- お役立ち記事
- Fundamentals of Surface Roughness Management in Metalworking
月間76,176名の
製造業ご担当者様が閲覧しています*
*2025年3月31日現在のGoogle Analyticsのデータより
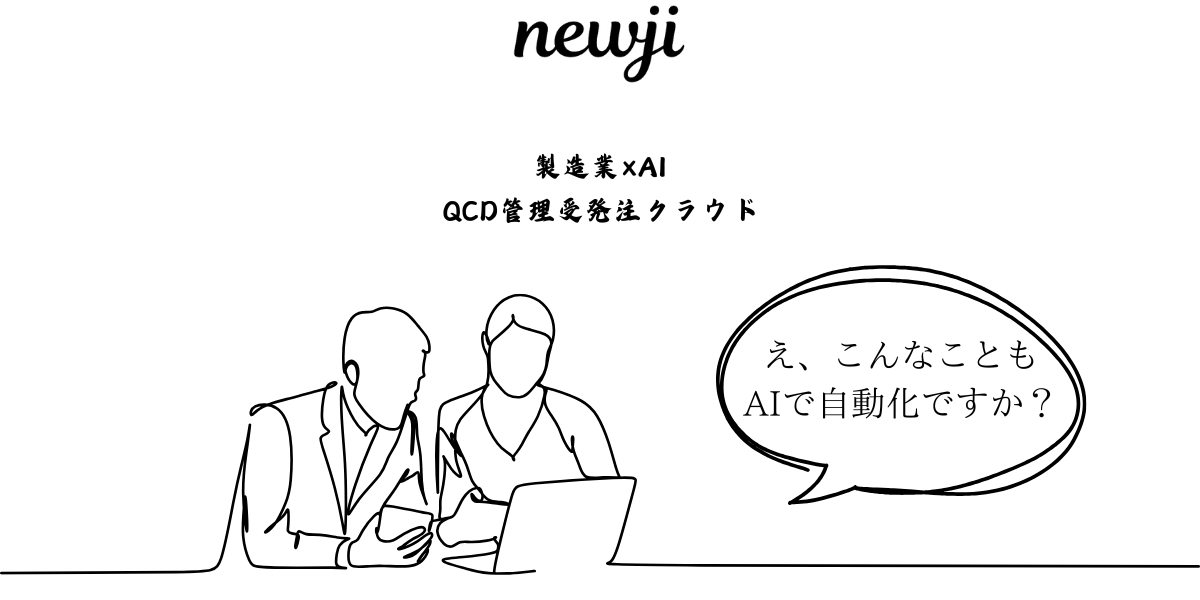
Fundamentals of Surface Roughness Management in Metalworking
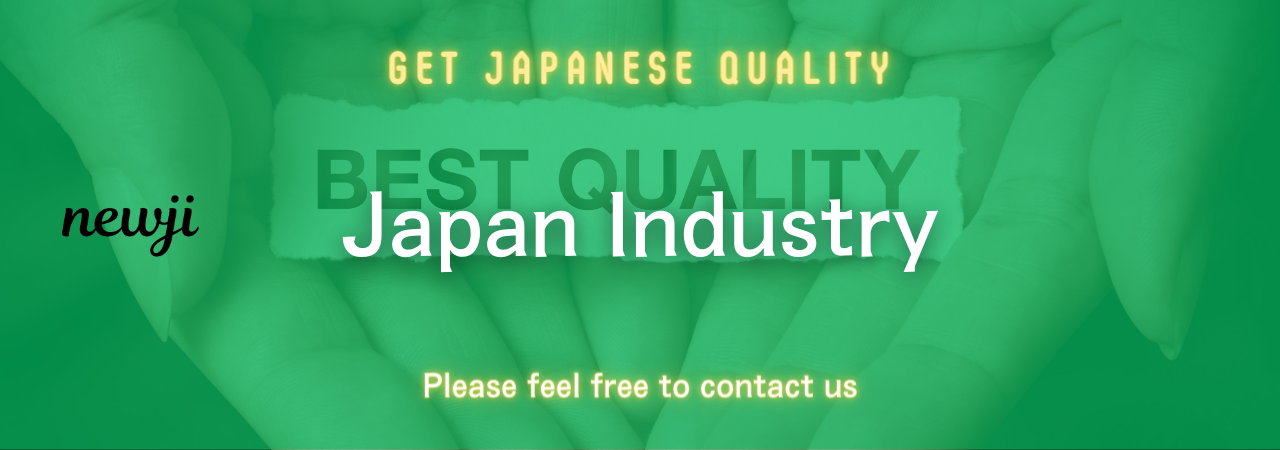
目次
Understanding Surface Roughness
Surface roughness refers to the texture and irregularities found on the surface of metal workpieces.
It is a crucial factor in metalworking as it affects the performance, aesthetics, and lifespan of the finished product.
A smooth surface may be desired for aesthetic purposes or to reduce friction, while a rougher surface may be necessary for applications that require enhanced bonding or adhesion.
Monitoring and managing surface roughness is vital in ensuring the quality and functionality of metal components.
