- お役立ち記事
- Fundamentals of statistical reliability analysis
月間76,176名の
製造業ご担当者様が閲覧しています*
*2025年3月31日現在のGoogle Analyticsのデータより
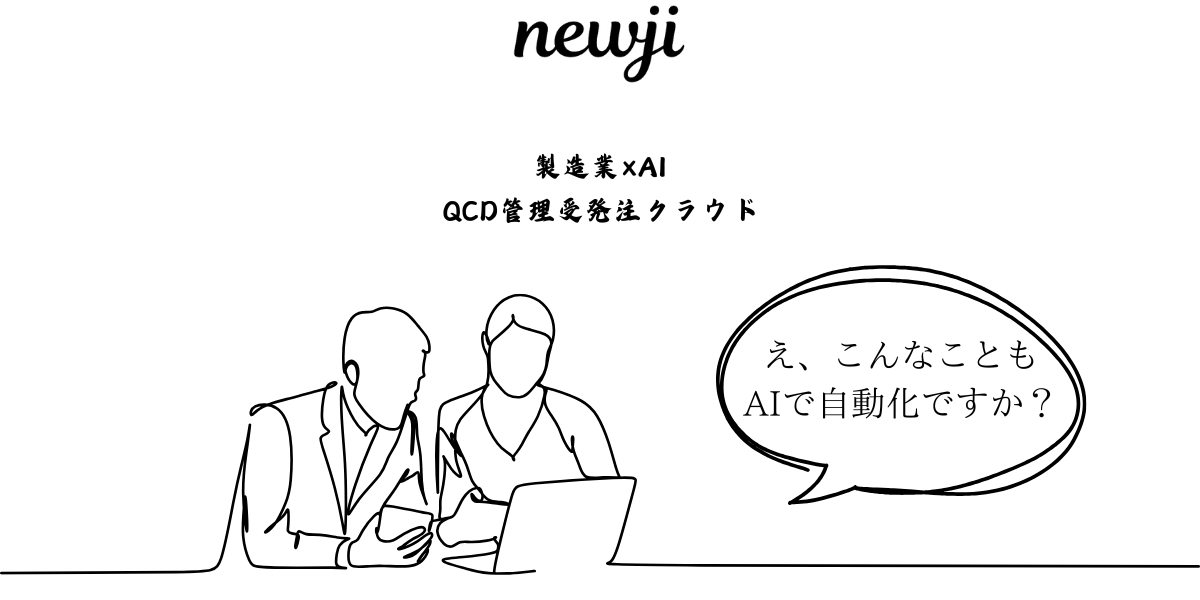
Fundamentals of statistical reliability analysis
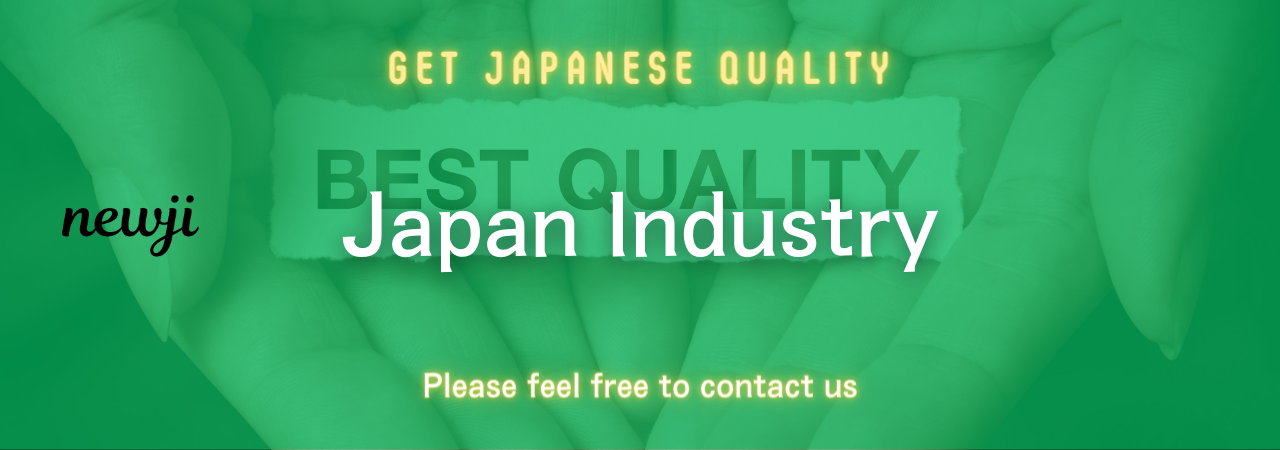
Understanding Statistical Reliability Analysis
Reliability analysis is a significant aspect of statistics, especially in fields where safety and performance are crucial, such as engineering, manufacturing, and quality control.
By understanding the fundamentals of statistical reliability analysis, you gain insights into how likely a system or component will perform its intended function under specific conditions for a specified period.
In this article, we will dive deep into what statistical reliability analysis is, why it is essential, and the basic concepts and methods used in the analysis process.
What is Statistical Reliability Analysis?
Statistical reliability analysis is the study of the probability that a system or component will not fail over a specified period under defined conditions.
It aims to determine the lifespan and predict potential failures, thereby ensuring that performance standards are met.
The analysis uses statistical methods to assess the life distribution, reliability functions, and failure rates of products and systems.
