- お役立ち記事
- Fundamentals of vacuum and vacuum film formation technology, trouble examples and solutions in creating functional thin films
月間76,176名の
製造業ご担当者様が閲覧しています*
*2025年3月31日現在のGoogle Analyticsのデータより
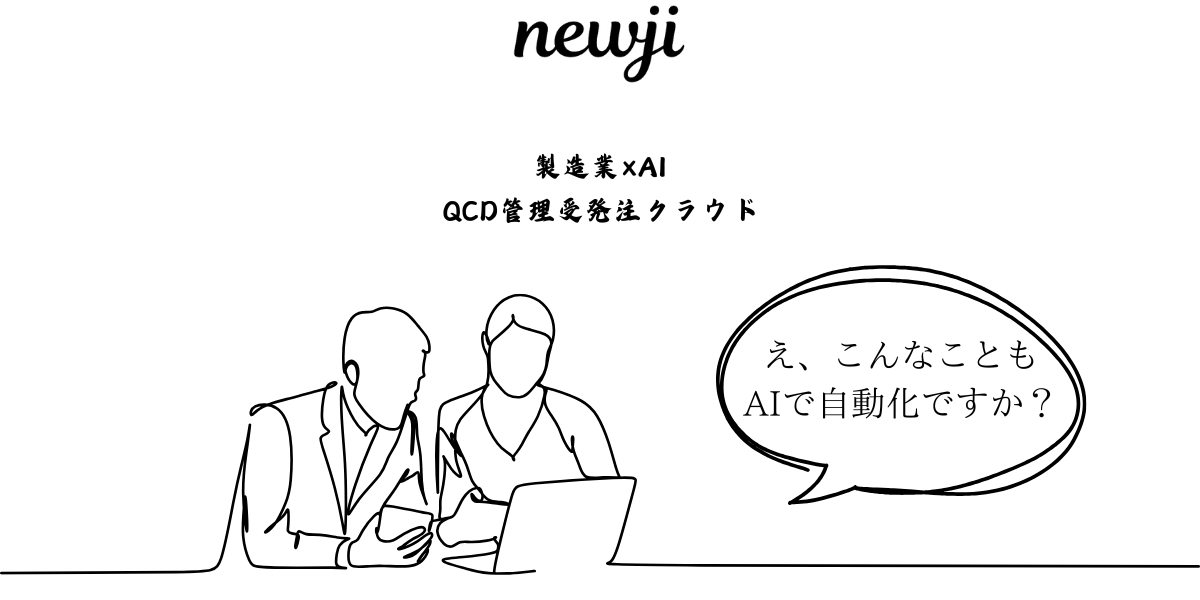
Fundamentals of vacuum and vacuum film formation technology, trouble examples and solutions in creating functional thin films
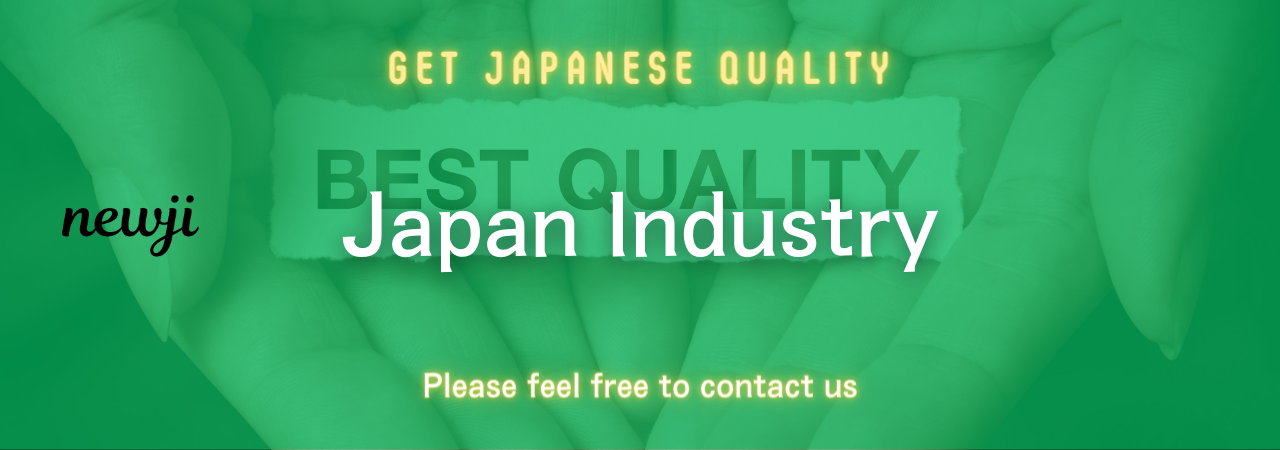
目次
Understanding Vacuum Film Formation Technology
Vacuum film formation technology is a critical component in the production of functional thin films.
Thin films are versatile and are used in a multitude of applications ranging from electronics, optics, to energy devices.
They are composed of materials that are atomically or molecularly deposited onto a substrate in precise layers.
The process typically involves several key stages, namely deposition, growth, and patterning of films.
Among these, the use of vacuum technology is fundamental because it ensures that impure substances do not interfere with the purity and quality of the deposited film.
The Role of Vacuum in Thin Film Deposition
Vacuum plays an indispensable role in the thin film deposition process.
By removing all atmospheric interference, vacuum conditions allow atoms and molecules to travel in a straight path toward the substrate.
