- お役立ち記事
- Fundamentals of stirring technology and key points for scale-up and optimal selection and evaluation of stirrers
月間76,176名の
製造業ご担当者様が閲覧しています*
*2025年3月31日現在のGoogle Analyticsのデータより
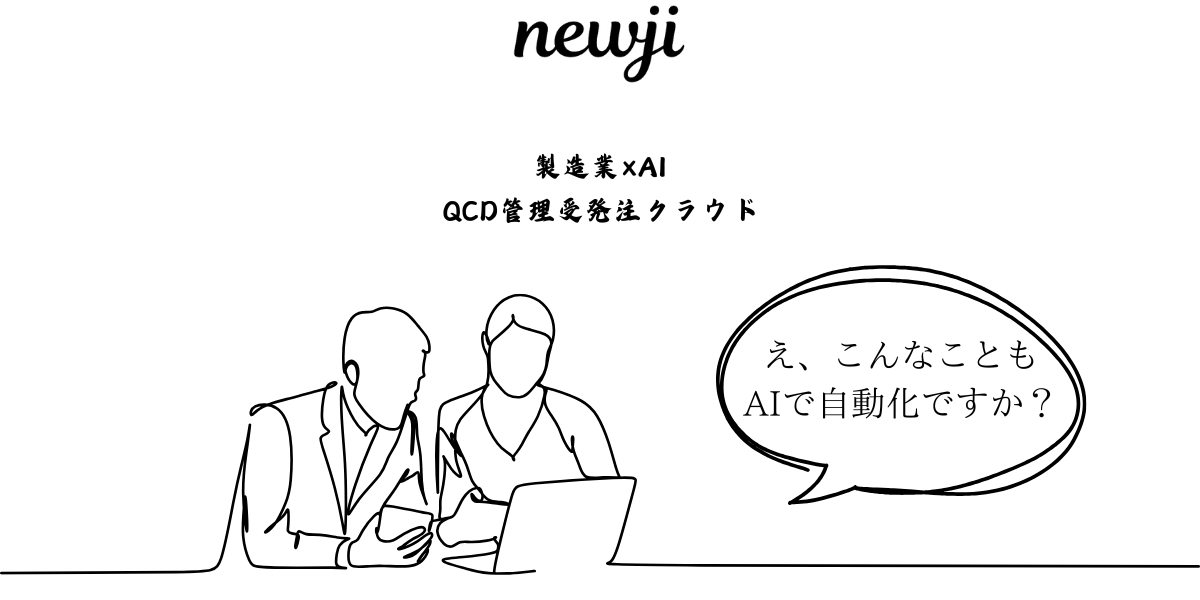
Fundamentals of stirring technology and key points for scale-up and optimal selection and evaluation of stirrers
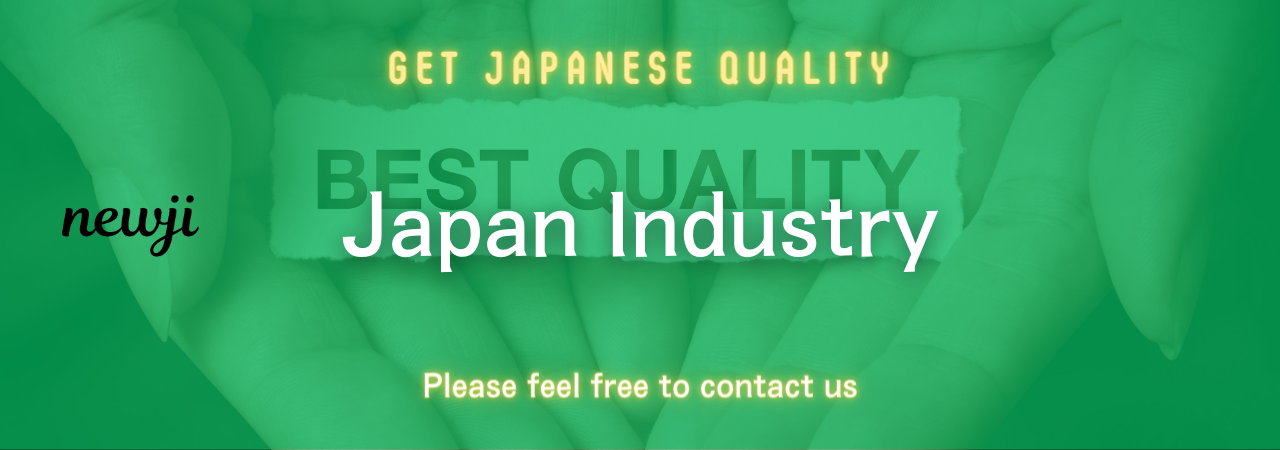
目次
Understanding Stirring Technology
Stirring technology plays a vital role in various industrial processes, including chemical manufacturing, pharmaceuticals, food production, and more.
At its core, stirring involves the movement of liquid or solid particles, resulting in homogenization, heat transfer, or chemical reactions.
Understanding the fundamentals of stirring technology is crucial for optimizing these processes and achieving the desired outcomes.
Stirrers come in various designs and operate under different principles.
The selection of an appropriate stirrer depends on factors such as the type of material being processed, the desired mixing outcome, and the scale of operation.
