- お役立ち記事
- Fundamentals of welding technology, causes of cracking and deformation, and countermeasure points
月間77,185名の
製造業ご担当者様が閲覧しています*
*2025年2月28日現在のGoogle Analyticsのデータより
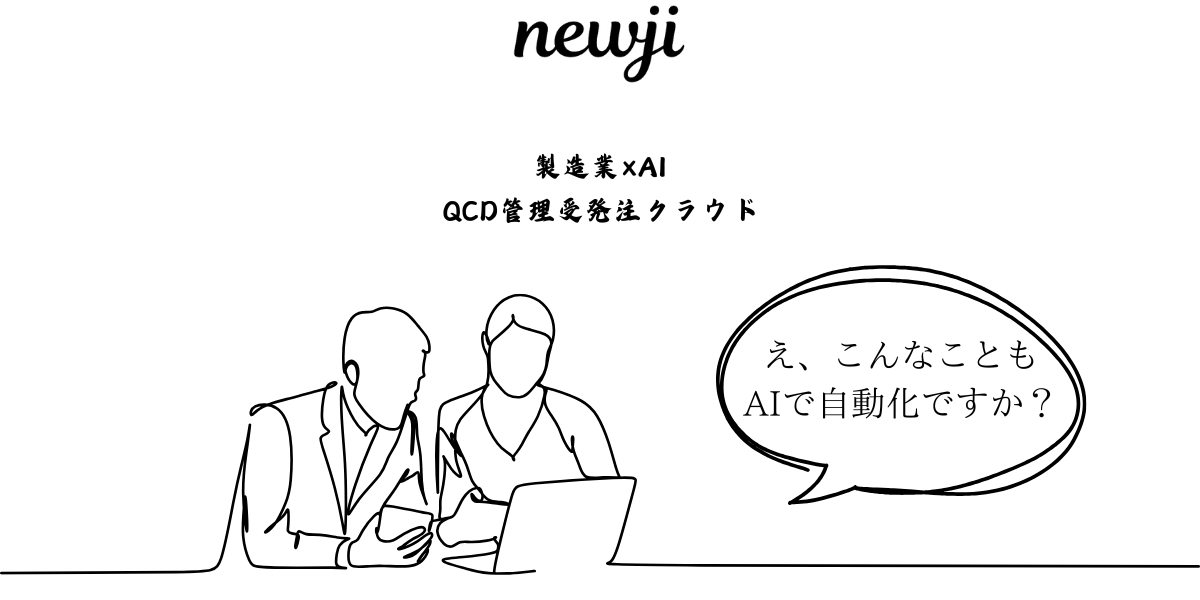
Fundamentals of welding technology, causes of cracking and deformation, and countermeasure points
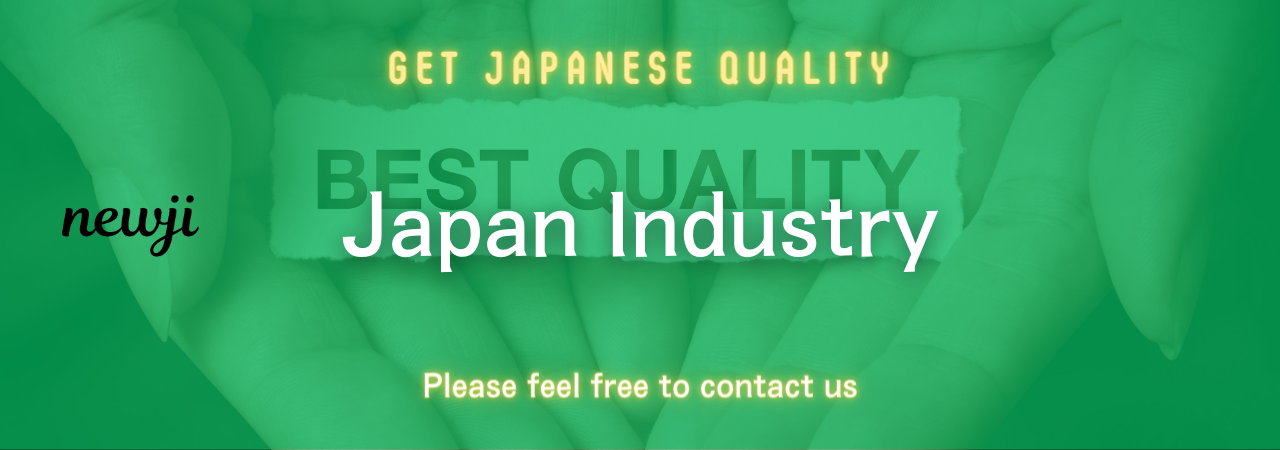
目次
Understanding Welding Technology
Welding technology is a critical process in various industries, from construction to automotive, shipbuilding to aerospace.
It involves joining two or more pieces of metal, or thermoplastics, to form a single, coherent unit.
The process is achieved through the application of heat, pressure, or both, to melt the materials at the joining point and then allowing them to cool and fuse together.
Understanding the fundamentals of welding technology is essential for ensuring strong, durable, and reliable welds.