This clean, controlled environment ensures that the film is free from contamination, adheres uniformly to the substrate, and performs its intended function effectively.
Without a vacuum, atmospheric gases like oxygen, nitrogen, and carbon dioxide can become part of the film, possibly leading to defective films with properties that do not match the design specifications.
Types of Vacuum Film Deposition Techniques
Understanding the various methods of vacuum deposition is essential for mastering thin film technology.
The primary methods include:
Physical Vapor Deposition (PVD)
Physical Vapor Deposition is a method where material is vaporized in a vacuum and then condensed onto the substrate surface.
PVD includes several processes like evaporation and sputtering.
Evaporation involves heating the material until it vaporizes; sputtering, on the other hand, involves bombarding a target material with energetic particles causing atoms to be ejected and deposited as a thin film on a substrate.
Chemical Vapor Deposition (CVD)
Chemical Vapor Deposition involves the chemical reaction of gaseous precursors, which results in the formation of a thin film.
CVD is highly versatile and can be used to deposit a wide range of materials.
It is particularly valued for its ability to form films with excellent purity and conformal coating across complex surfaces.
Molecular Beam Epitaxy (MBE)
Molecular Beam Epitaxy is a highly controlled method where materials are deposited atomic layer by atomic layer.
This technique is known for creating films with high crystalline quality and thickness precision and is particularly useful in semiconductor manufacturing.
Common Issues in Thin Film Formation
Even with precise control offered by vacuum deposition methods, various challenges can arise during the thin film formation process.
These issues can compromise film quality and functionality.
Contamination
Contamination is a frequent issue that occurs when unwanted particles or gases are incorporated into the film.
This can be due to impurities in the deposition materials, improperly cleaned substrates, or leaks in the vacuum system.
To mitigate contamination, all equipment and materials must be meticulously cleaned, and the vacuum system needs regular maintenance.
Non-uniform Film Thickness
Achieving uniform film thickness is essential for the optimal performance of thin films.
Non-uniform deposits can result from an improper substrate alignment, inconsistent deposition rates, or fluctuations in the deposition environment.
Adjustments in substrate movement, deposition parameters, and detailed monitoring of the process can help address these issues.
Adhesion Problems
Poor adhesion between the thin film and the substrate can lead to delamination or peeling, causing functional failure.
Several factors such as surface roughness, inadequate surface preparation, or a mismatch of thermal expansion coefficients can contribute to adhesion problems.
Surface treatment techniques and selecting compatible materials for both the film and substrate can improve adhesion.
Stress in Films
Stress in thin films can lead to buckling, cracking, or failure.
This stress can be intrinsic, caused by the deposition process, or extrinsic, due to thermal or mechanical factors.
Careful selection of deposition parameters, substrate materials, and annealing processes can help alleviate unwanted stress.
Solutions and Best Practices
Addressing issues in vacuum film formation technology involves a combination of careful process design, regular maintenance, and using appropriate materials.
Key solutions and best practices to improve thin film deposition include:
Regular Maintenance
Keeping equipment in optimal condition through regular maintenance minimizes the risk of leaks and contamination.
Ensure that vacuum pumps, gas lines, and deposition sources are all functioning correctly and are free from contaminants.
Optimizing Process Parameters
Fine-tuning deposition parameters such as temperature, pressure, and deposition rate can lead to better quality films.
Regularly calibrate instruments and perform trial runs to establish the optimal settings for each specific application.
Material Selection
Selecting the right materials for both the thin film and the substrate is crucial in preventing adhesion issues and ensuring film functionality.
Consider materials’ chemical compatibility, thermal expansion coefficients, and durability.
Using Advanced Monitoring Techniques
Implementing advanced monitoring and analysis techniques, such as spectrometry and microscopy, enables real-time observation of the deposition process.
These tools help detect and rectify problems early, ensuring the production of high-quality films.
Conclusion
The fundamentals of vacuum and vacuum film formation technology provide a solid framework for understanding the challenges and solutions in creating functional thin films.
The use of a vacuum in deposition processes is key to achieving films with the desired properties, free from contamination and defects.
Awareness of common issues and implementing best practices ensure that thin film technology continues to meet the advancing needs of various industries.
資料ダウンロード
QCD管理受発注クラウド「newji」は、受発注部門で必要なQCD管理全てを備えた、現場特化型兼クラウド型の今世紀最高の受発注管理システムとなります。
ユーザー登録
受発注業務の効率化だけでなく、システムを導入することで、コスト削減や製品・資材のステータス可視化のほか、属人化していた受発注情報の共有化による内部不正防止や統制にも役立ちます。
NEWJI DX
製造業に特化したデジタルトランスフォーメーション(DX)の実現を目指す請負開発型のコンサルティングサービスです。AI、iPaaS、および先端の技術を駆使して、製造プロセスの効率化、業務効率化、チームワーク強化、コスト削減、品質向上を実現します。このサービスは、製造業の課題を深く理解し、それに対する最適なデジタルソリューションを提供することで、企業が持続的な成長とイノベーションを達成できるようサポートします。
製造業ニュース解説
製造業、主に購買・調達部門にお勤めの方々に向けた情報を配信しております。
新任の方やベテランの方、管理職を対象とした幅広いコンテンツをご用意しております。
お問い合わせ
コストダウンが利益に直結する術だと理解していても、なかなか前に進めることができない状況。そんな時は、newjiのコストダウン自動化機能で大きく利益貢献しよう!
(β版非公開)