- お役立ち記事
- Fundamentals of “Toyota-style problem solving” and “why-why analysis” and improvement of solving ability/examples
月間76,176名の
製造業ご担当者様が閲覧しています*
*2025年3月31日現在のGoogle Analyticsのデータより
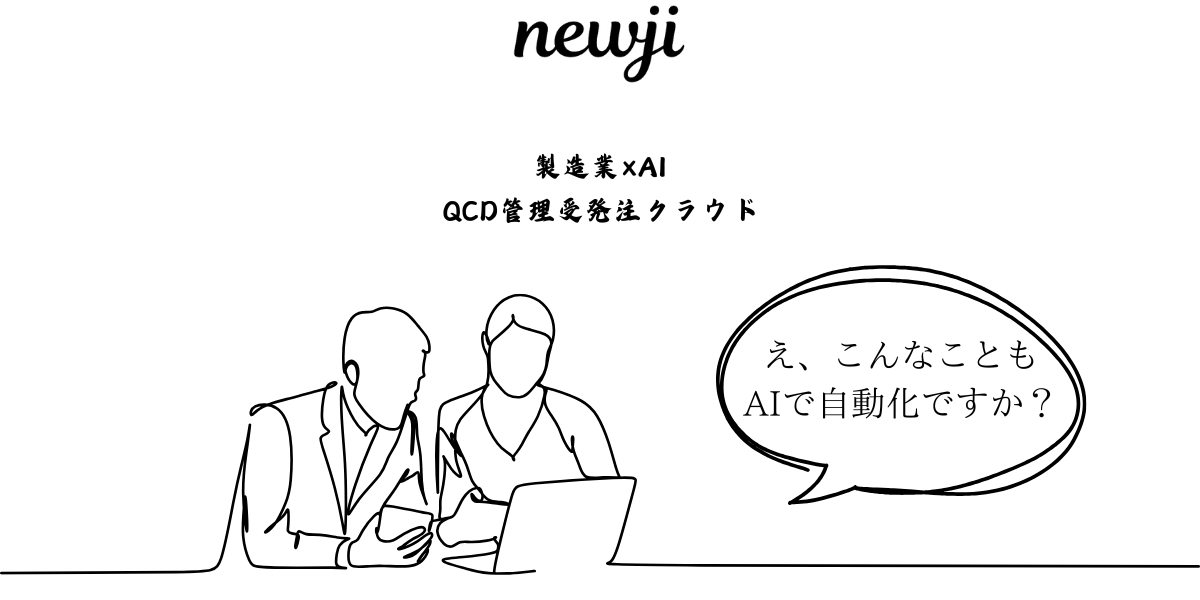
Fundamentals of “Toyota-style problem solving” and “why-why analysis” and improvement of solving ability/examples
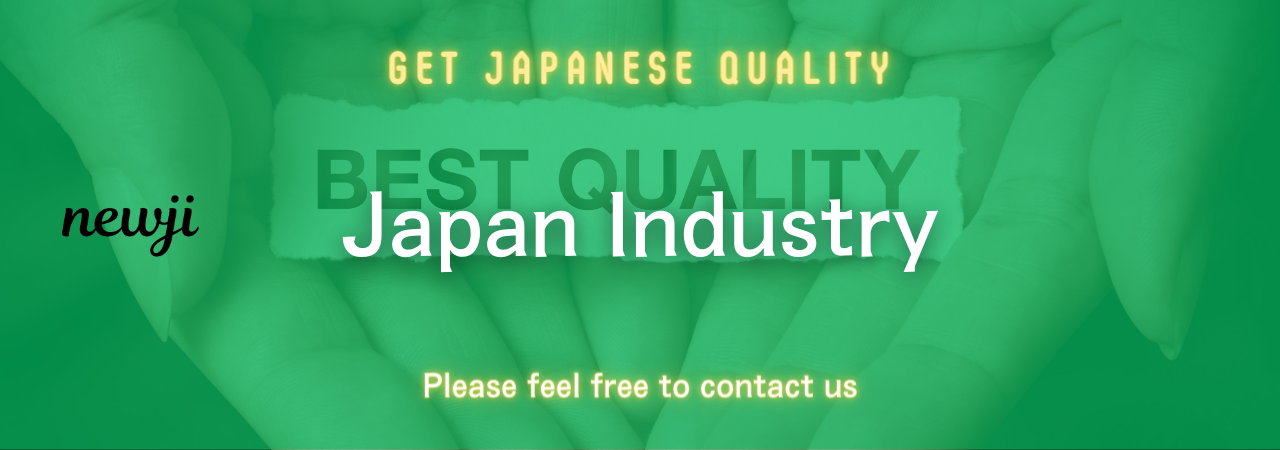
目次
Understanding the Toyota-Style Problem Solving Approach
Toyota’s problem-solving philosophy is renowned worldwide for its effectiveness and efficiency in optimizing processes and enhancing productivity.
This method is deeply rooted in continuous improvement, known as “kaizen,” and encourages organizations to foster a culture of constant development.
The Toyota-style problem-solving approach hinges on identifying problems fundamentally, understanding their root causes, and implementing sustainable solutions.
By delving into the essence of an issue, rather than just addressing its symptoms, companies can achieve long-term improvements.
