- お役立ち記事
- Gas Welding Processing in OEM Manufacturing for High-Quality Welded Parts
Gas Welding Processing in OEM Manufacturing for High-Quality Welded Parts
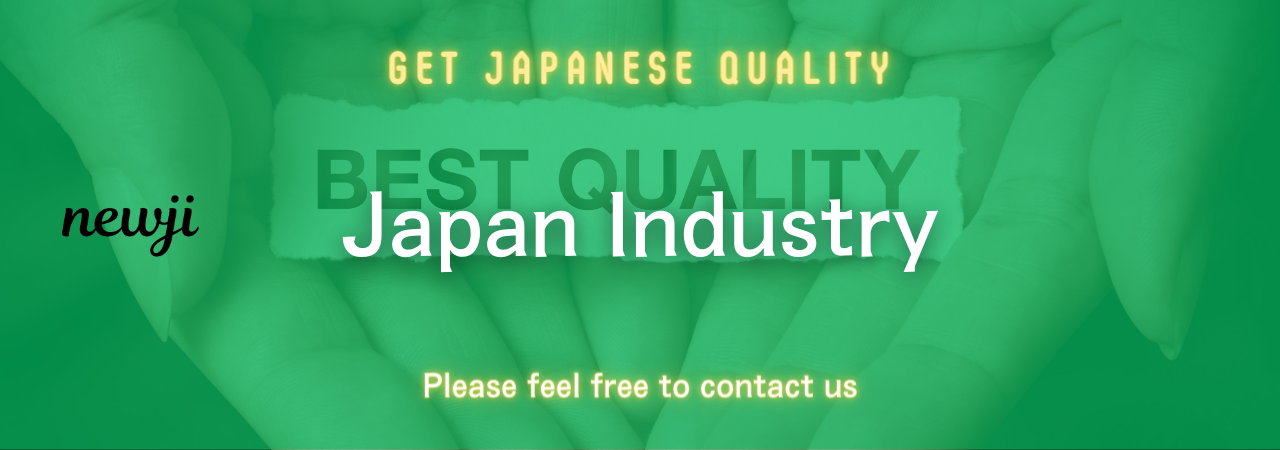
Gas welding is a crucial technique in the world of manufacturing, especially when it comes to Original Equipment Manufacturer (OEM) production.
The process is intricately designed to join metals efficiently, creating strong and reliable parts.
But what exactly is gas welding in OEM manufacturing?
目次
Understanding Gas Welding
Gas welding, also known as oxy-fuel welding, involves the use of a torch to heat metals until they are in a molten state.
A mixture of oxygen and fuel gases such as acetylene is used to produce a flame hot enough to melt and join pieces of metal together.
This type of welding is particularly useful in OEM manufacturing due to its precision and durability.
The Importance of Gas Welding in OEM Manufacturing
OEM manufacturing revolves around producing parts that are not sold directly to consumers but used in the assembly of final products by other companies.
Precision and Quality
One of the primary reasons gas welding holds a vital place in OEM manufacturing is its precision.
The ability to control the heat and flow of the welding process ensures that parts are joined accurately, resulting in higher-quality products.
This precision is essential when creating complex machinery or delicate components.
Durability and Strength
Gas welding provides strong and durable joints, which is a necessity in OEM manufacturing.
These welded parts must withstand high levels of stress and function reliably over time.
The robustness of gas-welded joints ensures that the final products are safe and effective, meeting the stringent requirements set by regulatory bodies and end consumers alike.
The Gas Welding Process
The process of gas welding in OEM manufacturing is methodical and requires a skilled hand.
Let’s break down the essential steps involved.
Preparation
Before any welding occurs, thorough preparation is necessary.
This involves cleaning the metal surfaces to remove any contaminants that might interfere with the welding process.
Proper alignment of parts ensures that the welding will be consistent and strong.
Setting Up the Equipment
The next step is setting up the gas welding equipment.
This includes attaching the correct torch tips, checking the pressure of the gas cylinders, and ensuring the torch is functioning correctly.
Safety checks are also crucial at this stage to prevent any accidents during the welding process.
Executing the Weld
Once everything is set up, the actual welding can begin.
The welder ignites the torch and adjusts the flame to achieve the optimal temperature.
They then move the torch along the joint, melting the edges of the metal and adding filler material if necessary.
Control and finesse are vital here, as inconsistent movement can result in weak joints or defects.
Applications of Gas Welding in OEM Manufacturing
Gas welding is used across a multitude of industries within OEM manufacturing.
