- お役立ち記事
- Fundamentals of ultrasonic sensing and applications to nondestructive measurement, material evaluation, and condition monitoring
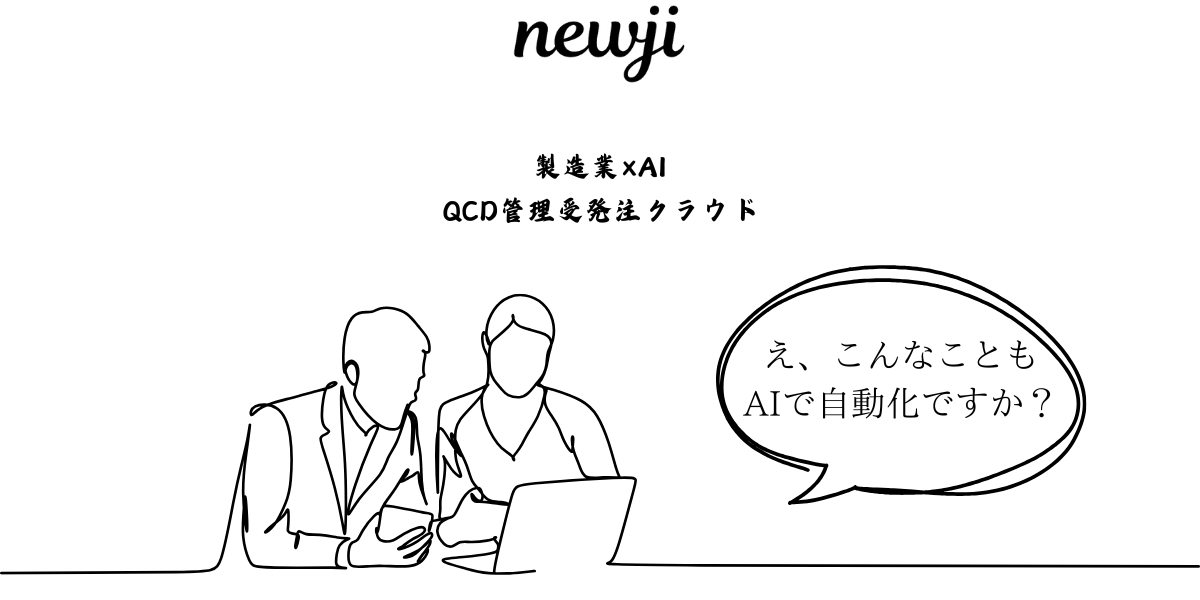
Fundamentals of ultrasonic sensing and applications to nondestructive measurement, material evaluation, and condition monitoring
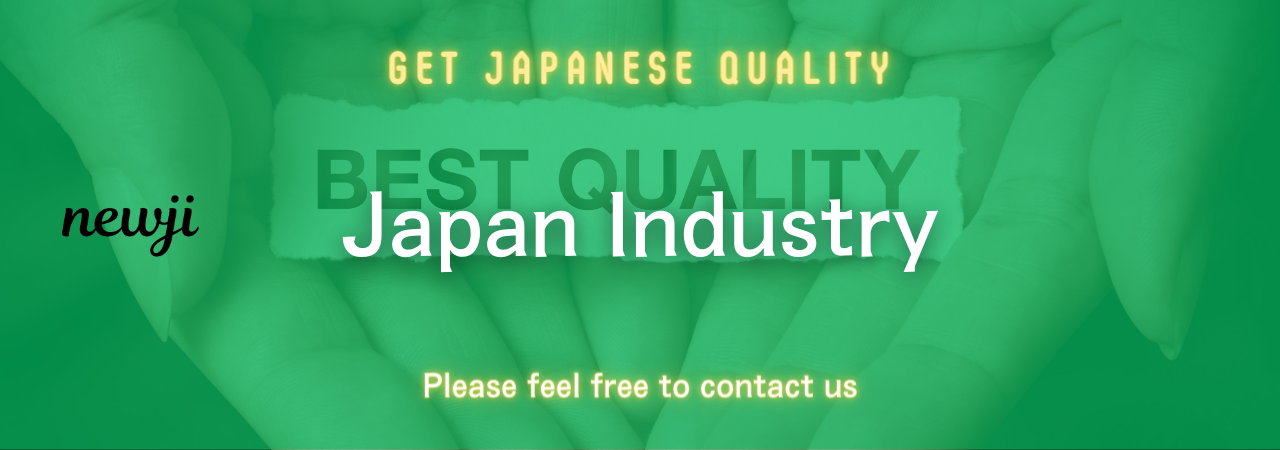
Understanding Ultrasonic Sensing
Ultrasonic sensing is a technology utilized in various fields for measuring distances, detecting objects, and monitoring conditions without causing harm or destruction to the objects being assessed.
By leveraging sound waves beyond human hearing capabilities, ultrasonic sensors play a crucial role in collecting data and providing insights into material evaluation and condition monitoring.
The key aspect of ultrasonics lies in their ability to penetrate materials and provide information that might not be detectable by other means.
At the heart of ultrasonic sensing is the piezoelectric effect, where mechanical stress applied to materials such as quartz or certain ceramics generates an electric charge.
When an electric signal is applied to a piezoelectric crystal inside the sensor, it vibrates, creating ultrasonic waves.
These waves travel through the air, liquid, or solids, and when they encounter an obstacle, they reflect back to the sensor.
