- お役立ち記事
- Fundamentals of resin product design and injection molding for mass production, and key points to prevent molding defects.
月間76,176名の
製造業ご担当者様が閲覧しています*
*2025年3月31日現在のGoogle Analyticsのデータより
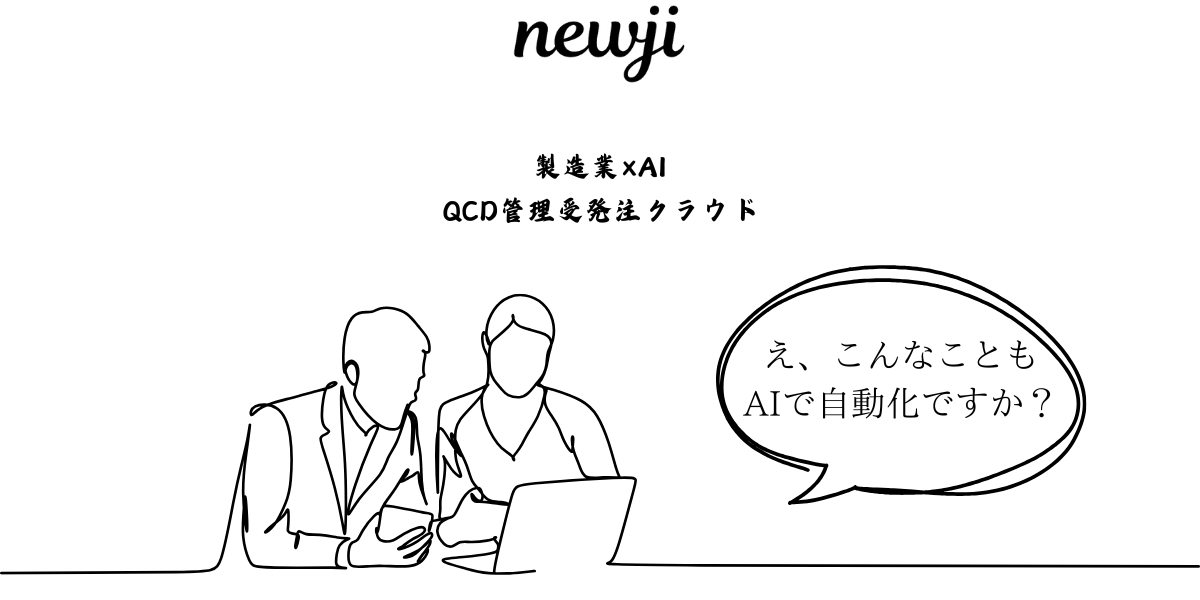
Fundamentals of resin product design and injection molding for mass production, and key points to prevent molding defects.
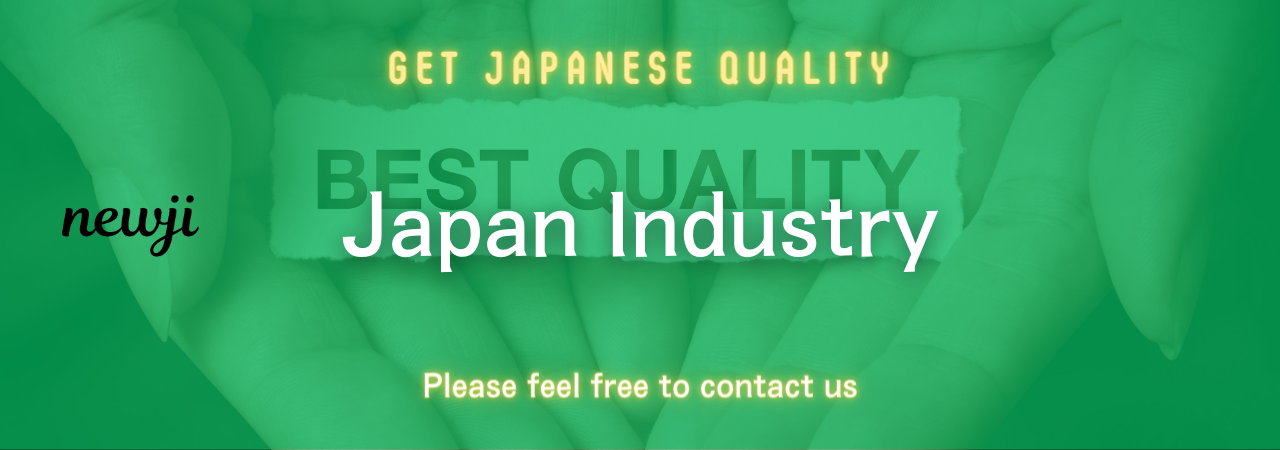
目次
Introduction to Resin Product Design
Resin product design is a critical aspect of manufacturing that blends creativity with technical precision.
Whether creating everyday household items or complex components for machinery, the fundamentals of resin design lay the groundwork for successful mass production.
Understanding these basics is essential for both designers and engineers to produce high-quality products efficiently.
In the realm of resin product design, the three primary considerations include material selection, design structure, and functionality.
Material choice greatly influences the durability, flexibility, and cost-effectiveness of the final product.
Common resins like polyethylene, polypropylene, and ABS have unique properties that must align with the intended application’s requirements.
Choosing the right material is the first step in ensuring product success.
Structural design elements come next, where designers focus on the shape, thickness, and features of the product.
A well-structured design not only enhances aesthetics but also optimizes performance and feasibility for mass production.
Incorporating features that facilitate easy assembly, reduce weight, and enhance strength are often priorities.