Let’s explore some of its applications.
Automotive Industry
One of the most prominent industries relying on gas welding is the automotive sector.
Welding is essential for assembling various car parts, including exhaust systems, frames, and fuel tanks.
The precise and robust welds ensure that vehicles are safe and perform well on the road.
Aerospace Industry
In aerospace manufacturing, the high strength-to-weight ratio of gas-welded joints makes them ideal for constructing aircraft components.
This includes everything from the engine parts to the body structure.
Given the critical nature of aerospace components, the reliability provided by gas welding cannot be overstated.
Construction Industry
Gas welding is also extensively used in the construction industry for building metal structures, frameworks, and pipelines.
The durability and longevity of gas-welded joints make them ideal for structures that need to withstand significant stress and environmental exposure.
Advantages of Gas Welding in OEM Manufacturing
Gas welding offers numerous benefits that make it a preferred method in OEM manufacturing.
Versatility
One major advantage is its versatility.
Gas welding can be used on a wide range of metals, including steel, aluminum, and copper.
This flexibility makes it suitable for various applications across different industries.
Cost-Effectiveness
Compared to other welding methods, gas welding is relatively cost-effective.
The equipment and setup costs are lower, and it doesn’t require an external power source, which reduces operational expenses.
Portability
The portable nature of gas welding equipment means it can be used in various locations, including in-field repairs and on-site construction projects.
This mobility is particularly useful in OEM manufacturing when quick and efficient repairs or welds are needed on the production line.
Challenges in Gas Welding
While gas welding offers numerous advantages, it also presents some challenges.
Skill Requirement
Gas welding requires a high degree of skill and experience.
The welder must have a steady hand and deep understanding of the welding process to produce high-quality joints.
Training and certification are essential to ensure that welders can execute their tasks efficiently and safely.
Safety Concerns
Gas welding involves handling flammable gases and high temperatures, which poses safety risks.
Proper safety measures, including protective gear, adequate ventilation, and regular equipment maintenance, are necessary to mitigate these risks.
Manufacturers must also comply with safety regulations to protect their workforce.
Future of Gas Welding in OEM Manufacturing
The future of gas welding in OEM manufacturing looks promising, with advancements in technology and techniques expanding its capabilities.
Automation and Robotics
Automation and robotics are increasingly being integrated into gas welding processes.
Automated welding systems can achieve higher precision and consistency, reducing human error and increasing production efficiency.
Robotic welders are especially beneficial in large-scale manufacturing operations where high-volume, repetitive welding is required.
Advanced Materials
As new materials are developed, gas welding techniques are also evolving to accommodate them.
Researchers are working on improving the welding process for advanced alloys and composite materials, broadening the scope of gas welding applications in OEM manufacturing.
Sustainability
Sustainability is becoming a critical focus in manufacturing.
Efforts to make gas welding more eco-friendly include reducing gas consumption and improving the efficiency of the welding process to minimize waste.
Sustainable practices not only benefit the environment but also enhance the reputation and operational efficiency of manufacturing companies.
In conclusion, gas welding plays a pivotal role in OEM manufacturing, offering precision, durability, and versatility.
While it presents certain challenges, ongoing advancements and a focus on safety and sustainability continue to enhance its applications and effectiveness.
資料ダウンロード
QCD調達購買管理クラウド「newji」は、調達購買部門で必要なQCD管理全てを備えた、現場特化型兼クラウド型の今世紀最高の購買管理システムとなります。
ユーザー登録
調達購買業務の効率化だけでなく、システムを導入することで、コスト削減や製品・資材のステータス可視化のほか、属人化していた購買情報の共有化による内部不正防止や統制にも役立ちます。
NEWJI DX
製造業に特化したデジタルトランスフォーメーション(DX)の実現を目指す請負開発型のコンサルティングサービスです。AI、iPaaS、および先端の技術を駆使して、製造プロセスの効率化、業務効率化、チームワーク強化、コスト削減、品質向上を実現します。このサービスは、製造業の課題を深く理解し、それに対する最適なデジタルソリューションを提供することで、企業が持続的な成長とイノベーションを達成できるようサポートします。
オンライン講座
製造業、主に購買・調達部門にお勤めの方々に向けた情報を配信しております。
新任の方やベテランの方、管理職を対象とした幅広いコンテンツをご用意しております。
お問い合わせ
コストダウンが利益に直結する術だと理解していても、なかなか前に進めることができない状況。そんな時は、newjiのコストダウン自動化機能で大きく利益貢献しよう!
(Β版非公開)