By calculating the time it takes for the waves to return, the sensor can determine the distance to the object or the characteristics of the material.
Nondestructive Measurement Applications
Ultrasonic sensing is widely used in nondestructive testing (NDT) to inspect materials without altering or damaging them.
Industries such as aerospace, automotive, and construction rely heavily on ultrasonic testing to ensure the integrity and safety of components and structures.
Ultrasonic testing can reveal flaws like cracks, voids, and inclusions in metals and composites, which might affect the performance or safety of a piece.
One of the significant advantages of ultrasonic sensing in nondestructive measurement is its precision.
Technicians can inspect components with complex geometries and produce detailed images of their internal structure.
Ultrasonic sensors can detect minute inconsistencies in thickness or composition, allowing for early detection of potential issues.
The technology is not only limited to inspecting solid objects.
Ultrasonic sensing also measures levels and flow rates of liquids, often found in tanks or pipelines.
This application is invaluable in industries such as oil and gas, chemical processing, and water treatment, where accurate fluid monitoring is essential.
Material Evaluation Through Ultrasonic Sensing
Material evaluation often requires detailed understanding of a material’s properties, such as thickness, density, elasticity, and homogeneity.
Ultrasonic sensing provides a non-invasive method to assess these properties with high accuracy and rapid results.
This becomes critical in quality control and material research sectors where repeated, precise assessments are necessary.
An essential feature of ultrasonic material evaluation is its ability to detect changes in material during various production stages or throughout a product’s lifecycle.
For instance, in metal fabrication, ultrasonic testing can evaluate welds and ensure joints are sound and free of defects.
In continuous manufacturing processes, integrating ultrasonic sensors allows for real-time analysis and alerts, ensuring the highest quality products.
Beyond quality control, material evaluation is also crucial for reverse engineering applications.
Ultrasonic testing aids in creating accurate models of existing components without damaging or altering the original item.
This capability is particularly useful in heritage conservation and restoration, where maintaining the original state of historical artifacts is essential.
Condition Monitoring Using Ultrasonics
Condition monitoring with ultrasonic sensing enhances maintenance strategies, extending the life and safety of machines and structures.
By implementing ultrasonic condition monitoring, industries can transition from reactive to predictive maintenance approaches, where anomalies are detected early, preventing potential failures.
One common application in condition monitoring is the use of ultrasound to monitor mechanical wear and lubrication conditions.
By listening to the ultrasonic noise generated by machinery, the system identifies changes in friction levels, indicating inadequate lubrication or excessive wear.
This is especially beneficial in rotating equipment such as motors, pumps, and gearboxes, where maintaining optimal lubrication conditions is critical for performance and longevity.
Furthermore, ultrasonic sensing can monitor structural health in buildings, bridges, and other infrastructures.
By assessing materials like concrete and metal, it detects changes in the material properties and alerts engineers to potential structural weaknesses or fatigue.
Such proactive measures are vital in ensuring structural integrity and public safety, particularly for critical infrastructures like bridges and dams.
Challenges and Future of Ultrasonic Sensing
While ultrasonic sensing offers numerous benefits, certain challenges remain.
For example, the performance of ultrasonic sensors can be affected by environmental conditions such as temperature, humidity, and acoustic impedance variations in the materials.
Methods to mitigate these issues include advanced signal processing techniques and adaptive threshold settings in sensors.
Despite these challenges, the future of ultrasonic sensing technologies is promising, with advancements in sensor designs and materials.
Incorporating artificial intelligence and machine learning with ultrasonic data is expanding the potential applications, enabling more accurate diagnostics and faster response times.
Moreover, newer sensor designs are becoming smaller, more energy-efficient, and capable of operating wirelessly.
These innovations aim to integrate ultrasonic sensing more seamlessly into devices and systems, broadening its application scope further, from medical diagnostics to smart home devices.
Ultrasonic sensing has proven to be a versatile and powerful tool in nondestructive measurement, material evaluation, and condition monitoring.
With continued advancements in technology, its applications will continue to grow and evolve, offering new possibilities across various industries.
資料ダウンロード
QCD調達購買管理クラウド「newji」は、調達購買部門で必要なQCD管理全てを備えた、現場特化型兼クラウド型の今世紀最高の購買管理システムとなります。
ユーザー登録
調達購買業務の効率化だけでなく、システムを導入することで、コスト削減や製品・資材のステータス可視化のほか、属人化していた購買情報の共有化による内部不正防止や統制にも役立ちます。
NEWJI DX
製造業に特化したデジタルトランスフォーメーション(DX)の実現を目指す請負開発型のコンサルティングサービスです。AI、iPaaS、および先端の技術を駆使して、製造プロセスの効率化、業務効率化、チームワーク強化、コスト削減、品質向上を実現します。このサービスは、製造業の課題を深く理解し、それに対する最適なデジタルソリューションを提供することで、企業が持続的な成長とイノベーションを達成できるようサポートします。
オンライン講座
製造業、主に購買・調達部門にお勤めの方々に向けた情報を配信しております。
新任の方やベテランの方、管理職を対象とした幅広いコンテンツをご用意しております。
お問い合わせ
コストダウンが利益に直結する術だと理解していても、なかなか前に進めることができない状況。そんな時は、newjiのコストダウン自動化機能で大きく利益貢献しよう!
(Β版非公開)