- お役立ち記事
- Fundamentals of sputtering, trouble prevention measures, and quality improvement/improvement measures
月間76,176名の
製造業ご担当者様が閲覧しています*
*2025年3月31日現在のGoogle Analyticsのデータより
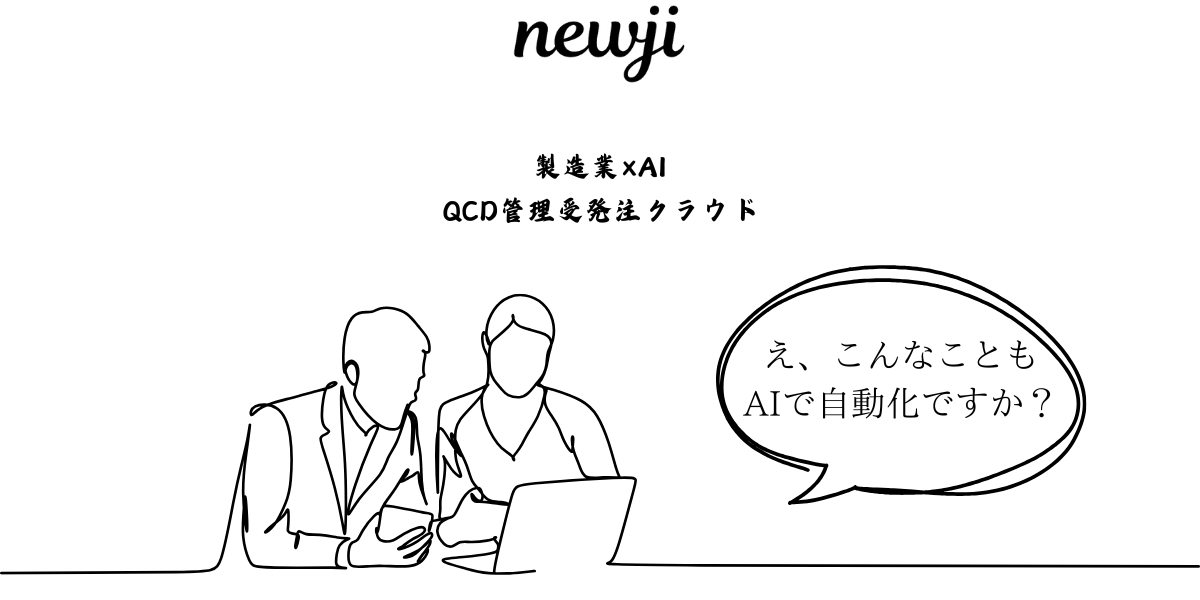
Fundamentals of sputtering, trouble prevention measures, and quality improvement/improvement measures
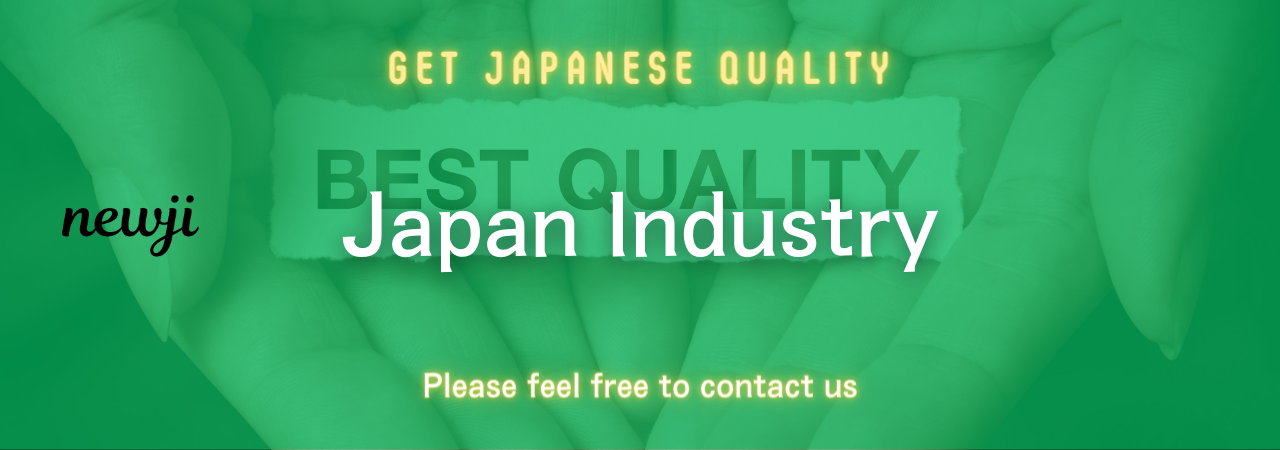
目次
What is Sputtering?
Sputtering is a widely used physical vapor deposition (PVD) process for creating thin films on various substrates.
In this technique, atoms are ejected from a solid target material due to bombardment by energetic particles, typically ions.
These ejected atoms then deposit onto a substrate, forming a thin film.
