- お役立ち記事
- Fundamentals of sliding mode control
月間76,176名の
製造業ご担当者様が閲覧しています*
*2025年3月31日現在のGoogle Analyticsのデータより
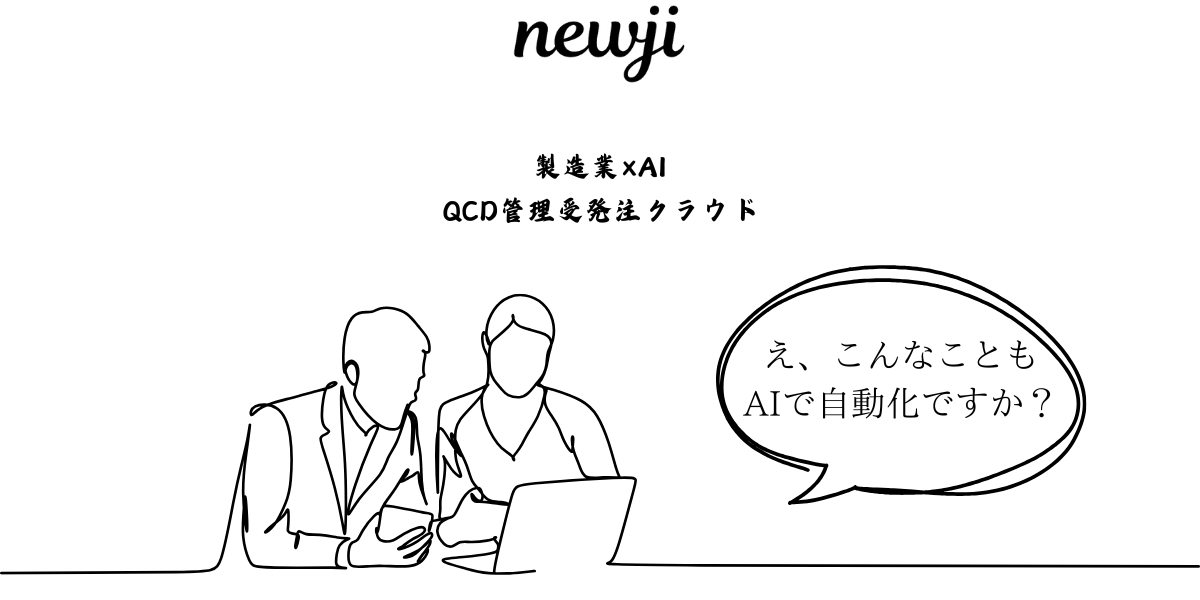
Fundamentals of sliding mode control
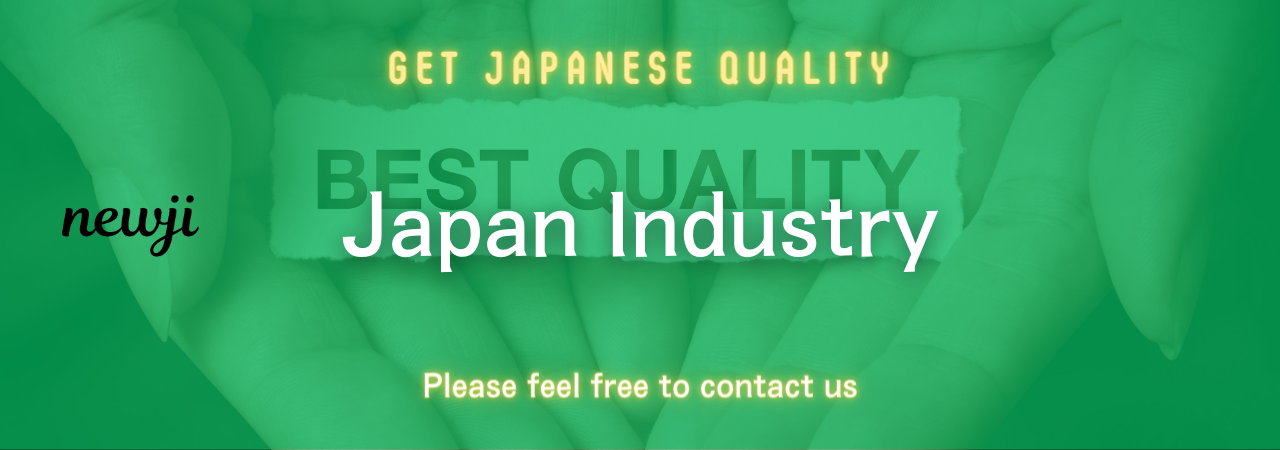
Understanding Sliding Mode Control
Sliding mode control is a powerful and dynamic approach used in control systems engineering to manage and maintain the behavior of complex systems.
It is particularly effective in dealing with systems that experience uncertainties and disturbances, providing robustness and reliability.
In this article, we will explore the fundamentals of sliding mode control in an easy-to-understand manner.
What is Sliding Mode Control?
