- お役立ち記事
- Gas Valve Manufacturing Process and Durability Improvement
Gas Valve Manufacturing Process and Durability Improvement
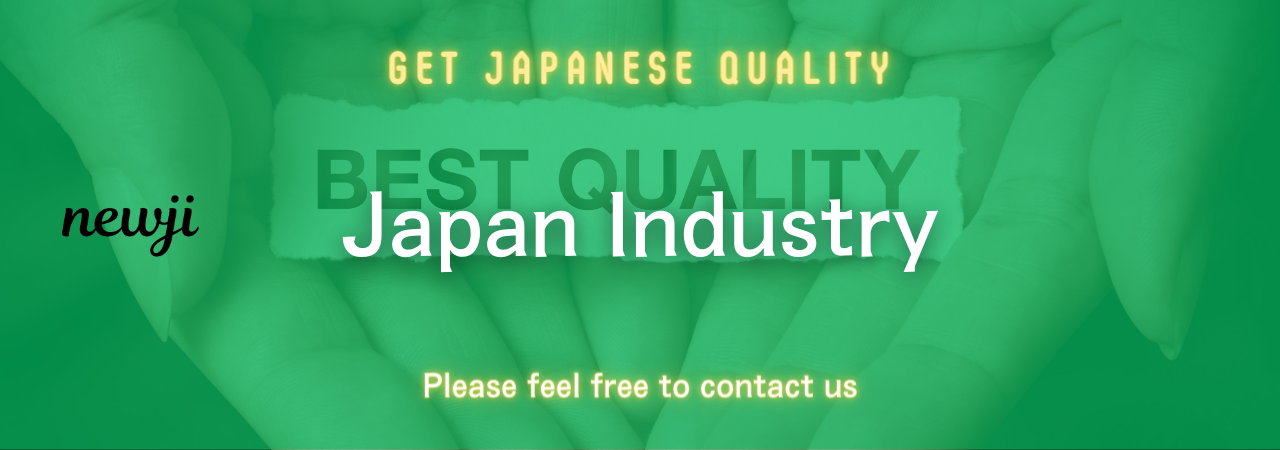
目次
Introduction to Gas Valve Manufacturing
Gas valves play an essential role in controlling the flow and pressure of gas in various applications, including residential, commercial, and industrial settings.
The quality and durability of these valves are critical because they ensure the safe and efficient operation of gas systems.
Understanding the gas valve manufacturing process and the techniques used to improve their durability can provide valuable insights into this essential component of gas distribution systems.
The Basics of Gas Valve Components
Gas valves are composed of several key components, each serving a specific function in the operation of the valve.
The main parts include the body, bonnet, disc, seat, stem, and actuator.
The **body** is the outer shell that holds the other components together and connects the valve to the pipes.
The **bonnet** acts as a cover for the valve’s internal parts, providing access for maintenance and repairs.
The **disc** is the movable part that opens or closes to regulate the gas flow, and the **seat** provides a surface against which the disc seals.
The **stem** connects the disc to the actuator, which is the mechanism controlling the movement of the disc.
Each of these components plays a vital role in the valve’s functionality and longevity.
Materials Used in Manufacturing
The selection of materials is a critical aspect of gas valve manufacturing.
Manufacturers generally use durable materials such as brass, stainless steel, and sometimes plastic composites, depending on the application.
Brass is commonly used due to its corrosion resistance and machinability, making it suitable for both low-pressure and high-pressure applications.
Stainless steel is preferred for higher-pressure scenarios or where better resistance to harsh environmental factors is necessary.
Plastic composites may be used for valves that require a softer seal or less thermal conductivity.
Selecting the right material is crucial to ensure that the valve can withstand the pressures and temperatures it will face in its intended environment.
Manufacturing Techniques
Multiple techniques are involved in manufacturing gas valves, each stage contributing to the creation of a robust and reliable product.
Forging and Casting
The initial step often involves forging or casting the valve’s body and major components.
