- お役立ち記事
- Fundamentals of sintering technology and its application to adding and improving functionality by controlling the microstructure of ceramics
月間76,176名の
製造業ご担当者様が閲覧しています*
*2025年3月31日現在のGoogle Analyticsのデータより
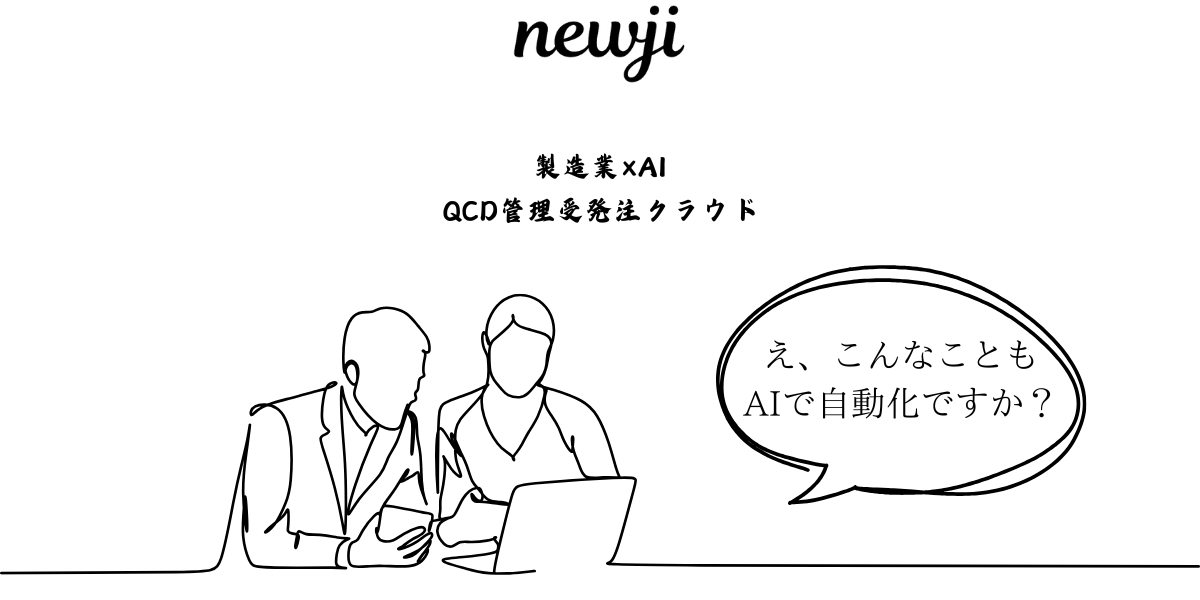
Fundamentals of sintering technology and its application to adding and improving functionality by controlling the microstructure of ceramics
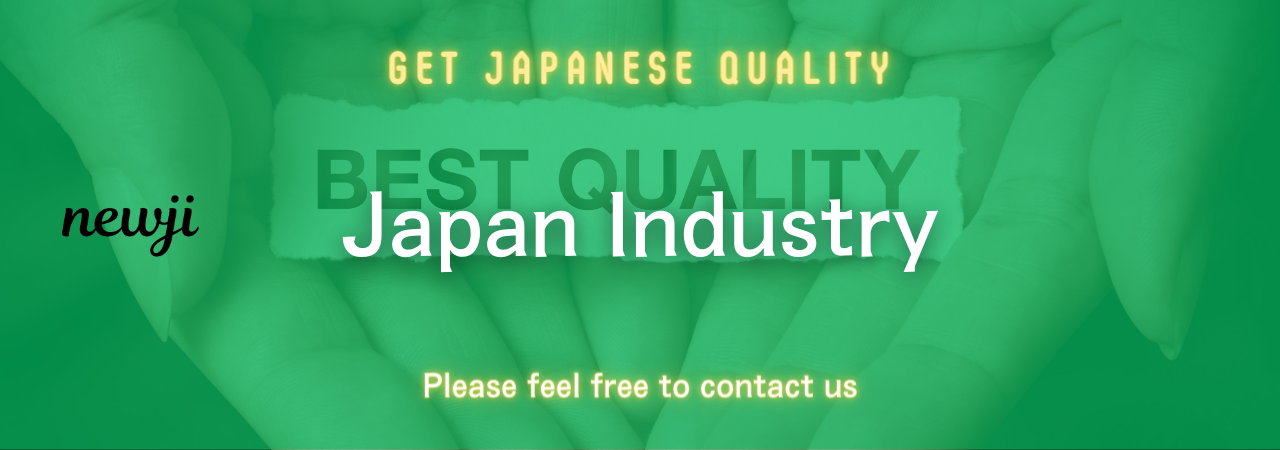
目次
Understanding Sintering Technology
Sintering is a widely used technology in the field of materials science, particularly in the production and enhancement of ceramics.
The process involves compacting and forming a solid mass of material by heat or pressure without melting it to the point of liquefaction.
This technique plays a pivotal role in controlling the microstructure of ceramics, thereby improving their functionality.
