- お役立ち記事
- Fundamentals of thermal spraying technology and its application to high functionality and properties
月間76,176名の
製造業ご担当者様が閲覧しています*
*2025年3月31日現在のGoogle Analyticsのデータより
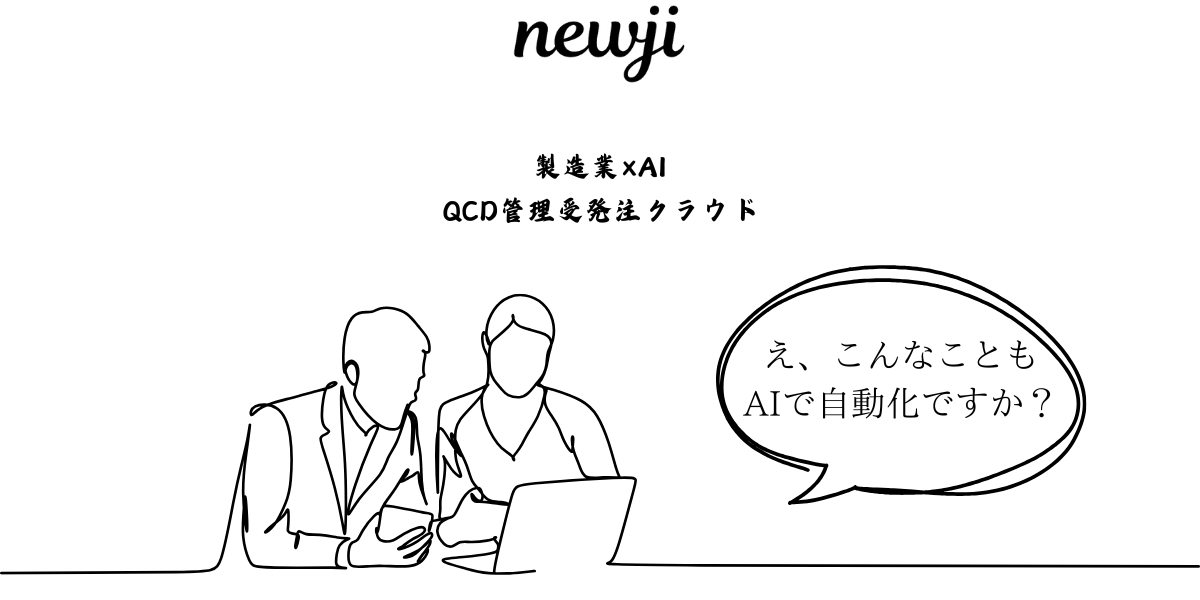
Fundamentals of thermal spraying technology and its application to high functionality and properties
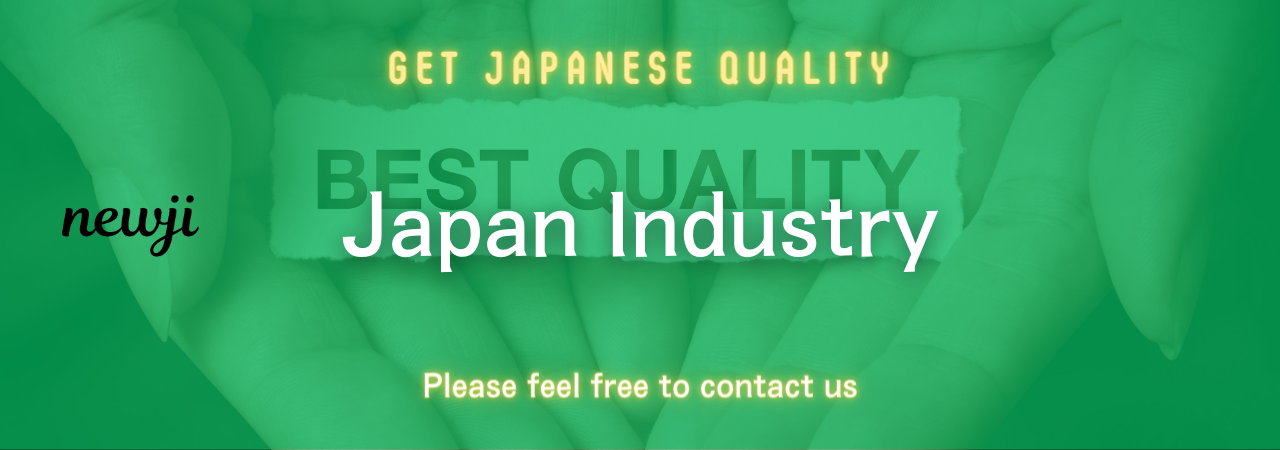
目次
Introduction to Thermal Spraying Technology
Thermal spraying is a group of processes used to apply materials onto a surface to enhance its properties and performance.
This technique involves the heating of materials in various forms—such as powders, wires, or rods—and then propelling them onto a substrate.
The deposited layer forms a coating that can improve wear resistance, reduce corrosion, or enhance other surface characteristics.
What makes thermal spraying unique is its versatility and the range of material options, allowing for customized coatings to meet specific functional requirements.
The Process of Thermal Spraying
Preparation
Before thermal spraying begins, proper surface preparation is crucial for optimal coating adhesion.