Forging is a process where a metal is heated and then hammered or pressed to shape.
This method ensures high strength and durability, perfect for valves that need to withstand high pressures.
Casting, on the other hand, involves pouring liquid metal into a mold.
This technique is useful for producing complex shapes and allows for large-scale production of parts.
Machining
Once the rough shapes have been formed through forging or casting, they undergo precision machining.
Machining involves cutting, drilling, and milling to achieve the exact dimensions and specifications required for optimal performance.
This step is crucial since it directly affects the functionality of the valve.
Tolerance levels must be carefully controlled to ensure that components fit together seamlessly and operate without frictional losses.
Assembly
After machining, the components go through the assembly phase.
This involves fitting parts like the disc, seat, stem, and actuator into the valve body.
Proper alignment and secure fitting are paramount to ensure that the valve operates efficiently.
Automated systems may be used to apply consistent torque settings to guarantee that all parts are correctly fixed.
Testing for Quality Assurance
Testing is a vital part of the manufacturing process for ensuring that every gas valve meets stringent safety and performance standards.
Pressure Testing
Pressure testing is conducted to verify that the valve can withstand the operating pressure without leakage.
This involves subjecting the valve to pressures above its rated capacity to ensure it maintains integrity under stress.
Leak Testing
In addition to pressure tests, leak testing is performed to confirm that the valve does not allow gas to escape when closed.
This often involves using inert gases to detect leaks with high sensitivity.
Improving Valve Durability
Several strategies are employed to enhance the durability of gas valves, ensuring long-term reliable performance.
Enhancements in Material Coatings
One way to enhance durability is by applying specialized coatings to valve surfaces.
Coatings like Teflon or epoxy can improve corrosion resistance, which is essential for valves exposed to corrosive gases or environments.
Advanced Manufacturing Processes
Employing advanced manufacturing techniques like Computer Numerical Control (CNC) machining allows for tighter tolerances and more precise component manufacturing.
These improvements reduce the likelihood of mechanical failure, contributing to longer service life.
Regular Maintenance and Upgrades
While manufacturing processes are crucial, regular maintenance in the field is equally important.
Routine checks can identify wear and tear before they lead to failure.
Also, upgrading actuators and seals to modern, more robust models can further enhance valve longevity.
Conclusion
The manufacturing process of gas valves is intricate and involves precise engineering and high-quality materials.
Manufacturers employ various techniques and consistently enhance their processes to improve the durability of these critical components.
Through advanced materials, stringent testing, and regular maintenance, gas valve manufacturers can ensure optimal performance and safety for their customers.
Understanding these elements highlights the importance of quality and durability in gas valve manufacturing, ensuring the safe and efficient operation of gas distribution systems.
資料ダウンロード
QCD調達購買管理クラウド「newji」は、調達購買部門で必要なQCD管理全てを備えた、現場特化型兼クラウド型の今世紀最高の購買管理システムとなります。
ユーザー登録
調達購買業務の効率化だけでなく、システムを導入することで、コスト削減や製品・資材のステータス可視化のほか、属人化していた購買情報の共有化による内部不正防止や統制にも役立ちます。
NEWJI DX
製造業に特化したデジタルトランスフォーメーション(DX)の実現を目指す請負開発型のコンサルティングサービスです。AI、iPaaS、および先端の技術を駆使して、製造プロセスの効率化、業務効率化、チームワーク強化、コスト削減、品質向上を実現します。このサービスは、製造業の課題を深く理解し、それに対する最適なデジタルソリューションを提供することで、企業が持続的な成長とイノベーションを達成できるようサポートします。
オンライン講座
製造業、主に購買・調達部門にお勤めの方々に向けた情報を配信しております。
新任の方やベテランの方、管理職を対象とした幅広いコンテンツをご用意しております。
お問い合わせ
コストダウンが利益に直結する術だと理解していても、なかなか前に進めることができない状況。そんな時は、newjiのコストダウン自動化機能で大きく利益貢献しよう!
(Β版非公開)