- お役立ち記事
- Gas Assist Molding Technology and Its Advantages in OEM Manufacturing
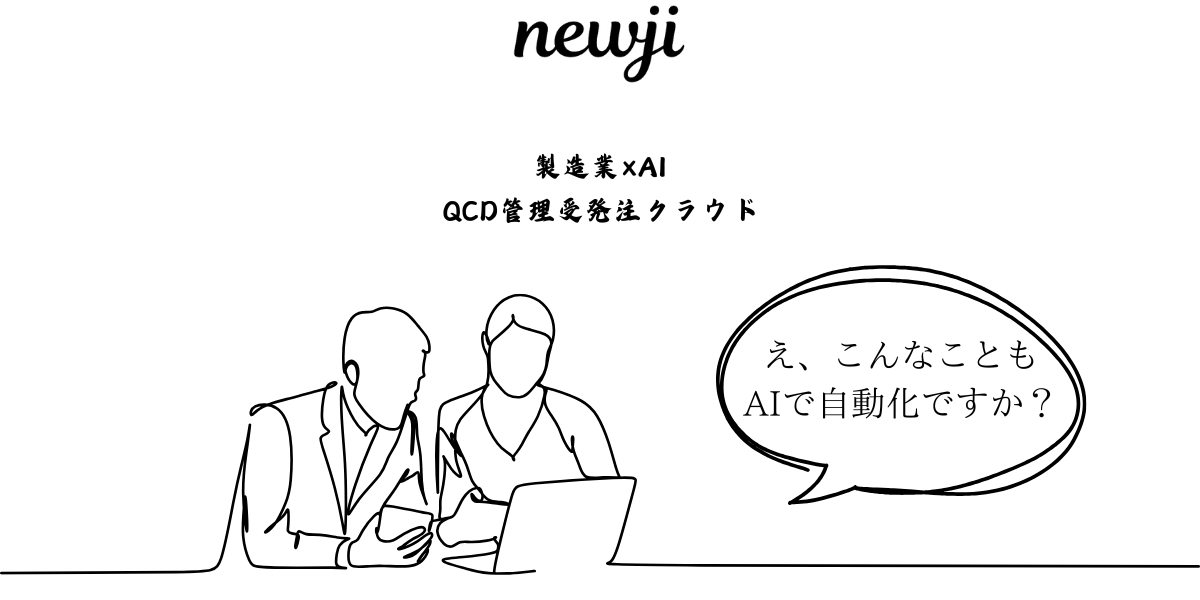
Gas Assist Molding Technology and Its Advantages in OEM Manufacturing
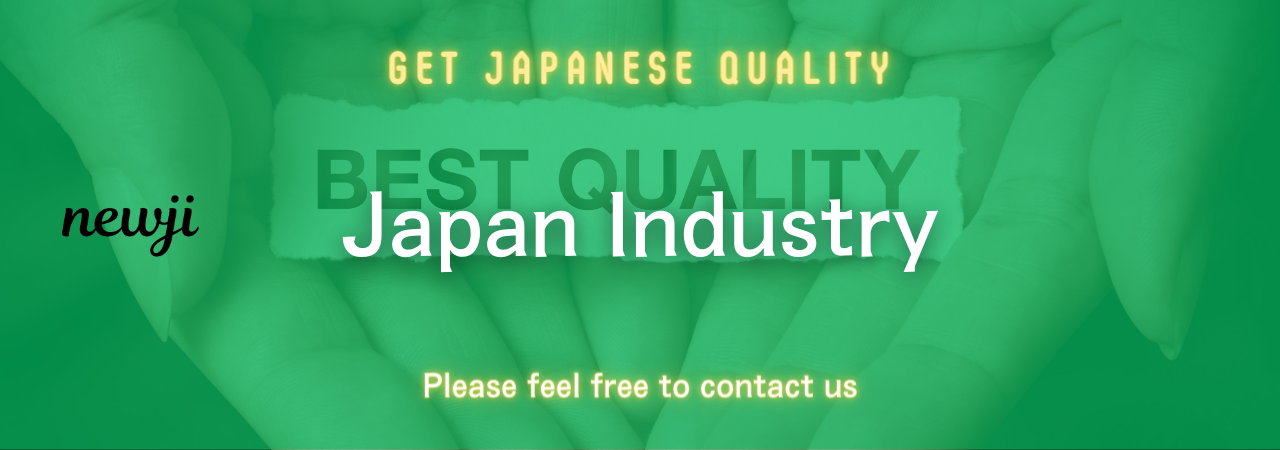
Gas assist molding technology has emerged as a revolutionary process in the field of OEM (Original Equipment Manufacturer) manufacturing. This innovative technique offers numerous advantages over traditional molding processes. In this article, we will explore what gas assist molding technology is, how it works, and the various benefits it provides in OEM manufacturing.
目次
What is Gas Assist Molding Technology?
Gas assist molding is an advanced injection molding process that uses gas to assist in the formation of plastic parts. During this process, a controlled amount of gas, typically nitrogen, is injected into the molten plastic within the mold. The gas creates hollow sections in the part, reducing the amount of material needed without compromising structural integrity.
