- お役立ち記事
- Fundamentals, points to note, and troubleshooting of film-forming technology using vacuum evaporation, sputtering, and CVD
月間76,176名の
製造業ご担当者様が閲覧しています*
*2025年3月31日現在のGoogle Analyticsのデータより
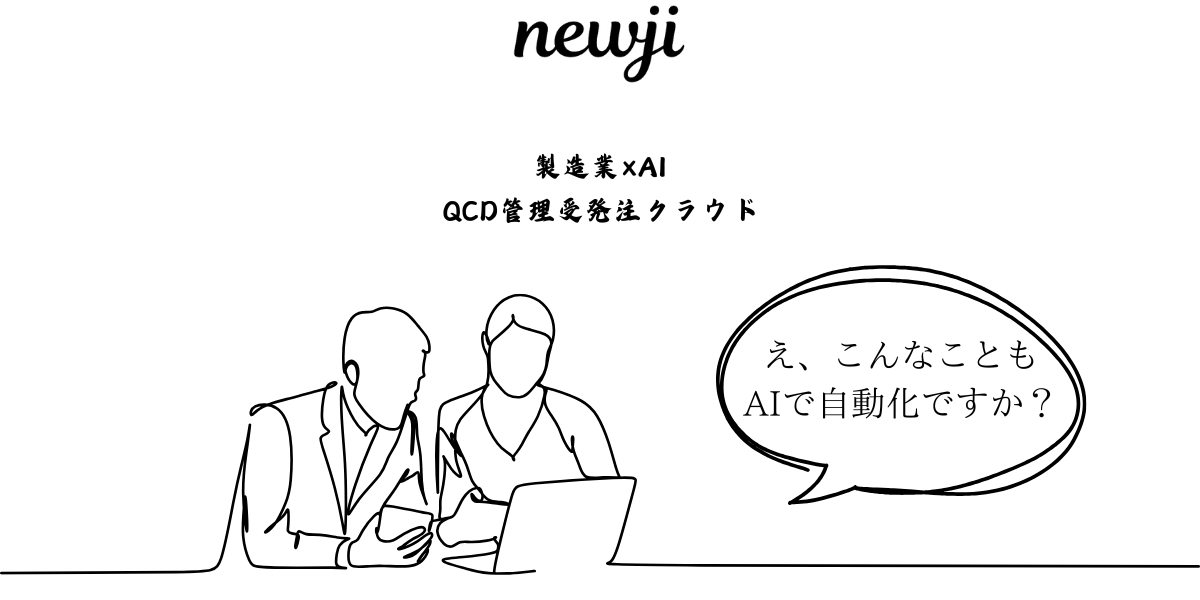
Fundamentals, points to note, and troubleshooting of film-forming technology using vacuum evaporation, sputtering, and CVD
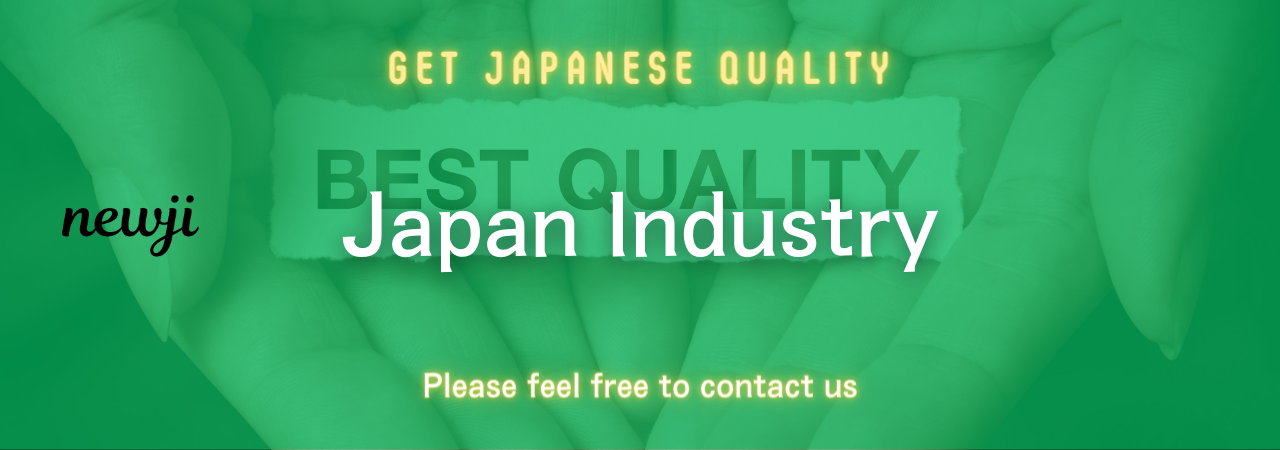
目次
Understanding Film-Forming Technology
Film-forming technology is an essential part of fabricating modern electronic devices, optoelectronic components, and various other industrial applications.
It involves the deposition of thin films onto substrates, allowing for the creation of functional layers with specific properties.
The three primary techniques used for this purpose are vacuum evaporation, sputtering, and chemical vapor deposition (CVD).
