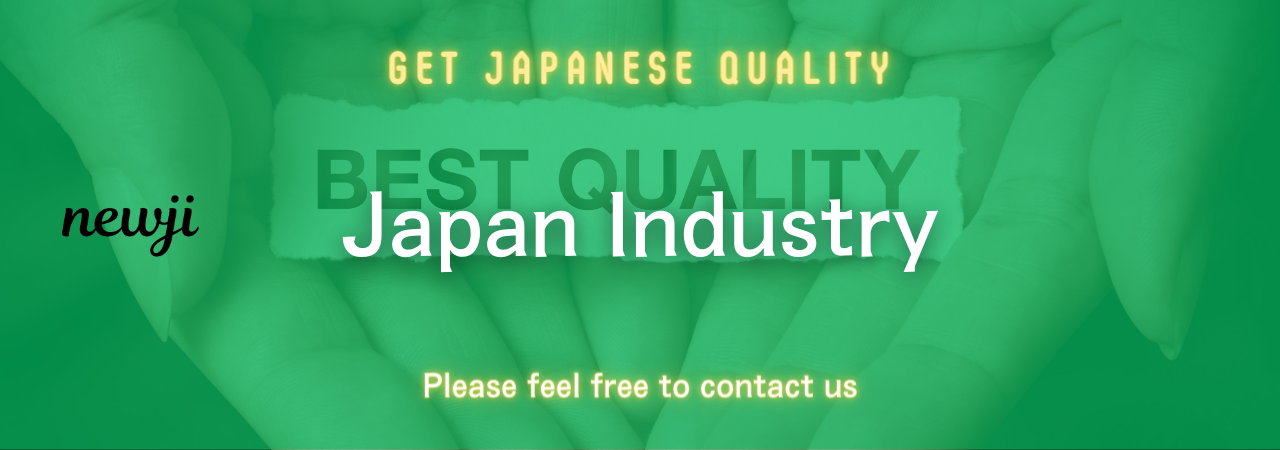
目次
Understanding Reliability Testing
Reliability testing is a crucial process in product development and quality assurance, aiming to ensure that a product or system performs its intended function under specified conditions for a designated period.
This type of testing is especially important in industries such as automotive, electronics, and aerospace, where product failures can lead to significant risks and liabilities.
There are several methods used in reliability testing.
The most common include life testing, accelerated life testing, and environmental testing.
Life testing involves evaluating a product over its expected life span to understand potential failure modes and rates.
Accelerated life testing speeds up the aging process, allowing testers to simulate the product’s behavior over time by increasing stress levels such as temperature or voltage.
Environmental testing assesses how products perform under various environmental conditions, such as extreme temperatures, humidity, or vibration.
The Role of Failure Analysis
Failure analysis is a systematic investigation into why a product, component, or process has failed.
Understanding the cause of failure is essential in improving reliability and preventing future occurrences.
This analysis often involves a detailed examination of the failed product, considering factors such as the design, materials used, and the conditions under which the product was operating.
Several techniques are used in failure analysis, including visual inspection, microscopic examination, and material testing.
Advanced methods, such as computer simulations and non-destructive testing, may also be employed.
The goal is to identify the root cause of the failure and recommend necessary changes to improve product performance and reliability.
Steps in Failure Analysis
1. **Data Collection:** Gather all relevant information about the failure, including operating conditions, maintenance records, and environmental factors.
2. **Initial Examination:** Conduct a visual inspection and document any immediate observations.
3. **Detailed Analysis:** Use various tools and techniques to delve deeper into the failure, such as scanning electron microscopy (SEM) or X-ray diffraction.
4. **Root Cause Identification:** Identify the underlying cause(s) of the failure through thorough analysis and testing.
5. **Reporting and Recommendations:** Compile findings into a report and suggest corrective actions to prevent recurrence.
Failure Prevention Methods
Preventing failures is a key component of reliability engineering.
By identifying potential risks and implementing measures to mitigate them, organizations can enhance the durability and performance of their products.
Design for Reliability
A proactive approach to failure prevention begins with design.
Incorporating reliability into the design phase ensures that reliability requirements are considered from the beginning.
This includes selecting robust materials, using redundant systems where necessary, and conducting stress testing early in the development cycle.
Regular Maintenance and Monitoring
Routine maintenance and monitoring are critical in preventing unexpected failures.
Implementing a preventive maintenance schedule can help identify issues before they lead to significant problems.
Moreover, using condition-monitoring tools such as vibration analysis and thermal imaging can provide insights into equipment health, allowing for timely interventions.
Quality Control and Testing
Rigorous quality control measures and testing protocols are essential in minimizing the risk of failure.
Quality audits, both internal and external, can ensure that processes meet specified standards.
Additionally, real-time testing and feedback during production can help identify defects early, reducing the likelihood of failures post-production.
Real-World Examples of Reliability Testing and Failure Analysis
Several industries have set benchmarks for successful reliability testing and failure prevention strategies:
Automotive Industry
In the automotive sector, reliability testing is paramount.
Manufacturers perform extensive testing on vehicle components such as engines, brakes, and electronics to ensure safety and performance.
Failure analysis plays a critical role in recalls and improvements, as seen when issues like airbags or ignition systems become common across specific models.
Electronics Industry
For electronics, reliability testing often focuses on component life cycles and stress endurance.
Smartphones and other gadgets undergo rigorous testing to ensure they can withstand drops, water exposure, and long-term usage without failing.
When failures occur, as with battery malfunctions, comprehensive failure analysis helps manufacturers correct defects and enhance product safety.
Aerospace Industry
In aerospace, failure prevention is of utmost importance due to the high stakes involved.
Reliability testing under extreme conditions is routine, and failure analysis can involve complex simulations to recreate scenarios leading to a failure.
Pre-emptive measures help in designing aircraft that meet rigorous safety standards.
In summary, understanding and applying the principles of reliability testing, failure analysis, and failure prevention are vital in developing products that are safe, durable, and perform as expected.
Through diligent testing, analysis, and quality control, organizations can mitigate risks, enhance product quality, and ultimately achieve customer satisfaction.
資料ダウンロード
QCD管理受発注クラウド「newji」は、受発注部門で必要なQCD管理全てを備えた、現場特化型兼クラウド型の今世紀最高の受発注管理システムとなります。
ユーザー登録
受発注業務の効率化だけでなく、システムを導入することで、コスト削減や製品・資材のステータス可視化のほか、属人化していた受発注情報の共有化による内部不正防止や統制にも役立ちます。
NEWJI DX
製造業に特化したデジタルトランスフォーメーション(DX)の実現を目指す請負開発型のコンサルティングサービスです。AI、iPaaS、および先端の技術を駆使して、製造プロセスの効率化、業務効率化、チームワーク強化、コスト削減、品質向上を実現します。このサービスは、製造業の課題を深く理解し、それに対する最適なデジタルソリューションを提供することで、企業が持続的な成長とイノベーションを達成できるようサポートします。
製造業ニュース解説
製造業、主に購買・調達部門にお勤めの方々に向けた情報を配信しております。
新任の方やベテランの方、管理職を対象とした幅広いコンテンツをご用意しております。
お問い合わせ
コストダウンが利益に直結する術だと理解していても、なかなか前に進めることができない状況。そんな時は、newjiのコストダウン自動化機能で大きく利益貢献しよう!
(β版非公開)