- お役立ち記事
- Fundamentals of structural optimization technology and application to equipment development and design
月間77,185名の
製造業ご担当者様が閲覧しています*
*2025年2月28日現在のGoogle Analyticsのデータより
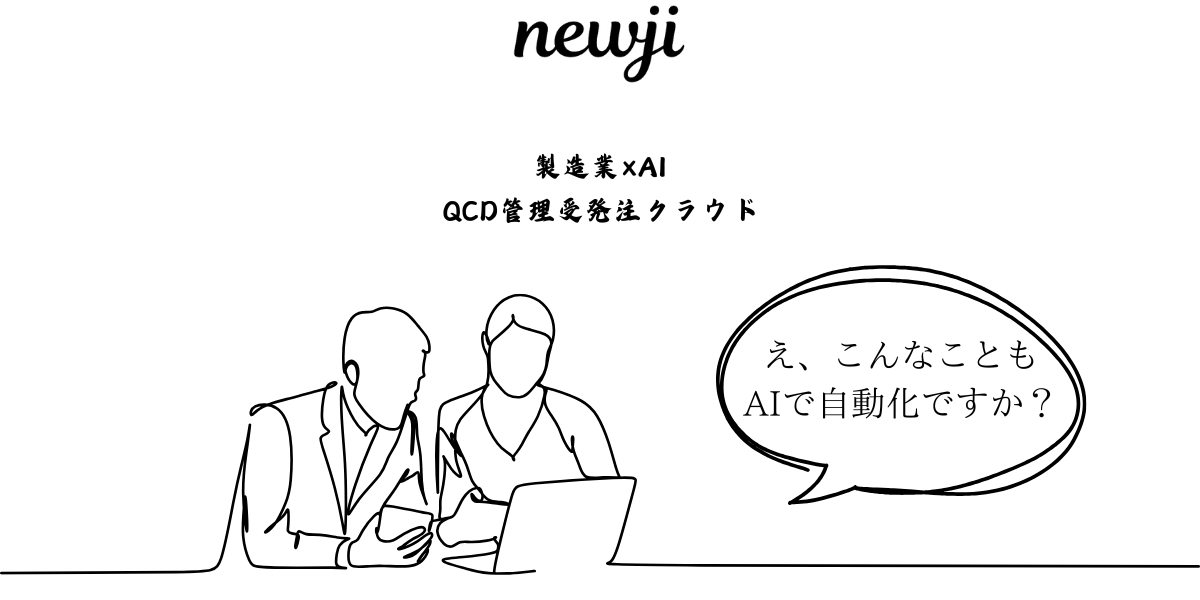
Fundamentals of structural optimization technology and application to equipment development and design
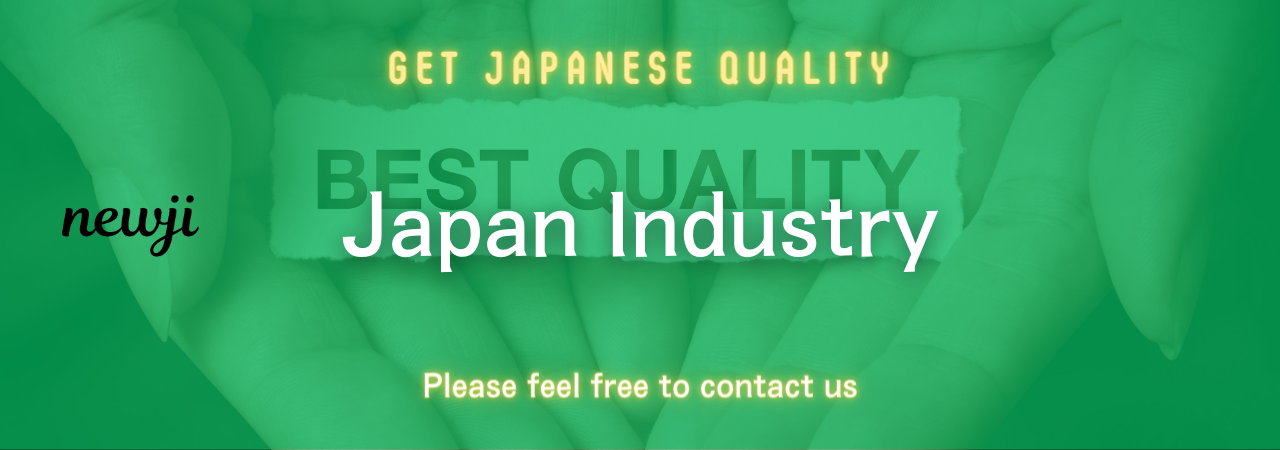
目次
Understanding Structural Optimization Technology
Structural optimization is a crucial component of modern engineering that focuses on improving the efficiency and performance of equipment and structures.
This technology uses mathematical models and algorithms to identify the best possible design configurations.
By doing so, it minimizes material usage while maximizing performance capabilities, which is essential in a world where resources are finite.
In essence, structural optimization seeks to create designs that are lightweight yet robust, reducing costs while maintaining or enhancing functionality.
The principles of this technology have been applied in various fields, including aerospace, automotive, civil engineering, and more, leading to significant advancements in these industries.
Key Concepts of Structural Optimization
Structural optimization involves a few fundamental concepts, which include design variables, objectives, and constraints.
These elements work together to form the backbone of optimization problems.
Design variables are the parameters that can be altered during the optimization process.
These are the aspects of a design, such as the shape, size, or material properties, that can be modified to achieve optimal performance.
Objectives refer to the goals set for the optimization process.
These can be goals such as minimizing weight, maximizing strength, or achieving a balance between various performance criteria.