How It Works
The gas assist molding process begins with the injection of molten plastic into a mold cavity. Once the mold is partially filled, gas is introduced through strategically placed nozzles. The gas forms hollow cavities within the part, displacing the plastic and pushing it against the mold walls. The plastic then cools and solidifies, and the gas is vented out, leaving behind a lightweight, yet strong part.
Advantages of Gas Assist Molding in OEM Manufacturing
Gas assist molding offers several advantages in OEM manufacturing that make it a preferred choice for many industries.
Reduced Material Usage
One of the most significant benefits of gas assist molding is the reduction in material usage. By creating hollow sections within the part, less plastic is required. This not only reduces material costs but also makes the parts lighter, which can be crucial in industries like automotive, where weight reduction is a constant goal.
Improved Part Strength and Quality
Despite using less material, parts produced using gas assist molding are often stronger than those made with traditional methods. The process ensures that the plastic is uniformly distributed and that the part has fewer defects, such as sink marks or warping. The result is a more robust and higher-quality product.
Design Flexibility
Gas assist molding technology offers greater flexibility in design. It allows for the creation of complex geometries and intricate designs that would be difficult or impossible to achieve with standard injection molding. This flexibility is particularly beneficial for OEMs looking to differentiate their products in the market through unique design features.
Cost Efficiency
With reduced material usage and improved part quality, gas assist molding can significantly lower production costs. Additionally, the process often requires shorter cycle times, leading to increased production efficiency. These cost savings can be especially advantageous for OEMs operating in highly competitive markets.
Environmental Benefits
By using less plastic material, gas assist molding contributes to environmental sustainability. The process generates less waste and reduces the carbon footprint associated with material production and disposal. This aligns well with the growing emphasis on eco-friendly manufacturing practices.
Applications of Gas Assist Molding in OEM Manufacturing
Gas assist molding technology is versatile and can be applied across various industries.
Automotive Industry
In the automotive sector, weight reduction is a top priority for improving fuel efficiency and performance. Gas assist molding is used to produce lightweight yet strong components such as instrument panels, door handles, and structural supports. These parts contribute to overall vehicle weight reduction without sacrificing safety or durability.
Consumer Electronics
Manufacturers of consumer electronics, such as smartphones and tablets, benefit from gas assist molding by being able to create sleek, lightweight, and robust housings. The process allows for precise detailing and complex designs, which are essential for modern electronic devices.
Furniture Manufacturing
Gas assist molding is increasingly used in the production of furniture, particularly for creating ergonomic and lightweight chairs and tables. The technology enables the design of comfortable and aesthetically pleasing furniture pieces while minimizing material waste.
Medical Devices
In the medical field, gas assist molding is employed to produce lightweight and durable components for various medical devices. This includes parts for medical instruments, diagnostic equipment, and aids for mobility-impaired individuals. The precision and quality of parts are critical in this industry, and gas assist molding meets these stringent requirements.
Challenges and Considerations
While gas assist molding technology offers numerous advantages, there are some challenges and considerations to keep in mind.
Initial Setup Costs
Implementing gas assist molding technology requires an initial investment in specialized equipment and mold modifications. Although this can be a significant expense, the long-term benefits in terms of material savings and production efficiency often outweigh the initial costs.
Technical Expertise
The gas assist molding process demands a higher level of technical expertise compared to traditional injection molding. Operators and engineers must be trained to understand the intricacies of the process, including gas injection timing and pressure control. Proper training and experience are critical to achieving optimal results.
Compatibility of Materials
Not all plastic materials are suitable for gas assist molding. It’s important to select compatible materials that can withstand the gas injection process without compromising the quality of the final part. Consulting with material suppliers or technical experts can help determine the best materials for specific applications.
Conclusion
Gas assist molding technology is a game-changer in the field of OEM manufacturing. With its ability to reduce material usage, improve part strength and quality, offer design flexibility, and enhance cost efficiency, it is no wonder that this technology is gaining widespread adoption across various industries.
By addressing the challenges and leveraging the advantages, OEM manufacturers can significantly enhance their production processes and create high-quality, innovative products that meet the demands of today’s market.
資料ダウンロード
QCD調達購買管理クラウド「newji」は、調達購買部門で必要なQCD管理全てを備えた、現場特化型兼クラウド型の今世紀最高の購買管理システムとなります。
ユーザー登録
調達購買業務の効率化だけでなく、システムを導入することで、コスト削減や製品・資材のステータス可視化のほか、属人化していた購買情報の共有化による内部不正防止や統制にも役立ちます。
NEWJI DX
製造業に特化したデジタルトランスフォーメーション(DX)の実現を目指す請負開発型のコンサルティングサービスです。AI、iPaaS、および先端の技術を駆使して、製造プロセスの効率化、業務効率化、チームワーク強化、コスト削減、品質向上を実現します。このサービスは、製造業の課題を深く理解し、それに対する最適なデジタルソリューションを提供することで、企業が持続的な成長とイノベーションを達成できるようサポートします。
オンライン講座
製造業、主に購買・調達部門にお勤めの方々に向けた情報を配信しております。
新任の方やベテランの方、管理職を対象とした幅広いコンテンツをご用意しております。
お問い合わせ
コストダウンが利益に直結する術だと理解していても、なかなか前に進めることができない状況。そんな時は、newjiのコストダウン自動化機能で大きく利益貢献しよう!
(Β版非公開)