- お役立ち記事
- Fundamentals of sputtering, trouble prevention measures, and quality improvement/improvement measures
月間77,185名の
製造業ご担当者様が閲覧しています*
*2025年2月28日現在のGoogle Analyticsのデータより
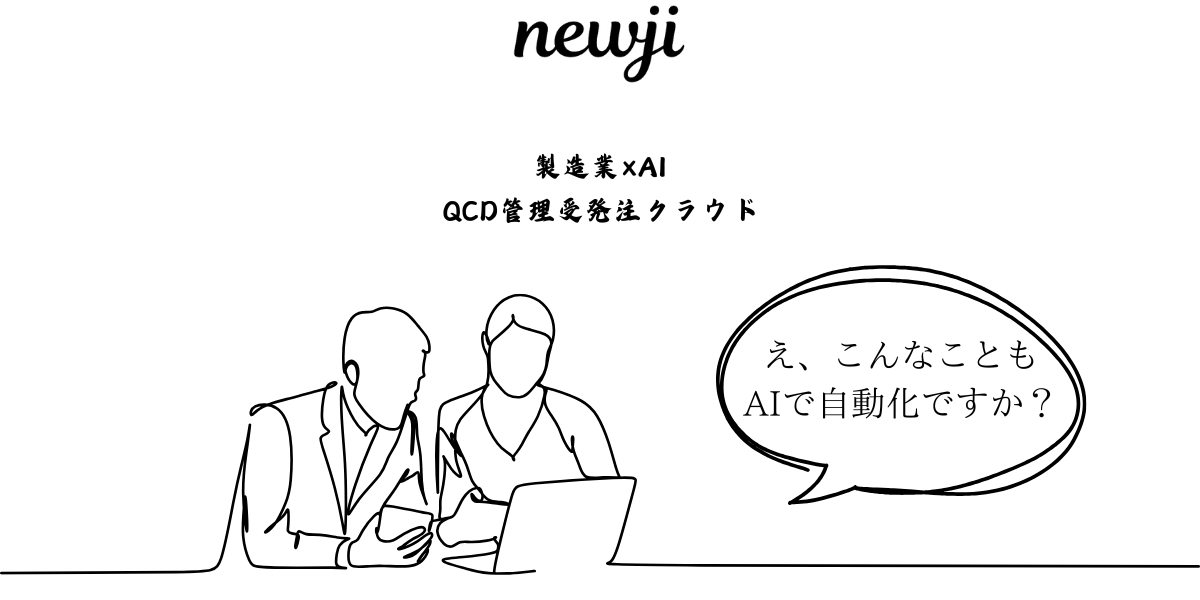
Fundamentals of sputtering, trouble prevention measures, and quality improvement/improvement measures
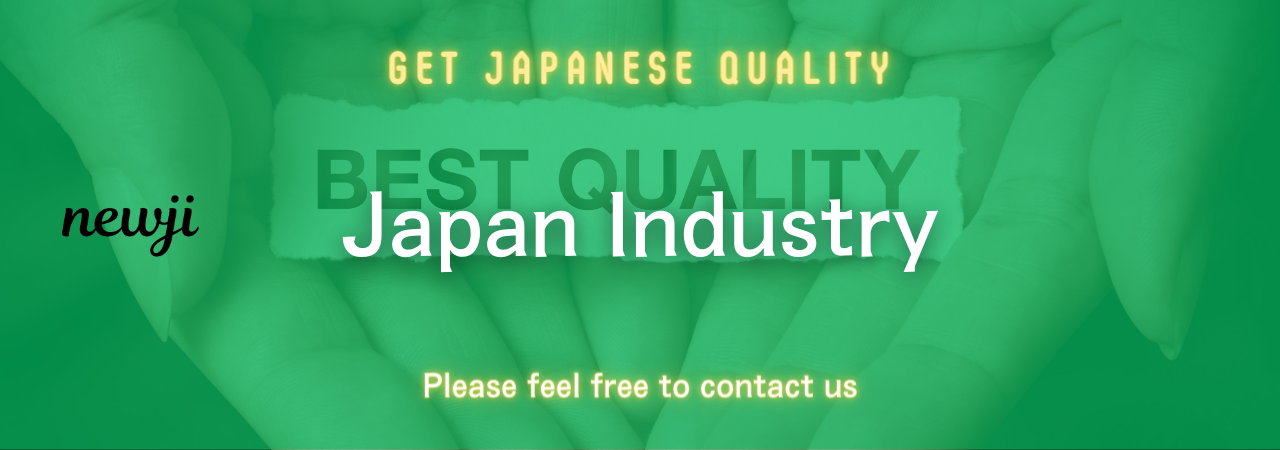
目次
Understanding the Basics of Sputtering
Sputtering is a widely used technique in the field of material science for depositing thin films onto various substrates.
This process plays a crucial role in the manufacturing of semiconductors, solar panels, and various types of coatings.
At its core, sputtering involves the ejection of atoms from a target material, which are then deposited onto a substrate surface.
The process takes place in a vacuum environment to enhance the quality and adherence of the coating.
The main components of a sputtering system include a vacuum chamber, target material, substrate holder, and power source.
How Sputtering Works
The sputtering process begins when a high-energy particle, often from an inert gas like argon, collides with the target material.
