- お役立ち記事
- Fundamentals of Waste Elimination: Capacity-Creation Approach
Fundamentals of Waste Elimination: Capacity-Creation Approach
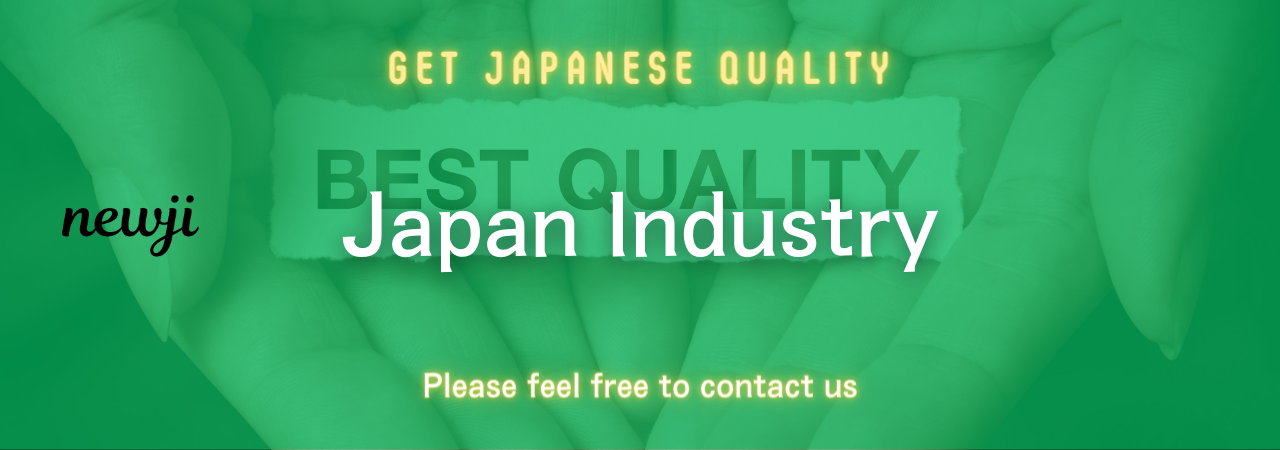
目次
Understanding Waste Elimination
Waste elimination is a crucial aspect of improving efficiency and productivity in any process or organization.
By identifying and removing waste, you can create more capacity for valuable activities.
This approach not only saves resources but also enhances the overall effectiveness of operations.
What is Waste Elimination?
Waste elimination involves recognizing and getting rid of activities that do not add value to the final product or service.
Waste is anything that consumes resources without generating any beneficial outcome.
This could include unnecessary steps in a process, materials that are not utilized, or time wasted.
The goal is to streamline processes to ensure maximum efficiency.
Types of Waste
It’s essential to understand the different types of waste to effectively identify and eliminate them.
Here are the main categories:
1. Overproduction
Producing more than what is needed can lead to excess inventory and wasted resources.
By aligning production with demand, you can minimize overproduction.
2. Waiting
Idle time where workers or machines are waiting is a form of waste.
This can occur due to delays in the supply chain or inefficient scheduling.
Reducing waiting time ensures a smoother, more efficient workflow.
3. Transportation
Unnecessary movement of materials or products can cause delays and increase costs.
Optimizing logistics can help reduce transportation waste.
4. Excess Inventory
Holding more inventory than necessary ties up capital and storage space.
Implementing just-in-time inventory practices can help manage inventory levels effectively.
5. Motion
Unnecessary movements of people or equipment that do not add value to the process are considered waste.
Ergonomic improvements and better workspace layouts can reduce motion waste.
6. Defects
Errors or defects requiring rework consume extra time and resources.
Implementing quality control measures can help minimize defects.
7. Over-Processing
Performing more work than what is required is over-processing.
Streamlining processes and eliminating redundant tasks can reduce this type of waste.
Steps to Eliminate Waste
Now that we understand the types of waste, let’s explore the steps to eliminate them:
1. Identify Waste
The first step is to identify where waste exists in your processes.
Conducting a waste audit can help pinpoint problem areas.
Involve employees in this process as they have firsthand knowledge of the workflow.
2. Analyze Processes
Document and analyze each step of your processes.
Flowcharts and process maps can be useful tools for visualizing workflows.
Look for activities that do not add value and determine the root causes of waste.
3. Implement Changes
Once you’ve identified waste, make changes to eliminate it.
This could involve redesigning processes, investing in new technologies, or retraining staff.
Make sure to communicate changes clearly and provide support during the transition.
4. Monitor Progress
Track the impact of your changes and measure progress.
Use key performance indicators (KPIs) to assess improvements.
Continuous monitoring allows for further adjustments and ensures long-term success.
Benefits of Waste Elimination
Eliminating waste brings numerous benefits to an organization:
1. Increased Efficiency
By removing unnecessary activities, processes become more streamlined and efficient.
This leads to faster production times and improved productivity.
2. Cost Reduction
Reducing waste helps lower operational costs.
Savings can come from reduced material usage, lower storage costs, and less time spent on rework.
3. Improved Quality
Focusing on quality control reduces defects and errors.
High-quality products increase customer satisfaction and loyalty.
4. Enhanced Employee Morale
When processes are efficient, employees experience less frustration and stress.
A well-organized workspace promotes a positive work environment.
5. Better Resource Management
Efficient use of resources helps conserve materials and energy.
This is beneficial for the environment and can improve a company’s sustainability efforts.
Tools for Waste Elimination
There are several tools and methodologies available to assist in waste elimination:
1. Lean Manufacturing
Lean principles focus on creating more value with fewer resources.
Techniques like the 5S methodology (Sort, Set in order, Shine, Standardize, Sustain) help organize and streamline processes.
2. Six Sigma
Six Sigma emphasizes reducing variation and improving quality.
Data-driven analysis helps identify and eliminate defects.
3. Value Stream Mapping
This tool helps visualize the flow of materials and information.
It identifies bottlenecks and areas of waste, providing a clear path for improvement.
Conclusion
Understanding and implementing waste elimination practices can significantly enhance your organization’s capacity and efficiency.
By identifying various types of waste and following a structured approach to eliminate them, you can achieve substantial benefits.
Improved efficiency, cost reduction, and higher quality are just a few of the rewards.
Make use of lean, Six Sigma, and value stream mapping to guide your efforts.
Embrace waste elimination today for a more productive and profitable tomorrow.
資料ダウンロード
QCD調達購買管理クラウド「newji」は、調達購買部門で必要なQCD管理全てを備えた、現場特化型兼クラウド型の今世紀最高の購買管理システムとなります。
ユーザー登録
調達購買業務の効率化だけでなく、システムを導入することで、コスト削減や製品・資材のステータス可視化のほか、属人化していた購買情報の共有化による内部不正防止や統制にも役立ちます。
NEWJI DX
製造業に特化したデジタルトランスフォーメーション(DX)の実現を目指す請負開発型のコンサルティングサービスです。AI、iPaaS、および先端の技術を駆使して、製造プロセスの効率化、業務効率化、チームワーク強化、コスト削減、品質向上を実現します。このサービスは、製造業の課題を深く理解し、それに対する最適なデジタルソリューションを提供することで、企業が持続的な成長とイノベーションを達成できるようサポートします。
オンライン講座
製造業、主に購買・調達部門にお勤めの方々に向けた情報を配信しております。
新任の方やベテランの方、管理職を対象とした幅広いコンテンツをご用意しております。
お問い合わせ
コストダウンが利益に直結する術だと理解していても、なかなか前に進めることができない状況。そんな時は、newjiのコストダウン自動化機能で大きく利益貢献しよう!
(Β版非公開)