- お役立ち記事
- Fundamentals of strength design, damage and deterioration measures, and key points for pressure vessels and pressure equipment
Fundamentals of strength design, damage and deterioration measures, and key points for pressure vessels and pressure equipment
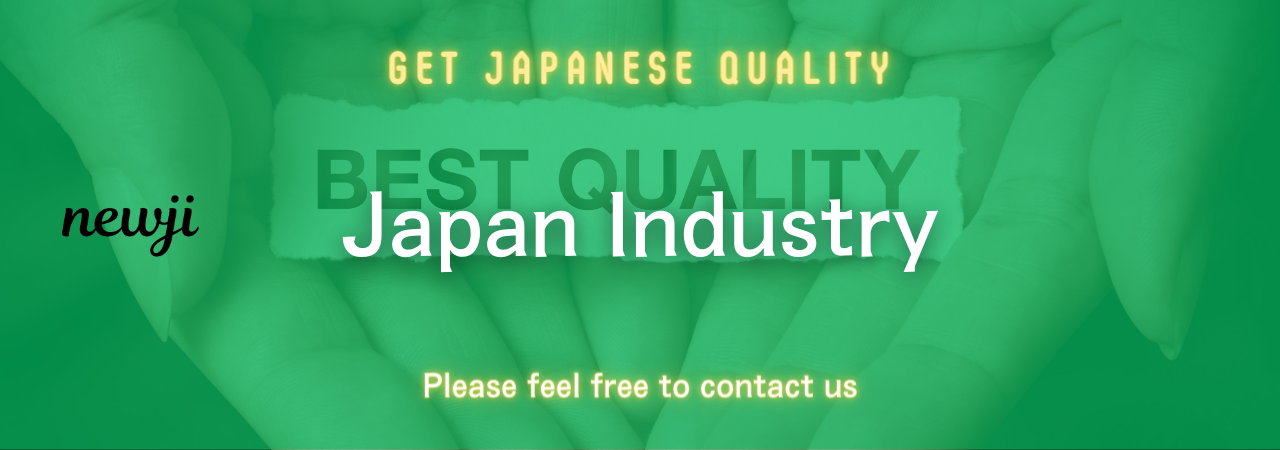
目次
Understanding the Basics of Strength Design
Strength design forms the backbone of engineering, especially when it comes to pressure vessels and equipment.
Engineers must ensure that these vessels can withstand high pressure without compromising functionality or safety.
The concept of strength design revolves around assessing how materials and structures behave under stress.
It involves calculating the maximum load-bearing capacity of materials and ensuring they perform optimally in various conditions.
When designing pressure equipment, engineers often rely on several key principles.
These include analyzing the forces acting upon the equipment, assessing the properties of the materials used, and applying safety factors to prevent failure.
Importance of Material Choice
Selecting the right materials is crucial in strength design.
Materials need to possess the necessary mechanical properties to handle the pressure and temperature conditions they will face.
Common materials used in pressure vessels include steel, aluminum, and composite materials.
Each material has unique properties such as tensile strength, ductility, and corrosion resistance that make them suitable for different applications.
The choice of material impacts not only the strength but also the long-term durability of the pressure vessel.
Materials must be chosen based on how well they resist damage and deterioration over time.
Damage and Deterioration in Pressure Equipment
Damage and deterioration are inevitable challenges faced by pressure vessels and equipment.
Various factors contribute to these issues, including environmental conditions, operating pressure, temperature fluctuations, and chemical exposure.
Understanding the potential causes of damage is fundamental in mitigating these risks and extending the lifespan of pressure equipment.
Types of Damage
Several types of damage can affect pressure vessels and equipment.
These include mechanical damage, such as cracking, fatigue, and deformation; chemical damage, such as corrosion and erosion; and thermal damage caused by temperature variations.
Mechanical damage often occurs due to excessive stress or pressure beyond the designed limits.
Fatigue is a common type of mechanical damage that results from repeated loading and unloading cycles.
Corrosion, a chemical form of damage, can seriously impair the integrity of pressure equipment.
It arises from harmful reactions between the equipment’s material and environmental elements.
Preventive Measures
Preventing damage involves implementing proper design features, regular maintenance, and using protective coatings or treatments.
Conducting regular inspections and maintenance checks can help identify early signs of wear and tear, enabling timely repairs.
Choosing corrosion-resistant materials, applying protective coatings, and maintaining a controlled environment can significantly reduce the risk of chemical damage.
Key Points in Pressure Equipment Design
Designing pressure equipment requires careful consideration of numerous factors to ensure safety and longevity.
Following guidelines and standards is vital in achieving a reliable design.
Component Design
The design of individual components that make up the pressure equipment is critical.
These components include shells, heads, nozzles, and supports.
Each part must be designed to withstand the internal pressure and any external forces acting upon it.
Stress analysis is a common technique used to ensure components do not exceed their stress limits.
This involves calculating the stress distribution within the equipment and optimizing the design accordingly.
Safety Considerations
Safety is a paramount concern in the design and operation of pressure equipment.
Implementing redundancy in design, such as adding extra safety valves or overpressure protection devices, can reduce the likelihood of catastrophic failure.
Additionally, adhering to industry standards and regulations, such as the ASME Boiler and Pressure Vessel Code, ensures that the design meets recognized safety benchmarks.
Testing and Inspection
Testing and inspection are crucial aspects of pressure equipment design.
Hydrostatic testing, non-destructive testing, and visual inspections are commonly performed to verify the equipment’s integrity and performance.
Regular inspections help ensure that the equipment continues to operate safely and efficiently.
Inspection schedules should be determined based on the risk assessment and operating conditions of the equipment.
Conclusion
In summary, the fundamentals of strength design, addressing damage and deterioration, and emphasizing key design points are essential for pressure vessels and equipment.
By understanding material properties, implementing preventive measures, and prioritizing safety, engineers can design pressure equipment that is robust, reliable, and long-lasting.
Continuous advancements in materials, design techniques, and safety standards play a significant role in the evolution of pressure equipment, contributing to safer, more efficient industrial operations.
資料ダウンロード
QCD調達購買管理クラウド「newji」は、調達購買部門で必要なQCD管理全てを備えた、現場特化型兼クラウド型の今世紀最高の購買管理システムとなります。
ユーザー登録
調達購買業務の効率化だけでなく、システムを導入することで、コスト削減や製品・資材のステータス可視化のほか、属人化していた購買情報の共有化による内部不正防止や統制にも役立ちます。
NEWJI DX
製造業に特化したデジタルトランスフォーメーション(DX)の実現を目指す請負開発型のコンサルティングサービスです。AI、iPaaS、および先端の技術を駆使して、製造プロセスの効率化、業務効率化、チームワーク強化、コスト削減、品質向上を実現します。このサービスは、製造業の課題を深く理解し、それに対する最適なデジタルソリューションを提供することで、企業が持続的な成長とイノベーションを達成できるようサポートします。
オンライン講座
製造業、主に購買・調達部門にお勤めの方々に向けた情報を配信しております。
新任の方やベテランの方、管理職を対象とした幅広いコンテンツをご用意しております。
お問い合わせ
コストダウンが利益に直結する術だと理解していても、なかなか前に進めることができない状況。そんな時は、newjiのコストダウン自動化機能で大きく利益貢献しよう!
(Β版非公開)