Types of Welding Techniques
There are several welding techniques, each suited for specific applications and material types.
Some of the most common techniques include:
– **Arc Welding**: This method uses an electric arc to melt the base material and the filler material, usually a welding rod.
– **MIG (Metal Inert Gas) Welding**: Uses a continuous solid wire electrode fed through a welding gun.
– **TIG (Tungsten Inert Gas) Welding**: Utilizes a non-consumable tungsten electrode to produce the weld.
– **Spot Welding**: A resistance welding method primarily used for joining sheet metal.
Each method has its advantages and limitations, making the selection of the welding technique a critical decision in the fabrication process.
Causes of Cracking in Welds
Cracks in welding are one of the most common and severe defects that can occur.
Understanding the causes of cracking is essential for preventing weld failure and maintaining structural integrity.
Hot Cracking
Hot cracks occur at high temperatures, typically above 1000°C, as the welded joint cools from its molten state.
These cracks appear in the weld metal or in the heat-affected zone next to the weld.
They are often caused by the solidification of low melting point alloys or impurities.
Cold Cracking
Cold cracking, also known as hydrogen-induced cracking, occurs after the weld has cooled.
It’s usually associated with hydrogen trapped in the weld metal, which interacts with the metal at lower temperatures.
Other contributing factors include residual stress, hardness of the weld, and the presence of brittle microstructures.
Lamellar Tearing
This type of cracking typically occurs in the base metal, parallel to the weld fusion boundary.
Lamellar tearing is often associated with the presence of non-metallic inclusions within the metal or due to inappropriate loading conditions.
Deformation in Welding
Welding deformation refers to the unexpected changes or distortions that can occur in the shape or dimensions of a welded component.
This deformation can significantly impact the component’s functionality and aesthetic appearance.
Causes of Welding Deformation
Deformation occurs due to the uneven distribution of thermal expansion and contraction during the welding process.
Several factors contribute to this phenomenon:
– **Welding Sequence**: Unplanned or improper welding sequence can result in significant deformation.
– **Excessive Heat Input**: More heat than necessary can cause expansion and contraction that leads to warping or distortion.
– **Residual Stress**: Stresses locked into the welded material as it cools can cause bending or twisting.
Countermeasures to Prevent Defects and Deformation
While welding defects and deformation pose challenges, several strategies can minimize their occurrence:
Proper Material Selection
Choose materials with appropriate mechanical properties and minimal impurities to reduce the risk of defects.
Using materials with similar coefficients of thermal expansion when welding different metals can also help minimize distortion.
Control of Welding Parameters
Controlling the heat input by adjusting the welding parameters such as voltage, amperage, and travel speed can prevent overheating and reduce residual stress.
A balanced approach to heat distribution helps control distortion.
Preheating and Post-Weld Heat Treatment
Preheating the material before welding can lower the cooling rate, reduce residual stress, and prevent cold cracking.
Post-weld heat treatment can relieve residual stresses, improve ductility, and ensure a more stable metal microstructure.
Sequencing and Fixturing
Using proper welding sequences, including intermittent welding or back-step techniques, can distribute stress more evenly across the weld area.
Fixtures and jigs can help hold components in place, minimizing movement and distortion during welding.
Monitoring and Inspection
Conducting regular inspections and using non-destructive testing methods such as ultrasonic or radiographic testing can help identify defects early.
This allows for timely corrections before significant issues arise.
Conclusion
Welding technology is a complex process crucial for many structural applications.
Understanding the fundamental aspects of welding techniques, the causes of common defects like cracking and deformation, and the countermeasures to mitigate these issues is essential for any welder or engineer.
By employing proper techniques, consistent monitoring, and maintaining a thorough understanding of material behavior, defects can be minimized, resulting in stronger, more reliable welded structures.
資料ダウンロード
QCD管理受発注クラウド「newji」は、受発注部門で必要なQCD管理全てを備えた、現場特化型兼クラウド型の今世紀最高の受発注管理システムとなります。
ユーザー登録
受発注業務の効率化だけでなく、システムを導入することで、コスト削減や製品・資材のステータス可視化のほか、属人化していた受発注情報の共有化による内部不正防止や統制にも役立ちます。
NEWJI DX
製造業に特化したデジタルトランスフォーメーション(DX)の実現を目指す請負開発型のコンサルティングサービスです。AI、iPaaS、および先端の技術を駆使して、製造プロセスの効率化、業務効率化、チームワーク強化、コスト削減、品質向上を実現します。このサービスは、製造業の課題を深く理解し、それに対する最適なデジタルソリューションを提供することで、企業が持続的な成長とイノベーションを達成できるようサポートします。
製造業ニュース解説
製造業、主に購買・調達部門にお勤めの方々に向けた情報を配信しております。
新任の方やベテランの方、管理職を対象とした幅広いコンテンツをご用意しております。
お問い合わせ
コストダウンが利益に直結する術だと理解していても、なかなか前に進めることができない状況。そんな時は、newjiのコストダウン自動化機能で大きく利益貢献しよう!
(β版非公開)