- お役立ち記事
- G-line, I-line, KrF, ArF, ArF immersion, EUV lithography technology and evaluation
G-line, I-line, KrF, ArF, ArF immersion, EUV lithography technology and evaluation
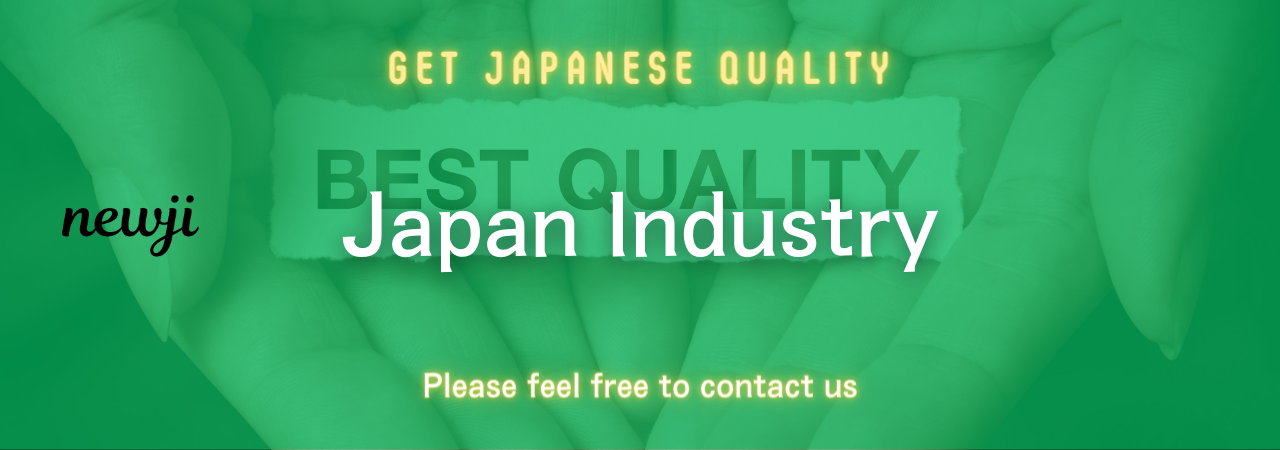
目次
Introduction to Lithography Technology
Lithography technology plays a crucial role in the manufacturing of semiconductor devices.
It involves the transfer of complex circuit patterns onto silicon wafers to build integrated circuits.
This process has evolved significantly over the years, developing various methods to meet the ever-growing demand for smaller, faster, and more efficient microchips.
Among these methods, G-line, I-line, KrF, ArF, ArF immersion, and EUV lithography are prominent techniques employed in the semiconductor industry.
Understanding G-line Lithography
G-line lithography refers to the use of near-ultraviolet (UV) light with a wavelength of approximately 436 nanometers.
It was one of the earliest methods utilized in the photolithography process for semiconductor manufacturing.
G-line lithography paved the way for the miniaturization of devices, allowing manufacturers to produce smaller transistors with improved performance.
Although considered somewhat outdated today due to newer technologies, G-line lithography still finds application in some areas.
It is mainly used for less demanding layers in semiconductor fabrication where the resolution requirement is not as high.
Introduction to I-line Lithography
Following the G-line, I-line lithography emerged with a shorter wavelength of about 365 nanometers.
I-line lithography enhanced the resolution and pattern fidelity, making it suitable for more advanced circuit patterns.
The shorter wavelength allowed manufacturers to create finer features, which contributed to the production of more compact and efficient microchips.
I-line technology is often employed alongside G-line lithography, especially in scenarios where improved precision is necessary without the complexity and cost of more advanced systems.
The Rise of KrF Lithography
The transition to KrF lithography marked a significant leap in technology, utilizing deep ultraviolet (DUV) light with a wavelength of around 248 nanometers.
KrF lithography substantially increased resolution capabilities, enabling the production of more complex semiconductor architectures.
This technology became a game-changer for the industry, as it allowed for the mass production of highly integrated circuits.
It played a pivotal role in the rapid advancement of electronics, contributing to the miniaturization and increased functionality of devices.
Advancements with ArF Lithography
ArF lithography further pushed the boundaries with its use of a 193-nanometer wavelength.
This improvement allowed for even smaller feature sizes on semiconductor wafers, accommodating the increasing demand for powerful and energy-efficient chips.
