- お役立ち記事
- Fundamentals of sliding mode control and examples of its application to controller design
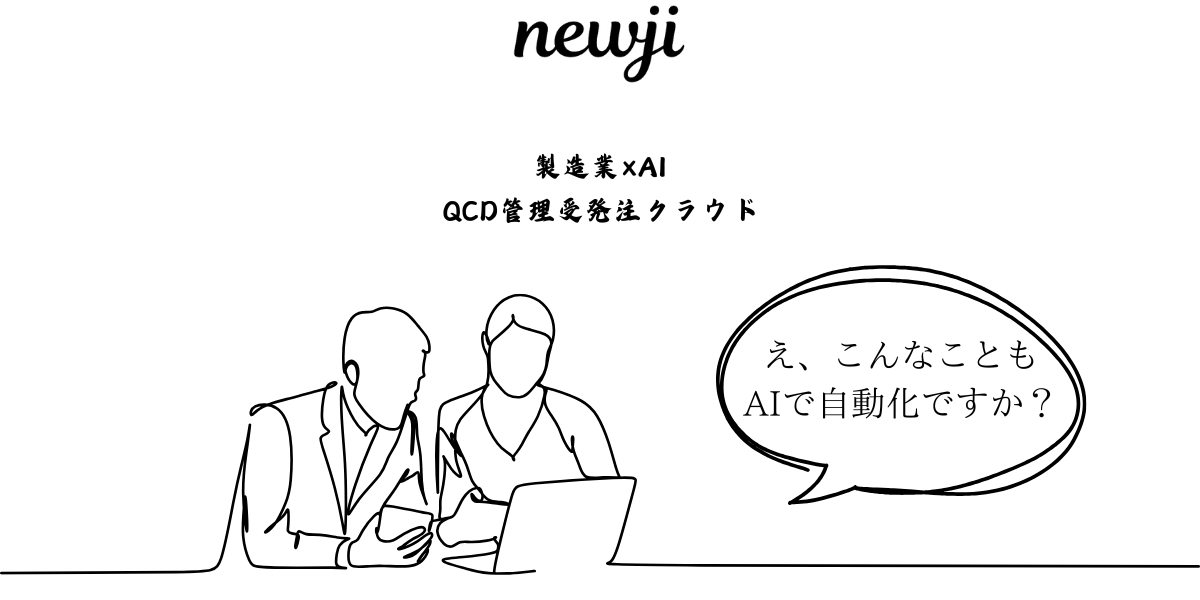
Fundamentals of sliding mode control and examples of its application to controller design
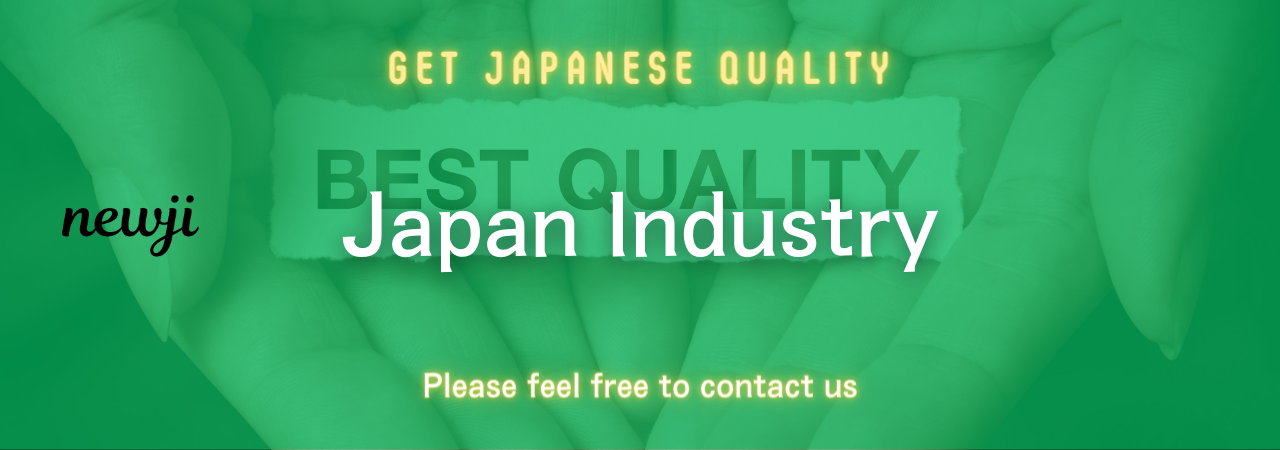
目次
Understanding Sliding Mode Control
Sliding mode control is a popular control strategy used in a variety of engineering applications due to its robustness and simplicity in design.
This method offers an effective solution for controlling systems with uncertainties or disturbances.
In essence, sliding mode control is a nonlinear control method that alters the dynamics of a system by applying a discontinuous control signal.
This allows for high precision and performance, making it suitable for demanding applications.
Concept of Sliding Mode Control
The main idea behind sliding mode control is to transform the system dynamics into a desired behavior by driving the system states onto a predefined surface in the state space, known as the “sliding surface.”
Once on this surface, the system will “slide” towards the desired equilibrium point.
The control law is designed to ensure that the trajectory of the system reaches and stays on this sliding surface.