Constraints are limitations or requirements that the design must adhere to.
These could be physical limitations, such as maximum allowable stress, or regulatory standards that must be met.
Types of Structural Optimization
There are several types of structural optimization, each with its own methodology and applications.
Some of the most common types include:
1. **Size Optimization**: This involves adjusting the dimensions or thicknesses of components to meet desired performance criteria.
It is particularly useful for reducing material costs without compromising the structure’s integrity.
2. **Shape Optimization**: Shape optimization focuses on altering the geometry of a design to enhance performance.
It is widely used in aerodynamics to minimize drag and improve fuel efficiency in vehicles and aircraft.
3. **Topology Optimization**: This type of optimization is concerned with the spatial distribution of material within a given design space.
It often leads to innovative designs that use less material while retaining structural strength.
Topology optimization is frequently employed in additive manufacturing, where complex geometries can be easily produced.
The Process of Structural Optimization
The process of structural optimization generally follows a systematic approach:
1. **Define the Problem**: The first step involves clearly defining the optimization problem, including specifying design variables, objectives, and constraints.
2. **Modeling**: Create a mathematical or computational model of the structure.
This model will simulate how the structure behaves under various conditions and provide a basis for optimization.
3. **Optimization Algorithm**: Select and apply an appropriate optimization algorithm.
Algorithms can be heuristic, such as genetic algorithms, or deterministic, like gradient-based methods.
4. **Iterative Process**: The optimization process is typically iterative, meaning it involves repeated cycles of testing and refining the design.
This continues until the desired performance criteria are achieved.
5. **Validation**: Once an optimal solution is found, it is important to validate it through practical testing or further simulation to ensure its feasibility and performance.
Applications of Structural Optimization in Equipment Development
Structural optimization plays a vital role in equipment development across various industries by enabling better design solutions that are both cost-effective and environmentally friendly.
Aerospace Industry
In the aerospace industry, structural optimization is critical for developing aircraft that are lighter and more fuel-efficient.
Optimization techniques are used to design wing structures, fuselage components, and other parts to improve aerodynamics and reduce weight.
This leads to better fuel economy and lower greenhouse gas emissions, making flights not only more cost-effective but also environmentally friendly.
Automotive Industry
The automotive industry benefits from structural optimization by producing vehicles that are safer, lighter, and more efficient.
Optimizing the structure of a vehicle helps manufacturers meet stringent safety regulations while also enhancing performance and fuel efficiency.
Additionally, with the rise of electric vehicles, optimizing battery pack structures is essential to extend their range and lifespan.
Civil Engineering
In civil engineering, structural optimization is used in the design of bridges, buildings, and other infrastructure projects.
By optimizing the structure, engineers can ensure that these projects are both cost-effective and capable of withstanding environmental challenges such as earthquakes or high winds.
This technology plays a critical role in sustainable development by maximizing the use of available resources.
Challenges in Structural Optimization
Despite its advantages, structural optimization comes with its own set of challenges:
1. **Complexity**: Optimization problems can become highly complex, requiring significant computational power and time to solve.
This is especially true for large-scale projects or where numerous variables and constraints are involved.
2. **Uncertainty**: Real-world applications often involve uncertainties, such as variable material properties or unpredictable load conditions, which can complicate the optimization process.
3. **Integration**: Integrating optimized designs into existing production processes or systems can pose challenges, particularly when transitioning from traditional manufacturing methods to modern techniques like additive manufacturing.
4. **Balancing Objectives**: Often, multiple objectives must be balanced, such as cost versus performance.
Finding an optimal solution that satisfies all criteria can be difficult and requires careful consideration.
The Future of Structural Optimization
As technology and computing power continue to advance, the future of structural optimization looks promising.
Machine learning and artificial intelligence are being integrated into optimization processes, allowing for more sophisticated analyses and faster computations.
This will likely lead to groundbreaking innovations in various fields.
Moreover, with an increased focus on sustainability, structural optimization will become even more essential in developing technologies and systems that make efficient use of resources.
It will continue to drive progress in the design and development of equipment, leading to significant improvements in performance, cost, and environmental impact.
In conclusion, structural optimization technology is an indispensable tool in modern engineering, providing solutions that are cost-effective and environmentally sustainable.
Its continued advancement will undoubtedly contribute to a future where engineering solutions meet the complex demands of a rapidly evolving world.
資料ダウンロード
QCD管理受発注クラウド「newji」は、受発注部門で必要なQCD管理全てを備えた、現場特化型兼クラウド型の今世紀最高の受発注管理システムとなります。
ユーザー登録
受発注業務の効率化だけでなく、システムを導入することで、コスト削減や製品・資材のステータス可視化のほか、属人化していた受発注情報の共有化による内部不正防止や統制にも役立ちます。
NEWJI DX
製造業に特化したデジタルトランスフォーメーション(DX)の実現を目指す請負開発型のコンサルティングサービスです。AI、iPaaS、および先端の技術を駆使して、製造プロセスの効率化、業務効率化、チームワーク強化、コスト削減、品質向上を実現します。このサービスは、製造業の課題を深く理解し、それに対する最適なデジタルソリューションを提供することで、企業が持続的な成長とイノベーションを達成できるようサポートします。
製造業ニュース解説
製造業、主に購買・調達部門にお勤めの方々に向けた情報を配信しております。
新任の方やベテランの方、管理職を対象とした幅広いコンテンツをご用意しております。
お問い合わせ
コストダウンが利益に直結する術だと理解していても、なかなか前に進めることができない状況。そんな時は、newjiのコストダウン自動化機能で大きく利益貢献しよう!
(β版非公開)