Reliability analysis helps to make informed decisions about product design, maintenance schedules, and risk management strategies.
It is an effective way to understand failure mechanisms and improve safety and efficiency.
Why is Reliability Analysis Important?
Reliability analysis plays a critical role in many industries for several reasons:
1. **Product Safety and Performance:** Reliable products ensure safety, which is especially important in industries like aviation, healthcare, automotive, and consumer electronics.
2. **Cost Efficiency:** By predicting failures and implementing effective maintenance strategies, companies can minimize costly downtimes and repairs, maximizing profitability.
3. **Customer Satisfaction:** High reliability improves customer satisfaction and loyalty, as products are more likely to meet user expectations.
4. **Competitive Advantage:** Companies that consistently deliver reliable products and services gain a competitive edge in the marketplace.
Key Concepts in Reliability Analysis
To fully grasp reliability analysis, it’s essential to understand its key concepts:
Reliability Function (R(t))
The reliability function R(t) represents the probability that a system or component will not fail by time t.
It is a fundamental concept used to determine the performance over time.
Reliability functions typically follow specific statistical distributions, such as the exponential, Weibull, or log-normal distributions.
Failure Rate (λ)
The failure rate, often represented by the Greek letter λ (lambda), is the frequency with which failures occur in a system or component.
It’s essential to differentiate between constant failure rate, often observed in electronic components, and time-dependent failure rates, often seen in mechanical products.
The failure rate can provide insight into the expected lifespan of a product.
Mean Time to Failure (MTTF)
MTTF is the average time expected until the first failure of a system or component occurs.
It is widely used for non-repairable systems.
In contrast, Mean Time Between Failures (MTBF) is used for repairable systems to estimate the expected time between two consecutive failures.
Weibull Analysis
Weibull analysis is a robust method in reliability engineering that helps in understanding the life data of products.
Named after Waloddi Weibull, this analysis can model diverse types of failure data.
The Weibull distribution provides a flexible approach to modeling data by adjusting its scale (β) and shape (η) parameters.
The scale parameter can show time, whereas the shape indicates the pattern of failure rates, i.e., constant, decreasing, or increasing.
Statistical Methods Used in Reliability Analysis
Reliability analysis employs various statistical techniques for data analysis:
Life Data Analysis
Also known as Weibull analysis, life data analysis involves collecting and analyzing data on the time it takes for a product to fail.
This data helps estimate the life distribution and reliability of the product.
Accelerated Life Testing (ALT)
Accelerated life testing simulates the life span of a product in a shorter period by exposing it to extreme stress conditions.
This method provides information on potential failures and their frequencies, allowing manufacturers to improve product durability.
Reliability Testing
Reliability testing assesses the reliability performance of a product under specified conditions.
Methods include environmental tests, stress tests, and endurance trials.
These tests help identify any design or manufacturing flaws that need correction before mass production.
Failure Modes and Effects Analysis (FMEA)
FMEA is a systematic approach for identifying potential failure modes and their causes.
It assesses the impact of each failure on the overall system and prioritizes them based on severity, occurrence, and detection, allowing for preventive actions.
Applications of Reliability Analysis
Reliability analysis finds its applications in various sectors:
1. **Aerospace:** Ensures aircraft safety by analyzing component reliability and predicting maintenance needs.
2. **Automotive:** Improves vehicle safety and performance while reducing warranty claims through better design and manufacturing.
3. **Electronics:** Assists in identifying failure points and extending the life of components like semiconductors and circuit boards.
4. **Healthcare:** Ensures the reliability of medical devices and equipment, safeguarding patient health.
5. **Manufacturing:** Optimizes production processes by predicting equipment failures and scheduling maintenance.
Conclusion
Understanding the fundamentals of statistical reliability analysis is crucial for anyone involved in designing, manufacturing, or maintaining products and systems.
By leveraging statistical methods to predict and mitigate failures, reliability analysis ensures product safety, efficiency, and customer satisfaction.
As industries continue to prioritize reliability, mastery of these concepts can significantly contribute to success and innovation.
資料ダウンロード
QCD管理受発注クラウド「newji」は、受発注部門で必要なQCD管理全てを備えた、現場特化型兼クラウド型の今世紀最高の受発注管理システムとなります。
ユーザー登録
受発注業務の効率化だけでなく、システムを導入することで、コスト削減や製品・資材のステータス可視化のほか、属人化していた受発注情報の共有化による内部不正防止や統制にも役立ちます。
NEWJI DX
製造業に特化したデジタルトランスフォーメーション(DX)の実現を目指す請負開発型のコンサルティングサービスです。AI、iPaaS、および先端の技術を駆使して、製造プロセスの効率化、業務効率化、チームワーク強化、コスト削減、品質向上を実現します。このサービスは、製造業の課題を深く理解し、それに対する最適なデジタルソリューションを提供することで、企業が持続的な成長とイノベーションを達成できるようサポートします。
製造業ニュース解説
製造業、主に購買・調達部門にお勤めの方々に向けた情報を配信しております。
新任の方やベテランの方、管理職を対象とした幅広いコンテンツをご用意しております。
お問い合わせ
コストダウンが利益に直結する術だと理解していても、なかなか前に進めることができない状況。そんな時は、newjiのコストダウン自動化機能で大きく利益貢献しよう!
(β版非公開)