The sliding surface is defined such that when the system states lie on it, they exhibit the desired dynamic behavior.
This is achieved by altering the control input based on a discontinuous function, often involving the sign of the error between the current state and the sliding surface.
This results in a control law that reacts aggressively to deviations from the sliding surface, ensuring quick convergence and robustness to disturbances.
Principles of Sliding Mode Control
Design of the Sliding Surface
The first step in designing a sliding mode controller is to define a suitable sliding surface.
This surface is typically chosen based on the desired performance criteria.
A common choice is a linear combination of the system states, which, when zero, represents the desired behavior of the system.
For example, consider a simple system where you wish to control the velocity of a motor.
The sliding surface might be defined as the difference between the actual velocity and the desired velocity.
The goal of the controller would be to adjust the input such that this difference, and thus the sliding surface, is driven to zero.
Reaching Phase and Sliding Phase
The operation of a sliding mode controller can be divided into two phases: the reaching phase and the sliding phase.
1. **Reaching Phase**: Initially, the system’s trajectory may not be on the sliding surface.
During the reaching phase, the control law is designed to drive the system states towards the sliding surface as quickly as possible.
This phase is often characterized by high-frequency switching of the control signal, which can introduce chattering.
2. **Sliding Phase**: Once the system states reach the sliding surface, they are expected to remain on it.
The control law in this phase is designed to maintain the system on the sliding surface despite any disturbances or parameter variations.
This phase is where the sliding mode control exhibits its robustness qualities, as the system dynamics are invariant to certain types of uncertainties.
Chattering Phenomenon
One of the main challenges in sliding mode control is the issue of chattering, which refers to the high-frequency oscillations of the control signal.
Chattering can cause wear and tear in mechanical systems or lead to instability in electronic applications.
Various techniques have been developed to mitigate chattering, including boundary layer approaches and higher-order sliding mode control.
These methods aim to smooth the control action while maintaining the robustness and performance benefits of sliding mode control.
Applications of Sliding Mode Control in Controller Design
Sliding mode control is utilized in numerous applications across various fields, owing to its robustness and adaptability.
Below are some areas where this control strategy is effectively applied:
Automotive Systems
Sliding mode control has been successfully implemented in various automotive systems to enhance performance and safety.
For instance, it is used in anti-lock braking systems (ABS) to prevent wheel lockup during sudden braking.
The robustness of sliding mode control ensures that the system can adapt to different road conditions and maintain optimal braking performance.
Robotics
In robotics, sliding mode control is employed to ensure precise control of robot manipulators.
The ability to handle model uncertainties and external disturbances is particularly beneficial in robotic applications where the exact dynamics may not be fully known.
Sliding mode control helps maintain the accuracy and stability of robotic movements, even in the presence of payload changes or joint friction.
Power Systems
Sliding mode control is applied in power systems to manage the stability and efficiency of converters and inverters.
For example, in renewable energy systems, such as wind or solar power systems, sliding mode control helps in tracking the maximum power point despite variations in environmental conditions.
Its robustness to load changes and parameter uncertainties makes it an ideal choice for maintaining consistent power output.
Aerospace
In the aerospace sector, sliding mode control is used for flight control systems to enhance the stability and maneuverability of aircraft.
Given the highly dynamic nature of aerospace environments, the ability of sliding mode control to handle disturbances and uncertainties is highly advantageous.
It is applied in control systems for drones, satellites, and other aerospace vehicles to ensure reliable operation under varied conditions.
Conclusion
Sliding mode control is a powerful and versatile control strategy, characterized by its robustness and simplicity.
Its ability to handle system uncertainties and disturbances makes it suitable for a wide range of applications, from automotive systems to aerospace.
Despite challenges such as chattering, continuous advancements in control strategies are expanding the scope and effectiveness of sliding mode control.
By understanding the fundamentals of sliding mode control, engineers can design controllers that are both resilient and efficient, leading to improved performance across various technological domains.
資料ダウンロード
QCD調達購買管理クラウド「newji」は、調達購買部門で必要なQCD管理全てを備えた、現場特化型兼クラウド型の今世紀最高の購買管理システムとなります。
ユーザー登録
調達購買業務の効率化だけでなく、システムを導入することで、コスト削減や製品・資材のステータス可視化のほか、属人化していた購買情報の共有化による内部不正防止や統制にも役立ちます。
NEWJI DX
製造業に特化したデジタルトランスフォーメーション(DX)の実現を目指す請負開発型のコンサルティングサービスです。AI、iPaaS、および先端の技術を駆使して、製造プロセスの効率化、業務効率化、チームワーク強化、コスト削減、品質向上を実現します。このサービスは、製造業の課題を深く理解し、それに対する最適なデジタルソリューションを提供することで、企業が持続的な成長とイノベーションを達成できるようサポートします。
オンライン講座
製造業、主に購買・調達部門にお勤めの方々に向けた情報を配信しております。
新任の方やベテランの方、管理職を対象とした幅広いコンテンツをご用意しております。
お問い合わせ
コストダウンが利益に直結する術だと理解していても、なかなか前に進めることができない状況。そんな時は、newjiのコストダウン自動化機能で大きく利益貢献しよう!
(Β版非公開)