Core Principles of Toyota’s Problem Solving
At the heart of Toyota’s problem-solving methodology are several key principles.
These include effective communication, a systematic approach, and an unwavering commitment to improvement.
The process often starts with identifying a problem and then involves gathering data to understand it fully.
Teamwork is crucial, with contributions from various team members offering diverse perspectives and insights into the issues at hand.
The second principle focuses on understanding the root causes.
Through techniques like the “Five Whys” or “why-why analysis,” teams can peel back the layers of symptoms to find the underlying cause.
Finally, the implementation of solutions is thorough and meticulous.
They emphasize testing potential solutions in a controlled environment to ensure they resolve the problem without creating new issues.
This methodical approach ensures long-lasting resolutions rather than temporary fixes.
Exploring the “Why-Why Analysis” Technique
The “why-why analysis” is a simple yet powerful tool designed to dig deeper into problems.
Originating from Toyota’s production system, this technique helps identify root causes by asking “why” multiple times, each answer requiring a further “why” until the fundamental issue is uncovered.
How to Perform a Why-Why Analysis
1. Clearly Define the Problem:
Start by ensuring that everyone involved understands the problem.
State it clearly and concisely to create a common understanding.
2. Ask “Why?”:
Pose the first “why” to identify the immediate cause of the problem.
It’s essential to document this process to maintain clarity.
3. Continue Asking “Why?”:
Each time you answer the question, follow up with another “why.”
Repeat this at least five times, hence the name “Five Whys.”
However, remember that the number five is a guideline, not a rule, and it might take fewer or more iterations to reach the root cause.
4. Review and Implement Solutions:
Once the root cause is identified, the next step is to brainstorm solutions.
Consider developing multiple solutions and evaluate them for feasibility and impact.
Implement the most effective one and monitor its outcome to ensure the problem is resolved.
5. Document and Communicate:
Document the entire process, the findings, and the actions taken.
Spread this information across the organization as it can serve as a learning tool and help prevent similar problems in the future.
Boosting Problem-Solving Skills
Improving problem-solving skills can significantly enhance an organization’s ability to handle challenges swiftly and effectively.
Here are some strategies to cultivate such skills:
Promote a Problem-Solving Culture
Encourage employees at all levels to engage in problem-solving activities.
When every team member understands their role in addressing issues, it fosters a proactive approach to improvement.
Organizations should nurture an environment where questioning and investigative thinking are respected and rewarded.
Provide Training and Resources
Offering training programs on techniques like the why-why analysis can help team members refine their skills.
Moreover, providing resources such as literature, workshops, and expert sessions can also contribute to deepening their understanding and capability.
Foster Collaborative Efforts
Collaboration is a crucial element in problem-solving.
Through group activities and cross-departmental teamwork, diverse perspectives can be utilized to offer multi-faceted solutions.
This collaborative spirit can often lead to innovative approaches that might not surface in isolated settings.
Encourage Creativity and Innovation
While systematic approaches are foundational, fostering creative thinking can lead to breakthrough solutions.
Encouraging innovation alongside structured techniques can produce unexpected yet effective results.
Examples of Effective Problem Solving
Real-world examples of the successful application of Toyota-style problem solving can offer valuable insights.
Manufacturing Improvements
In a manufacturing setting, frequent breakdowns of a critical machine might cause delays.
By employing the why-why analysis, the team might discover that insufficient lubrication caused these breakdowns.
The solution could involve implementing a schedule for regular maintenance and checks, leading to increased machinery uptime and productivity.
Service Industry Enhancements
In the service sector, if customer satisfaction scores drop, a why-why analysis might reveal that the root cause is a lack of training for new employees.
Addressing this problem with a new comprehensive training program for onboarding can result in higher satisfaction rates and better service delivery.
By understanding and implementing Toyota’s problem-solving techniques, organizations can unlock the potential to improve processes, enhance quality, and foster a more adaptive and resilient workforce.
This not only aids in addressing existing problems but also equips them to tackle future challenges effectively.
資料ダウンロード
QCD管理受発注クラウド「newji」は、受発注部門で必要なQCD管理全てを備えた、現場特化型兼クラウド型の今世紀最高の受発注管理システムとなります。
ユーザー登録
受発注業務の効率化だけでなく、システムを導入することで、コスト削減や製品・資材のステータス可視化のほか、属人化していた受発注情報の共有化による内部不正防止や統制にも役立ちます。
NEWJI DX
製造業に特化したデジタルトランスフォーメーション(DX)の実現を目指す請負開発型のコンサルティングサービスです。AI、iPaaS、および先端の技術を駆使して、製造プロセスの効率化、業務効率化、チームワーク強化、コスト削減、品質向上を実現します。このサービスは、製造業の課題を深く理解し、それに対する最適なデジタルソリューションを提供することで、企業が持続的な成長とイノベーションを達成できるようサポートします。
製造業ニュース解説
製造業、主に購買・調達部門にお勤めの方々に向けた情報を配信しております。
新任の方やベテランの方、管理職を対象とした幅広いコンテンツをご用意しております。
お問い合わせ
コストダウンが利益に直結する術だと理解していても、なかなか前に進めることができない状況。そんな時は、newjiのコストダウン自動化機能で大きく利益貢献しよう!
(β版非公開)