ArF lithography opened doors to new possibilities by supporting the fabrication of intricate designs required for modern microprocessors and memory chips.
Its higher resolution compared to KrF lithography made it the preferred choice for critical layers where precision is paramount.
The Introduction of ArF Immersion Lithography
To achieve even finer patterning, ArF immersion lithography was developed as an enhancement over standard ArF lithography.
By introducing a liquid medium between the lens and the wafer, immersion lithography effectively increased the numerical aperture, allowing for better focus and resolution.
This technique enabled the production of even smaller features, further pushing the limits of semiconductor device miniaturization.
ArF immersion lithography remains a widely-used approach for advanced node technologies, facilitating the creation of high-density, multi-functional chips.
The Era of EUV Lithography
Extreme Ultraviolet (EUV) lithography represents the most cutting-edge technological advancement in the semiconductor industry.
Operating at a wavelength of just 13.5 nanometers, EUV lithography offers unparalleled resolution, allowing for the fabrication of features at the nanometer scale with remarkable precision.
EUV technology is essential for the production of the latest generation of microchips, supporting the demand for smaller, faster, and more efficient electronic devices.
Despite its complexity and the challenges in development and implementation, EUV lithography is set to become the standard for the semiconductor industry in the coming years.
Comparing Lithography Technologies
Each lithography technology, from G-line to EUV, has its strengths and context of use.
G-line and I-line technologies are often favored for their simplicity and cost-effectiveness for less demanding layers.
KrF lithography provides a balance of higher resolution and efficiency, making it suitable for a wide range of applications.
ArF and ArF immersion lithographies offer more precise patterning, essential for advanced processors and memory devices.
EUV lithography, with its exceptional resolution and potential for next-generation devices, stands at the forefront, despite facing challenges related to cost and implementation.
Evaluating Lithography Performance
Evaluating the performance of lithography technologies involves multiple factors, including resolution, cost, complexity, and throughput.
Resolution is significant, as it dictates the minimum feature size that can be reliably fabricated, directly impacting device performance and density.
Cost considerations also play a crucial role, as advanced systems like EUV tend to be more expensive to develop and maintain, potentially affecting production budgets.
Additionally, throughput—the number of wafers processed per unit time—directly influences manufacturing efficiency and enterprise profitability.
Complexity encompasses the technical challenges associated with operating and maintaining the lithography equipment.
For instance, EUV systems require a precise vacuum environment and specialized components, adding layers of complexity to their operation.
The Future of Lithography Technology
Looking ahead, continued innovation is expected to address the challenges posed by advanced lithography technologies.
The industry will likely focus on increasing the efficiency and reducing the costs associated with EUV lithography.
R&D efforts will also explore alternative approaches and enhancements to further push the boundaries of what is achievable in semiconductor fabrication.
As the demand for more powerful and compact electronic devices grows, the evolution of lithography technology will remain a cornerstone in meeting industry expectations.
In conclusion, lithography techniques like G-line, I-line, KrF, ArF, ArF immersion, and EUV have each contributed significantly to the advancement of semiconductor manufacturing.
Their development has been pivotal in enabling the continued progression of technology, underlining the essential role of lithography in the modern world.
資料ダウンロード
QCD調達購買管理クラウド「newji」は、調達購買部門で必要なQCD管理全てを備えた、現場特化型兼クラウド型の今世紀最高の購買管理システムとなります。
ユーザー登録
調達購買業務の効率化だけでなく、システムを導入することで、コスト削減や製品・資材のステータス可視化のほか、属人化していた購買情報の共有化による内部不正防止や統制にも役立ちます。
NEWJI DX
製造業に特化したデジタルトランスフォーメーション(DX)の実現を目指す請負開発型のコンサルティングサービスです。AI、iPaaS、および先端の技術を駆使して、製造プロセスの効率化、業務効率化、チームワーク強化、コスト削減、品質向上を実現します。このサービスは、製造業の課題を深く理解し、それに対する最適なデジタルソリューションを提供することで、企業が持続的な成長とイノベーションを達成できるようサポートします。
オンライン講座
製造業、主に購買・調達部門にお勤めの方々に向けた情報を配信しております。
新任の方やベテランの方、管理職を対象とした幅広いコンテンツをご用意しております。
お問い合わせ
コストダウンが利益に直結する術だと理解していても、なかなか前に進めることができない状況。そんな時は、newjiのコストダウン自動化機能で大きく利益貢献しよう!
(Β版非公開)