- お役立ち記事
- Fundamentals of stirring technology, methods for measuring and evaluating stirring performance, and key points for scaling up
月間76,176名の
製造業ご担当者様が閲覧しています*
*2025年3月31日現在のGoogle Analyticsのデータより
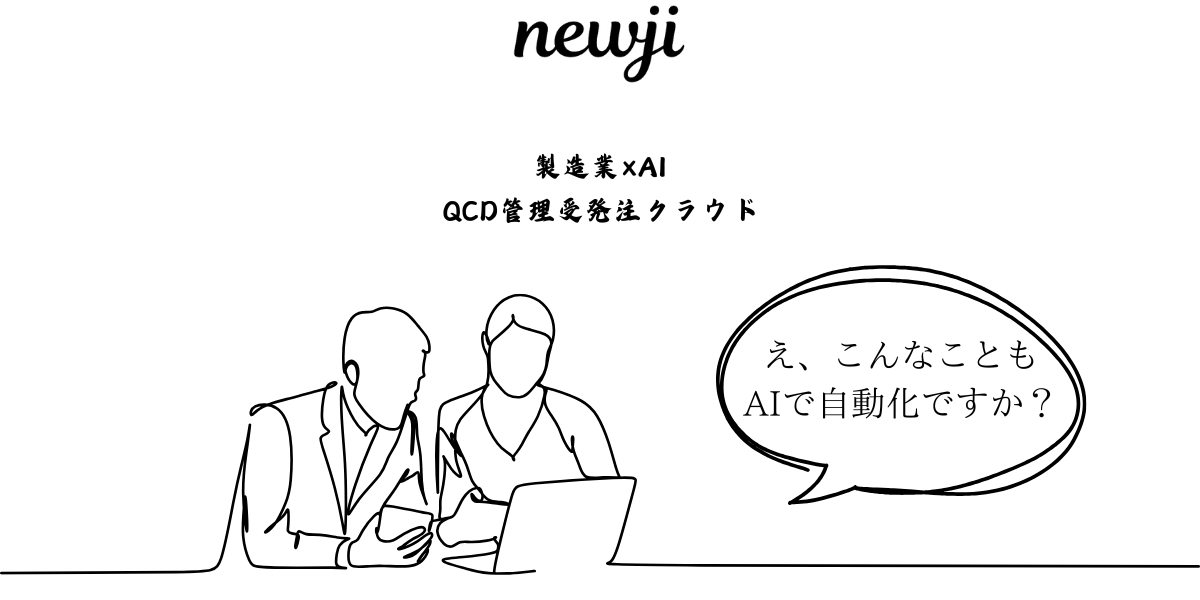
Fundamentals of stirring technology, methods for measuring and evaluating stirring performance, and key points for scaling up
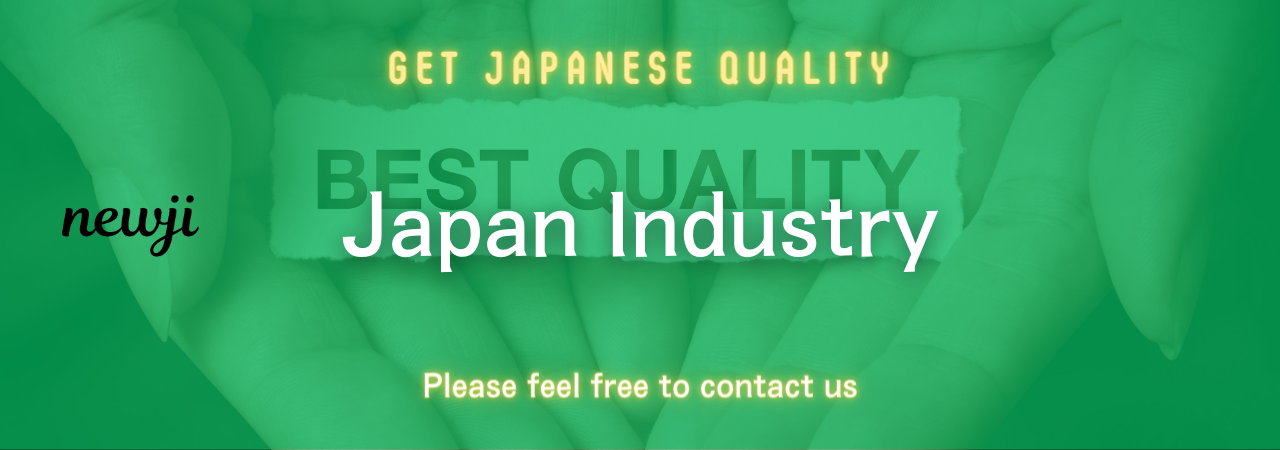
目次
Understanding the Basics of Stirring Technology
Stirring technology plays a crucial role in various industrial and laboratory processes, ensuring the homogeneity of mixtures, promoting chemical reactions, and influencing the quality of the final product.