This collision causes atoms to be ejected from the target.
These ejected atoms travel through the vacuum and eventually settle on the substrate, forming a thin film layer.
The choice of target material is vital, as it determines the composition of the thin film.
Materials must be selected based on the desired properties of the final product, such as electrical conductivity, optical transparency, or wear resistance.
Optimizing Sputtering Parameters
Several parameters influence the quality and efficiency of the sputtering process.
One key factor is the pressure within the vacuum chamber.
Maintaining an optimal pressure level is essential to control the energy of the sputtering gas ions and the deposition rate of the atoms.
Another factor is the power applied to the target material.
Higher power levels increase the rate of sputtering, but can also lead to increased stress in the thin film.
Finding the right balance is crucial to avoid defects and ensure uniform coating.
Temperature is also important, as it affects the adhesion and structure of the thin film.
Each material has an optimal deposition temperature that promotes better bonding and minimizes stresses.
Choosing the Right Sputtering Technique
There are various sputtering techniques depending on the application needs, including DC sputtering, RF sputtering, and magnetron sputtering.
DC sputtering is simple and cost-effective, suitable for conductive materials.
RF sputtering is ideal for insulating materials, as it uses alternating current to maintain plasma stability.
Magnetron sputtering uses magnetic fields to trap electrons near the target material, enhancing the efficiency of the process and allowing for higher deposition rates.
Selecting the appropriate technique involves evaluating factors such as material type, desired film quality, and production speed.
Preventing Sputtering Issues
Even with optimal parameters, sputtering processes can encounter several issues that impact quality and consistency.
Knowing how to prevent these problems is crucial to maintaining efficient operations and high-quality output.
Contamination Control
One common issue in sputtering processes is contamination, where foreign particles mix with the target material, leading to impure films.
To prevent contamination, it is essential to clean all components thoroughly before starting the sputtering process.
Regular maintenance of the vacuum chamber and filtration systems is also necessary to remove any accumulated contaminants.
Arcing and Particle Accumulation
Arcing, a disruptive electrical discharge, can damage both the target and the substrate, affecting film quality.
Arcing can be minimized by using proper grounding techniques and ensuring clean surfaces to prevent electrical imbalances.
Particle accumulation on the substrate can lead to defects in the thin film.
Using shield plates and optimizing the deposition angles can help reduce this risk, as it prevents particles from directly striking the substrate.
Improving Sputtering Quality
For manufacturers and researchers, improving the quality of sputtered films is an ongoing goal.
Several strategies can be implemented to enhance the results achieved through sputtering processes.
Substrate Preparation and Selection
Proper substrate preparation can greatly enhance the adherence and uniformity of the thin film.
Cleaning the substrate’s surface and removing any oxidation or organic residues are critical first steps.
Choosing the right substrate material is also important.
Materials should be chosen based on compatibility with the target material, thermal expansion coefficients, and intended application of the film.
Advanced Process Control
Employing advanced process control methods, such as real-time monitoring systems, can significantly improve sputtering quality.
These systems provide feedback on critical parameters like film thickness, uniformity, and deposition rate.
With real-time data, operators can make necessary adjustments promptly, ensuring consistent output and minimizing defects.
Layer Structuring
Layer structuring is a method that involves depositing multiple layers with varied materials or properties to enhance film performance.
For instance, applying a protective layer over a conductive layer can improve the durability and functionality of the thin film.
By strategically designing multilayer structures, manufacturers can meet specific application requirements and improve the overall quality of the sputtered film.
Conclusion
Sputtering is a versatile and essential technique in creating thin films for a multitude of applications.
Understanding its fundamentals, knowing how to prevent issues, and employing quality improvement strategies are critical for achieving optimal results.
By controlling sputtering parameters, preventing contamination, and leveraging advanced techniques, manufacturers can produce high-performance films that meet current and future demands.
With continuing advancements in sputtering technology, the possibilities for innovation and quality enhancement are virtually limitless.
資料ダウンロード
QCD管理受発注クラウド「newji」は、受発注部門で必要なQCD管理全てを備えた、現場特化型兼クラウド型の今世紀最高の受発注管理システムとなります。
ユーザー登録
受発注業務の効率化だけでなく、システムを導入することで、コスト削減や製品・資材のステータス可視化のほか、属人化していた受発注情報の共有化による内部不正防止や統制にも役立ちます。
NEWJI DX
製造業に特化したデジタルトランスフォーメーション(DX)の実現を目指す請負開発型のコンサルティングサービスです。AI、iPaaS、および先端の技術を駆使して、製造プロセスの効率化、業務効率化、チームワーク強化、コスト削減、品質向上を実現します。このサービスは、製造業の課題を深く理解し、それに対する最適なデジタルソリューションを提供することで、企業が持続的な成長とイノベーションを達成できるようサポートします。
製造業ニュース解説
製造業、主に購買・調達部門にお勤めの方々に向けた情報を配信しております。
新任の方やベテランの方、管理職を対象とした幅広いコンテンツをご用意しております。
お問い合わせ
コストダウンが利益に直結する術だと理解していても、なかなか前に進めることができない状況。そんな時は、newjiのコストダウン自動化機能で大きく利益貢献しよう!
(β版非公開)