- お役立ち記事
- Fundamentals of screw fasteners, fatigue strength improvement and loosening prevention technology
月間76,176名の
製造業ご担当者様が閲覧しています*
*2025年3月31日現在のGoogle Analyticsのデータより
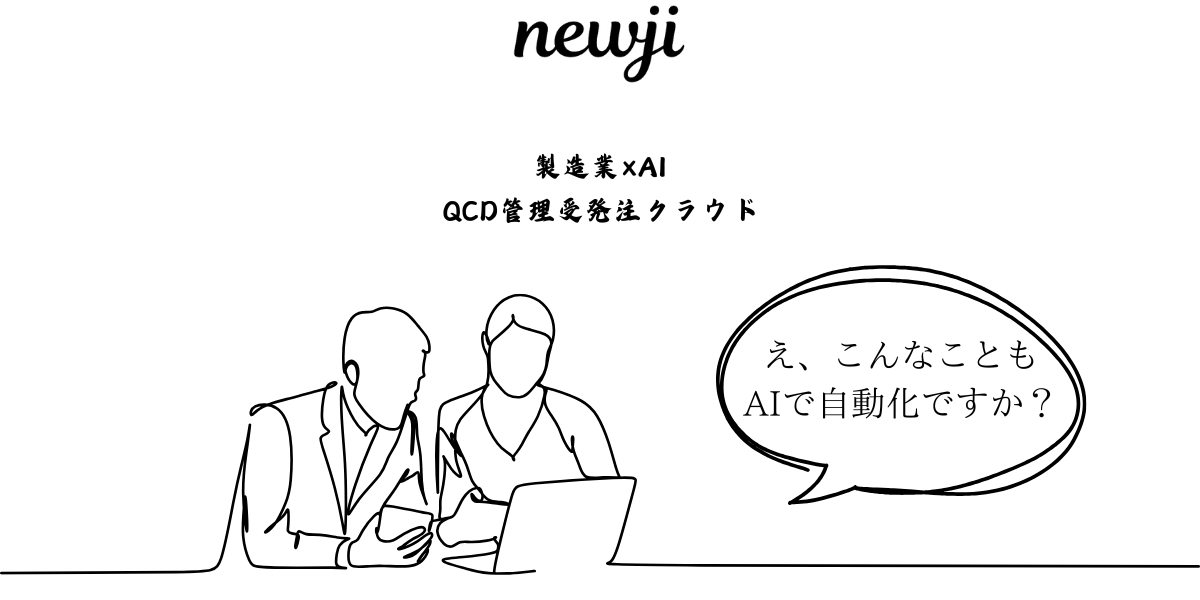
Fundamentals of screw fasteners, fatigue strength improvement and loosening prevention technology
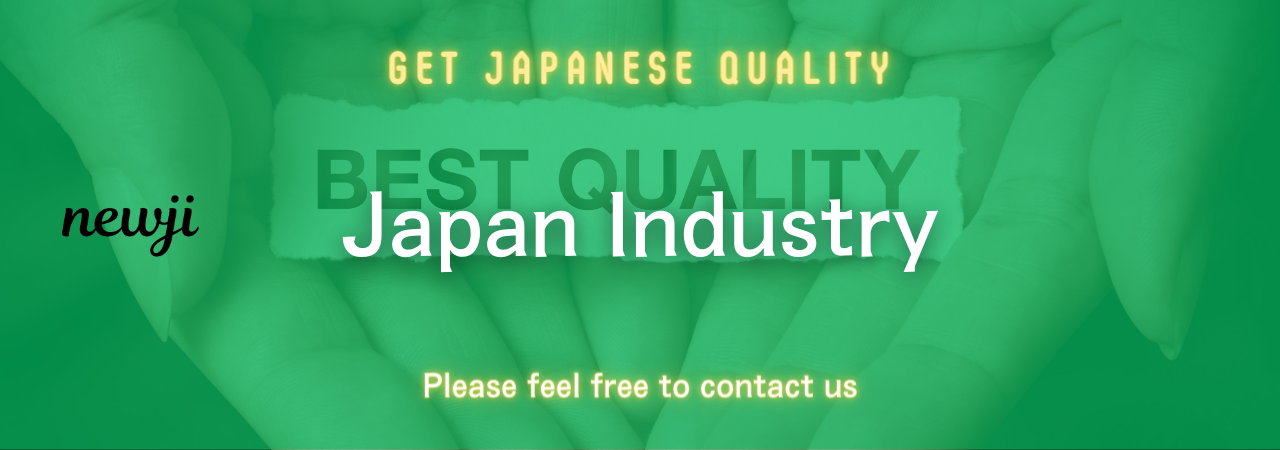
目次
Understanding Screw Fasteners
Screw fasteners are an essential component in various industries, serving numerous functions from holding pieces together to allowing for easy assembly and disassembly of parts.
Understanding their fundamentals is key to maximizing their effectiveness and ensuring the integrity of the structures they help build.
Screws are characterized by their helical structure, designed to convert rotational motion into linear motion.
This simple yet ingenious design makes them incredibly versatile and indispensable in mechanical assemblies.
Types of Screw Fasteners
There are numerous types of screw fasteners, each suited for specific applications.
Common types include machine screws, wood screws, sheet metal screws, and self-tapping screws, among others.
Machine screws are precision-threaded fasteners often used with nuts or tapped holes.
