- お役立ち記事
- Garbage Bag Manufacturing Process and Durability Improvement
Garbage Bag Manufacturing Process and Durability Improvement
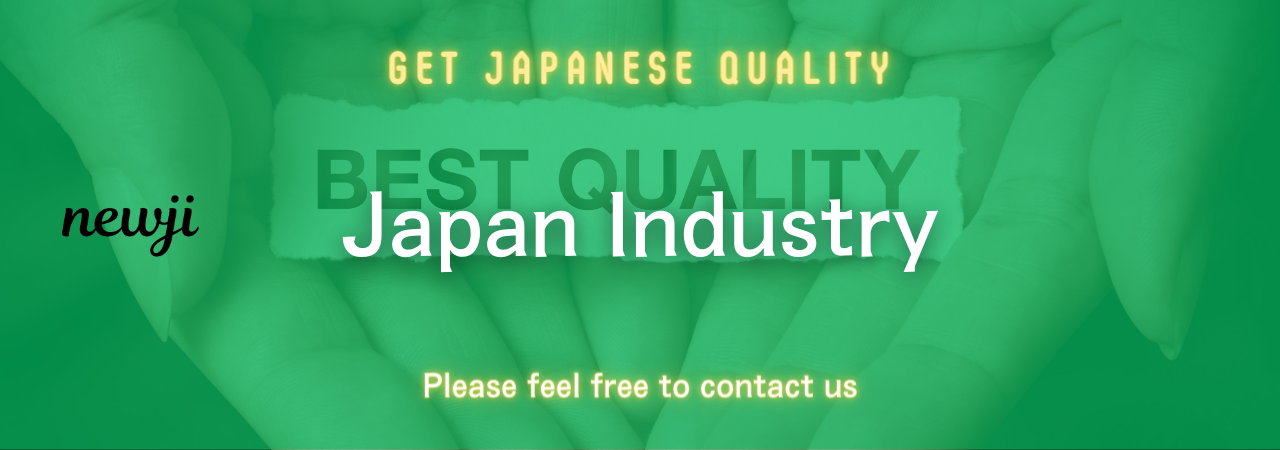
目次
Introduction to Garbage Bag Manufacturing
Garbage bags, an essential item in households and industries, go through a fascinating manufacturing process before they reach consumers.
These bags, often called trash bags or bin liners, are designed to hold waste securely and prevent leaks and odors.
Understanding the garbage bag manufacturing process can provide insight into how durability is enhanced to meet varying consumer needs.
The Initial Stage: Material Selection
The manufacturing process begins with the selection of raw materials.
Garbage bags are primarily made from polyethylene, a versatile type of plastic.
There are two main types of polyethylene used: low-density polyethylene (LDPE) and high-density polyethylene (HDPE).
LDPE is known for its flexibility and strength, making it suitable for heavy-duty bags.
On the other hand, HDPE is more rigid and cost-effective, often used for lightweight bags.
Manufacturers choose the type based on the intended use of the garbage bags, balancing factors such as strength, cost, and environmental impact.
Additives for Enhanced Durability
To improve durability, manufacturers may add various additives to the polyethylene during production.
For instance, anti-tear compounds can be added to make the bags more resistant to punctures and tearing.
Additionally, some garbage bags include colorants for aesthetic purposes or to differentiate types, such as recycling bags.
Additives like ultraviolet stabilizers protect the bags from degrading when exposed to sunlight, extending the lifespan of outdoor waste bags.
Extrusion: Forming the Bag Material
Once the raw materials and additives are prepared, the next step is extrusion, a process that transforms these components into thin sheets of plastic.
The polyethylene mixture is first heated to its melting point and then forced through a die – a specialized tool that shapes the material.
The extruded plastic emerges as a continuous sheet that is then rapidly cooled using a series of rollers.
This cooling process solidifies the plastic and helps achieve the desired thickness and texture.
Blown Film Process
Some manufacturers employ the blown film extrusion process to form the bag film.
In this method, the molten plastic is extruded into a large bubble, which is continuously inflated and stretched until it reaches the required thickness.
The inflated bubble is then collapsed, flattened, and cut into rolls of film.