Common types of stirring equipment include impellers, agitators, and blenders, each suited for specific mixing tasks.
Key Components of Stirring Equipment
When selecting a stirrer, it is essential to consider its key components and how they influence performance.
One important component is the impeller, which is responsible for generating flow within the mixture.
Impellers vary in size, shape, and design, impacting their effectiveness in different applications.
Another critical aspect is the power source or motor, which drives the stirrer.
The motor must be capable of providing sufficient power to achieve the desired mixing effect without causing excessive wear or damage to the equipment.
Finally, the vessel or container in which stirring takes place is also significant.
The shape and size of the vessel can influence the efficiency of the stirring process.
Specialized vessels with features like baffles or sloping bottoms can enhance mixing performance.
Scale-Up Considerations
Scaling up stirring processes from laboratory or pilot plant settings to full-scale industrial operations presents several challenges.
The key is to maintain the same mixing efficiency and product quality as the process is scaled up.
One critical factor in scale-up is the geometric similarity between the small-scale and large-scale systems.
This involves maintaining consistent ratios of dimensions, such as impeller diameter to vessel diameter, across scales.
Geometric similarity ensures that the flow patterns and mixing dynamics remain consistent.
Additionally, maintaining dynamic similarity is essential.
This means that the forces acting on the mixture at different scales should be proportional.
Dynamic similarity can be achieved by adjusting stirring speed and other parameters to match the flow characteristics observed at a smaller scale.
Optimal Selection of Stirrers
Choosing the right stirrer for a specific application requires careful evaluation of several factors.
First, consider the properties of the material being mixed, such as viscosity, density, and particle size.
Different stirrers are designed to handle various material properties effectively.
Next, determine the desired mixing outcome.
For example, some processes may require gentle mixing to avoid damaging delicate components, while others may require vigorous agitation to achieve thorough blending.
Selecting a stirrer that aligns with the desired outcome ensures optimal performance.
The scale of operation is another key consideration.
For large-scale processes, industrial-grade stirrers with robust motors and durable materials are necessary to handle the increased load and continuous operation.
Finally, evaluate the overall cost of ownership, including initial purchase price, maintenance requirements, and energy consumption.
This comprehensive evaluation helps in selecting a stirrer that offers the best value for the specific application.
Evaluation of Stirrer Performance
Assessing the performance of a stirrer involves measuring parameters such as mixing time, power consumption, and product uniformity.
Mixing time refers to the duration required to achieve a homogeneous mix, which directly impacts productivity and efficiency.
Power consumption is an important consideration, as energy-efficient stirring equipment can significantly reduce operational costs.
Monitoring power usage helps identify opportunities for optimization and savings.
Product uniformity is a critical quality metric, especially in industries like pharmaceuticals, where consistent product quality is essential.
Techniques such as sampling and analysis can be used to evaluate uniformity and ensure that the desired level of mixing has been achieved.
Innovations in Stirring Technology
Advancements in stirring technology continue to enhance mixing efficiency and expand the range of applications.
One significant development is the integration of digital monitoring and control systems, which allow for real-time adjustments and optimization of stirring processes.
These smart systems can adapt to changing conditions and improve overall process performance.
Another innovation is the use of computational fluid dynamics (CFD) simulations to model and analyze stirring processes.
CFD provides insights into flow patterns and mixing dynamics, aiding in the design and optimization of stirring equipment.
Sustainable mixing solutions are also gaining attention, with a focus on reducing energy consumption and minimizing environmental impact.
Stirrers that are designed for lower energy usage and made from eco-friendly materials align with the growing emphasis on sustainability.
Conclusion
Stirring technology is a fundamental aspect of many industrial processes, and understanding its principles is crucial for achieving desired results.
By considering factors such as material properties, desired outcomes, and scale, businesses can select the appropriate stirrers and optimize their operations.
Continuous evaluation and innovation in stirring technology contribute to improved performance, energy efficiency, and sustainability.
As technology advances, industries can expect further enhancements in stirring capabilities, ultimately leading to more efficient and effective processes.
資料ダウンロード
QCD管理受発注クラウド「newji」は、受発注部門で必要なQCD管理全てを備えた、現場特化型兼クラウド型の今世紀最高の受発注管理システムとなります。
ユーザー登録
受発注業務の効率化だけでなく、システムを導入することで、コスト削減や製品・資材のステータス可視化のほか、属人化していた受発注情報の共有化による内部不正防止や統制にも役立ちます。
NEWJI DX
製造業に特化したデジタルトランスフォーメーション(DX)の実現を目指す請負開発型のコンサルティングサービスです。AI、iPaaS、および先端の技術を駆使して、製造プロセスの効率化、業務効率化、チームワーク強化、コスト削減、品質向上を実現します。このサービスは、製造業の課題を深く理解し、それに対する最適なデジタルソリューションを提供することで、企業が持続的な成長とイノベーションを達成できるようサポートします。
製造業ニュース解説
製造業、主に購買・調達部門にお勤めの方々に向けた情報を配信しております。
新任の方やベテランの方、管理職を対象とした幅広いコンテンツをご用意しております。
お問い合わせ
コストダウンが利益に直結する術だと理解していても、なかなか前に進めることができない状況。そんな時は、newjiのコストダウン自動化機能で大きく利益貢献しよう!
(β版非公開)