Each method has unique principles, advantages, and limitations that need to be understood for effective application.
Vacuum Evaporation
Vacuum evaporation is one of the simplest and oldest techniques used for thin film deposition.
In this method, the material to be deposited is vaporized in a vacuum environment and then condensed onto a substrate, forming a thin film.
One of the major advantages of vacuum evaporation is the high purity of films obtained.
Since the process is conducted in a high vacuum, contamination from the air is minimized.
This method is particularly useful for depositing metals and certain compounds on substrates that are sensitive to high temperatures.
However, there are some challenges associated with vacuum evaporation.
The method is largely line-of-sight, meaning it struggles with uniform coating on complex geometries.
Furthermore, maintaining a stable evaporation rate and achieving a uniform thickness can be difficult.
Sputtering
Sputtering is a versatile film-forming technique that involves bombarding a target material with high-energy particles, typically ions, causing the target atoms to be ejected and deposited onto a substrate.
This process can be used to deposit a wide range of materials, including metals, insulators, and alloys.
One of the key advantages of sputtering is its ability to produce highly uniform and adherent films, even on substrates with complex shapes.
It also offers better control over the film thickness and composition, making it suitable for applications in microelectronics and semiconductors.
However, sputtering does have its limitations.
The process can be relatively slow and energy-intensive, and the equipment required is often more complex and costly compared to simpler techniques.
Chemical Vapor Deposition (CVD)
Chemical vapor deposition (CVD) is a widely used technique for depositing thin films through chemical reactions of gaseous precursors on a substrate surface.
CVD is highly versatile and can be used to produce various materials, including metals, oxides, nitrides, and carbides.
A significant advantage of CVD is its ability to produce high-quality films with excellent uniformity and conformity over large areas and complex shapes.
The process temperature and pressure can be adjusted to tailor the film properties, making CVD suitable for depositing materials onto thermally sensitive substrates.
Despite its benefits, CVD can present some challenges.
The process typically requires precise control over reaction conditions and the handling of hazardous gaseous precursors.
Moreover, quality management can be difficult, as unwanted parasitic reactions may occur, affecting the film’s composition.
Points to Note
Each film-forming technique has its own set of considerations that must be accounted for to achieve successful deposition.
– **Material Compatibility**: Choosing the right deposition method depends on the substrate material and the desired film properties.
For example, thermally unstable substrates may not be suitable for high-temperature processes.
– **Adhesion and Thickness**: Ensuring good adhesion between the film and substrate is crucial.
Adjusting parameters like temperature, pressure, and time can help achieve the desired thickness without compromising film integrity.
– **Uniformity and Coverage**: For applications where uniformity is critical, such as in semiconductors, careful control over deposition parameters is necessary.
This is particularly important with line-of-sight techniques like vacuum evaporation.
Troubleshooting Common Issues
Despite the precision of modern techniques, issues can arise during thin film deposition.
Here are some common problems and solutions:
– **Inadequate Adhesion**: Surface preparation is critical.
Ensure the substrate is clean and pre-treated to improve film adhesion.
– **Non-Uniform Film Thickness**: Adjust the deposition parameters, such as source placement and substrate movement, to achieve more consistent thickness.
– **Contamination**: Maintaining a clean processing environment and using high-purity source materials help to minimize contamination.
– **Cracking or Delamination**: This may result from thermal expansion mismatches.
Gradual cooling and optimization of deposition conditions can help mitigate these issues.
Conclusion
Film-forming technology using vacuum evaporation, sputtering, and CVD is essential for numerous industrial applications.
Each technique has its unique strengths and challenges.
Understanding the fundamental principles behind these methods allows for better choice and application, helping avoid common issues, and optimizing film quality.
Whether producing microelectronic components or functional coatings, proper knowledge and troubleshooting can significantly enhance performance and reliability.
資料ダウンロード
QCD管理受発注クラウド「newji」は、受発注部門で必要なQCD管理全てを備えた、現場特化型兼クラウド型の今世紀最高の受発注管理システムとなります。
ユーザー登録
受発注業務の効率化だけでなく、システムを導入することで、コスト削減や製品・資材のステータス可視化のほか、属人化していた受発注情報の共有化による内部不正防止や統制にも役立ちます。
NEWJI DX
製造業に特化したデジタルトランスフォーメーション(DX)の実現を目指す請負開発型のコンサルティングサービスです。AI、iPaaS、および先端の技術を駆使して、製造プロセスの効率化、業務効率化、チームワーク強化、コスト削減、品質向上を実現します。このサービスは、製造業の課題を深く理解し、それに対する最適なデジタルソリューションを提供することで、企業が持続的な成長とイノベーションを達成できるようサポートします。
製造業ニュース解説
製造業、主に購買・調達部門にお勤めの方々に向けた情報を配信しております。
新任の方やベテランの方、管理職を対象とした幅広いコンテンツをご用意しております。
お問い合わせ
コストダウンが利益に直結する術だと理解していても、なかなか前に進めることができない状況。そんな時は、newjiのコストダウン自動化機能で大きく利益貢献しよう!
(β版非公開)