This technique provides superior strength and uniform thickness, contributing to the overall durability of the garbage bags.
Bag Formation and Sealing
With the plastic film ready, the next phase involves forming the garbage bags to their specific shape and size.
Cutting and Folding
The continuous rolls of film are unwound and fed into a cutting machine, where they are cut to the desired bag length.
The cut sheets are often folded to accommodate gussets – fold indentations that increase the bag’s capacity and strength.
Sealing Techniques
Once cut and folded, the bag’s edges need to be sealed to prevent leaks and ensure durability.
There are various sealing methods employed, including heat sealing, a popular method due to its effectiveness in creating airtight seals.
In heat sealing, heated bars press the edges, melting and bonding them together.
Alternatively, manufacturers might use ultrasonic sealing, which uses high-frequency vibrations to fuse the material.
Quality Control and Testing
Durability is a key consideration in garbage bag manufacturing, and rigorous quality control measures are in place to ensure high standards.
Puncture and Tear Testing
After sealing, bags undergo puncture and tear resistance tests.
These tests simulate harsh conditions where bags may come in contact with sharp objects or heavy loads.
Passing these tests assures consumers that the garbage bags can withstand regular use.
Thickness Measurements
The thickness of garbage bags is a critical factor in their durability.
To ensure consistency, manufacturers perform thickness checks using precise instruments.
This ensures that every batch meets specified requirements, maintaining product integrity.
Durability Improvements in Modern Garbage Bags
Over the years, manufacturers have continuously innovated to create more durable garbage bags.
Advanced Material Blending
The modern garbage bag often features a blend of LDPE and HDPE plastics.
This technique combines the strengths of both materials: the flexibility and tear-resistance of LDPE with the rigidity and cost-saving benefits of HDPE.
This blending enhances durability while maintaining cost efficiency.
Reinforced Handles and Ties
Improvements in bag designs have led to the introduction of reinforced handles and ties.
Bags with strong, built-in ties or handles make it easier to carry heavy loads without tearing.
These features are particularly beneficial for industrial use, where the bags are subjected to rough handling.
Environmental Considerations
While ensuring durability, the environmental impact of garbage bags is a significant concern.
Manufacturers are increasingly focusing on creating eco-friendly options by using recycled materials and developing biodegradable alternatives.
Biodegradable bags break down into harmless substances over time, reducing landfill waste.
Moreover, by utilizing post-consumer plastics, companies decrease the demand for virgin material, ultimately contributing to sustainability.
Conclusion
The manufacturing process of garbage bags is detailed and tailored to enhance durability and functionality.
From the careful selection of raw materials to the implementation of advanced technologies and stringent quality controls, each step is essential in producing reliable waste management solutions.
As sustainability becomes a growing priority, future innovations will likely continue to prioritize eco-friendly practices while maintaining the strength and reliability that consumers expect.
資料ダウンロード
QCD調達購買管理クラウド「newji」は、調達購買部門で必要なQCD管理全てを備えた、現場特化型兼クラウド型の今世紀最高の購買管理システムとなります。
ユーザー登録
調達購買業務の効率化だけでなく、システムを導入することで、コスト削減や製品・資材のステータス可視化のほか、属人化していた購買情報の共有化による内部不正防止や統制にも役立ちます。
NEWJI DX
製造業に特化したデジタルトランスフォーメーション(DX)の実現を目指す請負開発型のコンサルティングサービスです。AI、iPaaS、および先端の技術を駆使して、製造プロセスの効率化、業務効率化、チームワーク強化、コスト削減、品質向上を実現します。このサービスは、製造業の課題を深く理解し、それに対する最適なデジタルソリューションを提供することで、企業が持続的な成長とイノベーションを達成できるようサポートします。
オンライン講座
製造業、主に購買・調達部門にお勤めの方々に向けた情報を配信しております。
新任の方やベテランの方、管理職を対象とした幅広いコンテンツをご用意しております。
お問い合わせ
コストダウンが利益に直結する術だと理解していても、なかなか前に進めることができない状況。そんな時は、newjiのコストダウン自動化機能で大きく利益貢献しよう!
(Β版非公開)