Sputtering is highly valued in industries due to its ability to deposit thin films with precise control over composition and thickness.
This process is commonly used in the production of semiconductors, solar cells, and optical coatings, among others.
The Basics of Sputtering
The sputtering process begins with creating a plasma in a vacuum chamber.
A target material, which will form the thin film, is placed within the chamber.
Energetic ions, often derived from inert gases like argon, bombard the target, causing atoms to be ejected.
These atoms then move through the vacuum and deposit onto the substrate.
The entire process takes place under low pressure to ensure that the ejected atoms have a clear path to the substrate, ensuring a uniform thin film.
Magnetron Sputtering
One popular variation of sputtering is magnetron sputtering.
This method utilizes a magnetic field to trap electrons close to the target surface.
With more electrons residing near the target, ionization becomes more efficient, increasing the number of ions available to bombard the material.
This efficiency makes magnetron sputtering a preferred choice in industrial applications, providing higher deposition rates and better film adhesion.
Trouble Prevention in Sputtering
While sputtering is an effective method for thin-film deposition, it is not without its challenges.
To prevent issues, several precautionary measures can be implemented.
Contamination Control
Contamination is a significant concern in sputtering processes.
Even small amounts of impurities can affect film quality.
Maintaining a clean vacuum environment is crucial, requiring regular maintenance and cleaning of the chamber.
Additionally, selecting high-purity target materials can minimize contamination risks.
Managing Film Uniformity
Achieving uniform film thickness across the substrate is often a challenging task.
To counteract this, rotating the substrate or target during deposition can help maintain uniform thickness.
Additionally, monitoring deposition parameters closely, such as pressure and power density, ensures consistent results.
Handling Substrate Heating
During sputtering, the substrate may receive direct thermal energy, potentially causing damage or compromising film adhesion.
To mitigate this, cooling systems can be installed to regulate substrate temperature.
Moreover, adjusting power settings can aid in controlling the substrate’s thermal load.
Quality Improvement in Sputtering
Enhancing the quality of sputtered films is crucial for their performance in specific applications.
Several techniques and approaches can be adopted to ensure improved film quality.
Optimizing Deposition Parameters
To improve film quality, one must optimize deposition parameters like ion energy, gas pressure, and target-to-substrate distance.
Experimentation and fine-tuning of these parameters can result in better film adhesion, reduced defects, and desired thickness.
Layered Films for Enhanced Properties
Employing multilayered thin films can result in improved film properties, such as increased hardness or enhanced thermal resistance.
By carefully controlling the composition of each layer, specific characteristics can be achieved.
Post-Deposition Treatments
Post-deposition treatments, like annealing or laser treatments, can enhance film properties by promoting crystallinity or reducing stress.
Such treatments can significantly improve the mechanical and electrical properties of the film.
Innovations in Sputtering Techniques
Sputtering continues to evolve with advancements in technology, providing more efficient and effective deposition methods.
Pulsed DC Sputtering
Pulsed DC sputtering is an innovative technique where a pulsed voltage is applied, rather than constant DC voltage.
This method reduces arcing and allows for better control over film quality, particularly beneficial for insulating or highly reactive materials.
High-Power Impulse Magnetron Sputtering (HiPIMS)
HiPIMS is a relatively new technology that utilizes very high power pulses for short durations.
This results in a high ionization degree of the sputtered material, improving film density and adhesion.
Conclusion
Sputtering remains a vital technique in the production of advanced materials and components across various industries.
By understanding its fundamentals, potential issues can be mitigated, and film quality can be enhanced.
As technology advances, innovative sputtering methods continue to emerge, paving the way for even more precise and efficient thin-film deposition.
Whether you are stepping into this field or seeking to refine your current processes, grasping these core aspects of sputtering will undoubtedly be beneficial.
資料ダウンロード
QCD管理受発注クラウド「newji」は、受発注部門で必要なQCD管理全てを備えた、現場特化型兼クラウド型の今世紀最高の受発注管理システムとなります。
ユーザー登録
受発注業務の効率化だけでなく、システムを導入することで、コスト削減や製品・資材のステータス可視化のほか、属人化していた受発注情報の共有化による内部不正防止や統制にも役立ちます。
NEWJI DX
製造業に特化したデジタルトランスフォーメーション(DX)の実現を目指す請負開発型のコンサルティングサービスです。AI、iPaaS、および先端の技術を駆使して、製造プロセスの効率化、業務効率化、チームワーク強化、コスト削減、品質向上を実現します。このサービスは、製造業の課題を深く理解し、それに対する最適なデジタルソリューションを提供することで、企業が持続的な成長とイノベーションを達成できるようサポートします。
製造業ニュース解説
製造業、主に購買・調達部門にお勤めの方々に向けた情報を配信しております。
新任の方やベテランの方、管理職を対象とした幅広いコンテンツをご用意しております。
お問い合わせ
コストダウンが利益に直結する術だと理解していても、なかなか前に進めることができない状況。そんな時は、newjiのコストダウン自動化機能で大きく利益貢献しよう!
(β版非公開)