- お役立ち記事
- Galvanometer Characteristics and Their Use in Manufacturing
Galvanometer Characteristics and Their Use in Manufacturing
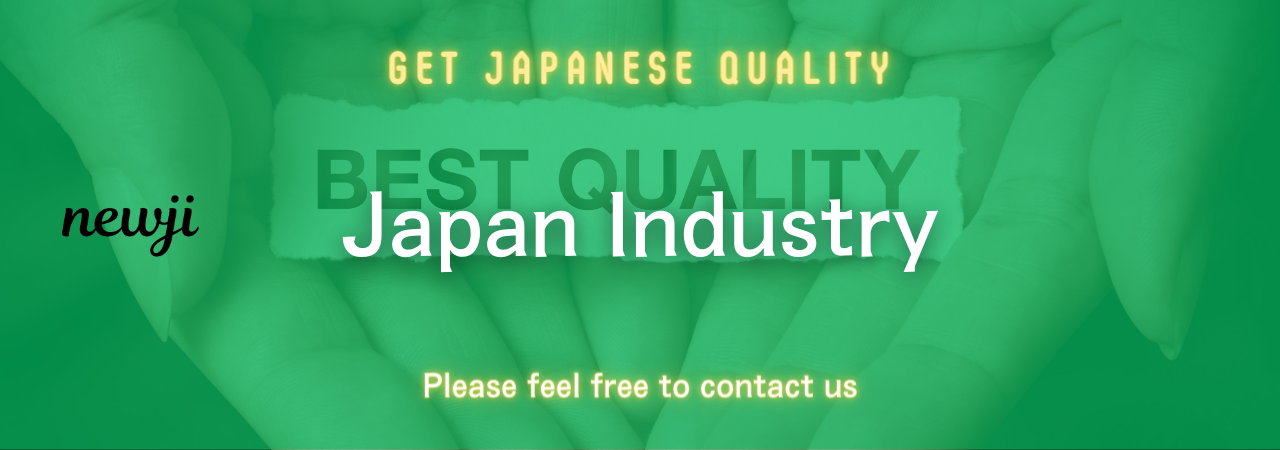
Galvanometers are devices used to detect and measure electric current.
They work by using a moving coil or a moving magnet that interacts with a magnetic field.
This interaction causes a needle or pointer to move, indicating the presence and magnitude of the current.
目次
Understanding Galvanometer Characteristics
Sensitivity
Sensitivity is one of the most important characteristics of a galvanometer.
It refers to the smallest current that can be detected by the device.
A high-sensitivity galvanometer can detect very small currents, making it valuable in precision measurement tasks.
The sensitivity is determined by various factors, including the number of turns in the coil, the strength of the magnetic field, and the resistance of the moving coil.
Resistance
The resistance of a galvanometer is another crucial characteristic.
This is typically the internal resistance of the coil through which the current passes.
Low resistance in the coil is often desirable for high-sensitivity measurements.
However, for accurate readings, the resistance must be carefully balanced with the measuring circuit’s total resistance.
Torque and Damping
Torque refers to the rotational force that moves the needle.
The torque is generated by the interaction between the electric current and the magnetic field.
Higher torque results in faster needle movement.
Damping, on the other hand, is the process that prevents the needle from oscillating once it reaches the correct position.
Good damping ensures that the needle quickly comes to rest without excessive oscillation, providing a stable reading.
Types of Galvanometers
Moving Coil Galvanometer
The moving coil type is the most common form of galvanometer.
It consists of a coil of wire that moves in a magnetic field.
When an electric current passes through the coil, it experiences a torque that causes it to move.
This movement is proportional to the current, allowing for accurate measurement.
Moving Magnet Galvanometer
In a moving magnet galvanometer, the magnet moves instead of the coil.
The magnet is suspended within a coil of wire, and when current flows through the coil, the magnetic field generated interacts with the magnet.
The resulting movement of the magnet is used to measure the current.
This type is often used in devices where durable and long-term measurement accuracy is required.