By understanding the fundamentals of surface roughness, you can make informed decisions in the manufacturing process to achieve the desired surface finish.
The Importance of Surface Roughness Management
Proper surface roughness management in metalworking helps in maintaining consistent quality and performance of the produced parts.
In applications where precision is key, such as in aerospace or medical device manufacturing, maintaining the right level of surface roughness is critical.
It ensures that components fit together correctly and perform their intended functions without failure.
Additionally, good surface roughness management can lead to improved product durability.
A properly finished surface can resist wear and corrosion better, enhancing the longevity of the product.
This can result in lower maintenance costs and fewer replacements over time.
Factors Affecting Surface Roughness
Several factors influence the surface roughness of a metal workpiece.
These factors must be considered during the manufacturing process to achieve the desired finish.
Material Properties
The material of the workpiece plays a significant role in determining surface roughness.
Different metals have varying hardness, ductility, and grain structures, which can affect how they respond to machining processes.
Machining Parameters
The choice of machining parameters, such as cutting speed, feed rate, and depth of cut, can greatly influence surface roughness.
Optimizing these parameters helps in achieving the desired surface quality.
Tool Condition
The condition of the cutting tools used in machining also impacts surface roughness.
Dull or damaged tools can produce rougher surfaces, while well-maintained tools are essential for achieving smoother finishes.
Cooling and Lubrication
Effective cooling and lubrication reduce friction and heat during machining, which can help in attaining a smoother surface.
The choice of coolant and its application method should be tailored to the material and machining operation.
Methods to Measure Surface Roughness
Accurate measurement of surface roughness is essential in ensuring the product meets quality standards.
Several methods can be employed for measuring surface roughness, with varying levels of precision and applicability.
Contact Profilometry
Contact profilometry involves the use of a stylus that physically touches and traces the surface profile.
This method measures the vertical deviations from a mean surface level, providing a detailed analysis of surface features.
While highly accurate, contact profilometry can be time-consuming and may not be suitable for delicate surfaces.
Optical Profilometry
Optical profilometry uses light to measure surface roughness without contact.
It is faster than contact methods and suitable for delicate or soft surfaces, as it does not risk damaging them.
However, it may be less effective on highly reflective or transparent materials.
Scanning Electron Microscopy (SEM)
SEM provides high-resolution images of surface topography, making it a powerful tool for detailed analysis of surface roughness.
Though highly accurate, it is expensive and typically reserved for research or high-precision applications.
Techniques for Managing Surface Roughness
Several techniques can be employed to control and improve surface roughness in metalworking.
These techniques focus on optimizing machining processes and tool usage.
Tool Selection and Maintenance
Choosing the right tools for the job and ensuring they are properly maintained is crucial.
Regularly sharpening and replacing tools can help maintain optimal cutting conditions and achieve desired surface finishes.
Process Optimization
Optimizing machining parameters, such as feed rate, cutting speed, and depth of cut, can lead to better control of surface roughness.
Consider running experimental trials to find the best combination of parameters for your materials and processes.
Use of Proper Cooling and Lubrication
Proper application of coolants and lubricants minimizes friction and heat buildup during machining.
This not only extends tool life but also enhances surface finish quality.
Post-Machining Processes
In some cases, post-machining processes like polishing, honing, or buffing may be necessary to achieve the desired surface quality.
These additional steps can remove minor imperfections and refine the surface texture.
Conclusion
Understanding and managing surface roughness is fundamental to the success of metalworking projects.
By considering material properties, machining parameters, and tool conditions, manufacturers can produce high-quality, durable metal parts that meet precise specifications.
Regular measurement and monitoring of surface roughness, coupled with the right techniques, ensure optimal performance and aesthetics in finished products.
Implement these practices in your metalworking processes to achieve superior surface quality and gain a competitive edge in the market.
資料ダウンロード
QCD管理受発注クラウド「newji」は、受発注部門で必要なQCD管理全てを備えた、現場特化型兼クラウド型の今世紀最高の受発注管理システムとなります。
ユーザー登録
受発注業務の効率化だけでなく、システムを導入することで、コスト削減や製品・資材のステータス可視化のほか、属人化していた受発注情報の共有化による内部不正防止や統制にも役立ちます。
NEWJI DX
製造業に特化したデジタルトランスフォーメーション(DX)の実現を目指す請負開発型のコンサルティングサービスです。AI、iPaaS、および先端の技術を駆使して、製造プロセスの効率化、業務効率化、チームワーク強化、コスト削減、品質向上を実現します。このサービスは、製造業の課題を深く理解し、それに対する最適なデジタルソリューションを提供することで、企業が持続的な成長とイノベーションを達成できるようサポートします。
製造業ニュース解説
製造業、主に購買・調達部門にお勤めの方々に向けた情報を配信しております。
新任の方やベテランの方、管理職を対象とした幅広いコンテンツをご用意しております。
お問い合わせ
コストダウンが利益に直結する術だと理解していても、なかなか前に進めることができない状況。そんな時は、newjiのコストダウン自動化機能で大きく利益貢献しよう!
(β版非公開)