Having a thorough understanding of the end use is critical to developing a product that meets all necessary specifications without unnecessary complexity.
Functionality, the third pillar, ensures that the resin product not only meets design goals but also performs reliably and safely under expected conditions.
During the design phase, considering how the product will interact with other components, withstand environmental factors, and adhere to compliance standards is vital.
Thus, the fundamentals of resin product design set the stage for successful injection molding, a key process in turning designs into tangible products.
The Injection Molding Process
Injection molding is a widely used manufacturing process for mass-producing plastic parts with precision and speed.
At its core, the process involves injecting molten resin into a mold cavity where it cools and solidifies into the final product shape.
The injection molding process consists of several stages: material preparation, injection, cooling, and ejection.
The first step, material preparation, involves selecting and preparing the right resin material.
This includes drying the resin granules to remove any moisture, as moisture can lead to defects like bubbles and weak spots.
The dried resin is then fed into the machine’s hopper, ready for the next step.
During the injection phase, the resin is heated to its melting point and injected into a precisely designed mold.
This step requires careful control of temperature, pressure, and injection speed to ensure the material fills the mold completely and consistently.
High precision in mold design and machine settings is crucial to prevent defects and ensure uniformity in product dimensions.
Once injected, the resin begins to cool and harden within the mold.
The cooling phase is critical and can vary in duration depending on factors like the thickness of the product and the type of resin used.
During this phase, maintaining uniform cooling rates is essential to prevent warping, shrinkage, and other defects.
Finally, the product is ejected from the mold.
After ensuring it is adequately cooled and solidified, ejector pins or plates gently push the new product out of the mold cavity.
This step must be performed with care to avoid damaging the product, especially if it has delicate features.
Preventing Molding Defects
Defects in injection molding can significantly impact productivity and quality, potentially leading to increased costs and wasted resources.
Understanding common molding defects and how to prevent them is fundamental for optimal production outcomes.
One prevalent defect is sink marks, which occur when the plastic in thicker areas cools and contracts more than in thinner sections.
To prevent sink marks, designers should aim for uniform wall thickness and consider features like ribs or fillets that can reinforce and support the structure.
Warping is another common defect, typically caused by uneven cooling.
Ensuring that the mold and cooling systems enable even heat dissipation can help mitigate warping.
Material selection also plays a role, as some resins are more prone to warping than others.
Flash, a condition where excess material leaks out the sides of the mold, usually results from improper clamp force or mold damage.
Regular maintenance and careful setup of the mold can go a long way in preventing flash.
Additionally, using the correct clamping force for the particular resin and mold combination is essential.
Short shots, where the product is not fully formed due to insufficient material filling the mold, are often addressed by optimizing injection pressure and speed.
Ensuring the mold is properly vented can also help avoid this issue by enabling trapped air to escape.
Key Considerations for Mass Production
When scaling up from a prototype to high-volume production, several key considerations ensure the process remains efficient and cost-effective.
Mold design and setup are paramount, as they dictate the efficiency of the injection molding process.
Using high-quality materials for the mold, such as steel, can prolong its life and ensure consistency across all units produced.
Process optimization is another crucial consideration.
Implementing automation and monitoring systems allows for tight control over manufacturing variables, minimizing human error and enhancing throughput.
Optimized processes can lead to reduced cycle times and lower energy consumption, positively impacting the bottom line.
Logistics and supply chain considerations must also be factored in.
Maintaining adequate inventory levels of resin materials, components, and finished products ensures seamless production and fulfillment.
Establishing strong relationships with suppliers and implementing robust inventory management systems can prevent sudden shortages and delays.
Finally, emphasis on quality control cannot be overstated.
Implementing rigorous inspection protocols at various stages of production helps identify issues early, reducing waste and rework.
Investing in high-resolution inspection equipment and skilled personnel ensures that the final products meet all required standards before reaching customers.
Conclusion
Understanding the fundamentals of resin product design and injection molding is essential for anyone involved in the production of plastic parts.
From selecting the right material to ensuring precision in mold design and process optimization, each step plays a pivotal role in achieving successful mass production.
By taking proactive measures to prevent defects and focusing on quality control, manufacturers can produce high-quality resin products that meet both functional and aesthetic demands.
In turn, this approach leads to satisfied customers, reduced costs, and a competitive edge in the marketplace.
資料ダウンロード
QCD管理受発注クラウド「newji」は、受発注部門で必要なQCD管理全てを備えた、現場特化型兼クラウド型の今世紀最高の受発注管理システムとなります。
ユーザー登録
受発注業務の効率化だけでなく、システムを導入することで、コスト削減や製品・資材のステータス可視化のほか、属人化していた受発注情報の共有化による内部不正防止や統制にも役立ちます。
NEWJI DX
製造業に特化したデジタルトランスフォーメーション(DX)の実現を目指す請負開発型のコンサルティングサービスです。AI、iPaaS、および先端の技術を駆使して、製造プロセスの効率化、業務効率化、チームワーク強化、コスト削減、品質向上を実現します。このサービスは、製造業の課題を深く理解し、それに対する最適なデジタルソリューションを提供することで、企業が持続的な成長とイノベーションを達成できるようサポートします。
製造業ニュース解説
製造業、主に購買・調達部門にお勤めの方々に向けた情報を配信しております。
新任の方やベテランの方、管理職を対象とした幅広いコンテンツをご用意しております。
お問い合わせ
コストダウンが利益に直結する術だと理解していても、なかなか前に進めることができない状況。そんな時は、newjiのコストダウン自動化機能で大きく利益貢献しよう!
(β版非公開)