Typically, this involves cleaning the surface to remove contaminants and abrasives to roughen the surface.
Roughening ensures physical interlocking of the sprayed material with the substrate, improving the coating’s bond strength.
Material Selection
The choice of material for a thermal spray coating depends on the desired properties.
Common materials include metals, ceramics, plastics, or composites.
For instance, ceramics are popular for their high-temperature resistance, while metals might be chosen for their conductivity or thermal properties.
Application Techniques
There are several thermal spraying techniques, each suited to different materials and applications:
– **Plasma Spraying**: Utilizes a plasma torch to melt materials, suitable for high melting point materials like ceramics.
– **Flame Spraying**: Involves a flame generated by combusting gas to melt the material, often used for low melting point materials.
– **Arc Spraying**: Uses an electric arc to melt the material, common for coating large areas with metallic materials.
– **High-Velocity Oxy-Fuel (HVOF) Spraying**: Combines fuel and oxygen to create a high-velocity jet, ideal for dense, durable coatings.
The choice of technique depends on factors such as the material type, coating requirements, and underlying substrate.
Applications of Thermal Spraying
Industrial Applications
Thermal spraying is widely used in industrial settings to protect machinery and equipment from wear and corrosion.
It’s essential in industries like aerospace, automotive, and manufacturing.
For instance, jet engine components often receive thermal spray coatings to withstand high temperatures and reduce oxidation.
Structural Applications
In civil engineering, thermal spraying prolongs the lifespan of structures by protecting them from environmental conditions.
Steel bridges and buildings can benefit from corrosion-resistant coatings, preventing rust and deterioration.
Medical Applications
The medical industry benefits from thermal spraying, particularly in the development of prosthetics and implants.
Coatings can enhance biocompatibility and promote bone integration.
For example, hydroxyapatite coatings are applied to orthopedic implants to improve their integration with human bone.
Electronics and Energy
In the electronics sector, thermal sprays create insulating or conductive layers necessary for circuit boards and components.
Similarly, in the energy industry, protective coatings on turbines and generators are essential for efficient operation and longevity.
Advantages of Thermal Spraying
Thermal spraying offers several advantages, making it a preferred coating method for various applications.
It provides excellent corrosion resistance, significantly extending the service life of components exposed to harsh environments.
Additionally, it offers flexibility in selecting materials, allowing for tailored solutions that meet specific requirements.
The process is also relatively quick, reducing downtime and increasing productivity.
Moreover, thermal spraying can produce thick coatings without inducing excessive heat stress on the substrate, preserving the structural integrity of sensitive components.
Challenges and Solutions in Thermal Spraying
Coating Defects
One challenge is the occurrence of defects such as porosity, cracks, or delamination.
These can be mitigated by optimizing spraying parameters and proper surface preparation.
Employing advanced diagnostic tools can also help monitor and adjust the process in real-time.
Material Limitations
Not all materials are suitable for thermal spraying, primarily due to their melting point or thermal properties.
Selecting the right spraying method and equipment can address this issue, broadening the range of applicable materials.
Environmental and Health Concerns
Thermal spraying may generate dust and fumes, posing risks to workers and the environment.
Using safety protocols, personal protective equipment, and proper ventilation can mitigate these concerns.
Future Trends in Thermal Spraying
Advancements in thermal spraying technology continue to emerge, driven by the demand for improved coatings and increased efficiency.
Innovation efforts focus on developing new materials with enhanced properties, such as nano-structured coatings that offer superior performance.
Automation and digitalization are also key trends, with robotic spraying systems and data analytics enhancing precision and repeatability.
Furthermore, sustainable practices are gaining traction, encouraging the development of eco-friendly materials and processes.
Conclusion
Thermal spraying technology plays a vital role across various industries, providing an effective means of enhancing the functionality and longevity of components and structures.
With its versatility in materials and methods, it offers tailored solutions for specific needs, backed by ongoing advancements to address challenges and expand its potential.
As industries continue to strive for better performance and sustainability, thermal spraying will remain a crucial tool in achieving these goals.
資料ダウンロード
QCD管理受発注クラウド「newji」は、受発注部門で必要なQCD管理全てを備えた、現場特化型兼クラウド型の今世紀最高の受発注管理システムとなります。
ユーザー登録
受発注業務の効率化だけでなく、システムを導入することで、コスト削減や製品・資材のステータス可視化のほか、属人化していた受発注情報の共有化による内部不正防止や統制にも役立ちます。
NEWJI DX
製造業に特化したデジタルトランスフォーメーション(DX)の実現を目指す請負開発型のコンサルティングサービスです。AI、iPaaS、および先端の技術を駆使して、製造プロセスの効率化、業務効率化、チームワーク強化、コスト削減、品質向上を実現します。このサービスは、製造業の課題を深く理解し、それに対する最適なデジタルソリューションを提供することで、企業が持続的な成長とイノベーションを達成できるようサポートします。
製造業ニュース解説
製造業、主に購買・調達部門にお勤めの方々に向けた情報を配信しております。
新任の方やベテランの方、管理職を対象とした幅広いコンテンツをご用意しております。
お問い合わせ
コストダウンが利益に直結する術だと理解していても、なかなか前に進めることができない状況。そんな時は、newjiのコストダウン自動化機能で大きく利益貢献しよう!
(β版非公開)