Sliding mode control is a control technique designed to drive the states of a dynamic system to a predefined sliding surface and maintain them there.
This method takes advantage of the system’s dynamics to improve performance, making it less sensitive to parameter variations and external disturbances.
The essential goal of sliding mode control is to ensure that the system’s state vectors conform to specific requirements, leading to stability and desired trajectories.
Basic Principles
At the core of sliding mode control is the concept of the sliding surface, a condition that the system’s trajectory should ideally follow.
When the trajectory hits this sliding surface, the sliding mode is activated, enabling the system to keep moving along the surface despite disturbances.
Achieving this involves designing a control law that switches between different functions to bring the system’s state to the sliding surface.
The sliding surface is typically defined by a function of the system states.
For a simple system, this might look like \(s(x) = 0\), where \(s(x)\) is a scalar function that evaluates the deviation from the desired surface.
Once the system trajectory hits and remains on this surface, the system is said to be in sliding mode.
Features of Sliding Mode Control
Sliding mode control offers several beneficial features:
1. **Robustness:** One of the key advantages is its robustness to system parameter variations and external disturbances.
This makes it highly suited for systems operating in unpredictable environments.
2. **Finite-Time Convergence:** The approach provides finite-time convergence of system states to the desired equilibrium, making it efficient in reaching the targeted performance.
3. **Simplicity:** The implementation of sliding mode control is straightforward, often requiring only a limited set of system parameters to design the controller.
Applications of Sliding Mode Control
Sliding mode control is applied across various industries and domains due to its versatility and reliability:
– **Automotive Industry:** Used in vehicle suspension systems and engine control to enhance performance and safety.
– **Robotics:** Helps in trajectory tracking and manipulation tasks where precision and adaptability are crucial.
– **Aerospace:** Applied in flight control systems for aircraft and unmanned aerial vehicles to maintain stability and control in varying conditions.
– **Electrical Systems:** Widely used in power electronics for controlling converters, inverters, and motor drives.
Designing a Sliding Mode Controller
To design a sliding mode controller, one must follow a series of steps to ensure it fits the system’s requirements:
1. **Define the Sliding Surface:** The first step is to determine a suitable sliding surface that aligns with the desired system behavior.
This surface should bring the system to a desired state and maintain it there.
2. **Develop a Control Law:** The control law is responsible for driving the system toward the sliding surface.
This can be a discontinuous or switching function, often involving high-frequency switching to counteract disturbances.
3. **Analysis of Stability:** Assessing the stability of the closed-loop system is critical.
Lyapunov’s stability theory is commonly used to confirm that the system will converge to the sliding surface and remain stable.
4. **Implementation and Testing:** Once the controller is designed, it should be implemented and tested within the actual system to ensure it meets performance criteria under all expected operating conditions.
Challenges and Considerations
While sliding mode control is effective, it is not without challenges.
One such challenge is the phenomenon known as “chattering.”
Chattering occurs due to high-frequency switching of the control input, which can lead to wear and inefficiencies in mechanical systems.
This issue can be mitigated by employing techniques such as boundary layer approaches or adaptive control laws that smooth out the switching action.
Another consideration is the design of the sliding surface.
Choosing the right sliding surface is critical, as it directly impacts the system’s performance and stability.
It requires careful selection and tuning based on the specific dynamics and requirements of the system.
Conclusion
Sliding mode control is a robust and efficient control strategy suitable for managing the complexities of modern dynamic systems.
Its ability to handle uncertainties and disturbances makes it a valuable tool across various engineering disciplines.
By understanding and applying the fundamentals of sliding mode control, engineers can design systems that operate reliably and effectively, even in challenging environments.
As technology continues to advance, the applications and methods of sliding mode control will further evolve, offering even greater precision and adaptability in the future.
資料ダウンロード
QCD管理受発注クラウド「newji」は、受発注部門で必要なQCD管理全てを備えた、現場特化型兼クラウド型の今世紀最高の受発注管理システムとなります。
ユーザー登録
受発注業務の効率化だけでなく、システムを導入することで、コスト削減や製品・資材のステータス可視化のほか、属人化していた受発注情報の共有化による内部不正防止や統制にも役立ちます。
NEWJI DX
製造業に特化したデジタルトランスフォーメーション(DX)の実現を目指す請負開発型のコンサルティングサービスです。AI、iPaaS、および先端の技術を駆使して、製造プロセスの効率化、業務効率化、チームワーク強化、コスト削減、品質向上を実現します。このサービスは、製造業の課題を深く理解し、それに対する最適なデジタルソリューションを提供することで、企業が持続的な成長とイノベーションを達成できるようサポートします。
製造業ニュース解説
製造業、主に購買・調達部門にお勤めの方々に向けた情報を配信しております。
新任の方やベテランの方、管理職を対象とした幅広いコンテンツをご用意しております。
お問い合わせ
コストダウンが利益に直結する術だと理解していても、なかなか前に進めることができない状況。そんな時は、newjiのコストダウン自動化機能で大きく利益貢献しよう!
(β版非公開)