Applications in Manufacturing
Quality Control
Galvanometers are extensively used in manufacturing for quality control purposes.
They help in detecting small electrical currents that may indicate issues in the manufacturing process.
For instance, in the production of electronic components, galvanometers can be used to ensure that circuits are functioning correctly by measuring the current flow through them.
If the measured current deviates from the expected value, it can signal a defect, allowing for timely corrections.
Calibration of Instruments
In manufacturing environments, precision instruments must be regularly calibrated to maintain their accuracy.
Galvanometers play a vital role in this calibration process.
By accurately measuring small currents, they help ensure that instruments such as ammeters and voltmeters provide accurate readings.
This calibration is crucial for maintaining the quality and reliability of the products being manufactured.
Automated Testing
Automation in manufacturing has reached a level where entire testing procedures can be automated.
Galvanometers are integrated into automated testing systems to monitor electric currents and detect anomalies.
These systems can quickly and efficiently test large quantities of products, ensuring that they meet the required standards.
This integration significantly reduces human error and increases the throughput of the manufacturing process.
Feedback Systems
In advanced manufacturing systems, feedback loops are used to maintain optimal conditions.
Galvanometers are used in these feedback systems to monitor current flow and adjust processes as needed.
For instance, in robotic assembly lines, galvanometers help in ensuring that the electrical signals controlling the robots are within the desired range.
If any deviations are detected, the system can automatically make necessary adjustments, maintaining the efficiency and accuracy of the production process.
Advantages of Using Galvanometers in Manufacturing
High Accuracy
One of the primary advantages of using galvanometers in manufacturing is their high accuracy.
They can detect even the smallest currents, making them invaluable for precision tasks.
This high level of accuracy ensures that even minor defects in the manufacturing process are identified and corrected promptly.
Real-Time Monitoring
Galvanometers provide real-time monitoring of currents, which is essential in dynamic manufacturing environments.
This real-time feedback allows for immediate detections of issues, reducing downtime and increasing overall efficiency.
Real-time monitoring also helps in maintaining the consistency and quality of the products being manufactured.
Cost-Effective
Using galvanometers in manufacturing can be cost-effective in the long run.
By identifying defects early in the production process, they help in reducing waste and minimizing rework.
Moreover, their integration into automated systems reduces the need for manual inspections, lowering labor costs and increasing productivity.
Conclusion
Galvanometers are essential tools in the field of manufacturing, providing high accuracy, real-time monitoring, and cost-effective solutions.
Understanding their characteristics, such as sensitivity, resistance, and damping, helps in selecting the right type for specific applications.
Whether ensuring quality control, calibrating instruments, or integrating into automated systems, galvanometers play a crucial role in maintaining the efficiency and quality of modern manufacturing processes.
資料ダウンロード
QCD調達購買管理クラウド「newji」は、調達購買部門で必要なQCD管理全てを備えた、現場特化型兼クラウド型の今世紀最高の購買管理システムとなります。
ユーザー登録
調達購買業務の効率化だけでなく、システムを導入することで、コスト削減や製品・資材のステータス可視化のほか、属人化していた購買情報の共有化による内部不正防止や統制にも役立ちます。
NEWJI DX
製造業に特化したデジタルトランスフォーメーション(DX)の実現を目指す請負開発型のコンサルティングサービスです。AI、iPaaS、および先端の技術を駆使して、製造プロセスの効率化、業務効率化、チームワーク強化、コスト削減、品質向上を実現します。このサービスは、製造業の課題を深く理解し、それに対する最適なデジタルソリューションを提供することで、企業が持続的な成長とイノベーションを達成できるようサポートします。
オンライン講座
製造業、主に購買・調達部門にお勤めの方々に向けた情報を配信しております。
新任の方やベテランの方、管理職を対象とした幅広いコンテンツをご用意しております。
お問い合わせ
コストダウンが利益に直結する術だと理解していても、なかなか前に進めることができない状況。そんな時は、newjiのコストダウン自動化機能で大きく利益貢献しよう!
(Β版非公開)