Wood screws, designed for fastening wood, have a tapered shank that helps create a secure grip in timber.
Sheet metal screws, identifiable by their sharp points and durable threads, are perfect for binding together sheet metal or other hard surfaces.
Self-tapping screws tap their own hole as they are driven in, making them extremely useful for quick assemblies.
Understanding the appropriate type of screw fastener for your application is the first step in ensuring a successful project outcome.
Materials Used in Screw Fasteners
Screw fasteners are available in a variety of materials, each offering different characteristics like strength, corrosion resistance, and cost-effectiveness.
Common materials include steel, stainless steel, brass, and aluminum.
Steel screws are preferred for their strength and cost-efficiency, although they may require a protective coating for corrosion resistance.
Stainless steel screws, though more expensive, offer superior resistance to rust and are perfect for harsh environments.
Brass screws are excellent for aesthetic purposes and provide good corrosion resistance, often used in electrical applications due to their conductivity.
Aluminum screws, being lightweight and resistant to corrosion, are used where weight reduction is crucial.
Selecting the right material is crucial for the longevity and performance of the screw fastener in its intended application.
Improving Fatigue Strength
Fatigue strength is an important consideration in the performance of screw fasteners, as it determines the fastener’s ability to withstand repeated loading and unloading cycles.
Over time, exposure to these cycles can lead to the formation of cracks and eventual failure, especially if the fastener is not properly designed or installed.
Design Considerations for Fatigue Strength
Improving fatigue strength can begin as early as the design phase.
Selecting the appropriate materials and coatings, as well as optimizing the geometry of the fastener, can significantly enhance its fatigue performance.
For instance, fasteners with rolled threads exhibit higher fatigue resistance compared to those with cut threads due to the work-hardening and smoother surface finish achieved through the rolling process.
Additionally, incorporating a transition radius between the shank and the head can help reduce stress concentrations that often lead to fatigue failure.
Proper Installation Techniques
Proper installation is crucial to maintaining the fatigue strength of screw fasteners.
Applying the correct torque during installation is essential to ensure an optimal clamp load, which helps distribute the applied load evenly across all fasteners in the assembly.
Excessive torque can cause overloading and lead to premature fatigue failure, while insufficient torque can lead to loosening and joint integrity loss.
Using calibrated tools and following manufacturer specifications can ensure proper torque application.
Regular maintenance and inspections are also vital to identify potential fatigue issues before they result in failure.
Loosening Prevention Technology
One of the common challenges faced with screw fasteners is the risk of loosening over time, especially under dynamic loads or vibration.
Loose fasteners can compromise the integrity of the entire assembly, leading to failures.
Thankfully, various technologies and methods have been developed to prevent loosening.
Mechanical Locking Solutions
Mechanical locking solutions are physical features or additional components designed to secure fasteners against loosening.
Common examples include lock washers, lock nuts, and lock wire.
Lock washers, such as split washers or star washers, provide tension and bite into the material to resist rotation.
Lock nuts are equipped with a nylon insert or other friction-locking mechanism that helps maintain tension even under vibration.
Lock wire involves using a thin wire to tie adjacent fasteners together, offering a reliable mechanical connection that prevents rotation.
Chemical Locking Solutions
Chemical locking solutions involve the use of adhesives or bonding compounds applied to the threads of the fasteners.
These solutions cure to form a cohesive layer that fills the gaps between the threads, enhancing friction and resistance to loosening.
Threadlocking adhesives, such as anaerobic adhesives, are popular for their ability to withstand various environmental conditions and maintain their locking properties over time.
Applying these solutions correctly is crucial, as improper application can either weaken the bond or make future disassembly difficult.
Conclusion
Screw fasteners are fundamental components that play a critical role in many types of assemblies.
By understanding their types, materials, and proper use, as well as methods for improving fatigue strength and preventing loosening, manufacturers and engineers can ensure reliable, long-lasting connections.
Investing time in selecting the right screw fasteners and implementing proper design and installation techniques can lead to enhanced performance and reduced maintenance costs.
As technology advances, new solutions continue to emerge, offering exciting prospects for innovation in the field of screw fasteners.
資料ダウンロード
QCD管理受発注クラウド「newji」は、受発注部門で必要なQCD管理全てを備えた、現場特化型兼クラウド型の今世紀最高の受発注管理システムとなります。
ユーザー登録
受発注業務の効率化だけでなく、システムを導入することで、コスト削減や製品・資材のステータス可視化のほか、属人化していた受発注情報の共有化による内部不正防止や統制にも役立ちます。
NEWJI DX
製造業に特化したデジタルトランスフォーメーション(DX)の実現を目指す請負開発型のコンサルティングサービスです。AI、iPaaS、および先端の技術を駆使して、製造プロセスの効率化、業務効率化、チームワーク強化、コスト削減、品質向上を実現します。このサービスは、製造業の課題を深く理解し、それに対する最適なデジタルソリューションを提供することで、企業が持続的な成長とイノベーションを達成できるようサポートします。
製造業ニュース解説
製造業、主に購買・調達部門にお勤めの方々に向けた情報を配信しております。
新任の方やベテランの方、管理職を対象とした幅広いコンテンツをご用意しております。
お問い合わせ
コストダウンが利益に直結する術だと理解していても、なかなか前に進めることができない状況。そんな時は、newjiのコストダウン自動化機能で大きく利益貢献しよう!
(β版非公開)