What is Sintering?
Sintering is a manufacturing process that uses heat to compact powders into a solid form.
The process is essential in producing items like ceramic components, metal parts, and some types of plastic items.
During sintering, the powder particles adhere to each other at the points of contact, allowing for the densification of the material without going through a liquid phase.
This leads to a reduction in porosity and enhances mechanical properties such as strength, electrical conductivity, translucency, and thermal conductivity.
Types of Sintering Processes
Sintering can be classified into several types depending on the method and energy source used.
Solid State Sintering
Solid-state sintering does not involve the presence of a liquid phase.
In this type, atomic diffusion between powder particles occurs through solid-state processes.
This is the most straightforward and common approach, especially for ceramics that have high melting points.
Liquid Phase Sintering
Liquid phase sintering involves a small quantity of liquid to enhance particle rearrangement.
The presence of this liquid phase helps in better particle packing, reducing porosity, and strengthening the material.
Viscous Sintering
Viscous sintering is a process relevant for glassy materials where the entire body is in a viscous state without a distinct solid framework structure.
The material flows while adhering to specific heat conditions.
The Microstructural Control in Ceramics
Microstructure refers to the structure of the solid material observed under a microscope.
The components include grains, any pores, and the boundaries between different grains.
The microstructure significantly influences the properties of a ceramic material.
By controlling these components through sintering, it’s possible to dramatically improve the functionality of ceramics.
Porosity Management
One of the key aims in sintering is to manage the porosity of the material.
Porosity affects mechanical strength, electrical properties, and thermal conductivity.
Through the sintering process, pores present during the initial powder compaction become smaller or entirely disappear, hence strengthening the end product.
Grain Size Control
Grain size within the microstructure is another critical element.
Smaller grain sizes generally lead to higher strength and better finish.
Sintering allows for control over grain growth through the adjustment of temperature and time, ultimately affecting the overall durability of the material.
Optimization of Grain Boundaries
Grain boundaries can either improve or degrade a material’s properties based on their optimization.
In ceramics, the characteristics of these boundaries affect functionality by influencing toughness, resistance to fracture, and other related properties.
Sintering enables the fine-tuning of these boundaries, optimizing the performance of ceramics for various applications.
Applications of Sintering in Ceramics
Sintering has broad applications across different kinds of ceramic products, each benefiting from the enhanced properties brought about by precise microstructural control.
Electrical Ceramics
In the electronics industry, ceramics produced via sintering are used in capacitors, insulators, and resistors.
For such applications, electrical properties like permittivity, conductivity, and resistivity are critically important.
Sintering can effectively tailor these properties to the desired specifications through microstructural adjustments.
Structural Ceramics
Ceramics used for structural applications need to be extraordinarily tough and wear-resistant.
This includes components for the aerospace sector, automotive engines, and bioceramics for prostheses.
Sintering strengthens these materials by optimizing their densification and grain boundary properties.
Ceramic Filters and Membranes
In environmental and chemical engineering, sintering is useful for producing highly efficient ceramic filters and membranes.
These products require precise porosity and permeability which are achievable through controlled sintering processes.
The Future of Sintering Technology
The future of sintering technology looks promising with ongoing research dedicated to expanding its boundaries.
Innovations such as spark plasma sintering and the use of additives to enhance sinterability are paving the way for even greater control over ceramic microstructures.
Future advancements are expected to focus on increased energy efficiency, reduction in processing times, and the applicability of sintering technologies to a broader range of materials.
Efforts are also underway to make the process more environmentally friendly with less waste and reduced emissions.
As the demand for high-performance materials continues to grow in various sectors, sintering technology holds the potential to meet these needs by providing strong, efficient, and adaptable ceramic products.
資料ダウンロード
QCD管理受発注クラウド「newji」は、受発注部門で必要なQCD管理全てを備えた、現場特化型兼クラウド型の今世紀最高の受発注管理システムとなります。
ユーザー登録
受発注業務の効率化だけでなく、システムを導入することで、コスト削減や製品・資材のステータス可視化のほか、属人化していた受発注情報の共有化による内部不正防止や統制にも役立ちます。
NEWJI DX
製造業に特化したデジタルトランスフォーメーション(DX)の実現を目指す請負開発型のコンサルティングサービスです。AI、iPaaS、および先端の技術を駆使して、製造プロセスの効率化、業務効率化、チームワーク強化、コスト削減、品質向上を実現します。このサービスは、製造業の課題を深く理解し、それに対する最適なデジタルソリューションを提供することで、企業が持続的な成長とイノベーションを達成できるようサポートします。
製造業ニュース解説
製造業、主に購買・調達部門にお勤めの方々に向けた情報を配信しております。
新任の方やベテランの方、管理職を対象とした幅広いコンテンツをご用意しております。
お問い合わせ
コストダウンが利益に直結する術だと理解していても、なかなか前に進めることができない状況。そんな時は、newjiのコストダウン自動化機能で大きく利益貢献しよう!
(β版非公開)