Grasping the fundamentals of stirring technology involves understanding the types of systems and equipment used, the mechanics of mixing, and the factors affecting performance.
There are several types of stirrers and mixers designed for different applications, including magnetic stirrers, overhead stirrers, and industrial mixers.
Magnetic stirrers are commonly used for small-scale applications in laboratories, while overhead stirrers are suitable for medium-sized volumes and viscous materials.
Industrial mixers, such as paddle agitators and turbine mixers, are often employed in large-scale industrial processes to handle hefty mixing loads.
Methods for Measuring Stirring Performance
Evaluating stirring performance is vital to ensure the efficiency and effectiveness of the mixing process.
Various methods can be used to measure stirring performance, focusing on parameters like mixing time, power consumption, and homogeneity.
Mixing Time
Mixing time is the duration required to achieve a uniform mixture after the onset of stirring.
It is a critical factor in determining the efficiency of a stirring system.
Shorter mixing times generally indicate more efficient stirring.
Mixing time can be measured by introducing a tracer material, such as a dye or a salt, into the mixture and recording how long it takes to reach a uniform concentration throughout the vessel.
Power Consumption
Power consumption is another crucial parameter that affects the operational costs of stirring processes.
Measuring power consumption involves monitoring the energy used by the stirring equipment.
This can be achieved using a power meter attached to the mixer motor.
By optimizing the stirring speed and system configurations, power consumption can be minimized, leading to more energy-efficient operations.
Homogeneity
Homogeneity refers to the uniform distribution of components within a mixture and is a key indicator of successful stirring.
Various analytical techniques can be employed to assess homogeneity, such as sampling and analyzing the mixture at different points, employing spectroscopic methods, or using automated image analysis systems.
Achieving the desired level of homogeneity ensures that the final product meets quality standards and performs as expected.
Key Points for Scaling Up Stirring Processes
Scaling up stirring processes from laboratory or pilot scale to full industrial scale presents unique challenges.
Several key factors must be considered to ensure a successful scale-up.
Geometric Similarity
Geometric similarity involves maintaining the same proportions of the stirring system components, such as the height-to-diameter ratio of the vessel and the shape and size of the impellers.
This practice helps preserve the flow patterns and mixing characteristics observed at the smaller scale.
Failure to maintain geometric similarity can lead to inefficient mixing and longer processing times at the industrial scale.
Dynamic Similarity
Dynamic similarity refers to the replication of the flow conditions within the mixer from the smaller to the larger scale.
This involves matching dimensionless numbers such as the Reynolds number, which characterizes the flow regime, and the Froude number, which relates to the surface dynamics of the fluid.
Maintaining dynamic similarity ensures that the forces and effects experienced during mixing are consistent across different scales.
Power and Energy Considerations
As the scale of a stirring process increases, the power and energy requirements typically grow.
It’s essential to ensure that the larger system can deliver the necessary power to achieve effective mixing.
This may involve redesigning or selecting new equipment capable of handling the increased demands.
Additionally, optimizing the mixing protocol to reduce energy consumption without compromising performance is crucial for cost-effective scale-up.
Material Properties
The physical properties of the materials being mixed, such as viscosity and density, can significantly influence the stirring process at different scales.
Understanding how these properties change with scale is essential for selecting the appropriate equipment and operating conditions.
Scale-up may require adjustments in the type or configuration of impellers and the selection of materials that can withstand higher environmental stresses.
Conclusion
Mastering the fundamentals of stirring technology and evaluating performance through various metrics is essential for successful industrial mixing applications.
The process of scaling up stirring systems requires careful consideration of geometric and dynamic similarities, power requirements, and material properties.
By addressing these key points, industries can optimize their stirring processes to ensure product quality and operational efficiency at any scale.
資料ダウンロード
QCD管理受発注クラウド「newji」は、受発注部門で必要なQCD管理全てを備えた、現場特化型兼クラウド型の今世紀最高の受発注管理システムとなります。
ユーザー登録
受発注業務の効率化だけでなく、システムを導入することで、コスト削減や製品・資材のステータス可視化のほか、属人化していた受発注情報の共有化による内部不正防止や統制にも役立ちます。
NEWJI DX
製造業に特化したデジタルトランスフォーメーション(DX)の実現を目指す請負開発型のコンサルティングサービスです。AI、iPaaS、および先端の技術を駆使して、製造プロセスの効率化、業務効率化、チームワーク強化、コスト削減、品質向上を実現します。このサービスは、製造業の課題を深く理解し、それに対する最適なデジタルソリューションを提供することで、企業が持続的な成長とイノベーションを達成できるようサポートします。
製造業ニュース解説
製造業、主に購買・調達部門にお勤めの方々に向けた情報を配信しております。
新任の方やベテランの方、管理職を対象とした幅広いコンテンツをご用意しております。
お問い合わせ
コストダウンが利益に直結する術だと理解していても、なかなか前に進めることができない状況。そんな時は、newjiのコストダウン自動化機能で大きく利益貢献しよう!
(β版非公開)